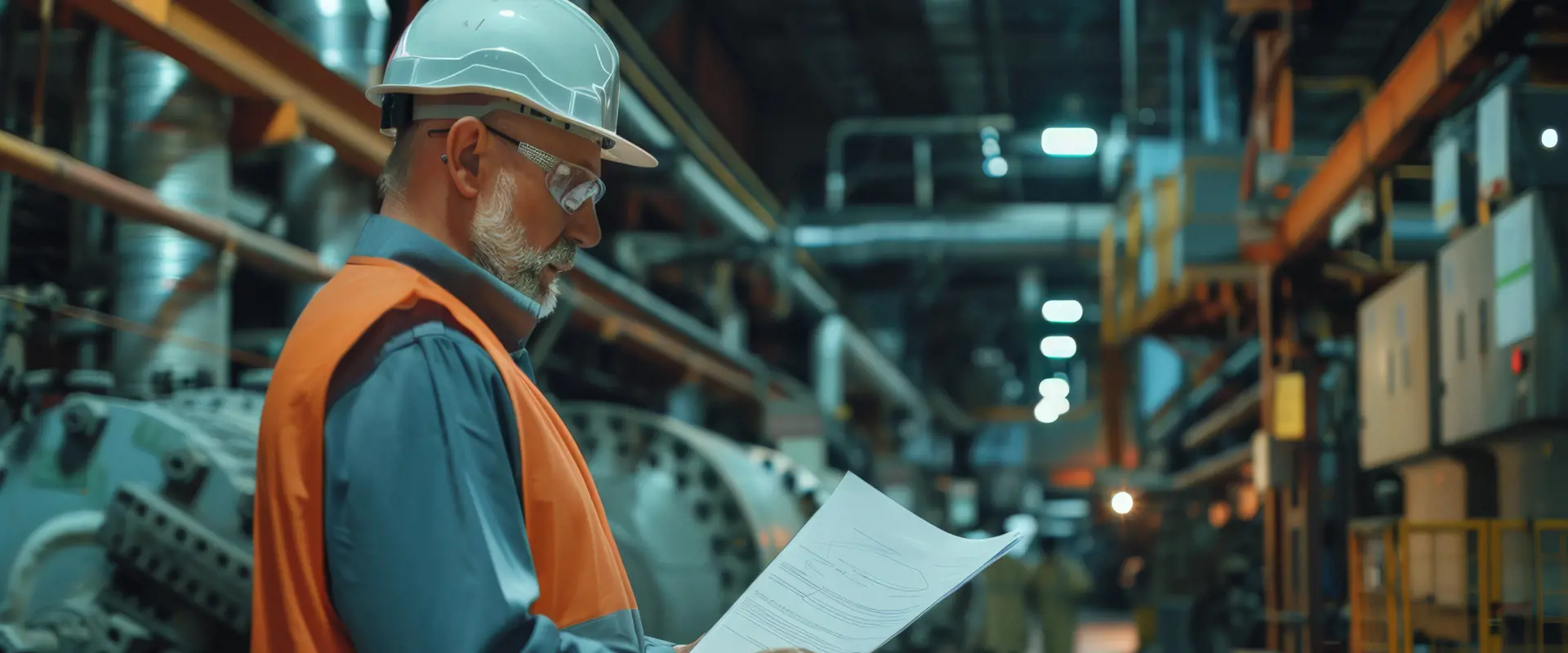
The Future of Manufacturing is Paperless: Discover Paperless Manufacturing with ThinkIN's Digital Displays
Have you ever imagined a production line without paper, where all information is accessible in real time and constantly updated? With paperless manufacturing, and especially with PDI Digitals digital displays, this is now possible.
Digital displays eliminate paper documents and simplify production management, making it easier to communicate instructions and maintain control of operations in real time.
- Operational Optimization: Digitalizing processes with interactive displays means faster, more precise, and real-time control over production processes.
- Traceability and Visibility: ThinkIN's digital displays provide a clear, real-time overview of every stage of production, reducing inefficiencies and waste.
- Sustainability: Paperless manufacturing not only enhances efficiency but also reduces your environmental impact, improving your company's reputation.
