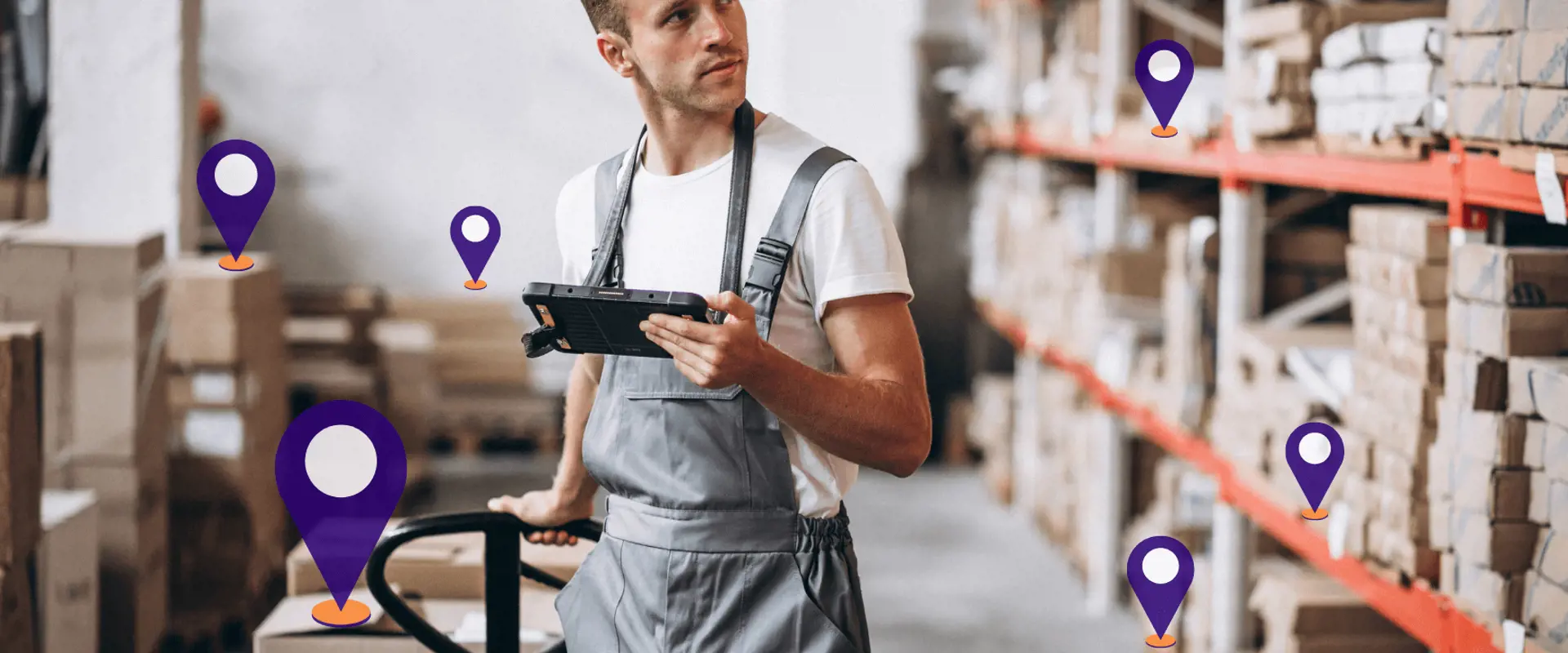
The importance of Asset Tracking in manufacturing
Manufacturing companies might face several challenges related to the inefficiencies of the production plant. Asset tracking helps organisations to enhance the overall efficiency and performance. Learn more in the article below.
- A digital twin of the manufacturing plant allows real-time control over the entire facility
- Inefficiencies like production delays and misalignments are reduced
- Workflow and overall performance are optimised
Imagine that your production plant is entirely optimised, efficiency scores cannot be better, as well as performance levels. Does it seem utopia? NO, Asset tracking can do this!
