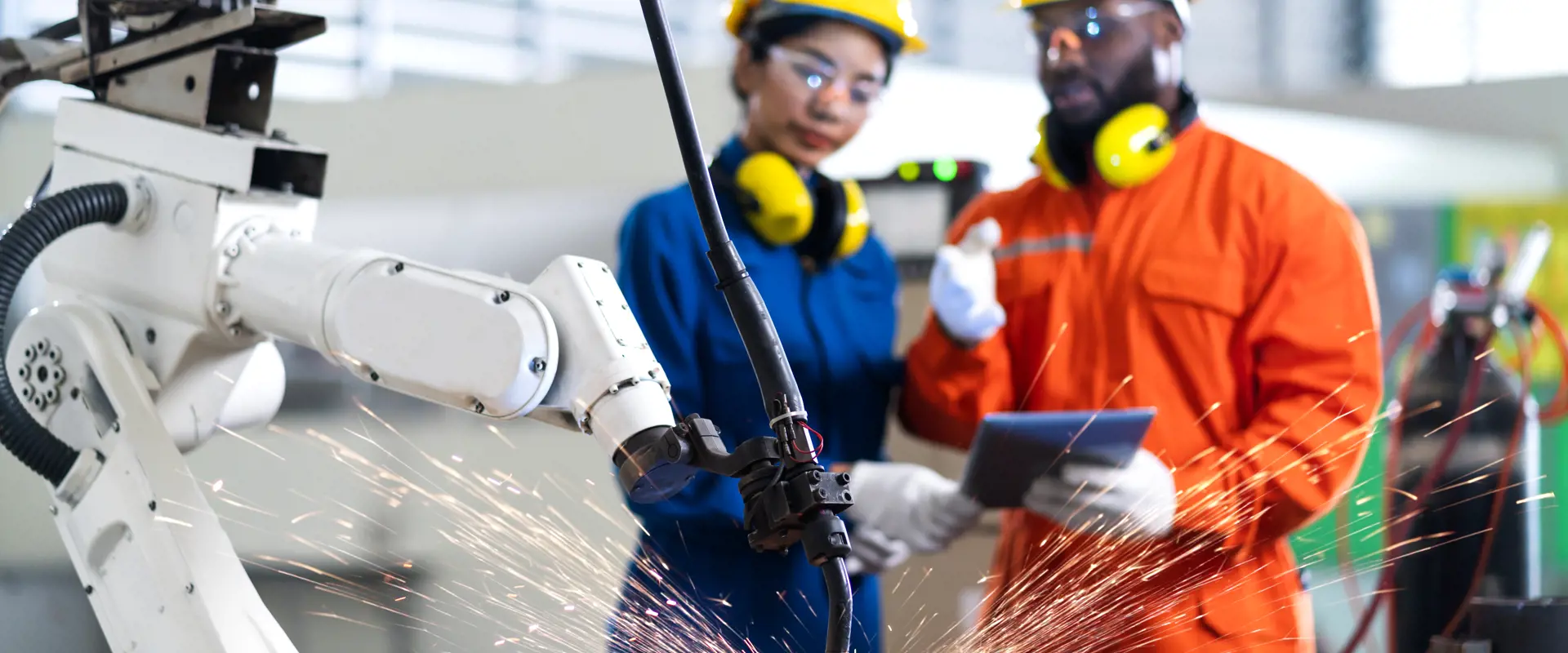
Investing in IoT: the benefits of the Industry 5.0 Decree
Industry 5.0 is unstoppable, and at the heart of this technological revolution lies the Internet of Things (IoT), which is radically changing the face of the metallurgical industry. In the context of the 2024 Industry 5.0 Decree, this article explores how IoT is transforming the sector, bringing tangible benefits and offering targeted incentives for the adoption of industrial software and the development of innovative solutions. Also important is training for digital skills and the advantages in terms of environmental sustainability that these technologies can bring.
- Why invest in industrial Software and IoT
- Exploring incentives of the industry 5.0 Decree
- The Opportunity for metallurgical companies
As already known, companies can access the Industry 5.0 Transition Tax Credit for investments 'in new material and immaterial assets instrumental to the business activity listed in Annexes A and B attached to Law no. 232 of December 11, 2016, and which are interconnected.'
Paragraph 4 lists:
a) the software, systems, platforms, or applications for plant intelligence that ensure continuous monitoring and visualization of energy consumption and self-produced and self-consumed energy, or introduce energy efficiency mechanisms, through the collection and processing of data also coming from field IoT sensors.
