Digital Display and Sensors
Through Digital Displays, Sensors, and other IoT devices, it is possible to interact with the physical world, creating a connection that starts from the digital front of the Digital Twin and provides operational support to those working in the physical world.
Digital Displays are IoT devices, battery-powered and remotely managed, allowing interaction with the physical world. The main features are a variable-size e-ink screen for conveying dynamic information, a high-visibility LED to visually guide operators, and configurable buttons that can be associated with different actions depending on application needs.
Sensors are battery-powered devices, remotely controlled, and capable of detecting field parameters such as temperature, humidity, door opening/closing, fill level, and much more. These devices can also control visual elements like a high-visibility LED, acoustic elements such as a siren/buzzer, or, more generally, a relay through which any powered device can be activated.
By providing and collecting the right field information, it is possible to achieve fully digitalized processes and constant visibility of the physical world, increasing productivity and reducing downtime.
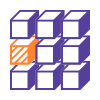
Seamless integration with major ERP, MES, and WMS systems for enhanced transparency and dynamism in business and production processes.
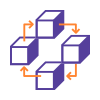
Thanks to the compact size of the devices, battery-powered operation, and easy installation, these technologies allow for the efficient collection of essential data at a low cost, enabling a comprehensive understanding of your processes.
Digital Displays: Key Features
ThinkIN Digital Displays use e-ink technology to display updated information directly on shelves or containers in the warehouse. Connected to weight and motion sensors, the displays continuously monitor component levels, automating the reordering process and providing a visual guidance system for operators during picking.
This technology not only optimizes operations but also eliminates the need for paper labels, promoting a more sustainable management approach.
