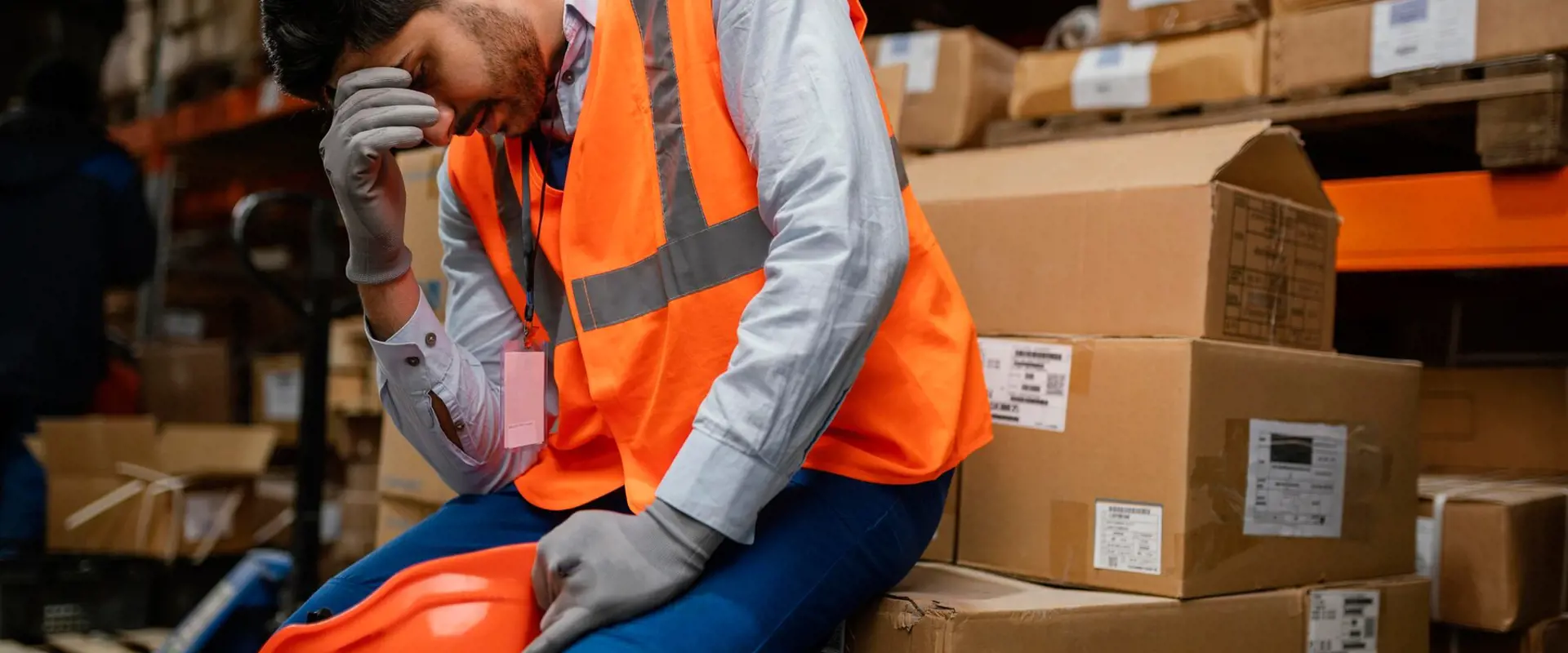
Would you be able to calculate how much time you spend each day searching for a lost batch?
Have you ever wondered how much time you spend each day searching for lost batches in a hectic business environment? A study conducted on 120 Italian manufacturing companies reveals that 76% lose about 2 hours a day searching for essential items, impacting productivity and causing stress. Explore practical use cases and envision a future where the time spent on searches is utilized in more meaningful activities.
- Understand the impact of time loss in searching for lost batches
- Discover IoT technological solutions tailored for you
- Explore the three main use cases
A study conducted by us
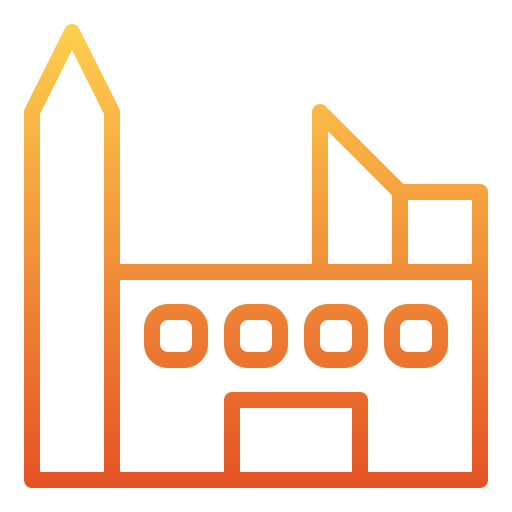
In the Italian manufacturing sector, and of medium to large size.