Immaterial Assets: Industrial Software
In March 2024, the Italian industrial landscape took a significant step forward with the introduction of the Industry 5.0 Decree. This decree, designed to strengthen the competitiveness of national companies, places particular emphasis on immaterial assets, especially industrial software, and the importance of investments in Internet of Things (IoT) technologies. For companies in the metallurgical sector, this represents an unprecedented opportunity for modernization and growth.
One of the fundamental pillars of the Industry 5.0 Decree is the attention dedicated to immaterial assets, especially industrial software. These tools, often underestimated, are actually the essence of the new industrial era. With advanced software, metallurgical companies can optimize production processes, reduce waste, improve quality and precision, and increase the flexibility of their operations.
Industrial software enables more efficient resource management, from production to logistics, offering real-time visibility into all processes. Through the integration of technologies like artificial intelligence and machine learning, these tools become increasingly intelligent in predicting issues and optimizing performance.
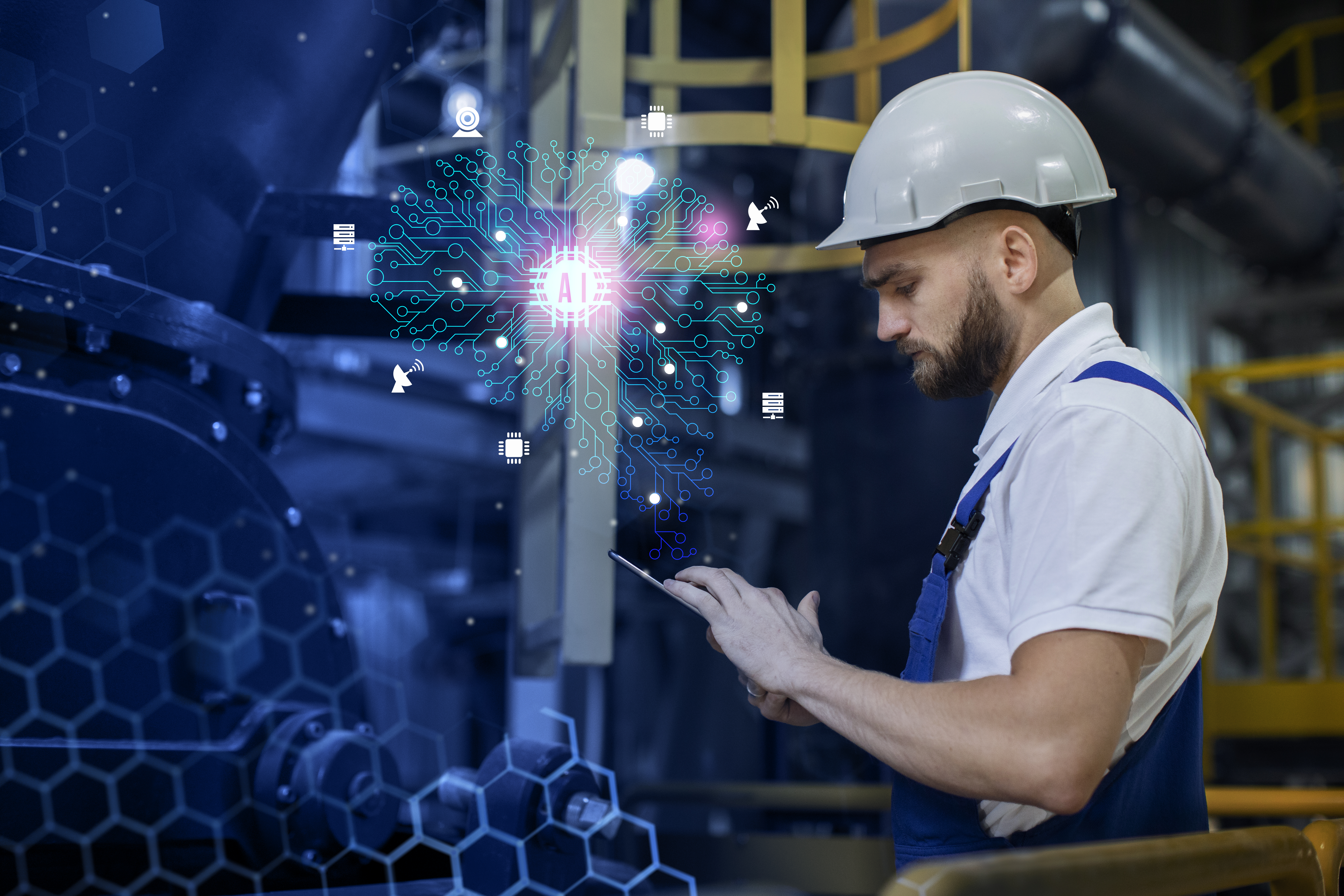
Some Benefits
Process Optimization
Imagine a foundry using industrial software to constantly monitor furnace temperatures. This software not only collects real-time data but also analyzes it to identify trends and predict when maintenance might be needed. This reduces downtime, optimizes the use of energy resources, and improves workplace safety.