If you're looking for a way to streamline processes, reduce waste, and bring your production into the digital era, paperless manufacturing is the right path. Imagine uninterrupted management, quick and accurate decisions, all thanks to the digitalization of your production processes.
What is Paperless Manufacturing?
Paperless manufacturing involves eliminating the use of paper in production processes and replacing it with advanced digital technologies. This doesn’t just mean digitalizing documents; it represents a radical transformation in how information is managed and utilized. Data becomes available in real time on interactive devices like digital displays, enabling operators to access all the information they need to perform their tasks more efficiently and accurately.
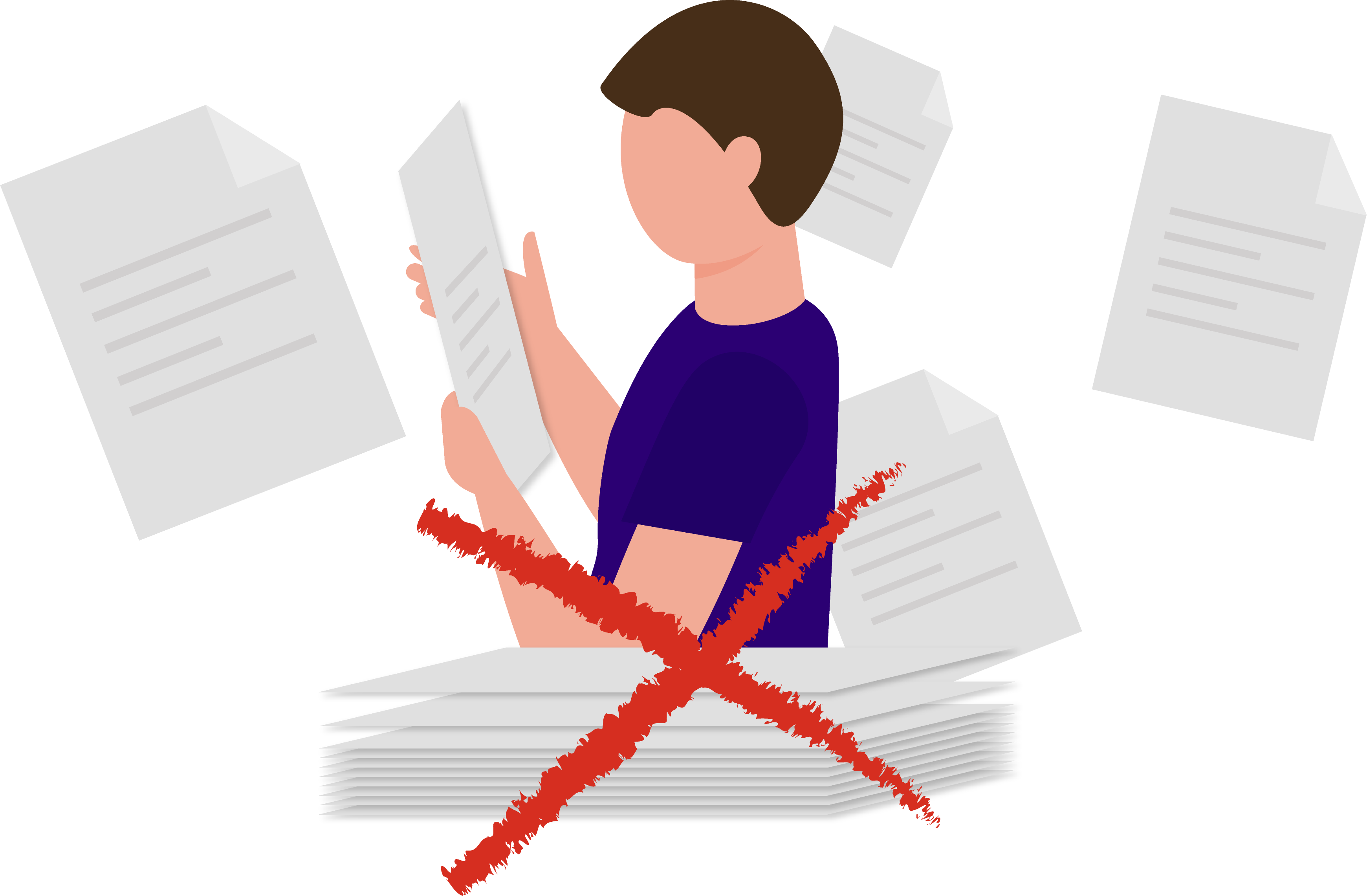
What Are Digital Displays?
