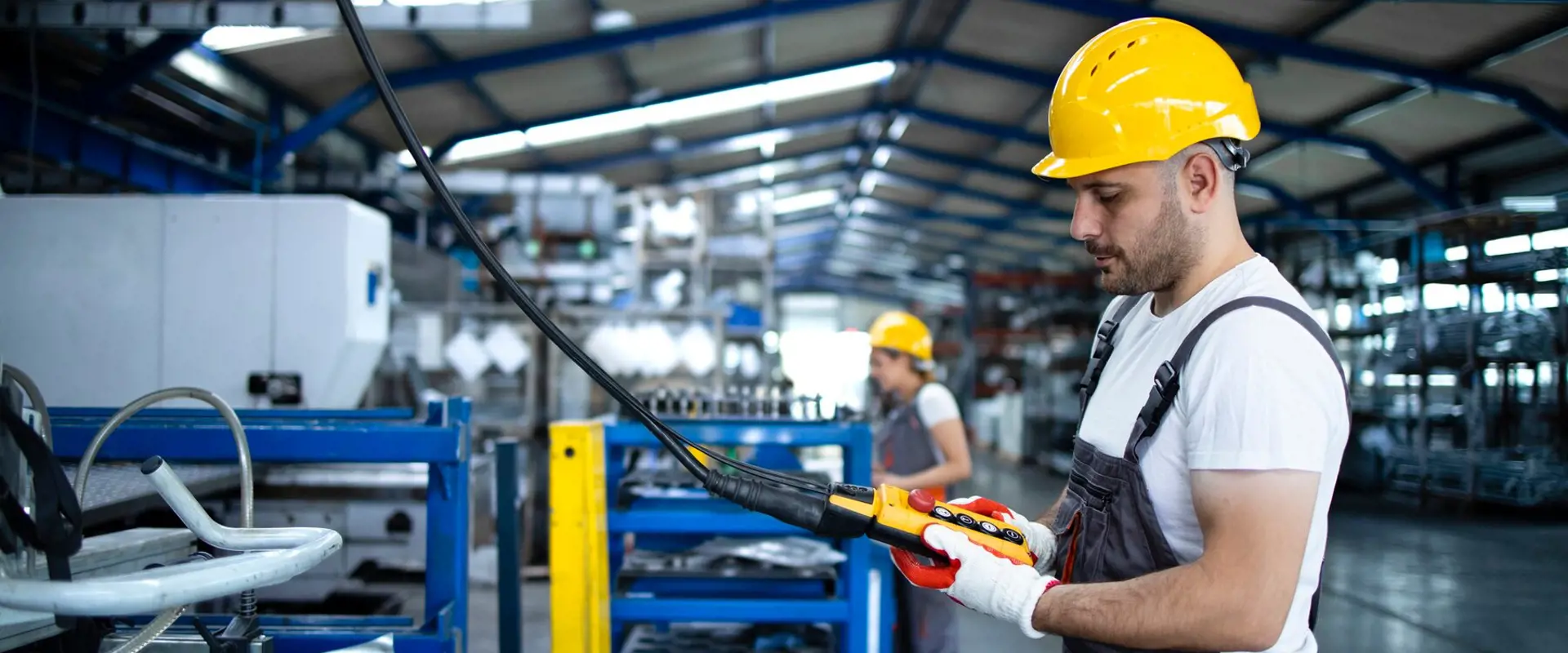
Why should you consider a Pilot Project before betting on RTLS?
The pilot project is a crucial step in many RTLS projects because it allows you to complete the design of the solution by assessing the limitations of the technologies involved in a real-world context. Find out all the aspects to consider before implementing a pilot project.
- A pilot project allows technologies to be validated in the field, reducing risks and ensuring the success of the project
- There are different types of pilot projects and their design requires in-depth knowledge of the customer's production environment
- thinkin is characterised by the possibility of testing several technologies in order to identify the one that best meets the customer's needs
The pilot project is a fundamental step in many projects to complete the design of the solution, as it allows the limits of the technologies involved to be assessed in a real context and the internal dynamics of a manufacturing company to be examined in detail, in order to gain a thorough understanding of how the proposed solution could be introduced into business processes.
The main objective is then to validate the solution in the field, in a controlled setup, reducing risks and ensuring the success of the project. In this article, we will discuss some of the key aspects to be taken into account when implementing a pilot project.
