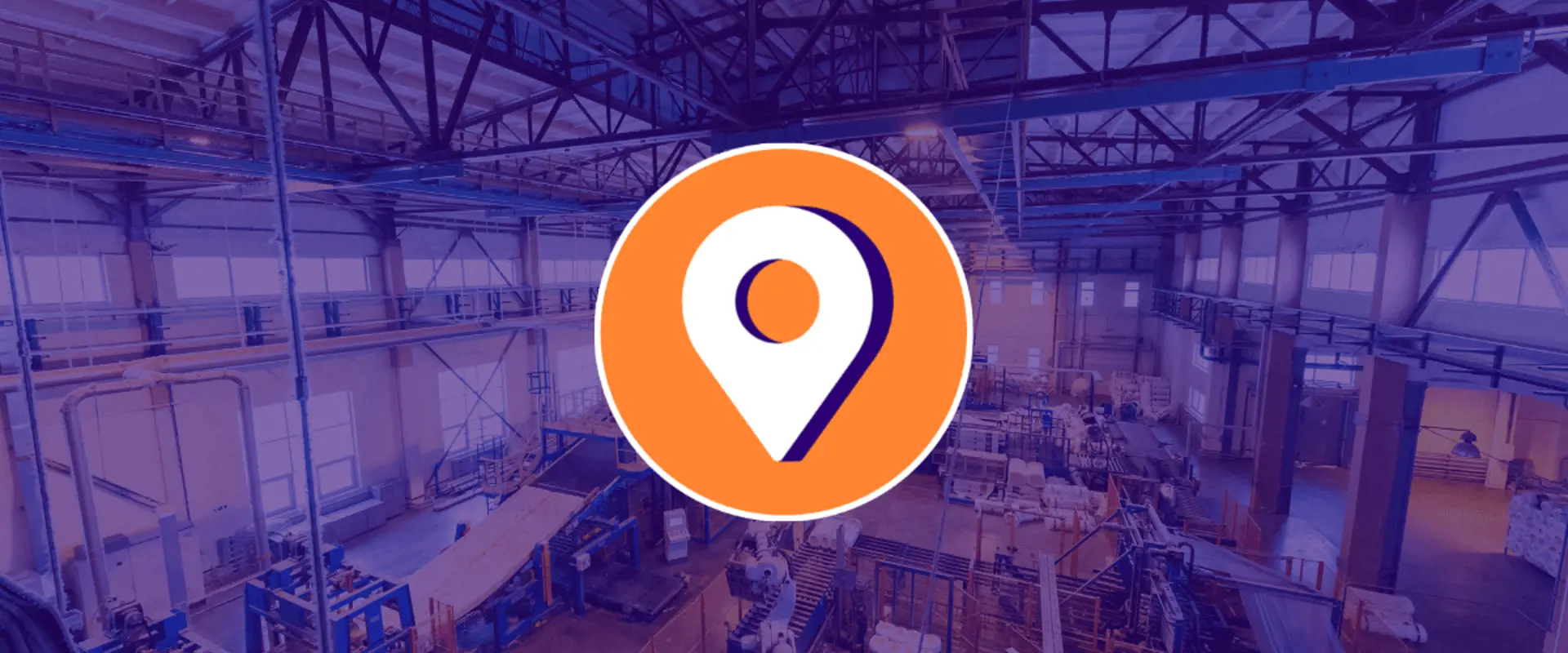
Indoor location: 5 steps to implement an RTLS project
Implementing an RTLS project: from problem to solution, in this article you will discover the 5 steps to implement an RTLS project.
- In order to implement an RTLS project we start from your problem
- It is important to choose the most appropriate technology solution for your needs
- ThinkIN supports its customers with expert assistance at all stages of the project
In our previous articles we have often told you about what indoor location systems are, what benefits they bring, and why you should start such a project. In this article, we will see what the steps for implementing an indoor location project in the manufacturing industry are.
