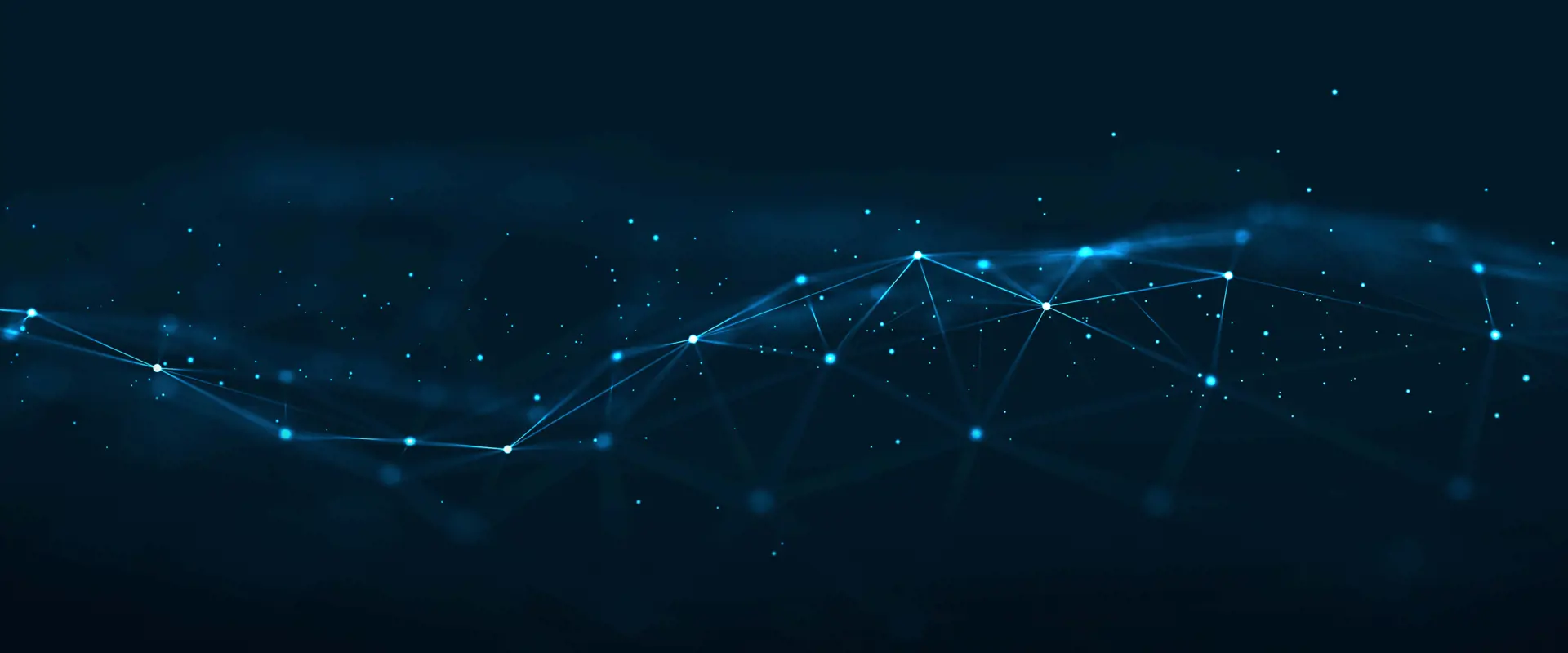
Industry 4.0: how is it shaping the future of manufacturing?
We all have heard about Industry 4.0 at least once in the last decade, since it represents such a relevant transition to the digital world and it is literally shaping the future of the manufacturing sector. The latest innovations unlock great value making the difference in a company’s overall performance. Read the article below to discover how.
- Industry 4.0 drives the digitisation of companies, which are more and more connected
- Value driven by innovation include up to 20% of inventory cost reduction, up to 30% of productivity increase and up to 50% of machine downtime reduction
- The digital twin, built up by real time location systems and services, gives companies the opportunity to have a guaranteed place in the future of the manufacturing industry
In the last decade we have all heard about Industry 4.0 which is significantly transforming the manufacturing sector, but what is it exactly? What is the value brought by the Industry 4.0 innovations?
What is Industry 4.0?
According to Forbes, Industry 4.0 is a transformation related to how products are produced and distributed and it involves the digitisation of manufacturing. Started in 2011 in Germany, it is still having such a huge impact on companies that they are continuously investing in the digitisation of their processes.
Industry 4.0 represents the fourth revolution of the manufacturing sector and it basically optimises the computerisation started in the Industry 3.0 stage, enhancing it with smart and autonomous systems.
Internet of Things (IoT), Artificial Intelligence (AI), Advanced Data Analytics and smart factories are all key concepts related to Industry 4.0, shaping the future of the manufacturing sector, which is inevitably more and more connected. The devices’ interconnection offers numerous advantages, since they are able to elaborate an extensive amount of data and to create comprehensive analysis and reports on which humans can make informed decisions.
The value driven by Industry 4.0 innovations
The innovation of the fourth industrial revolution drives substantial value to manufacturing companies, especially in terms of asset management as well as overall productivity and performance. Indeed, a McKinsey report states that with the implementation of such technologies, valuable returns across each area of the factory occur: 15-20% inventory-holding cost reduction, 15-30% productivity increase and 30-50% machine downtime reduction.
The Digital Twin
When talking about digitisation of manufacturing companies, the digital twin is to be mentioned as this technology has a lot of advantages to offer.
“A digital twin is a virtual model of a product, a service or a process and it acts as a bridge between the physical and the digital world."
- Bernard Marr, Forbes
The digital twin creates a digital representation of a physical space and process, in which every single asset moving inside the facility is digitised, located and tracked.
Everything starts with smart devices which are placed on physical items. These devices are detected by sensors that gather data about real-time positions as well as environmental conditions and send them to the gateway that, in turn, sends them in the cloud. The system underlying the data collection is called a Real-Time Location System (RTLS) and it is the starting point from which the digital twin is built.
A software intelligence receives and processes these data streams and generates analysis and reports to measure overall productivity and performance, as well as real-time location-based services to monitor and control processes inside the physical space.
Thanks the digital twin , it is possible to identify inefficiencies and reduce unnecessary costs, thus improving industrial processes, performances and productivity. Indeed, core real-time location services not only include asset tracking and process monitoring and control, but also tooling management as well as warehouse management, which can make a difference in reducing the cost of inventory-holding and lost inventory, since it gives the possibility of optimising inventory and have a real-time view of which items you already have and which you need instead.
In conclusion, Industry 4.0 is a really current topic that more and more companies rely on, in order to stay abreast of the new technologies and to not miss any opportunity to improve their business, assuring a place for them in the future of their industry.