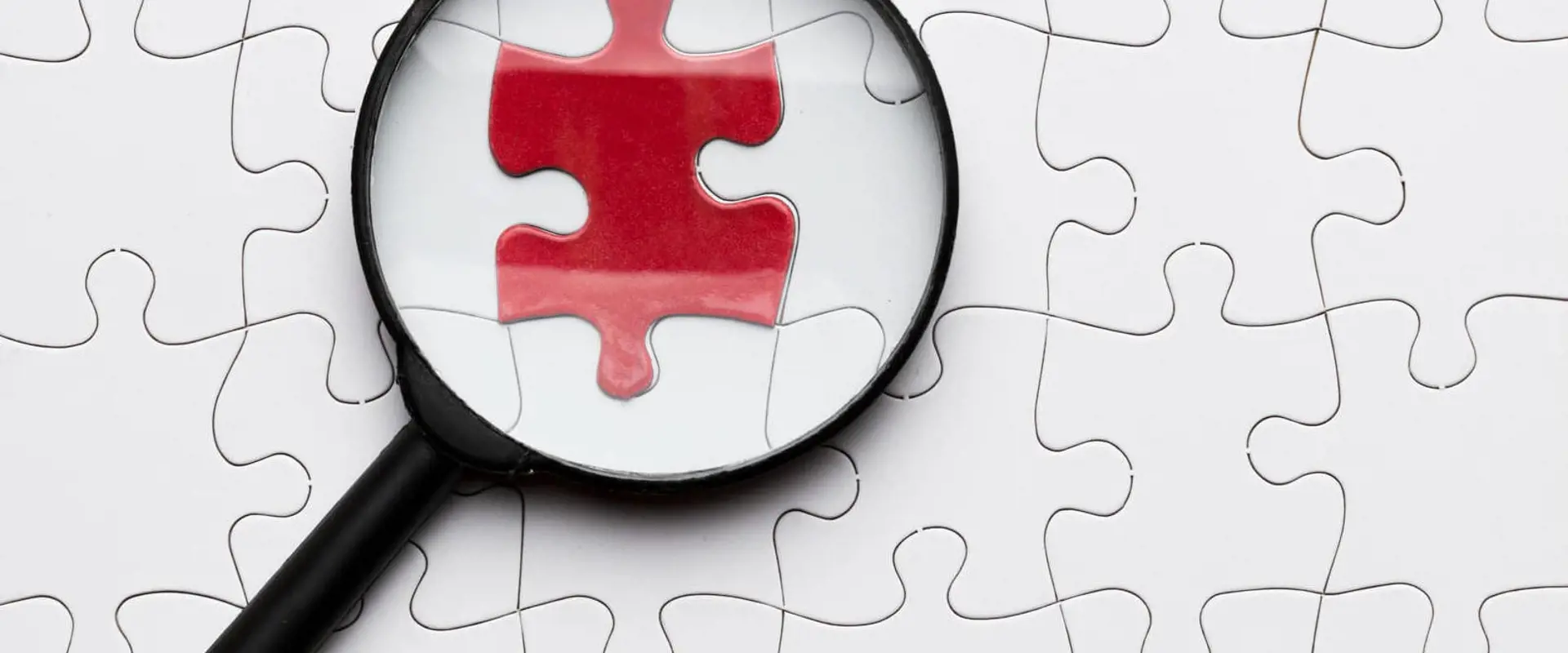
Step 1 of an RTLS project: problem identification
Identifying the problem is the first of the five steps in implementing an RTLS project. From a workshop to a detailed, customised report, here is how ThinkIN handles this first important step.
- An RTLS project starts from the problem
- Workshop to analyse the production process and the level of digitisation
- Customised report on what was analysed and a possible solution
In our previous article we talked about what the 5 steps for implementing an RTLS project are, in this article we will take a closer look at how the first step, the identification of the problem, is handled.
Usually, the customer comes to us because he sees the possibility of using RTLS technologies to meet a need related to production or some undertaken digitisation paths. For example, a lack of visibility on inventory or intra-logistic flows in their warehouse, or a lack of efficiency in the handling of semi-finished products in production.