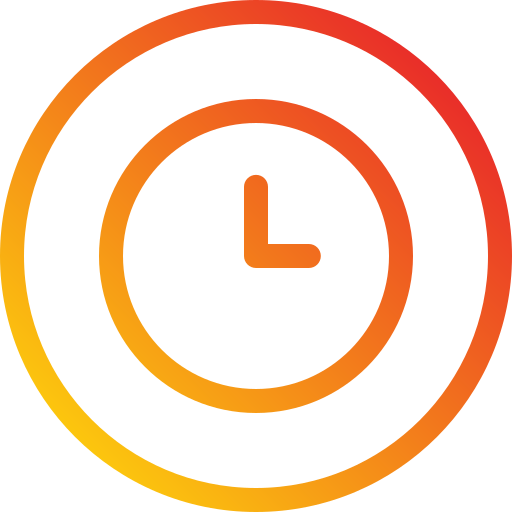
spent searching for semi-finished goods and objects of various sizes.
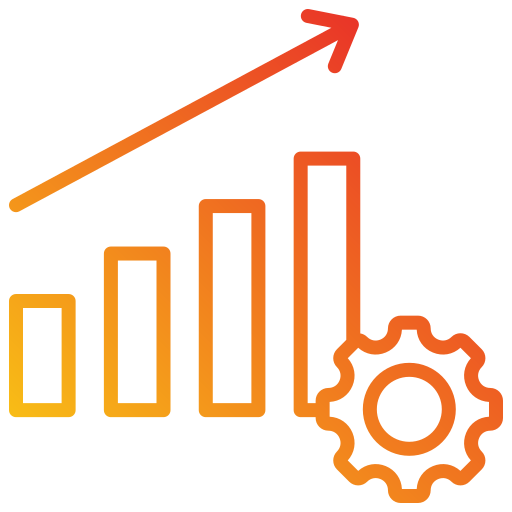
estimated during the planning phases
In an increasingly hectic business context, how much time do you lose searching for essential elements in the production process? According to a study we conducted on a sample of approximately 120 companies in the Italian manufacturing sector, 76% lose about 2 hours a day searching for semi-finished goods and items of various sizes (from carts and pallets to tools and small parts). In practice, this time is lost in assembling WIP as a result of batches being lost or moved, making it challenging to locate them promptly.
This implies that the department manager has to assign a couple of people to search for what has been lost, interrupting their actual work, and possibly even adding overtime hours. In essence, companies lose valuable time and pay resources for batch search and handling, resulting in a loss of at least 2 hours of productivity per day. All this translates into additional costs and significantly increased stress levels. Do you find yourself in this scenario?
If we were to multiply these 2 hours over a workweek, it amounts to 10 hours per week; 40 hours per month, 560 hours per year. But think about it: this time could be used much more efficiently.
The main causes of this scenario can be several.
Firstly, this situation primarily occurs in discrete manufacturing, where a batch may pass through a department more than once or require processing in multiple stages. This is not the case, of course, for an assembly line.
Moreover, these are batches often placed on carts and manually transported from one department to another. Without any identifying code, it often happens that the operator moves the wrong cart or violates the First In, First Out (FIFO) rules, if it's that type of production.