PDI Digital’s digital displays are advanced devices that use e-ink technology to display real-time information on a screen, such as item codes, quantities, descriptions, and other important data, directly on products or shelves. These displays automatically update through wireless connections, keeping information continuously synchronized with management systems like ERP or WMS.
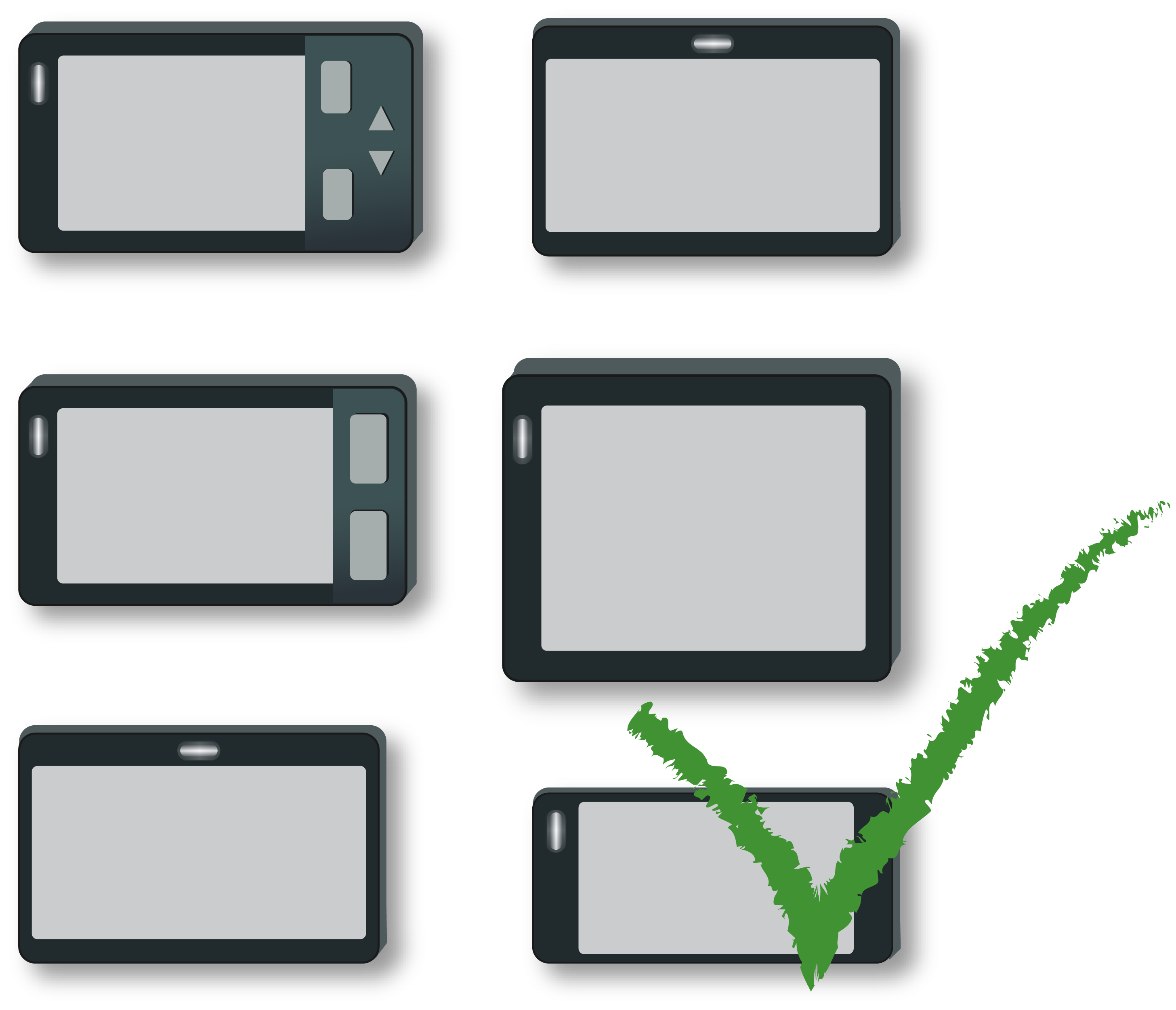
How Do Digital Displays Work?
