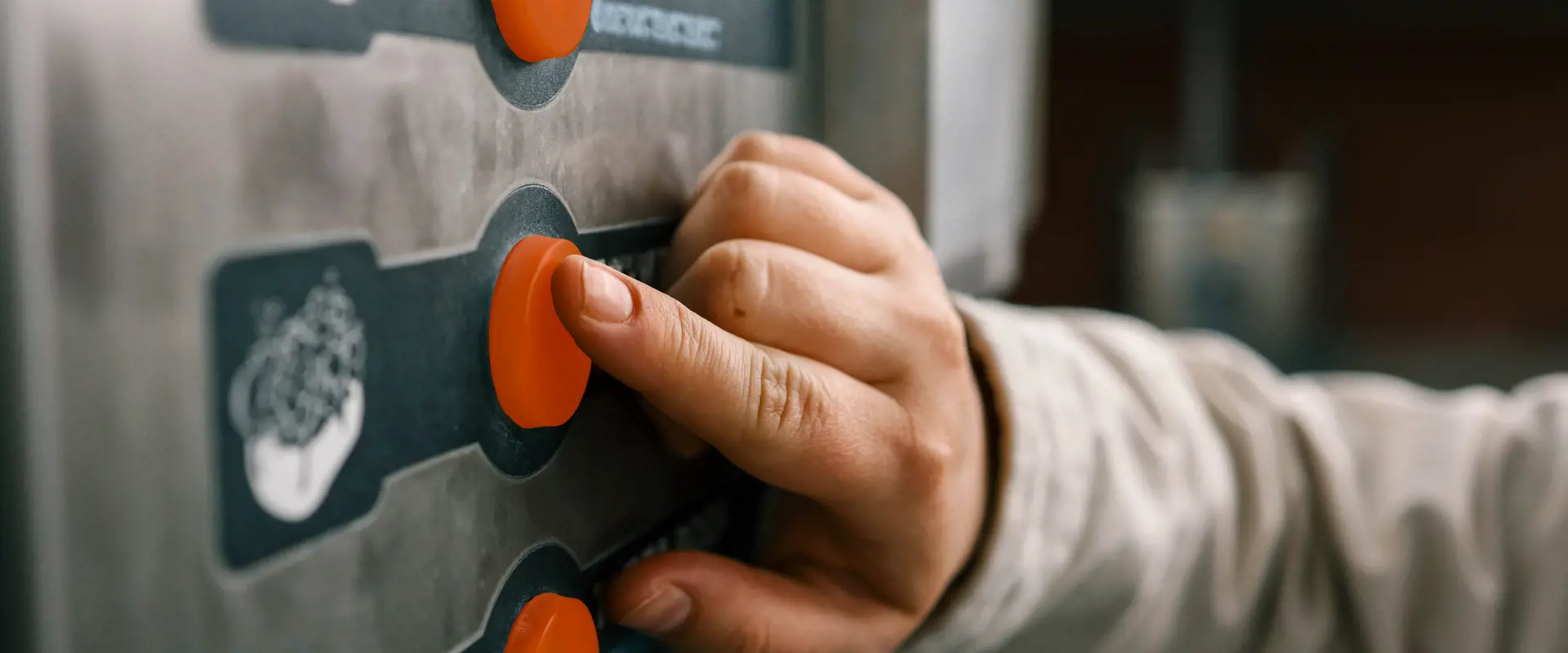
Enhance your production with ThinkIN’s Andon Wireless System
Imagine being able to identify and resolve issues on your production line in real time, without having to run from one end of the factory to the other or relying on constant phone calls. Imagine being able to track all these interventions, measure and optimize response times.
What if I told you this is possible thanks to ThinkIN’s Andon Wireless system?
Discover how this innovation can transform your production and make you more competitive.
- Improve production flow by reducing downtime and increasing overall productivity
- Provide immediate alerts for potential defects, enabling timely management of quality issues.
- Facilitate real-time communication between operators and supervisors, ensuring issues are addressed quickly, contributing to significant cost savings in production.
What is an Andon System?
An Andon system is a visual and acoustic communication tool used in production to alert workers and supervisors to quality or process issues. Originating from lean manufacturing practices, Andon systems allow operators to signal the need for assistance, ensuring that problems are addressed promptly to minimize downtime and maintain high-quality standards.
ThinkIN’s Andon service is designed to transform the way industries operate, enabling the efficient and straightforward management of production requests, providing the necessary information to increase operational efficiency and productivity.