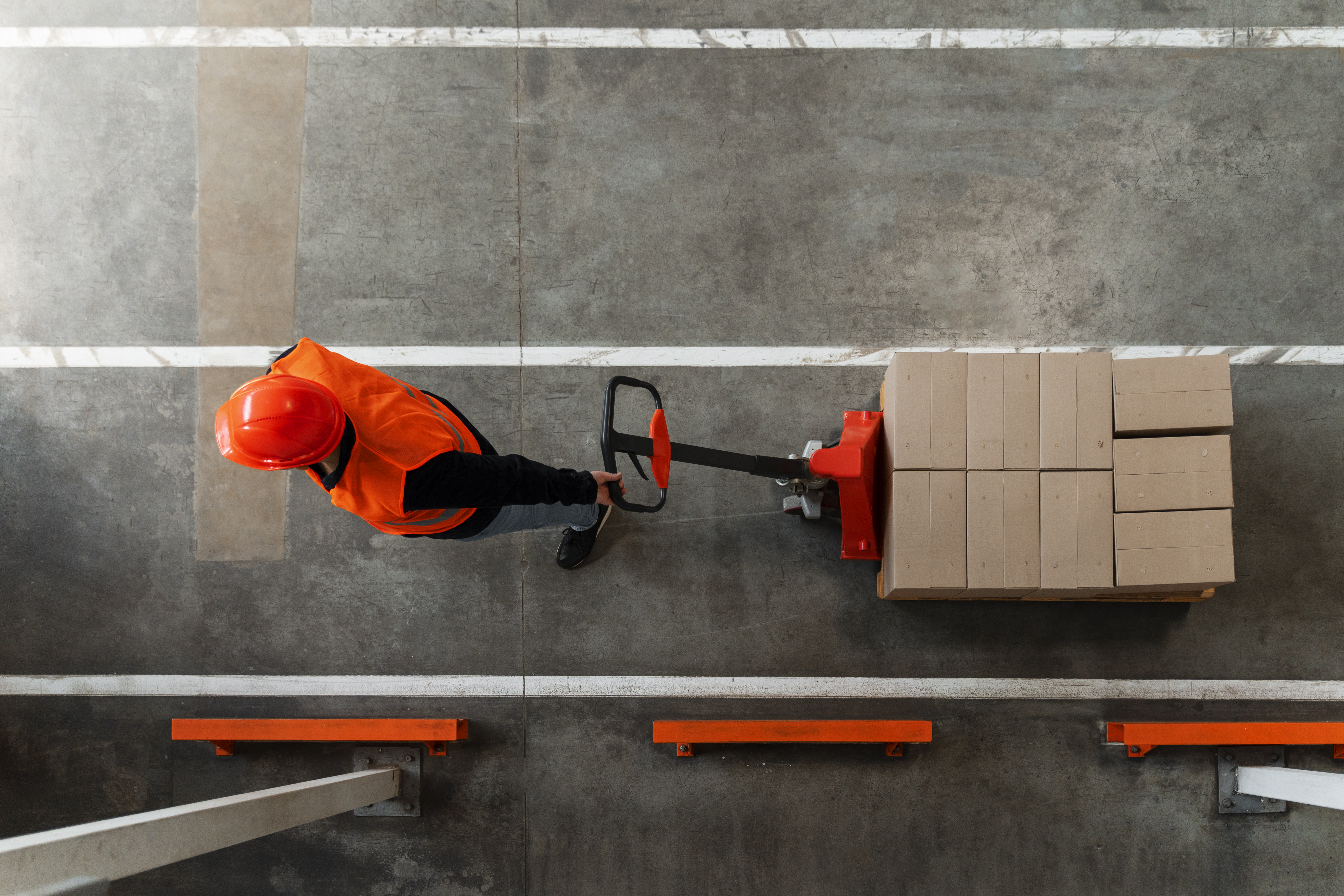
Ineffective management of enterprise information systems and the lack of integration between software further contribute to production inefficiency. Despite many companies using Material Requirements Planning (MRP) systems in their enterprise resource planning (ERP) for material management, the lack of proper tools to check production times and calculate production capacity causes bottlenecks and stops carts for extended periods, leading to a significant loss of efficiency, estimated at around 30% during planning phases.
To ensure sustainable improvement in production dynamics, it is essential to adopt a long-term, innovation-oriented, and continuously optimizing approach. In this context, overcoming obstacles related to efficiency loss requires an integrated and technological approach that goes beyond surface interventions and invests in the structural transformation of business processes, namely digital transformation.
The implementation of advanced solutions, such as intelligent monitoring and control systems, represents a first step towards more efficient resource management. These systems not only provide real-time visibility into production processes but also allow data analysis to identify critical points and optimize operations.
Similarly, leveraging emerging technologies, such as the integration of IoT devices and the use of advanced algorithms, enables faster and more accurate communication between departments. This not only reduces errors resulting from outdated or incomplete information but also facilitates synergistic collaboration between teams, helping overcome challenges related to time and resource dispersion.
Furthermore, investing in advanced warehouse management systems becomes crucial to ensuring accurate inventory traceability and optimal material management. Forecasting future demand and optimizing material layout are goals that can be achieved through the application of advanced technologies and predictive analysis.