Want to learn more about the evolution of logistics with digital Kanban? Read: E-Kanban: The Digital Evolution That Enhances Real-Time Logistics
Advanced Features of Digital Displays
-
Pick-by-Light Integrated:
Thinkin digital displays are equipped with pick-by-light functionality. When an operator needs to pick an item, the LED on the display lights up, visually indicating the correct position. This system guides the operator through the picking process, reducing search time and minimizing errors.
The visual feedback is especially useful in high-intensity work environments, where speed and accuracy are crucial. Additionally, the system can automatically mark the item as picked, updating the management system in real time. -
Visual Feedback and Dynamic Instructions:
The displays can show customized messages, dynamic instructions, and visual confirmations for operators. For example, during picking, the display can indicate the exact quantity to pick and confirm the action once completed.
This feature reduces the need for operator training and accelerates the onboarding process, as the instructions are clear and visible directly on the display. -
Sustainability:
The use of digital displays eliminates the need for paper labels and reduces the consumption of materials like paper and ink. Additionally, the e-ink technology has a minimal energy impact, contributing to corporate sustainability goals and reducing the overall carbon footprint.
The digitalization of the process also saves on printing costs and label management, increasing efficiency and reducing waste.
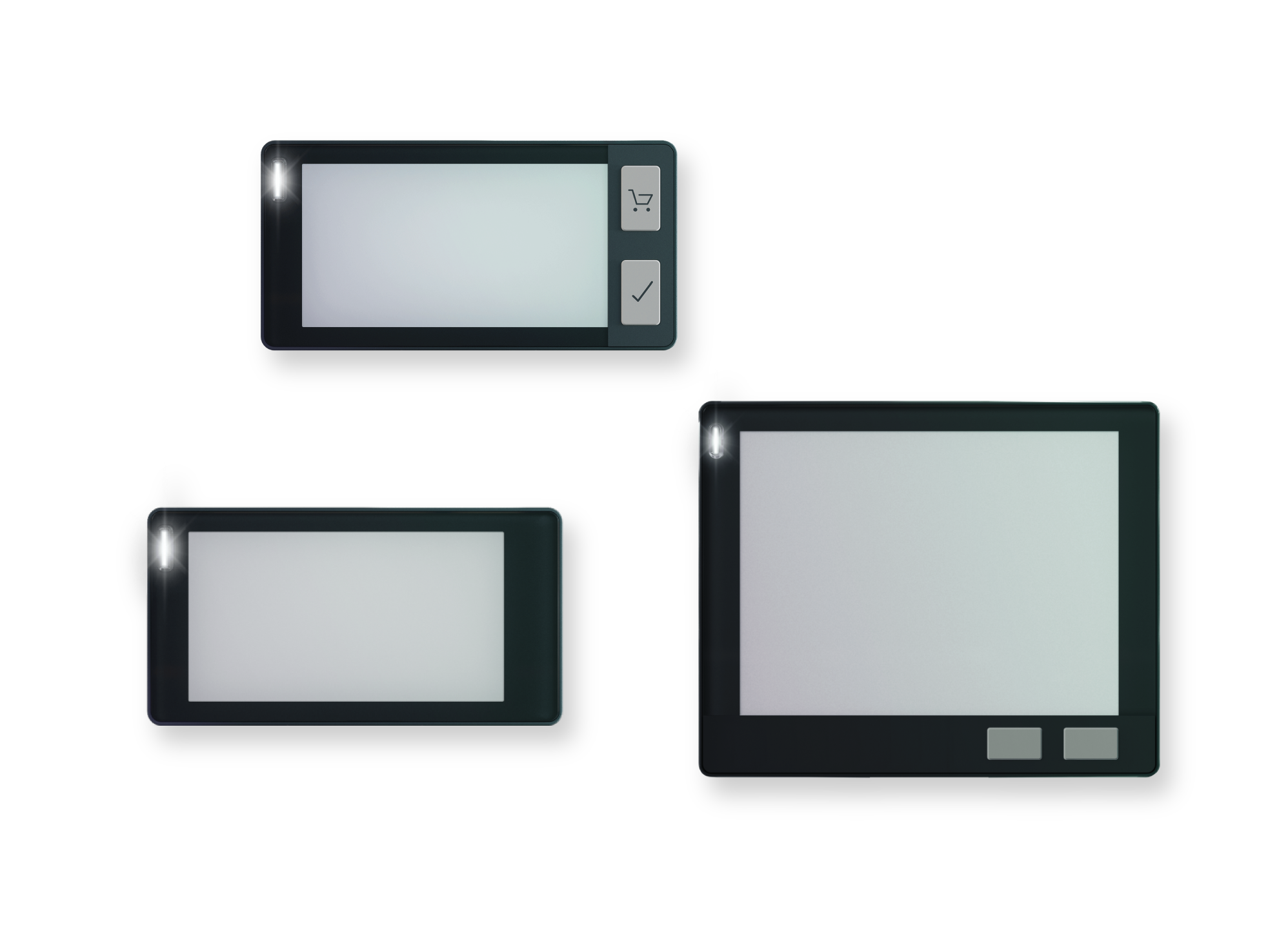
The integrated weight sensors continuously monitor the weight of the containers on which the displays are mounted. The sensor detects the decrease in weight as components are picked. When the level drops below a predefined threshold, the system automatically sends a reorder request to the management software, eliminating the need for manual checks.
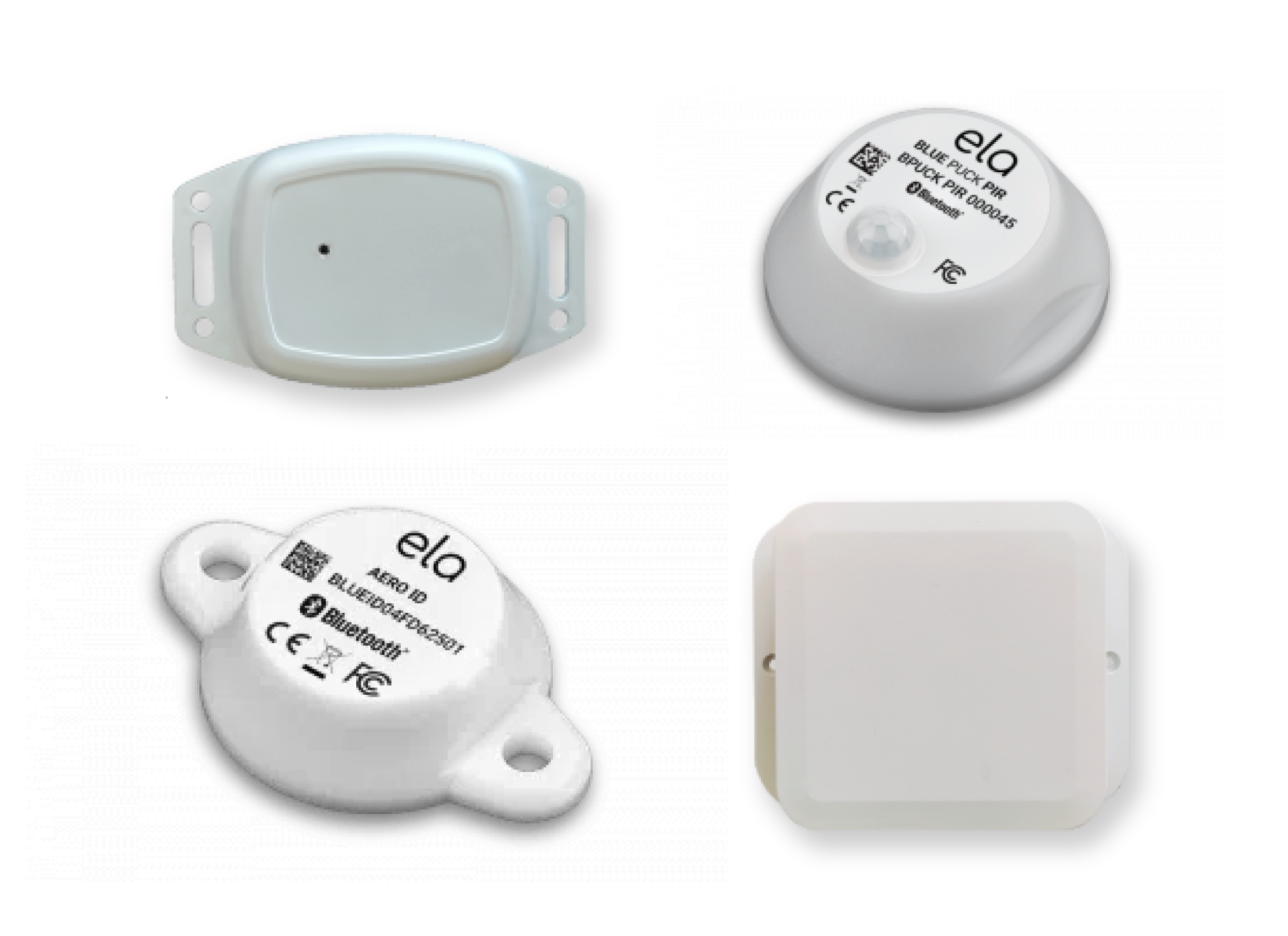
Contact or magnetic sensor:
- Machine opening detection for security scenarios
Door opening detection for access control
Temperature, humidity, air quality sensor:
- Safety monitoring in the working environment
- Quality control, production tracking
Distance or filling level:
- Industrial automation
- Automatic assignment of forklifts for
emptying/filling of waste bins, raw material bins, etc.
Remote presence sensor:
- Warehouse/production scenarios
- Picking by light, light for positioning, identification of handling unit
One Technology, many use cases!
The digital displays are like physical paper tags, but digital. They can be tracked accurately and show updated information directly on the item itself. Additionally, automated actions can be configured based on location data (e.g., triggering when items travel a certain distance or enter and exit defined areas).
- Use Case 1: ThinkIN Pick by Light
Used to quickly identify assets in the warehouse and help operators identify items to collect using the pick-by-light function.
- Use Case 2: ThinkIN e-Kanban
Used to manage digital Kanban for line-side replenishment, responding in real time to replenishment requests and optimizing milk run cycles and restocking.
The digitalization of line-side replenishment is one of the main challenges for companies aiming to increase efficiency, reduce errors, and improve inventory management. Thinkin has developed a digital display solution based on e-ink technology, automating the reordering process, improving picking, and optimizing milk run cycles and restocking.
- Use Case 3: ThinkIN WIP Management
Used to replace production orders with digital displays, reducing management overhead, making information more dynamic and accurate, and automating processes, all with a focus on sustainability.
To learn more about how the shift to digitalization can transform your business, read our article: The Future of Manufacturing is Paperless: Discover Paperless Manufacturing with ThinkIN's Digital Displays
Connection and integration with Business Management Software
- The displays and sensors are connected to the Thinkin IoT platform via Wi-Fi or BLE (Bluetooth Low Energy). The platform centralizes all the data, synchronizing it with the company's ERP (Enterprise Resource Planning), WMS (Warehouse Management System), and MES (Manufacturing Execution System).