The Benefits of Implementing ThinkIN's Andon Wireless Systems
Implementing Andon systems in a manufacturing environment offers several significant advantages, including:
- Efficiency Improvement: By allowing for the rapid identification and resolution of issues, Andon systems help maintain a steady production flow, reducing downtime and increasing productivity.
- Enhanced Quality Control: With immediate alerts for potential defects, quality issues can be addressed before they escalate, ensuring products meet high standards.
- Increased Employee Engagement: Empowering workers to report issues fosters a sense of responsibility and engagement, leading to higher job satisfaction and morale.
- Cost Reduction: By reducing interruptions and defects, Andon systems contribute to significant cost savings in the production process.
How Does ThinkIN’s Andon Wireless System Work?
Now let’s get into the details: how exactly does ThinkIN’s Andon Wireless system work? Get ready to discover a technology that will change the way you manage your production.
ThinkIN’s Andon Wireless system is designed to provide efficient and simple call management, eliminating the need for complex wiring and offering a completely flexible solution adaptable to different production needs.
1. Wireless Call Devices
Each workstation is equipped with a battery-powered wireless call device that can be easily installed and moved as needed. This device allows operators to quickly send an alert in case of issues on workstations or production lines.
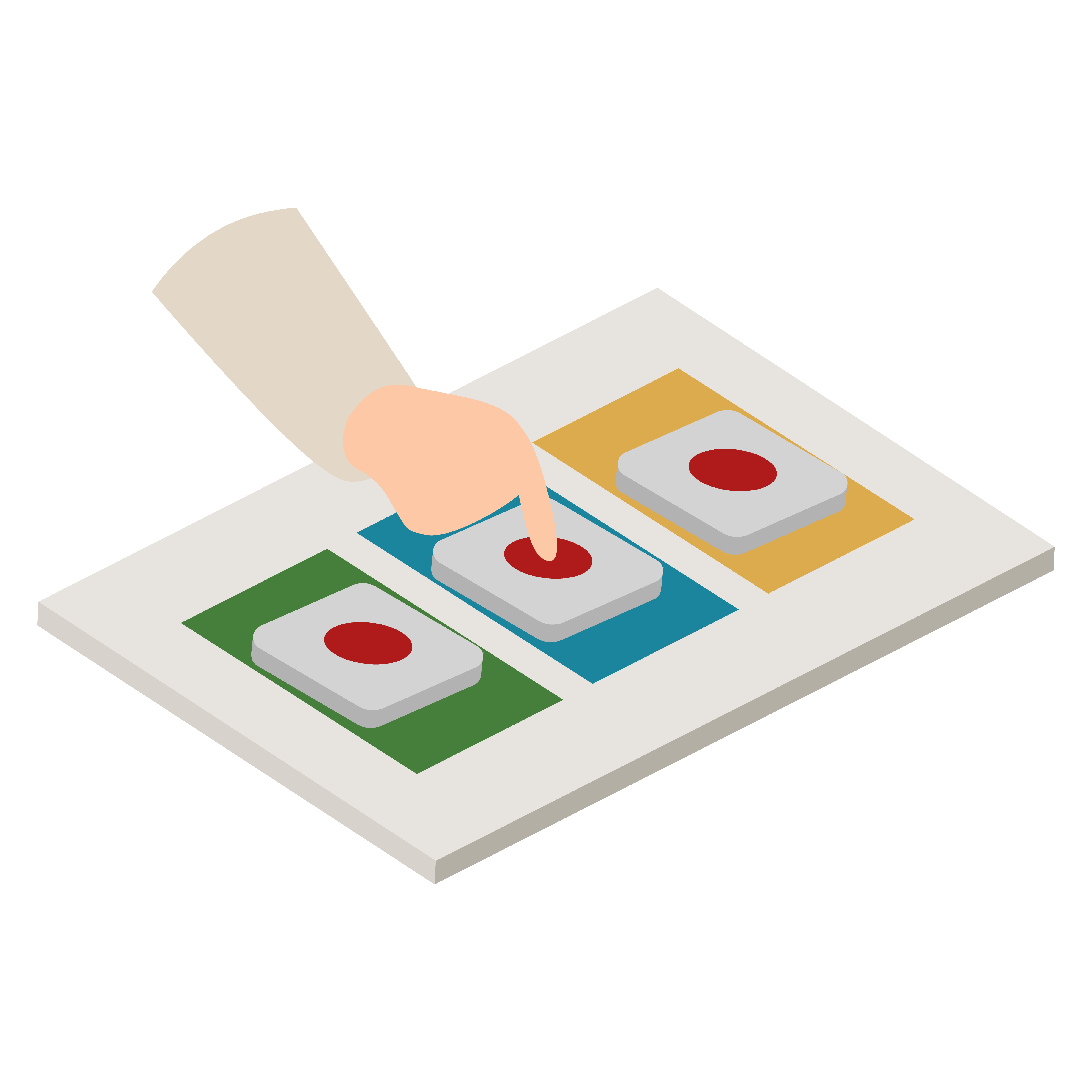
2. Alert and Management Process
When an operator detects an issue, such as a machine malfunction or non-compliance, they press the button on the call device. The signal is wirelessly transmitted to the relevant personnel, where the alert is immediately logged and displayed.