Digital displays consist of four main elements:
- E-ink Display: The e-ink screen displays clear, real-time information, such as production order details, available material quantities, or production stages. Since it doesn’t require constant energy to maintain the image, it only consumes power when the content changes. These displays ensure consistently clear readability without consuming too much battery. Multiple pages can be created on each display, with customizable templates.
- Programmable Buttons for Specific Actions: Each display is equipped with buttons that can be programmed to perform various actions depending on the application. For example, in an e-Kanban system, when an operator notices that a component has reached its minimum stock level, they can press a button to automatically send a reorder request to the management system. In an Andon scenario, the buttons can trigger other actions, such as calling a forklift for material transport or confirming the completion of a task. The button's behavior is configured based on the company’s operational needs, making the interaction with the system simple and efficient
- Visual Feedback with Integrated LED: Each display features an LED that can be remotely controlled to provide visual feedback to operators. The LED lights up to signal the status of an action, such as confirming that a pick has been logged correctly or that a reorder has been sent. For example, when an operator presses a button to request a reorder, the LED can light up to confirm that the action has been received and processed. The LED colors can be customized to indicate different situations, such as green for completed operations and red for signaling errors or operational issues.
- Geolocation: The digital displays can be geo-located within the production facility with accuracy ranging from 1 to 10 meters, depending on the technology used. This ensures that the right information is provided at the right time and place, improving the decision-making process.
In everyday use, digital displays can be used in various ways, such as monitoring and managing workflows, supporting line-side material reordering, or helping operators manage pick lists. Operators no longer need to handle paper tags or use manual scanners. Instead, everything is centralized on the display: the operator sees what to do on the screen, can interact with the buttons to execute commands like reorder requests or completion confirmations, and receives immediate visual feedback via the LED, indicating the success or status of an operation. This makes the process much faster, drastically reducing the risk of errors and optimizing operational efficiency.
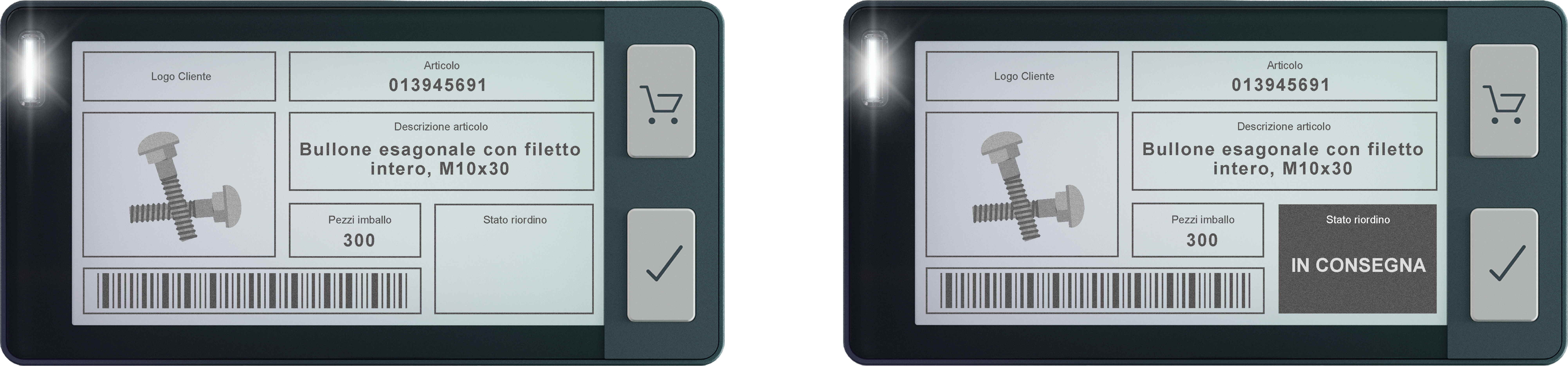
ThinkIN has successfully implemented digital display in various production environments, helping companies reduce downtime, improve efficiency, and minimize human errors.
