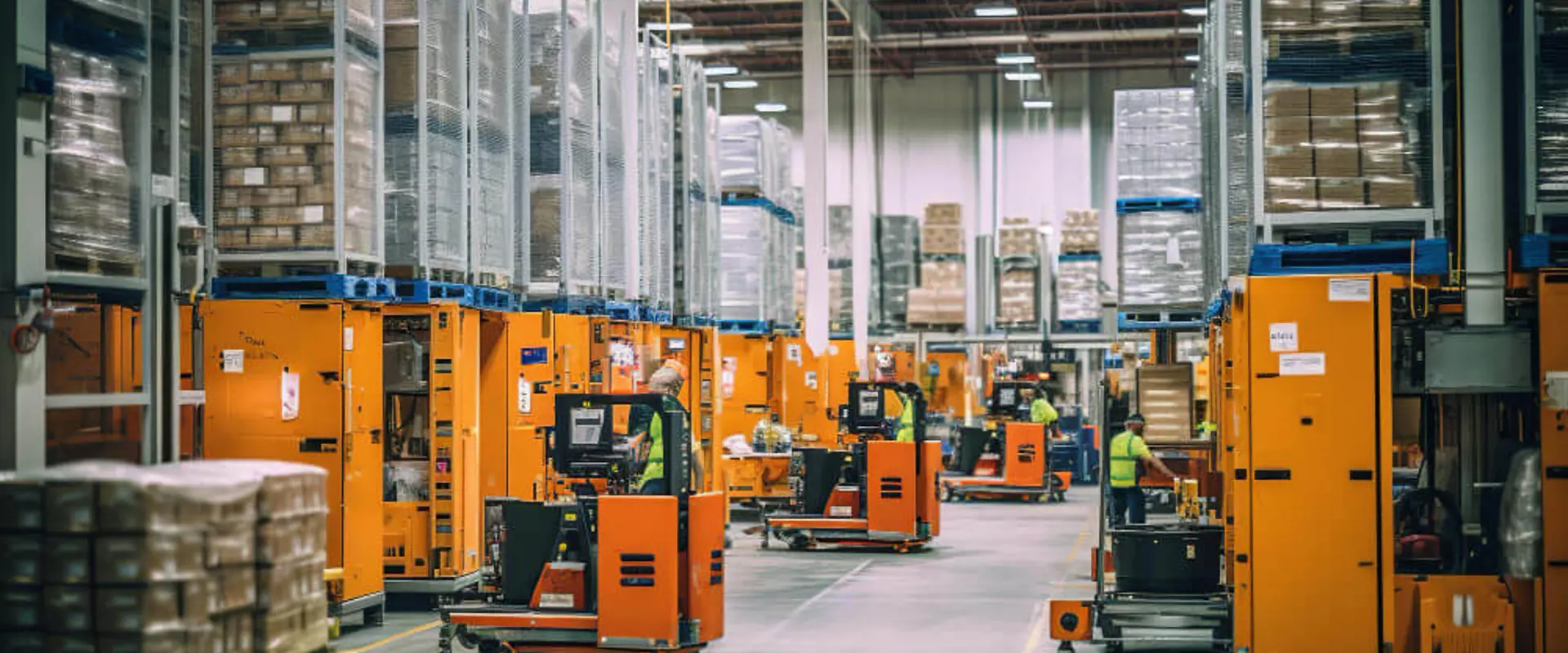
Manufacturing and digital transformation: the potential of RTLS-enabled services
RTLS systems revolutionise manufacturing with benefits such as real-time control and digitisation of production processes through indoor localisation. These scalable and interconnected services support production, warehouse management and safety. The interconnection between services provides a comprehensive view and improves operational efficiency, making RTLS systems essential for success in modern manufacturing.
- RTLS systems are scalable and flexible over time
- There are numerous applications enabled by indoor localisation that support various figures within a plant
- Software services are interconnected in a platform that communicates with other enterprise systems to provide increasingly comprehensive information.
RTLS systems are revolutionising the world of manufacturing, bringing important benefits on several fronts within the factory. This is made possible by a wide range of applications enabled by indoor localisation, interconnected in a single platform that allows a production process to be digitised from what happens in production. In fact, indoor localisation links the physical world to the digital world, creating a digital twin that allows complete control and visibility in real time over everything that happens inside the factory, bringing with it important advantages in terms of efficiency and production monitoring.
Given the wide range of services on offer, it is essential to be in a position to make an informed choice on the most appropriate services, based on one's needs and above all having a vision of what could be introduced over time. In this article, we will give a general overview of services in manufacturing, highlighting their benefits, use cases and their ability to be integrated and interconnected.
