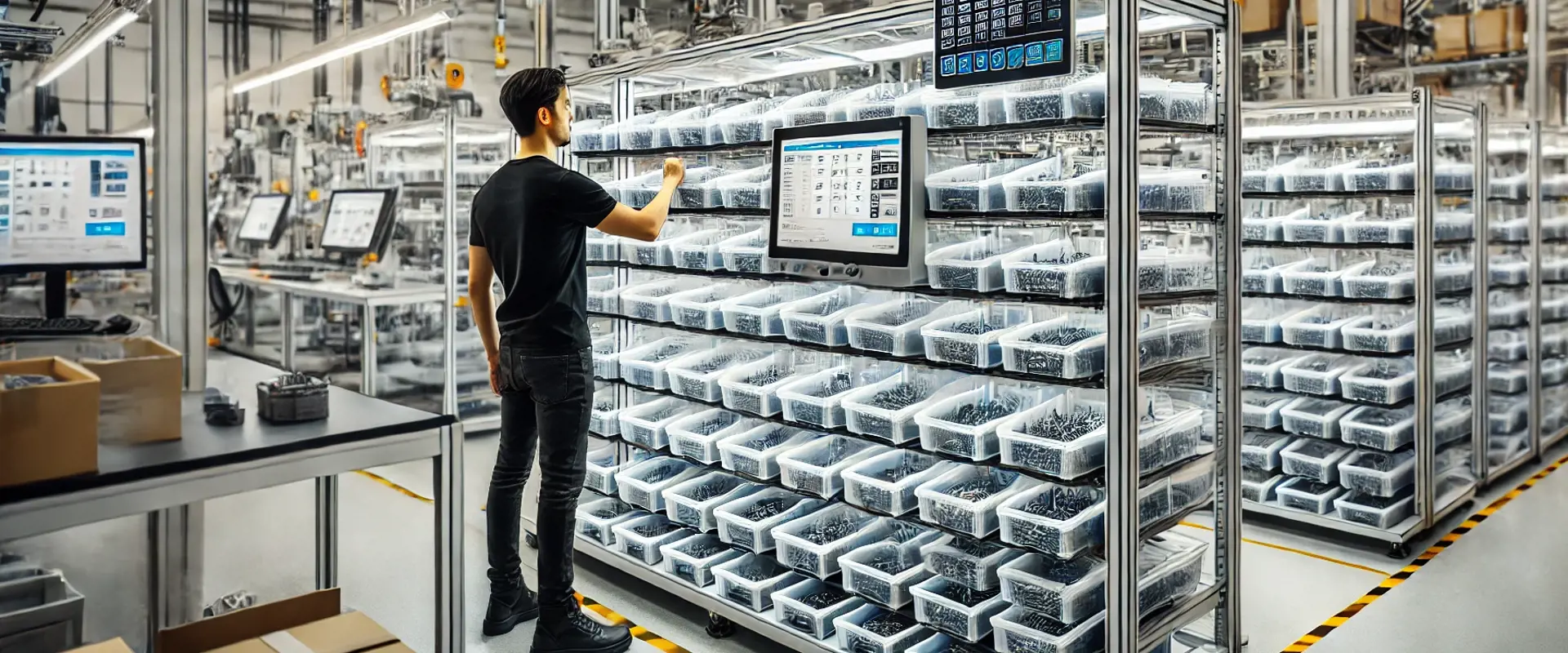
E-Kanban: The Digital Evolution That Enhances Real-Time Logistics
Imagine a Seamless Production
Imagine eliminating all inefficiencies associated with manual inventory management, knowing exactly when a component is about to run out. No more visual checks, paper cards, or phone calls. With ThinkIN’s E-Kanban, you can automate all of this and have full control over your production.
- Automates the real-time replenishment of components on the production line, reducing downtime and increasing operational efficiency.
- Provides complete visibility of stock levels, preventing interruptions and stockouts.
- Reduces costs and improves production planning through precise and reliable digital management.
What is Digital E-Kanban?
E-Kanban is an advanced system that digitalizes the traditional Kanban method used to manage the replenishment of components along the production line. The ThinkIN E-Kanban service eliminates paper cards and introduces connected digital displays that automate the replenishment process. This approach allows real-time monitoring of consumption, optimizes restocking activities, and minimizes human error.