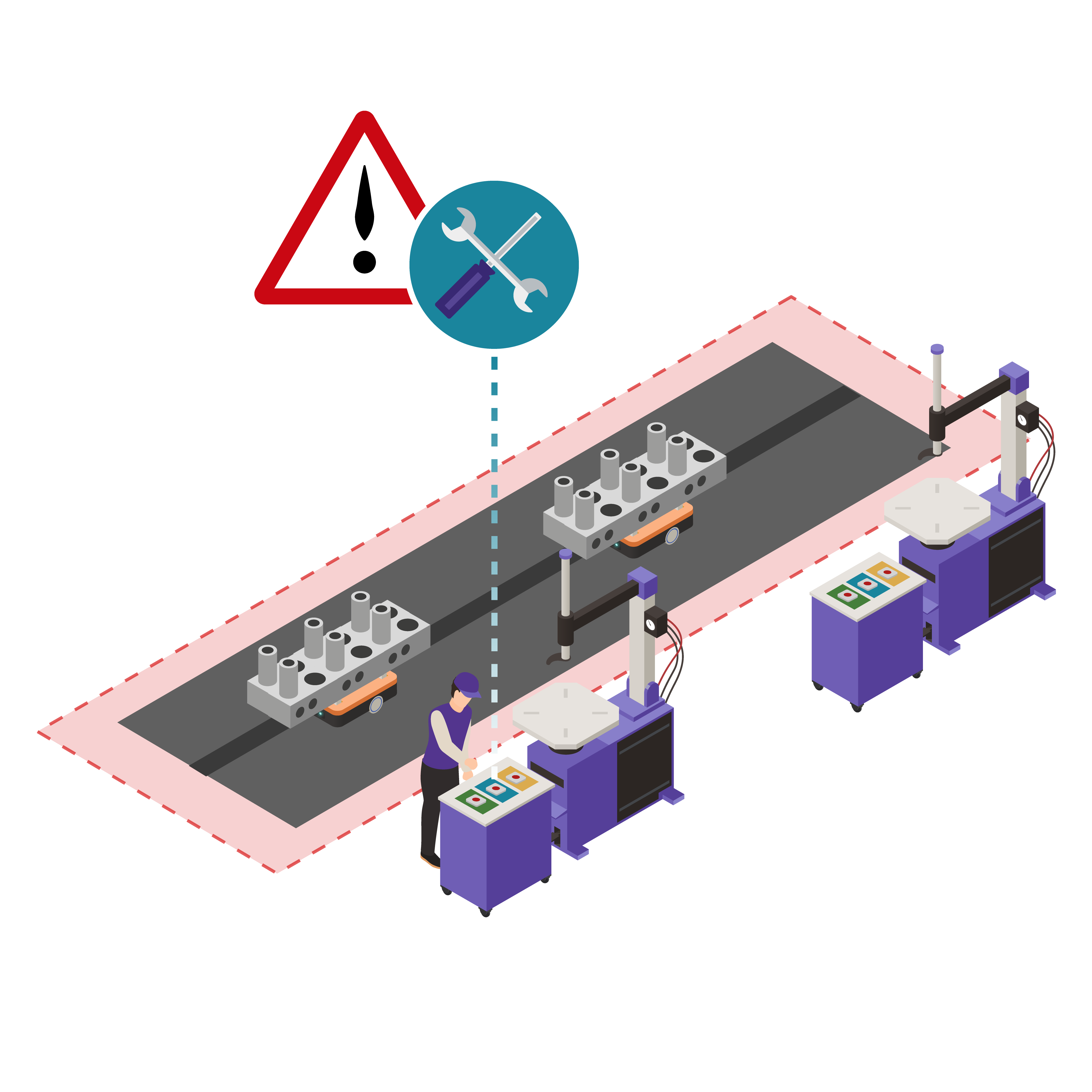
-
Categorization of Alerts: Alerts are automatically categorized, facilitating a timely and targeted response depending on the request. Categories can include maintenance calls, logistical issues, or emergencies.