RTLS systems in manufacturing
RTLS systems in the industrial environment are characterised by their remarkable scalability and flexibility, making them an ideal solution for today's constantly changing world. In fact, once the hardware infrastructure has been installed, software services can easily be added at a later stage, with limited cost. The RTLS system is therefore able to adapt to current and future needs of businesses, growing with the business and expanding incrementally to cover more and more assets and work areas.
Given the wide range of services on offer, it becomes essential to have an overview of what services can be enabled by indoor localisation, going beyond one's own area of competence and possibly involving other company figures in this type of evaluation. In fact, there are numerous applications enabled by indoor localisation that improve efficiency and safety in various industrial contexts. Let us look at some of them:
- Monitoring and control of resources and processes: the ThinkIN® solution makes it possible to locate and track every resource (goods, pallets, semi-finished products, forklifts) in an industrial plant in real time, monitoring the use and movement of the tracked resource, reducing downtime and potential delays, and promoting full visibility and control of industrial processes. The analysis of this data allows the generation of reports and analytics, enabling the company to make informed decisions to optimise processes.
- Tool management: in the context of tool management, ThinkIN® offers a significant advantage. The solution makes it possible to improve the management of work tools (tools, power tools, presses, moulds, etc.), monitoring their movement, detecting any situations of non-compliant use and providing analyses of their use, by category and production area.This makes it possible to quickly locate instruments and analyse their use, reducing unnecessary investments and better coordinating maintenance activities.
- Warehouse and intralogistic flows management: another very frequent use case is related to dynamic warehouse management. ThinkIN® allows the tracking and tracing of forklifts, pallet trucks and overhead cranes.Real-time data, as well as historical data, provide complete real-time visibility of warehouse status and incoming and outgoing flows. This makes it possible to track material storage, streamline handling operations and achieve dynamic and flexible warehouse space management.
- Workplace safety: applications enabled by indoor localisation also extend to workplace safety. Beginning with the tracking of vehicles and people, ThinkIN® provides access control and monitoring services for vehicles and workers, allowing access to specific areas of the plant to be controlled, sending alerts to security personnel, and mitigating risky situations such as lone working and collisions between moving vehicles and workers, and signalling emergencies such as man-down.
The wide range of applications enabled by asset tracking includes a diverse set of technological solutions aimed at improving efficiency and safety within industrial environments. These applications are used on various fronts within the plant and support different corporate functions:
- Production managers: through the tracking of semi-finished products and production orders, the system provides complete control and monitoring over processes, allowing the identification of bottlenecks, possible areas for efficiency gains, as well as delays or standstills caused by overloaded processes.