Download our infographic with the 5 basic steps to implement an RTLS project
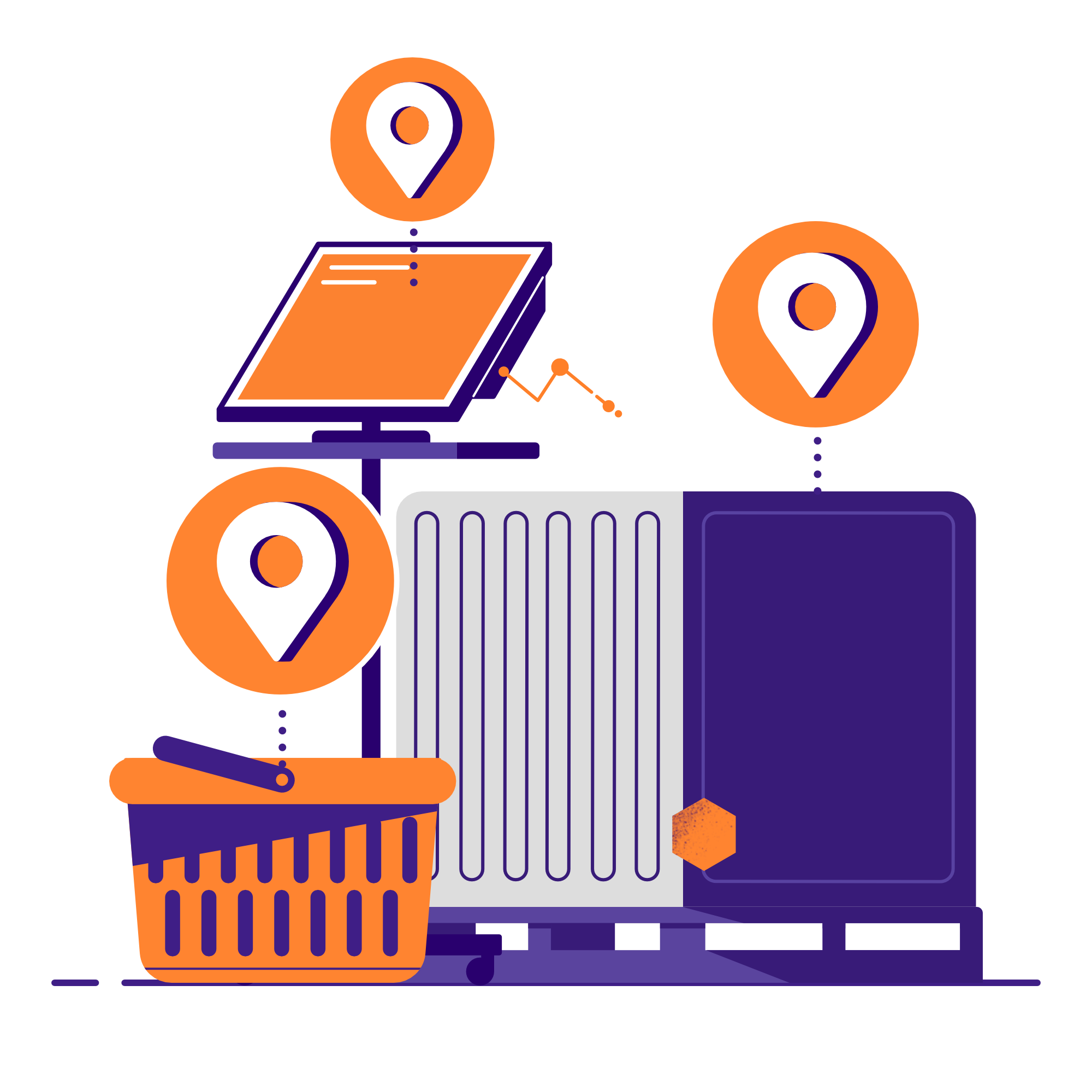
1) Problem identification
The first step is related to the identification of the problem. Usually, the Customer reaches out to us to solve a problem, e.g., they realise they have little visibility on the inventory or on the intra-logistics flows of their own warehouse, or they notice that they are little efficient in terms of productivity.
The first step consists of a workshop of a few hours, online or in-presence, during which our team of experts delves into the problems as well as necessities of the Customer, also analysing the process and the production environment. This consultation also includes a brief training on our indoor location services and technologies and how they have been successfully applied by various Clients, both in Italy and abroad, precisely to address the specific issues encountered.