Waste Reduction
In metallurgical production processes, every gram of material is valuable. Industrial software can help reduce waste by identifying critical points where losses are most frequent. With this information, companies can make targeted changes to optimize material use and reduce production costs.
Quality Control
The quality of the produced metal is essential for industrial applications. Industrial software can continuously monitor production parameters, ensuring that each batch of material meets the required standards. Additionally, it can quickly identify any defects or deviations, allowing for timely interventions to improve quality.
Operational Flexibility
With industrial software, metallurgical companies can quickly adapt to changes in demand. If there's a sudden demand for a specific type of material, intelligent systems can reconfigure production lines to meet this need without significant interruptions.
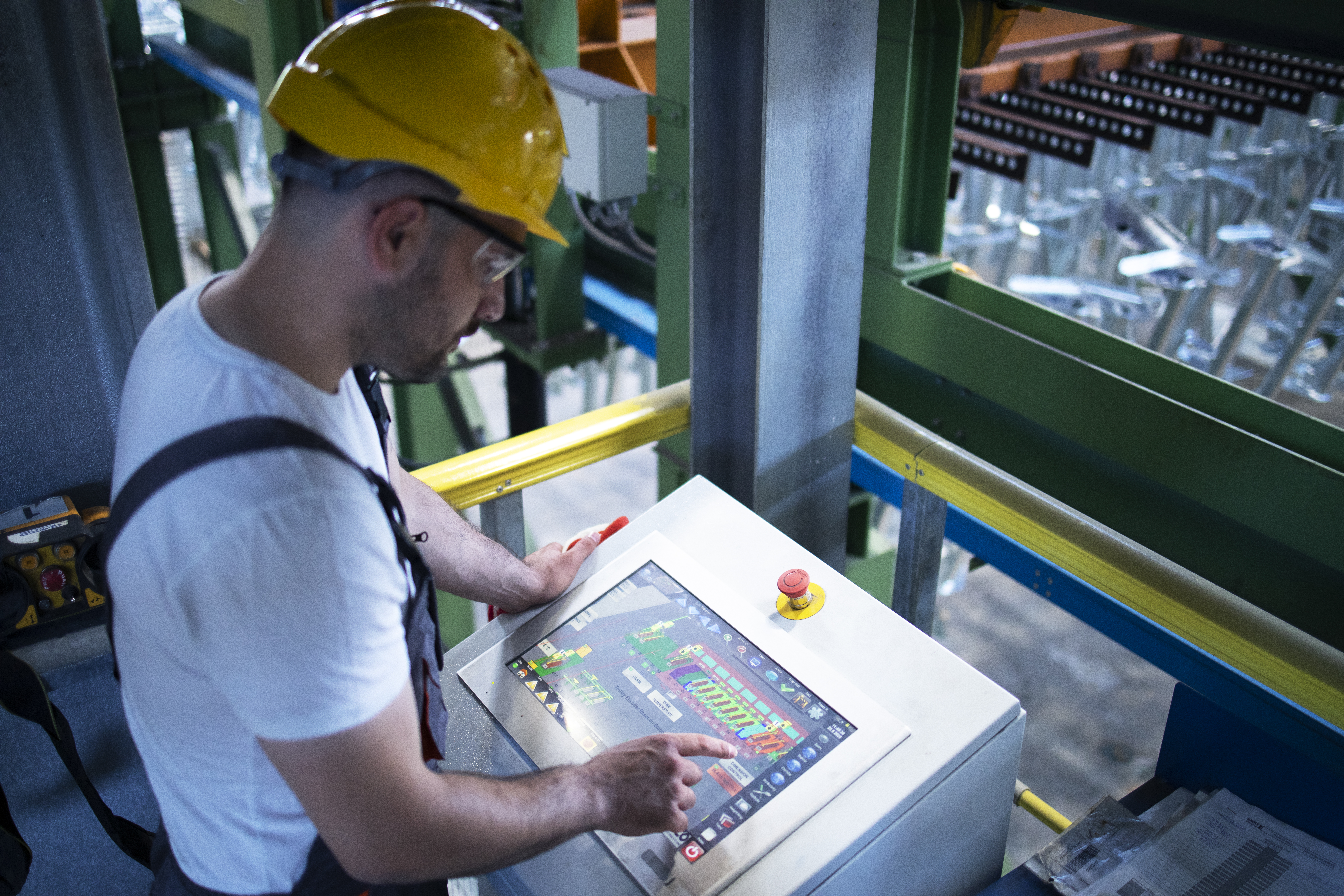
The Industry 5.0 Decree
The Industry 5.0 Decree, which came into effect on March 1, 2024, was designed with the goal of accelerating the digital transformation of the Italian industry. This decree introduced a series of incentives and measures to promote the adoption of cutting-edge technologies, such as industrial software and IoT, specifically to support the competitiveness of companies in the metallurgical sector and beyond.