Don't miss the chance to discover how our E-Kanban can make a difference in your production line.
Download our free brochure!
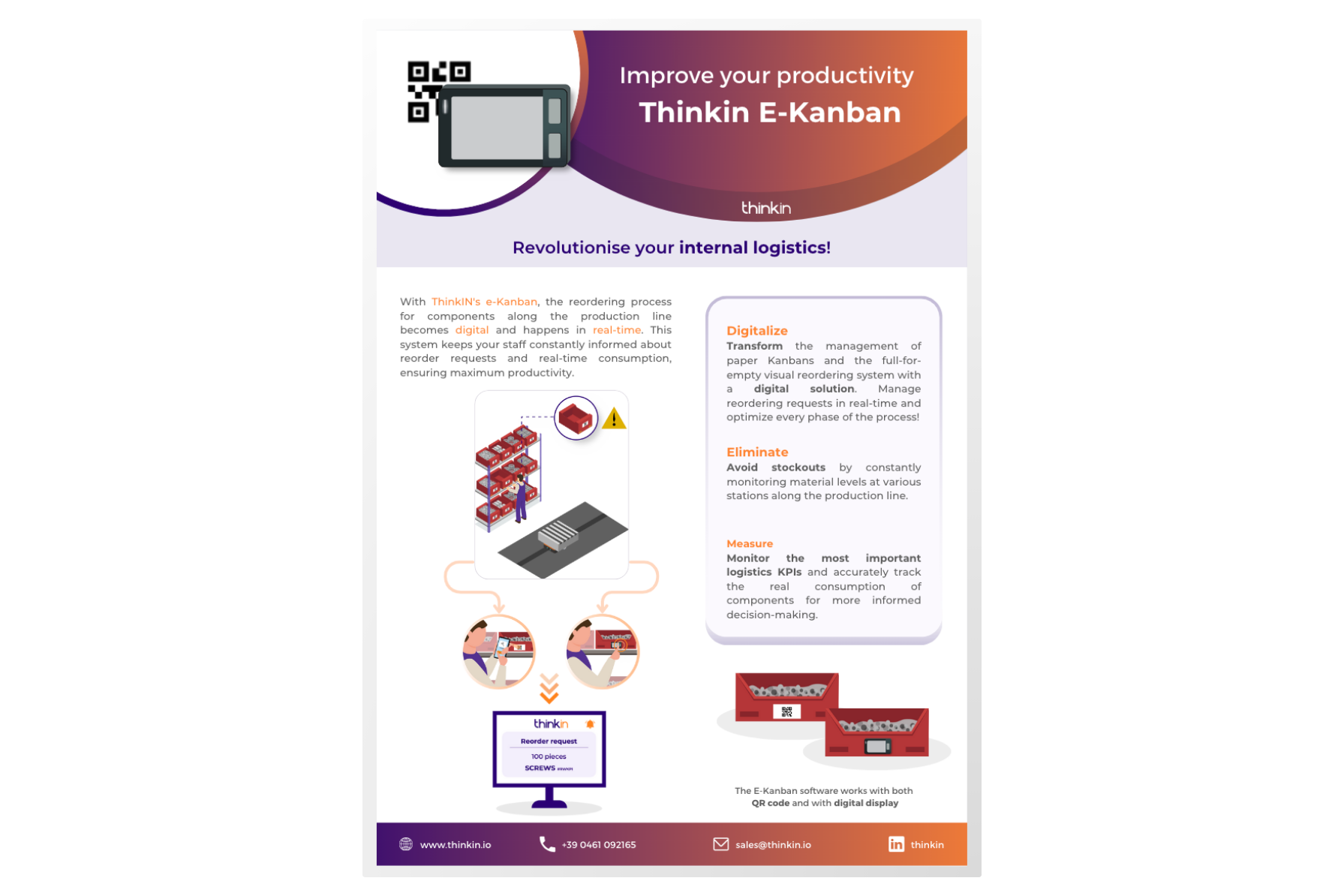
How Does E-Kanban Work with Digital Displays?
