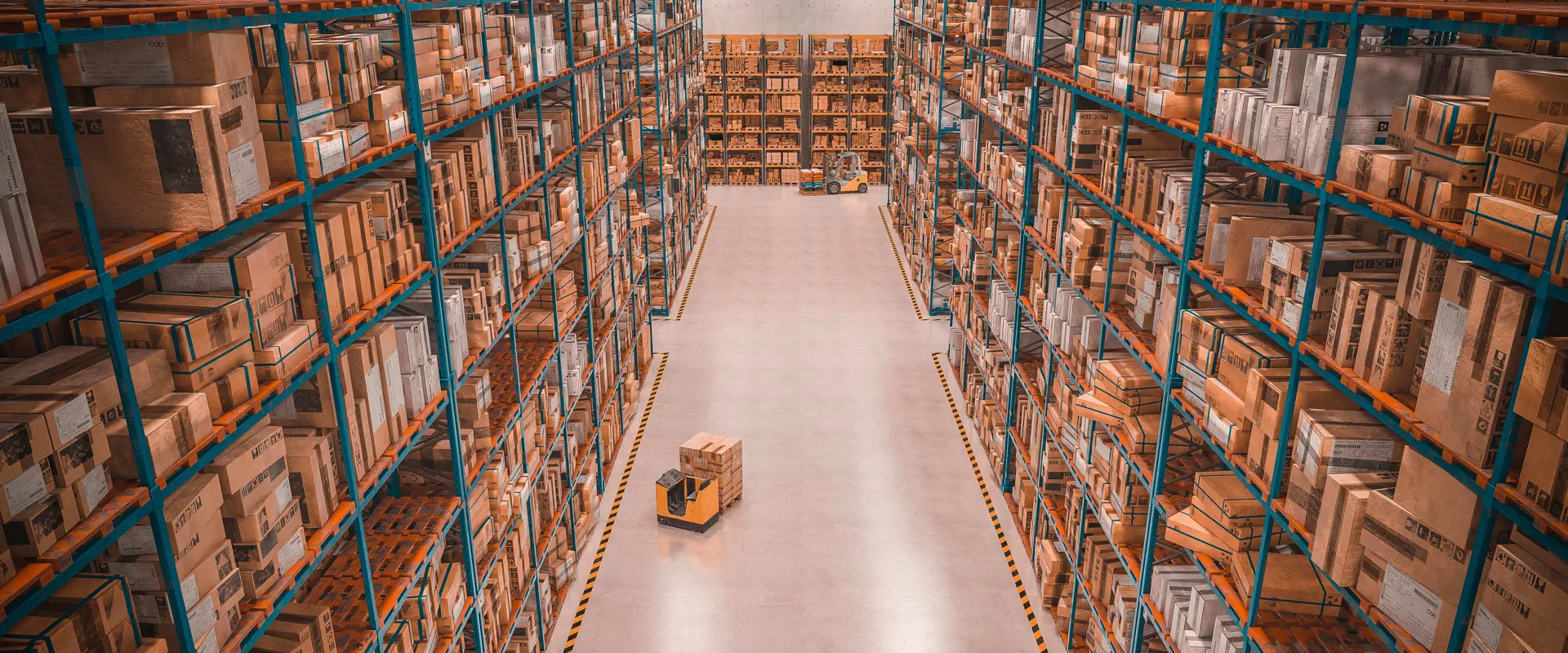
5 Warehouse Management issues that can be solved with indoor location services
Effective Warehouse Management is a crucial aspect of any business dealing with handling operations. Indoor location services provide an extremely important support to ensure process efficiency and optimisation and to enhance the overall warehouse performance.
- Full visibility and control on inventory management
- Optimisation of picking activities and space utilisation
- Enhanced safety and procedure compliance
The practice of monitoring and directing a warehouse's daily activities is known as Warehouse Management. This covers duties including inventory management, delivery and pickup, order fulfilment, and equipment maintenance. Effective Warehouse Management is critical for ensuring efficient and cost-effective operations, as well as maintaining customer satisfaction. Indoor location is a potent tool that can be used to improve Warehouse Management. In fact, indoor location services can optimise worker operations, increase productivity and efficiency, and improve the overall warehouse performance.
ThinkIN® solution for Warehouse Management
Indoor location services use a variety of real-time locating system (RTLS) technologies such as Bluetooth Low Energy (BLE) beacons, Wireless Mesh Network (WMN), and Ultra-Wideband (UWB) to determine the exact location of an asset or person inside an industrial plant. By tracking and locating the movements of goods, materials, semi-finished products, pallets, forklifts etc. ThinkIN® creates a digital twin of the warehouse, enabling a real-time control over the warehouse status and the intralogistics flows.
Extremely intuitive to use for operators, ThinkIN® is an enterprise-ready solution that can be fully customised according to specific customer requirements and can be integrated with existing systems such as ERP and WMS, among others. This is an extremely relevant aspect because even though systems such as WMSs can provide detailed information about, e.g. the warehouse inventory, the awareness of the position of the asset within the warehouse in real-time is missing without using RTLS technologies. The RTLS technology and the related indoor location services are therefore a significant value-added that not only brings numerous benefits, but also solves multiple issues.
Which Warehouse Management issues can indoor location services solve?
ThinkIN® indoor location services help solve a variety of problems in Warehouse Management, includiing:
1) Lack of inventory visibility
ThinkIN® provides real-time visibility and tracking of the entire inventory, allowing warehouse managers to quickly and easily locate specific items and track their movement throughout the warehouse. This leads to a reduction of holding costs and a better responsiveness to market demand changes thanks to a more efficient usage of resources.
2) Space utilisation
Space optimisation is enabled by the ThinkIN® services, as they can indicate areas of the warehouse where space is not effectively used, supporting the warehouse managers in making the best use of the available space. Indeed, real-time location data enables dynamic inventory management: since workers are aware of the position of the tracked assets at any time, they can be placed in the warehouse’s most convenient location at a given time rather than having to have a fixed location within the building. As a result, efficiency is significantly improved and the available space is entirely optimised.
3) Inefficiencies of picking activities
The ThinkIN® solution allows operators to not only access the picking list from any device connected to the platform (e.g. tablets, palmtops, laptops, wearable devices) but also to locate work orders within seconds as well as to optimise movements throughout the warehouse. Indeed, the ThinkIN® platform provides the fastest way to handle work orders, by showing the most efficient path to be followed on the map. This represents an extremely relevant support to speed up handling operations, by increasing efficiency.
4) Safety
Indoor location services help to improve safety and security at the workplace. For instance, ThinkIN® provides one specific service for collision avoidance, supporting the prevention of accidents caused by collisions between workers and moving vehicles, as they are both tracked and alarms are triggered in case the distance among them does not comply with safety criteria.
5) Procedures compliance
The ThinkIN® solution supports organisations in the compliance of warehouse protocols such as FIFO or LIFO thanks to the real-time tracking of the whole intralogistics flows.
Overall, indoor location services offer numerous advantages on multiple issues related to Warehouse Management, from the operations efficiency to safety at the workplace and from inventory management to procedures compliance. Contact us to have a free consultation to analyse your Warehouse Management challenges.