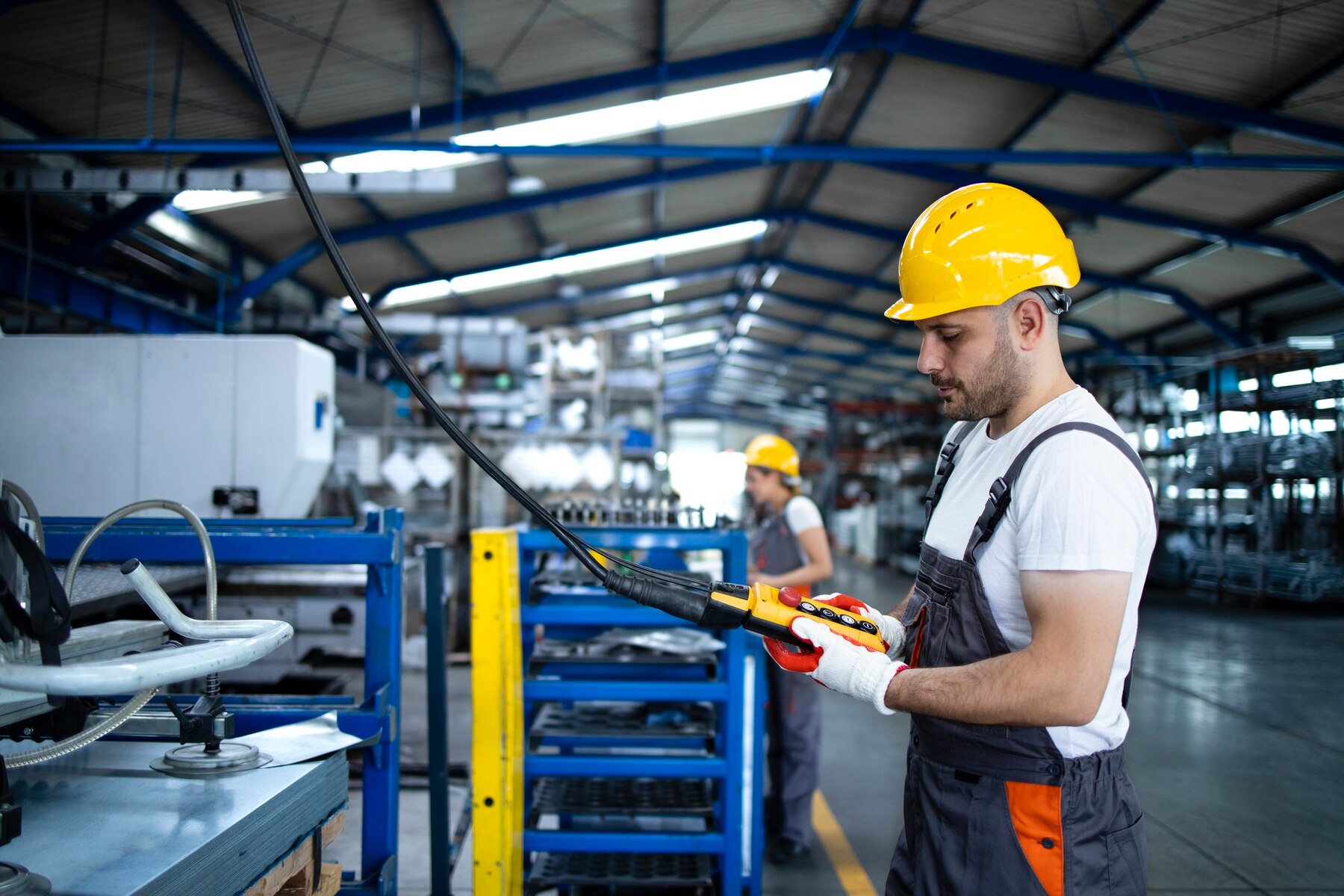
Why implement a pilot project?
First of all, he design and implementation of a Real-Time Location System (RTLS) project require a deep understanding of both the client's production environment and the processes involved, as well as necessary integrations with third-party systems.
There are numerous challenges to consider; for instance, industrial facilities are often extensive, with complexities that can impact not only the choice of the tracking system (such as highly metallic environments, enclosed spaces) but also its deployment (e.g., network wiring, wireless connectivity). Having the opportunity to field-test one or more technologies allows for understanding potential limitations and lets the client experience a portion of the solution firsthand.
Simultaneously, it provides a chance to finalize the design of the RTLS infrastructure, defining the executive project that takes into account both the installation positions of individual antennas and the necessary wiring work required to connect them (when needed).
A second aspect concerns processes and the usability of the system. Solutions like those offered by ThinkIN impact existing processes by introducing tools capable of enhancing efficiency. Naturally, this presupposes a thorough understanding of how a particular company operates, to discern where and how to introduce specific services, with which interfaces, where to create automations, and so on.