-
Visual Feedback: Operators receive immediate visual feedback via the LED on the device, confirming that the alert has been received and that the request has been processed.
-
Backoffice: Each alert registered in the system enters a structured management process, viewable through a back-office application. The application allows monitoring of request progress and tracking response times, viewable via an analytics dashboard. This is crucial for understanding how to improve and optimize response times to ensure maximum production continuity.
-
Notifications: You can subscribe to various categories of alerts across different notification channels to respond quickly to requests from the field. These include: push notifications from a mobile app, emails, and more.
3. Benefits of ThinkIN’s Andon Wireless System
- Operational Flexibility: The absence of wiring allows devices to be positioned wherever it is most convenient and moved easily if work island or production line configurations change.
- Reduced Installation Costs: Installing a wireless system is less invasive and costly compared to a wired system, reducing setup times and the need for structural interventions.
- Scalability: The system can be easily expanded as production grows, adding new devices without the complexity of extending a wired infrastructure.
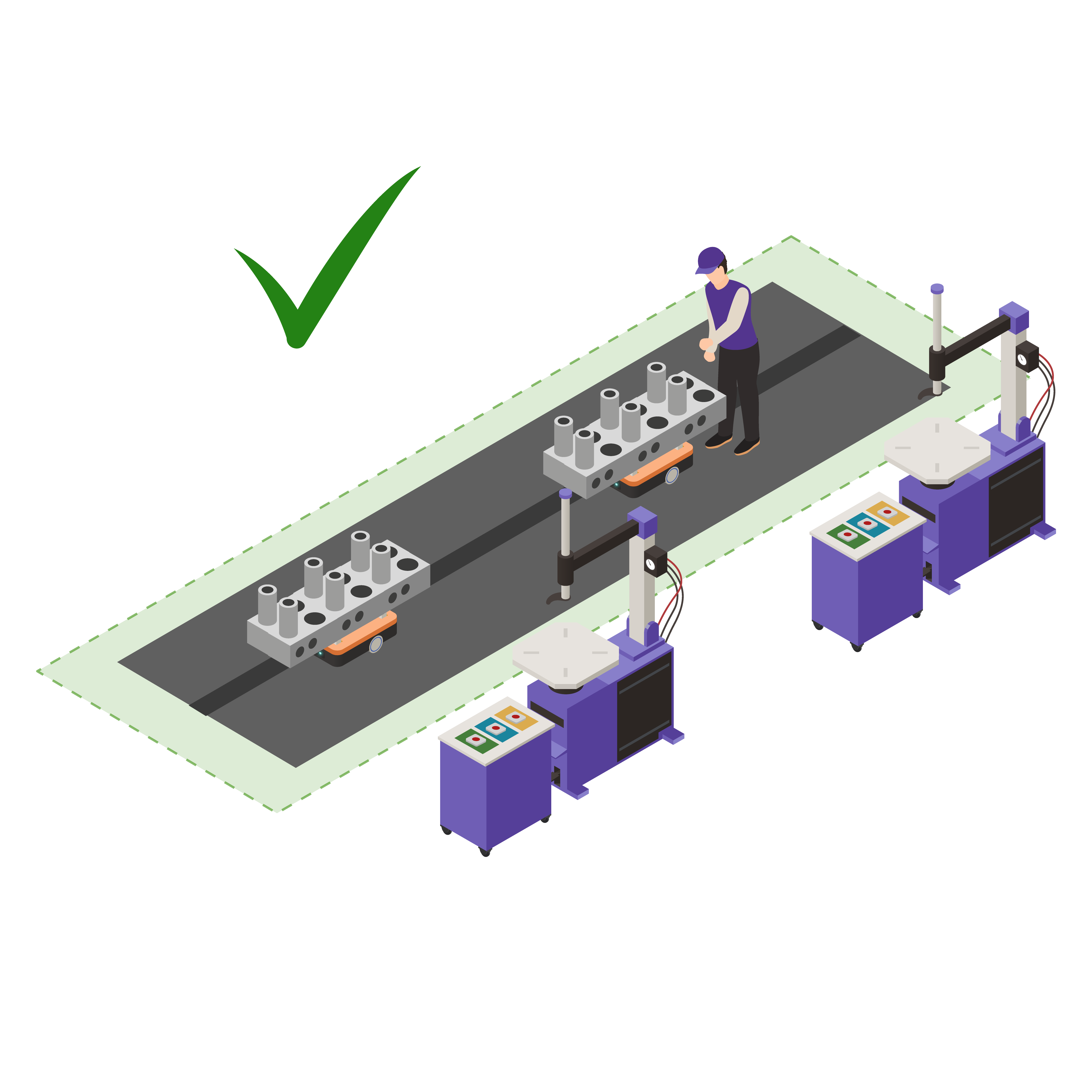
In summary
Incorporating Andon systems into production operations is a strategic move that offers numerous advantages, from improved communication to enhanced quality control. As manufacturers seek to optimize their processes and stay competitive, ThinkIN’s Andon systems stand out as a valuable tool for improving efficiency and productivity.