Tax Credit for the Purchase of Industrial Software and IoT
One of the most relevant aspects of the Decree is the introduction of a tax credit for companies investing in industrial software and IoT technologies. Companies in the metallurgical sector can benefit from a tax credit equal to 50% of the costs incurred for the purchase of software aimed at optimizing production processes and for the implementation of IoT solutions.
This tax incentive is crucial to make these cutting-edge technologies more accessible to companies, especially larger ones that require significant investments to adopt these solutions. Thanks to this tax credit, metallurgical companies can reduce the initial implementation costs and accelerate the return on investment.
Collaborations and Research and Development
The Industry 5.0 Decree also promotes collaboration between companies and research institutions for the development and application of innovative technologies. This aspect is particularly relevant for the metallurgical sector, where research and development of new materials and processes can lead to significant competitive advantages.
Companies that collaborate with universities, research centers, or other companies for the development of new technological solutions can benefit from tax breaks and state contributions. This encourages companies to invest in research and innovation, essential to remain competitive in an ever-evolving market.
Training and Digital Skills
Another important aspect of the Decree is the focus on training and the development of digital skills. Companies are encouraged to invest in staff training to acquire the digital skills necessary to make the best use of the new implemented technologies.
Through state-funded training programs, companies can ensure that their employees are adequately prepared to handle complex industrial software and fully exploit the potential of IoT. This not only improves internal efficiency and productivity but also helps create a culture of innovation and continuous improvement within the company.
Incentives for Sustainability
The Industry 5.0 Decree also includes specific incentives for environmental sustainability. Metallurgical companies that adopt IoT technologies to monitor and optimize energy consumption, reduce polluting emissions, or improve waste management can benefit from tax breaks and contributions.
This focus on sustainability is not only beneficial for the environment but also responds to the growing demand from consumers and institutions for more eco-friendly products and processes. Companies that invest in sustainability not only contribute to environmental protection but can also access new markets and improve their corporate reputation.
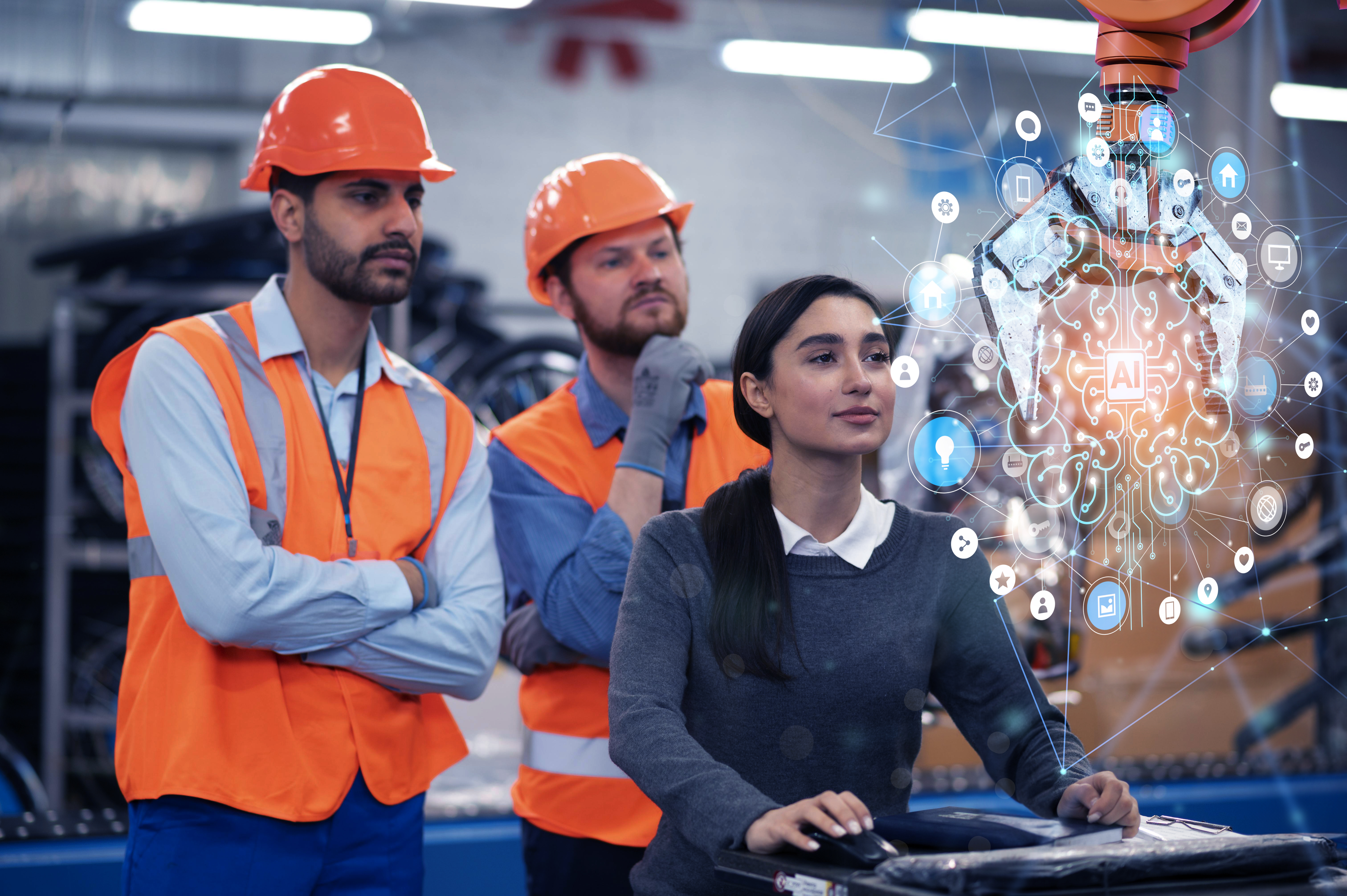
Benefits of investing in IoT technologies
Alongside the focus on industrial software, the Industry 5.0 Decree promotes investments in Internet of Things (IoT) technologies. For metallurgical companies, this means having the opportunity to transform their factories into highly interconnected and intelligent environments.