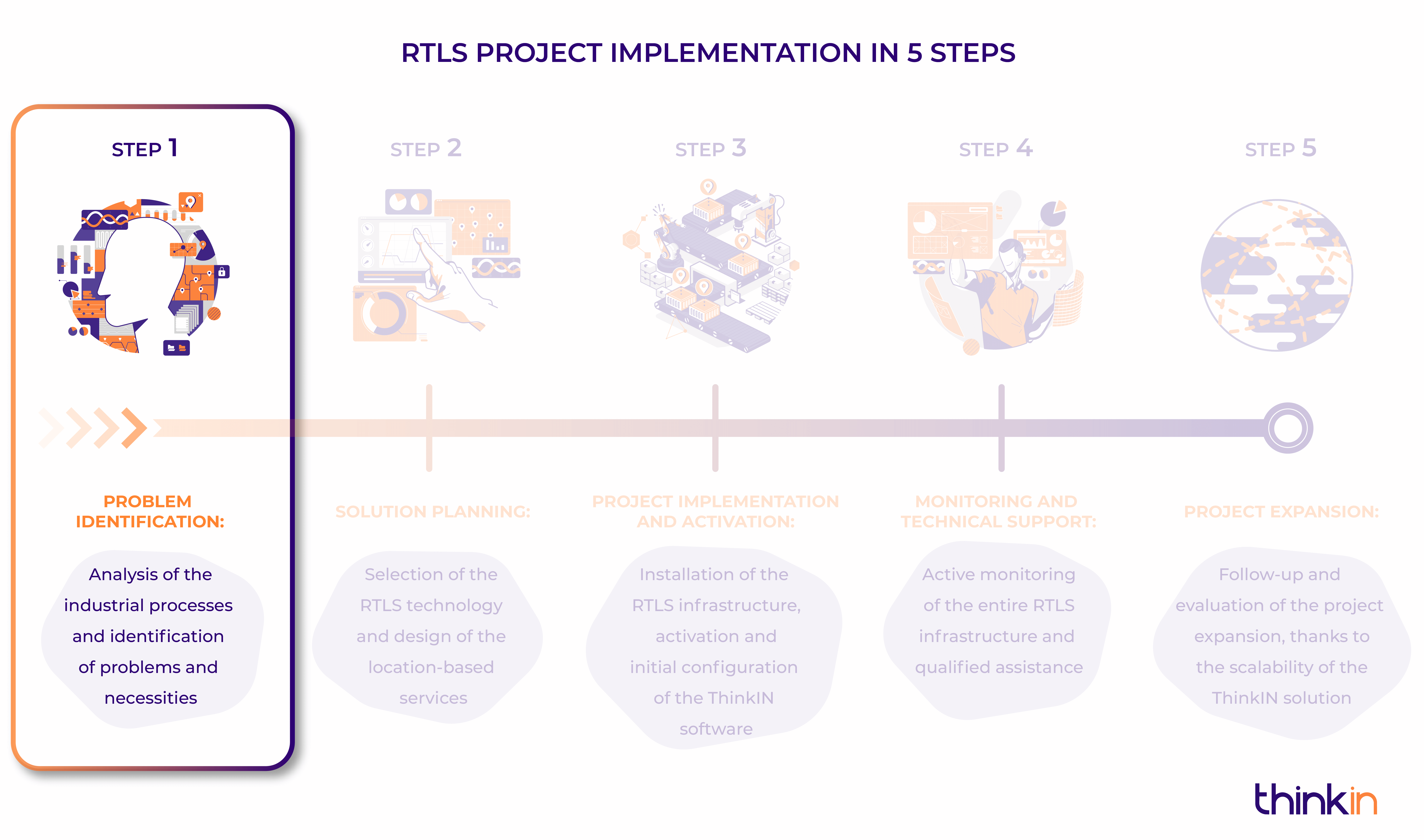
The WorkShop
Each RTLS project therefore starts with a thorough understanding of the problem, which inevitably involves an in-depth examination of the Customer's production process as well as any other aspects to be taken into account. This in-depth study is based on a design workshop lasting a few hours, which can be held online, but it is even better if it is held at the Customer in order to have a clearer and more complete view of the industrial environment in which the RTLS solution will be installed.
The workshop starts with a short training on indoor localisation services and technologies and how these have been successfully applied by several ThinkIN customers in Italy and abroad. This first part not only provides an in-depth look at RTLS and ThinkIN services, but also helps the customer to imagine a larger scale deployment, as opposed to a single infrastructure that would be installed.
Subsequently, our team of experts analyses the Customer's production process, the challenges being faced and tries to fully understand the project's objectives in both the short and medium term.
The key elements of our WorkShop
Some important requirements to be considered when organising the Workshop:
- Subjects involved: it is extremely important to involve the Customer's main figures involved directly (or indirectly) in the project (e.g. production manager, logistics, IT, field operators), in order to better understand both the aspects related to the difficulties encountered in the field and constraints on, for example, the usability of possible solutions.
- Analysis of the production process: together with the Customer, the entire production process is reviewed, in order to fully understand the various processing phases, the working tools used and the production environments. From this initial in-depth analysis, it is possible to gain a good understanding of the constraints on the use of technology and to hypothesise which solution would best suit the Customer's specific environment. Finally, this analysis also helps us to imagine possible other uses of RTLS technology beyond what was initially hypothesised.
- Quantification of the problem: the problem is then quantified in both qualitative (e.g. difficulty in finding semi-finished products) and quantitative terms (e.g. time lost searching for the semi-finished product, frequency of a certain event, etc.). This is a very important exercise to be able to define the expected benefits and especially the return over time on the investment made in the project.
- Level of digitisation: the existing IT systems (e.g. ERP, WMS, MES, etc.) are mapped. This is useful to understand the Customer's digitisation level and to document any difficulties or integration constraints with existing systems. It also allows us to create an incremental design, where integrations are only envisaged when necessary.
Upon completion of this problem identification phase, a report is issued, summarising the characteristics, difficulties and needs exposed by the Customer during the Workshop, and also identifies the main ThinkIN services that could support their resolution or mitigation. These could be existing services or services customised based on the Customer's specific need, again from the ThinkIN location intelligence platform.
The report also includes a budget indication of project implementation and a possible pilot project. This helps the customer to plan an eventual realisation of the project over time, with incremental steps according to the available budget.