The main goal of this study is to ensure the adoption of the technology by all involved parties, preserving normal operations and gradually providing benefits over time.
Finally, a last aspect involves integration with third-party systems, whether it be Manufacturing Execution Systems (MES), Enterprise Resource Planning (ERP), or Warehouse Management Systems (WMS). In (almost) every project, our service interacts with existing management systems that we need to integrate with.
It is, therefore, necessary to have a deep knowledge of the present management system, any customizations made, and especially the integration method (APIs, frontier tables, etc.).
Being able to experiment in the field is, therefore, the best way to test one or more technologies, understanding which one can best meet the project's needs, taking into account possible future scenarios. Often, all of this proves to be preparatory to the final offer to ensure the successful implementation of an RTLS project.
Types of pilot projects
Depending on the needs, it is possible to plan three types of pilot projects, each aimed at a different objective. The various phases are consecutive to each other, although not necessarily always present.
- Demonstration Project: In this case, the objective is a simple demonstration of the technology, going beyond what has already been presented through presentations and documents.
This typically involves a very limited temporary installation, lasting a few days (or even just one). This is especially targeted at clients who are completely new to the technology and need to understand it first, internally conveying its understanding to other functions. - Pilot Project: This is a project with the goal of validating the technology in a real environment, addressing some of the open points and laying the groundwork for a final project.
The typical duration of such a project can range from 3 to 6 months (best practice), and the installation could become permanent if the project is successful. - Production Pilot Project: Sometimes, as a natural subsequent phase to the pilot project, a "production pilot" phase is initiated, taking a further step forward by piloting some steps in the direction of production.
Examples of these steps may include integration with the management system, modification of some internal procedures, or some process automations facilitating specific activities.
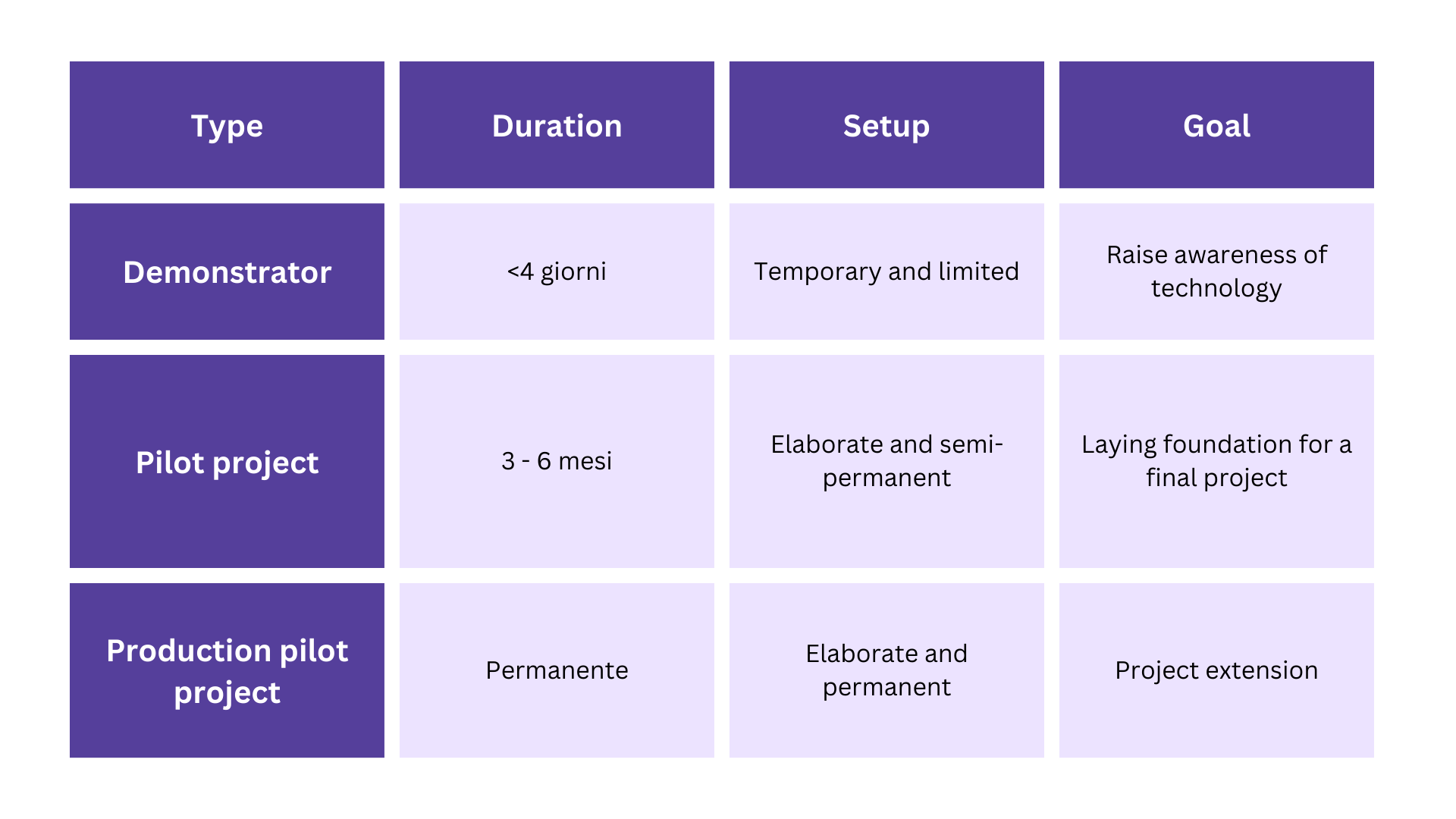
Planning the pilot project
To ensure the success of a pilot project, it is crucial to consider all the mentioned aspects. Planning, in particular, requires careful attention to all the elements crucial for achieving the project objectives. Some factors to consider include:
- Define Objectives: Often, a pilot project is initiated to address specific questions or uncertainties. It is, therefore, crucial to collaborate with the client to define the pilot's objectives and any metrics to be monitored.
These metrics may serve to instill confidence in the client (e.g., location accuracy) or highlight certain automations to be enabled (e.g., entry/exit from work zones).
Objectives are not exclusively technological but may also involve estimating the project's impact, such as defining a return on investment model, estimating potential efficiencies, enhancing safety, reducing operational costs, and so on. - Evaluate One or More Location Technologies: The pilot project often provides an opportunity to experiment in the field. Allowing the client to test technologies with different characteristics can be useful in identifying the one that best meets the project's needs.
There is often no superior technology; rather, there is one that more effectively adapts to the specific requirements of a particular application context. Experimenting with different options in the field guides the client through this process. - Identify a Representative Scenario: To maximize the effectiveness of a pilot project, it is essential to identify a sufficiently representative scenario in terms of the industrial environment (e.g., the department), the process, and the involved parties.
This maximizes the effectiveness of the various tests to be performed and, more importantly, involves relevant business functions from the outset in co-designing the solution and introducing it to the company. - Plan Activities in Advance: Manufacturing companies, especially in production and maintenance departments, are always busy. It is, therefore, fundamental to plan the pilot project well in advance, ensuring that various business functions allocate the necessary time and reserve any required activities (e.g., the maintenance team for ceiling antenna installation).
- Simplify: To initiate a pilot project as soon as possible, the aim is to simplify aspects that could be lengthy and complex for the client to manage. For example, bringing a 4G router to avoid relying on the client's network or having a local installation can help bypass formal IT department approvals, potentially saving a significant amount of time.
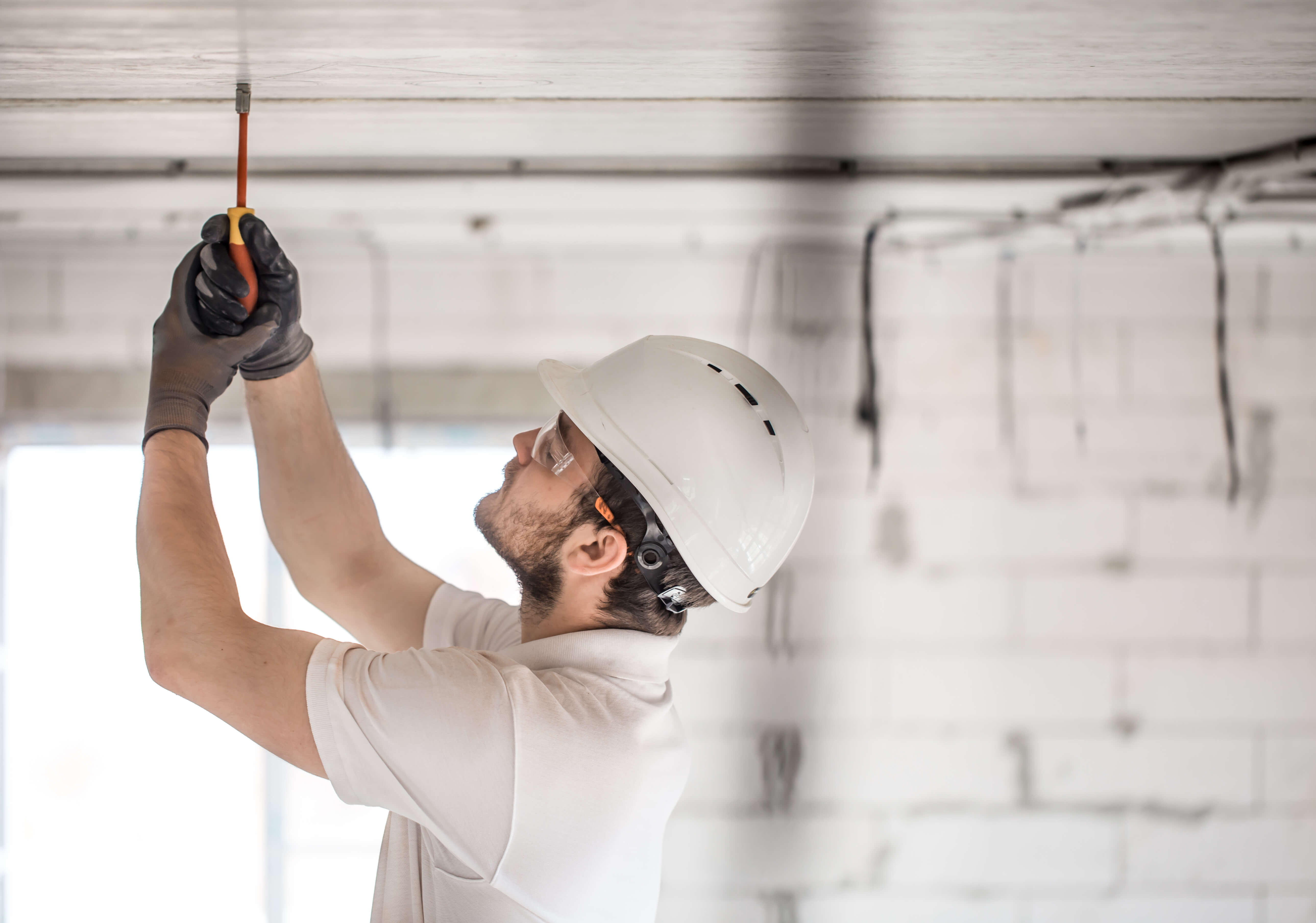
Implementing the pilot project
If the pilot project planning has een properly organized, the implementation phase follows naturally. The starting point is the deployment of the location infrastructure, from which the services to be validated derive.
Once the installation and calibration phase is complete, the data collection and service phase can commence. In the case where the validation of the RTLS infrastructure is one of the pilot project objectives, it is necessary to measure the quality of the obtained data, for example, in terms of location accuracy and reliability, and potentially organize a demonstration with the client.