Remote Monitoring and Predictive Maintenance
Thanks to IoT, sensors can be installed on critical machinery to constantly monitor operational conditions. These sensors transmit real-time data to a central system, where advanced algorithms can detect anomalies. If a machine shows signs of impending malfunction, the system can send alerts to operators to intervene before a breakdown occurs, enabling predictive maintenance rather than reactive.
Supply Chain Optimization
IoT doesn't stop at the factory walls; it can extend along the entire supply chain. Sensors placed on vehicles transporting raw metal can monitor the location and transport conditions. This not only improves logistical efficiency but also enables complete traceability of the material, from its origin to the finished product.
Creation of New Business Models
Metallurgical companies can leverage IoT to offer data-based services. For example, instead of just selling the metal, they can offer service contracts that include remote monitoring, predictive maintenance, and part replacement. These new business models not only generate additional revenue but also increase the perceived value of their products.
Safety and Compliance
With IoT, companies can improve workplace safety and better comply with environmental regulations. Smart sensors can detect hazardous situations, such as excessive temperatures or presence of harmful substances, and trigger immediate alerts for quick intervention. Additionally, the collected data can be used to demonstrate compliance with environmental regulations, enhancing the company's image and reducing the risk of penalties.
The opportunity for metallurgical companies
In conclusion, the Industry 5.0 Decree of March 2024 offers unprecedented opportunities for companies in the metallurgical sector to modernize, grow, and compete in the global market. Focusing on industrial software and the Internet of Things (IoT), the Decree provides incentives and facilitations to ease the adoption of these cutting-edge technologies.
Companies that decide to invest in advanced industrial software and IoT technologies can enjoy a range of benefits, including:
- Operational Efficiency: optimization of production processes, waste reduction, and increased productivity.
- Improved Quality: precise control of product quality, reduction of defects, and improved customer satisfaction.
- Cost Reduction: minimization of operational costs, increased energy efficiency, and reduced losses.
- New Business Opportunities: offering data-based services, developing innovative products, and diversifying offerings.
- Environmental Sustainability: reducing environmental impact, compliance with environmental regulations, and enhancing corporate reputation.
Decision-makers in large metallurgical companies now have the opportunity to lead their businesses towards a more efficient, intelligent, and sustainable future. By leveraging the opportunities offered by the Industry 5.0 Decree, they can position themselves at the forefront of industrial innovation, ensuring sustainable growth and a leadership position in the global market.