Whenever possible, following the consultation, an on-site visit to the client is also organised to get a clearer and more complete view of the application scenario in which the RTLS solution will be activated.
Upon completion of this problem identification phase, a report is issued summarising the features, difficulties, and needs exposed by the Customer during the free consultation, and the main ThinkIN services that could support their resolution or mitigation are identified. These could be existing services or custom tailored to the Customer's specific need, again from the ThinkIN location intelligence platform. The report also includes a budget indication of the project implementation.
2) Solution planning
Once problems, needs and possible solutions have been identified, it is necessary to define as accurately as possible which ThinkIN services best meet the Customer's needs. Indeed, the proposal of services aims not only at responding to the specific problem exposed by the customer itself, but also to create added value on several fronts. In fact, given the nature of the services themselves, it is possible to start with a targeted solution to solve a specific problem, and then shape it in such a way that it can also bring its value in improving other areas and/or processes. For example, the solution starts with services to monitor and control production processes and then is extended with tooling management to improve production efficiency by acting on multiple aspects.
In this phase, it will therefore be crucial to involve all the key players (e.g., production manager, IT staff, etc.) in order to go into details with respect to the technical-practical aspects that the ThinkIN solution will have to satisfy, such as: possible integrations with third-party systems (WMS, MES, other), levels of customization, and the technical requirements that the localization technology will have to meet.
The design is mainly concerned with:
- The choice of the RTLS technology: based on the latency and accuracy requirements of the requested services and the specific production environment, the most appropriate location technology is chosen, given the wide range of technologies used in indoor location, such as Bluetooth Low Energy (BLE), Ultra Wide Band (UWB) and Bluetooth Wireless Mesh Network.
- The design of the services: the ThinkIN service to be provided is shown to the Customer: either through the platform, in case the need turns out to be solvable through a standard service already in the portfolio, or through fully customizable graphical representations, created for illustrative and demonstration purposes to make the customer understand how the chosen solution would come to be.
3) Project implementation and activation
With the executive design ready, the implementation phase of the project is initiated, which can be a pilot project for limited-scale or full-scale evaluation. Based on the deployment plan, we then proceed with the physical installation of the RTLS infrastructure required to deliver the service, network configuration and calibration, at the end of which the infrastructure is up and running.
In parallel, activation and initial configuration of the ThinkIN service is initiated. Any customizations or additions are made at this stage. We then proceed with modelling the production site with space annotation, e.g., delineating restricted access vs. production areas, tracked assets (e.g., production orders, work tools, forklifts) and user groups.
4) Monitoring and technical support
A fundamental element of any RTLS service solution is the active monitoring of each and every component of both hardware and software of the solution to ensure the quality of service needed by a manufacturing plant.
The ThinkIN service is able to actively monitor the proper functioning of the entire IT infrastructure, namely both the Hardware (e.g., proper functioning RTLS antennas, TAGs battery level, field devices) and software (e.g., ThinkIN services, data storage and backup). Thanks to these monitoring tools, ThinkIN's technical support is able to promptly resolve any technical problems, offering support and qualified assistance both in Italy and abroad.
Furthermore, in this phase the maintenance of the infrastructure over time is also included, with security updates, the maintenance and updating of the platform as well as the release of improved versions of both the platform and the various services.
5) Project expansion
One of the interesting aspects of the ThinkIN solution is the scalability of services from the RTLS infrastructure already installed. Indeed, by expanding the number of tracked objects, it is possible to easily activate new services, ensuring a faster return on the investment.
In the phase following the start of the project, we have regular contacts with our Customers who give us feedback on their experience, through which we ensure that the implemented solution meets their needs and produces the expected results. It is at this stage that we evaluate possible extensions of the project over time. For instance, our Customers start with the project in a certain area and after experiencing the value of the solution, decide to extend it to other areas of the facility; or they add new services from the infrastructure already installed.
Implementing an RTLS project is easy with ThinkIN. ThinkIN is an international company that implements installations with Customers all over the world, including Europe, America and Australia. This is made possible not only by our experience in the field for more than 8 years, but also by an extensive network of partners at international level and by the qualified assistance we are able to provide remotely. Learn more about our success stories here.