- Warehouse managers: by tracking the movement of goods, materials and semi-finished products, the system provides complete real-time visibility of inventory and incoming and outgoing flows, enabling visibility of goods storage, optimisation of handling operations and dynamic and flexible management of warehouse space.
- Safety managers: thanks to the control of access to restricted or dangerous areas, as well as the prevention system against the risk of collision between operators and moving vehicles, the safety manager is notified in case of irregularities or emergencies. This makes it possible to prevent risks arising from non-compliance situations.
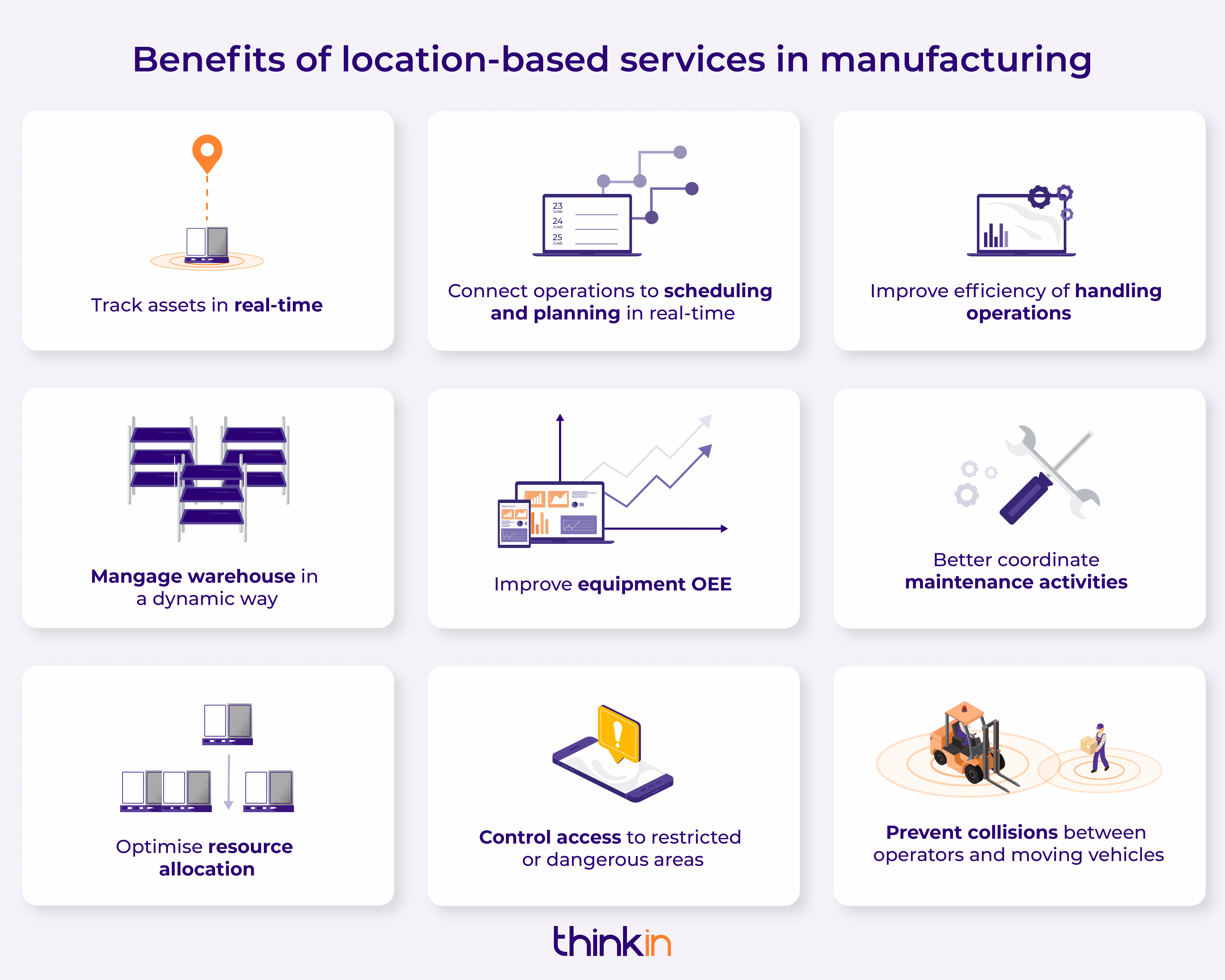
A suitable example is the case of our UK manufacturer client who started with an asset tracking solution, later integrating fully customised services related to process control and monitoring. This way, the company not only gained significant efficiencies in the tracking of numerous tracked assets, but also integrated the possibility of optimising resource utilisation and entire production processes.
It is important to know that these services are highly interconnected and give rise to a true ecosystem. Indeed, they can communicate and share data within the platform and with other business applications, creating a network of information that is easily accessible anywhere in the system. This interconnection enables a seamless flow of data between location services and other business applications, such as inventory management, logistics, security and more.
For example, a work order, such as a production order, may need two applications:
- process management, which lets you know at what stage of the process you are, through process control and monitoring - for example, a given part is entering production.
- tool management, which lets you know which tool is needed to complete the work order - for example, a certain type of screwdriver.
Therefore, thanks to the strong interconnection among services, given a production order one can know not only what stage of production it is in, but also what tools are needed to complete it. Of course, the applications enabled by indoor location allow for complete customisation based on specific customer requirements. For example, for a certain type of part, it may be necessary to be able to select the 'wrong' tool, i.e. a tool other than the one that is used by default. This can happen for various reasons, e.g. if the tool is too powerful or too weak for the production of a given product. In fact, it may happen that a given part requires, for example, a certain type of screwdriver. Applications enabled by indoor localisation, such as those related to tool management, allow this type of case to be dealt with as efficiently as possible.
In conclusion, RTLS systems are a key resource for digital transformation and optimisation of operations in the manufacturing sector. The diversity of applications enabled by indoor localisation offers a wide range of benefits, ranging from increased efficiency to improved workplace safety, from precise inventory management to monitoring of production processes. The synergy between services improves operational efficiency and provides a more complete picture of business operations. Ultimately, the scalability, flexibility and interconnectivity of RTLS systems make them a fundamental asset in the modern industrial environment, able to adapt to changing challenges and significantly improve business performance. Companies that embrace this technology are ready to meet future challenges with greater competitiveness and success. Contact us now to find out which applications can support your business efficiency.