Case Study: E-Kanban Implementation
One of ThinkIN’s most successful implementations was at a mechanical component manufacturing company, where an E-Kanban system was adopted to optimize component reordering.
Before the system was implemented, the company relied on a traditional reordering method based on paper labels and manual checks. Operators had to visually verify the remaining component quantities on shelves and then submit a reorder request by scanning barcodes or manually entering the information into the management system. This process was prone to errors and slowed down logistics, resulting in production delays.
The Solution: ThinkIN implemented an E-Kanban system, a digital Kanban management system based on digital displays. The digital labels, placed on shelves, display real-time information about components, such as remaining quantity and product code. When materials fall below a predefined threshold, operators can press a button on the label to automatically send a reorder request to the management system.
Results:
- Reduced reordering times thanks to automated requests and real-time synchronization with the ERP system.
- Errors reduced: With Pick-to-Light technology, operators were able to accurately pick the correct components, significantly minimizing human error.
- A 30% increase in efficiency, with substantial reductions in wait times and manual verification.
- Improved sustainability: Eliminating paper labels led to a significant reduction in the use of paper and ink, contributing to the company’s sustainability goals.
This solution allowed the company to optimize component management and increase productivity while simultaneously reducing operational costs and environmental impacts.
Case Study: Managing Semi-finished Products
A mechanical component manufacturing company approached ThinkIN to replace paper binders with a digital version.
Before the system implementation, the company used traditional binders based on paper labels printed at the start of each order and reprinted at certain stages of the process. Although effective, this traditional approach limited the tracking of information such as scraps or specific notes, which were often manually added to the binder to provide visual feedback to operators in subsequent stages. Additionally, handling production plan changes, such as switching machines for the next process or reworking, was difficult.
The Solution: ThinkIN implemented a system to replace the paper binder (or production order) with a digital version. At the start of each order, a digital display is programmed with all the order information, distributed over several pages. The display clearly shows the current work stage, the next stage, and any notes. From the ERP/MES, the display content can be updated in real time, allowing precise management of production flows and the tracking of certain events.
Results:
- Elimination of paper by using digital displays.
- Increased transparency: Thanks to more precise and timely information throughout the production flow.
- Improved efficiency, with the ability to more flexibly manage production flows, optimizing available resources.
- Enhanced sustainability: Eliminating paper labels led to a significant reduction in the use of paper and ink, contributing to the company’s sustainability goals.
Benefits of Paperless Manufacturing and Digital Displays
Adopting digital displays and a paperless manufacturing system provides numerous operational and strategic benefits:
- Improved Operational Efficiency: Digitalizing processes reduces downtime and human errors. Operators can access necessary information in real time, respond immediately to alerts, and manage activities with greater precision.
- Increased Transparency and Control: Every stage of production can be tracked in real time, allowing complete control over operations and enabling quick intervention in case of problems.
- Environmental Sustainability: Eliminating paper not only reduces costs but also contributes to a more sustainable production process, reducing the company’s environmental impact.
- Process Automation: With digital displays, manual processes like material reordering and work instruction management become automated, significantly reducing time and errors.
How Can Thinkin Help You?
ThinkIN is at the forefront of this transformation, with solutions perfectly aligned with the philosophy of paperless manufacturing. ThinkIN’s digital displays are designed to support the shift to paperless manufacturing, making production processes more fluid, controllable, and transparent.
Here’s how:
- Real-Time Monitoring: The digital displays provide a continuous and updated overview of all production activities. Each operator has immediate access to critical information directly from their workstation, without having to consult paper documents or wait for manual updates.
- Process Automation and Digitalization: With digital displays, it’s possible to automate work order management, maintenance requests, and performance monitoring. Every operation is visible on the display, allowing seamless and uninterrupted management.
- Work Instruction Management: ThinkIN’s digital displays show real-time work instructions and operational details, completely eliminating the need for paper instructions. This reduces error margins and ensures that operators always have the most up-to-date information.
Conclusion
The future of manufacturing is digital, and ThinkIN is ready to lead your company into this new era with paperless manufacturing solutions. It’s not just about reducing paper usage; it’s about radically transforming how you manage information, operations, and internal communication. With ThinkIN’s digital displays, you can gain total control over your processes, improve operational efficiency, and reduce your environmental impact, preparing your company for the future of industrial production.