The digital displays in ThinkIN’s E-Kanban system provide a simple and intuitive interface for operators.
Here’s how the process works:
- One-Click Reordering: Each Kanban-managed reference is equipped with a customizable digital display. When a component reaches the minimum stock level, the line-side operator can press a simple button on the display to request replenishment. There’s no need to use a physical card to trigger the reorder. The request is transmitted in real time to the warehouse, where the operator immediately receives the replenishment notification, checks stock levels, and confirms the reorder through the back-office application.
- Automatic Display Update: Once the request is sent and until the replenishment is completed, the digital display automatically updates, showing the real-time status of the operation. This instant feedback eliminates uncertainty and keeps both line-side and logistics operators promptly informed about the entire replenishment process.
- Full Customization: The digital displays can be customized with the most relevant information for each component: item code, description, images, and even specific notes. The information is centrally managed and linked to the company’s ERP, ensuring data is always up to date. They also support advanced features such as "long press" to signal urgent priorities.
- Process Monitoring and Analysis: All replenishment requests are tracked and logged in a back-office application, where managers can monitor the progress of requests and analyze response times. With an analytics dashboard, managers can identify bottlenecks and optimize replenishment times, ensuring a smooth and continuous production flow.
Watch our video on YouTube: E-Kanban Service
Benefits of Implementing ThinkIN’s E-Kanban System
- Operational Efficiency: By automating the replenishment process, the system minimizes downtime and ensures a consistent material flow to the production department.
- Error Reduction: Digital management eliminates human errors associated with card handling, improving accuracy and reducing operational costs.
- Scalability and Flexibility: The system can easily be expanded to include new displays or additional features, adapting to your growing production needs.
- Increased Operator Engagement: The digital displays offer an intuitive, user-friendly interface, enhancing operator engagement and satisfaction.
E-Kanban: A Case Study from an Italian Automotive Factory
A major Italian automotive company often faced difficulties with component replenishment, still relying on paper Kanban cards. Manual handling caused delays, errors, and excess stock. Seeking to improve efficiency, the company chose to implement ThinkIN’s E-Kanban system.
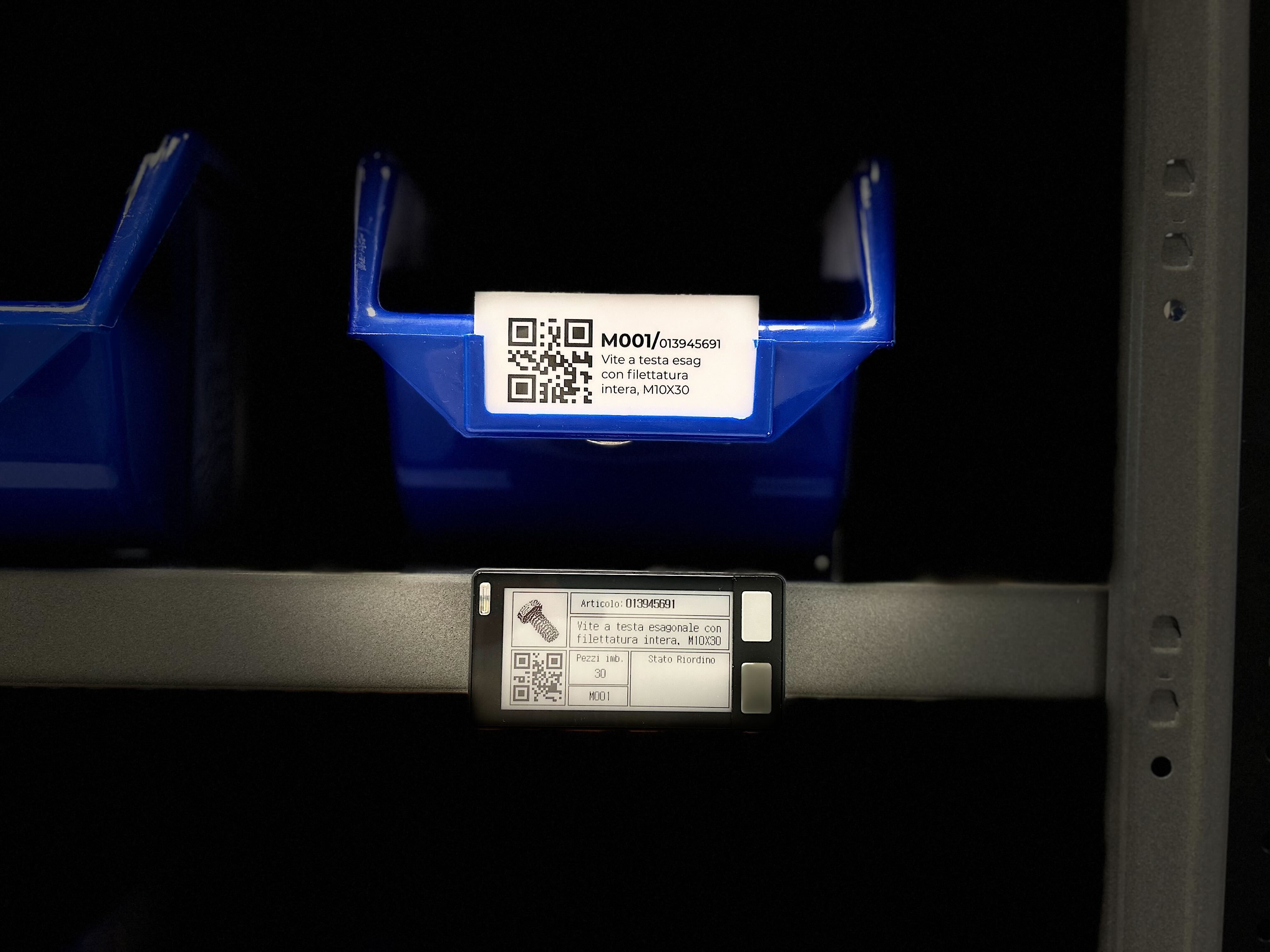
Initial Situation