- Integration with the management software allows for real-time updates of the information displayed on the screens, such as product descriptions, inventory levels, and other operator instructions, completely eliminating the use of paper labels.
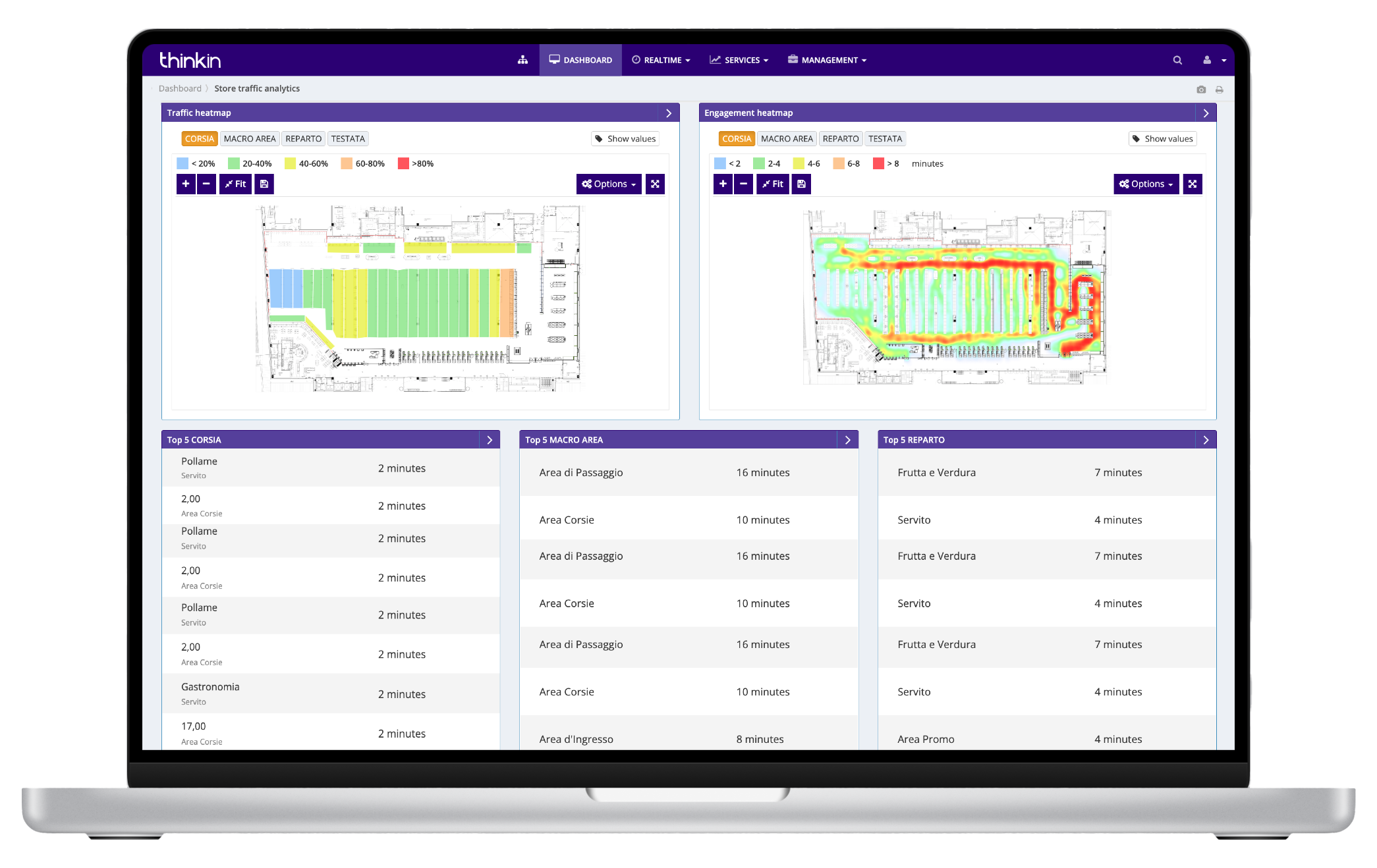