Following this phase, it is crucial to immediately engage with our clients to thoroughly understand the production process, identifying and documenting all the various stages, current challenges, and especially where human factors lead to errors, time wastage, or delays.
These are typically aspects where location systems can contribute. The objectives of this analysis are diverse:
- Understand Our Clients, Their Processes, Industrial Environment, and Current Challenges
- Lay the Foundation for Return on Investment Calculation
- Understand and Model Present and Future Scenarios: As already mentioned, solutions based on IoT and tracking technologies are based on an RTLS infrastructure.
In conclusion, the pilot project proves to be an essential component in the implementation strategy of RTLS solutions, allowing for experimentation and validation of technologies in real-world contexts. Through careful planning and a well-structured implementation phase, various development and expansion prospects for the project emerge.
One possible concluding scenario involves extending the pilot project to the entire facility, enabling complete coverage and a more in-depth assessment of business dynamics. This further step maximizes the impact of the technology, optimizing processes, and improving business efficiency on a large scale.
Another scenario may consider expanding the project to a specific part of the facility, focusing on critical areas or specific processes that require targeted implementation. This approach allows for greater precision in optimizing and refining the proposed solutions.
Furthermore, one could consider an additional test or pilot project in a different context, such as another corporate location or a different industry sector. This diversification enables adapting the technology to unique scenarios, expanding the application's scope, and demonstrating the flexibility of RTLS solutions.
Regardless of the chosen concluding scenario, continuous collaboration with the client is crucial. Through open communication and sharing experiences gained during the pilot project, the maximum benefit for the company can be ensured. In summary, the pilot project not only plays the crucial role of validating the proposed solution but also opens doors to new growth and optimization opportunities.
The adaptability of RTLS technologies allows exploration in various directions, guided by the goal of providing tailored solutions that fully meet the specific needs of the client. With years of field experience and a vast network of clients and partners with over 100 installations worldwide, thinkin offers expertise. Contact us for a free consultation!