Before implementing ThinkIN’s E-Kanban system, the factory used the traditional Kanban method, based on paper cards to signal component replenishment at the line side. This process required operators to move the cards to the reorder bins once the material was depleted. However, it often happened that:
- Cards were lost or misplaced, causing delays in the reorder request.
- The warehouse operator did not immediately notice the reorder cards, prolonging wait times.
- Replenishment planning was inefficient, leading to either excess stock or, conversely, stockouts that interrupted production.
This situation resulted in frequent machine downtime, delivery delays to customers, and significant waste of resources for manual inventory management.
The Solution: Implementing ThinkIN’s E-Kanban
The company decided to implement ThinkIN’s E-Kanban system to digitalize the replenishment process and improve operational efficiency. The transition was gradual, starting with a single assembly station to test the new solution and monitor the benefits. Here’s how the project was structured:
- Installation of Digital Displays: Each workstation was equipped with customizable digital displays, networked with the company’s ERP system. The displays show detailed information about each component at the workstation, including item code, description, and image.
- Automation and Instant Feedback: When an operator notices that stock levels are approaching the minimum threshold, they press the button on the display. The request is instantly transmitted to the warehouse, and the display updates in real time, indicating that the request has been received and is being processed. If the operator detects an urgency, they can use the "long press" function to signal a high priority, immediately highlighted in the ERP system with a special alert.
- Real-Time Monitoring and Data Analysis: All replenishment requests are recorded in the back-office system, where managers can view request statuses, average response times, and process bottlenecks. Thanks to an analytics dashboard, the company was able to analyze historical data and optimize warehouse planning, significantly reducing wait times.
Practical Results
In just six months, the company achieved:
- 20% Reduction in Replenishment Times: Thanks to the instant transmission of requests.
- Zero Waste: Stock levels were maintained optimally, eliminating excess inventory.
- 10% Increase in Operational Efficiency: Operators can now focus on higher-value activities.
The Logistics Manager stated: "With E-Kanban, we finally resolved our replenishment issues. It’s a practical and reliable system that has significantly improved our production process and warehouse management."
Conclusion
ThinkIN’s E-Kanban has proven to be a simple yet powerful solution to digitalize and optimize component replenishment. If you’re looking to reduce downtime and eliminate stockouts while improving efficiency, implementing an E-Kanban system could be the right choice for you.