Are you ready to take your manufacturing operations to the next level?
Find out more and download our brochure
Don't miss your change to find out how our Wirless Andon System can make a difference in your production line
Download our brochure!
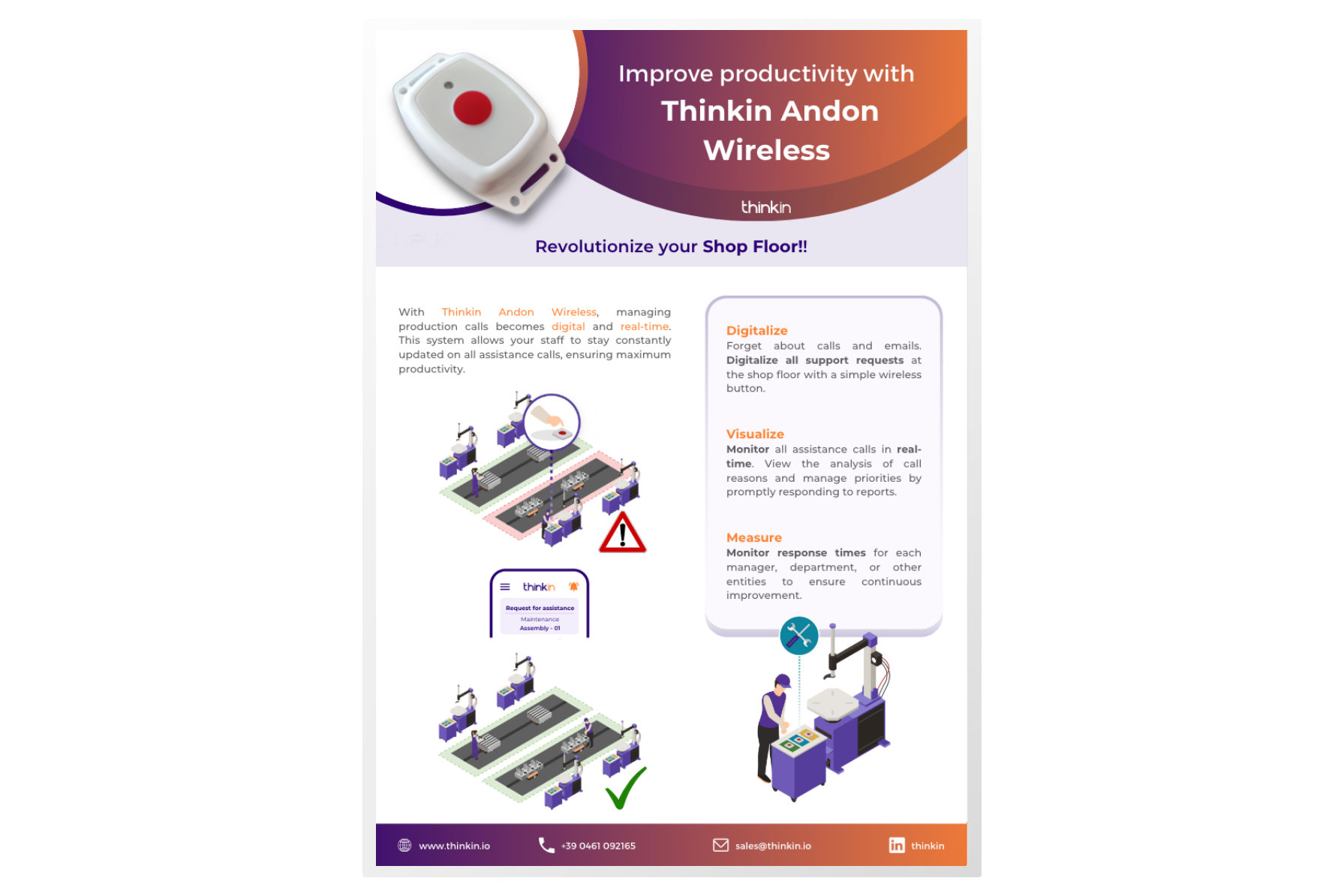