Asset tracking has become very popular in the last few years, as more and more companies understand the value that this technology can provide to their business.
What is Asset Tracking?
Asset tracking is a system that allows a manufacturing company to track assets within its production plant, thus ensuring full and real-time control over the entire facility. Asset tracking is enabled by Real-Time Locating Systems made up of small devices, called TAGs, installed on the assets to be tracked. While moving, these TAGs send the location signal to other devices (i.e. the receivers) that, in turn, send the real-time data streams on the location of tracked resources to the gateway.
What is possible to track? Basically anything that moves inside the factory can be digitised, located and tracked in order to know its location and state along the production process. This includes, as an example, job orders, forklifts, raw materials, semi-finished goods and pallets. Workers too, equipped with different types of TAGs (e.g. badges, bracelets), can be located for safety or social distancing and contact tracing reasons.
Why is Asset Tracking so relevant in the manufacturing industry?
Asset tracking can be an extremely helpful tool in each industry, wherever there is the need to locate something that has been lost or to have a better control of the process. However, it is of particular relevance in the manufacturing industry. Indeed, in the manufacturing industry, production cycles are generally complex and characterised by thousands of materials, goods, semi finished goods and parts moving within the facility and crossing several areas. Therefore, assets might be forgotten for long periods of time, not be in the right place at the right time or, in some cases, even lost. These complex settings of the industrial process suggest that any missing or lost component inside the facility can severely affect the production cycle, resulting in:
- heavy delays in production, possibly causing a lead time increase
- labour hours wasted in manual asset searching across the facility
- workers picking up the nearest job, without prioritising the most important
- misaligned planning and scheduling.
Asset tracking can become very handy to solve all of these challenges faced by companies in the manufacturing industry.
From Asset Tracking to Digital Twin
You’ve just learnt what asset tracking is and why it is extremely relevant in manufacturing, but you may be wondering what can I do next?
It’s right you need more than RTLS and its dot on the map. To benefit from research functionalities as well as notifications and analysis with all the relevant data on the production process, the RTLS technology has to be complemented with a software and its location-based services.
The Digital Twin of our solution works as it follows:
Starting from different RTLS technologies to locate industrial assets with configurable accuracy and in real-time, ThinkIN creates a Digital Twin of the manufacturing plant where every asset is digitalised and visualised on an interactive dashboard.
ThinkIN processes the stream of these location data and provides services, such as:
- process monitoring and control;
- tooling management;
- warehouse management and intra-logistics;
- safety
The Digital Twin therefore becomes a powerful tool to enhance performance in business processes.
The tangible value of digitalisation
So, what is the tangible value provided by the digitalisation of the manufacturing plant?
Over the years, digitalisation and Industry 4.0 technologies (for instance IoT, analytics and intelligence) have proved to enhance the efficiency of manufacturing processes unlocking substantial value through reduction of costs and increased efficiency. For instance, improvements from 15 to 30% have been recorded in labour productivity, from 10 to 30% in throughput increase and 30 to 50% in reduction of machine downtimes.
It is in complex shop floors, such as those of manufacturing companies (e.g. automotive, aerospace, electronics), that digitalisation and Industry 4.0 can truly support manufacturers in optimising their operations and enhance the level of automation in their production processes. To achieve these goals, a Capgemini report clearly states that “they need smart, interconnected systems as well as visibility into operational performance”.
With the ThinkIN solution in place, workers and plant managers have at their fingertips a digital representation of the factory, starting from RTLS and asset tracking, that allows them to have full visibility and real-time control over the production process. With this digital support (the dashboard can be indeed visualised on any portable device), workers can easily find assets and raw materials, know their production status and prioritise the jobs in line with planning and orders’ scheduling. Moreover, real-time notifications can be enabled if materials enter wrong production phases or areas, in order to avoid errors and improve lead times. Learn more about the value ThinkIN has unlocked at some Clients’ manufacturing plants.