Now let's look at some practical use cases in which adopting an RTLS solution has led to an overall improvement in production performance:
Warehouse Management of Finished Products:
If you manage a warehouse of finished products where pallets are dynamically stored and want to minimize the time to find them, the solution could be integrating an RTLS system and a location intelligence platform. With this technology, you can precisely detect the submetric position of finished products in the warehouse, speeding up retrieval operations and providing a real-time, comprehensive view of available and outgoing resources.
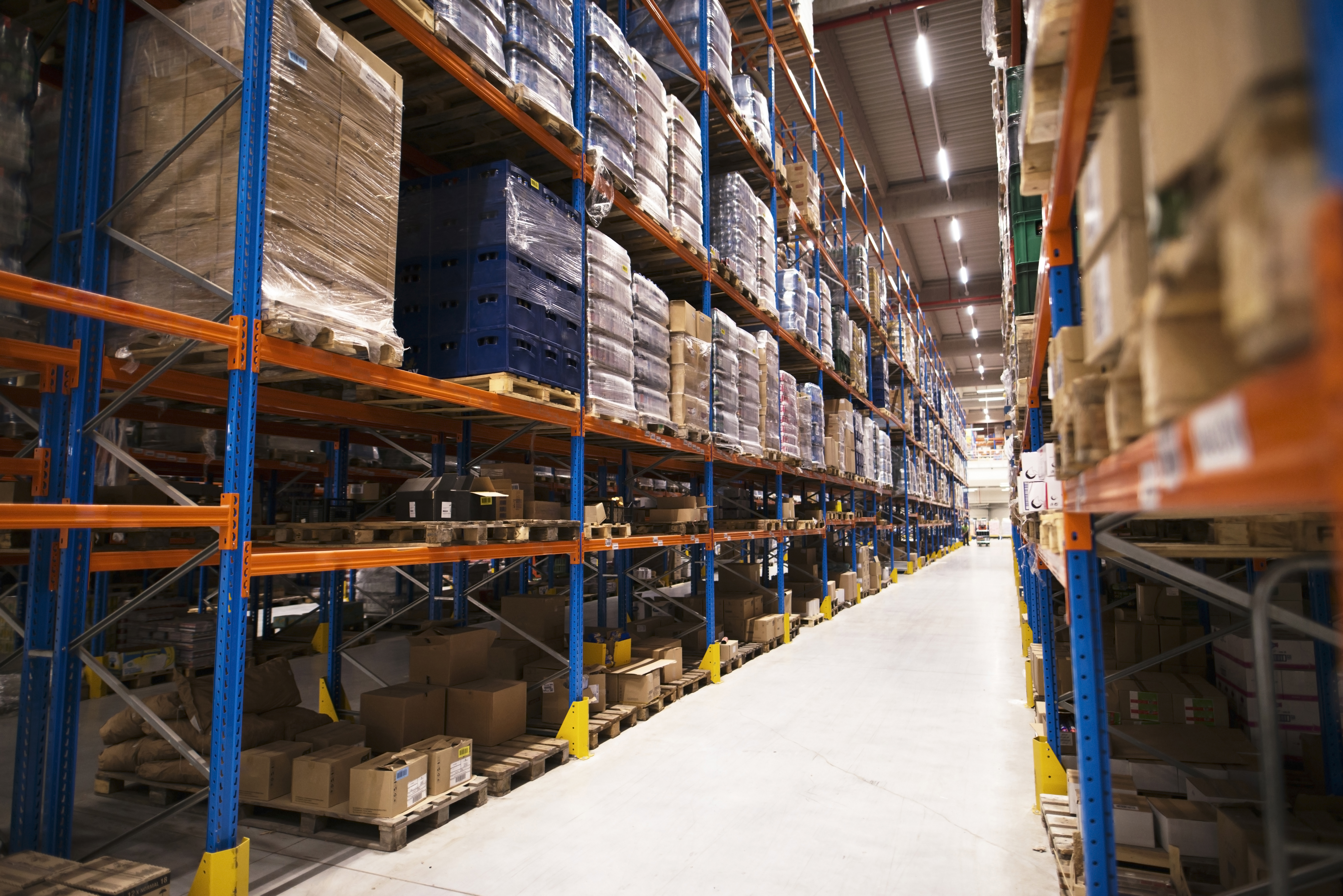
Maintenance of Automated Guided Vehicles (AGV):
Another operational mode involves tracking AGVs used to move goods, semi-finished products, and materials throughout the production facility, ensuring they undergo regular maintenance. This resolves the issue of not knowing their location since they move autonomously within large production plants. Knowing the real-time position of AGVs with great precision is also very useful for corporate safety, preventing collisions with forklifts and/or other operators.
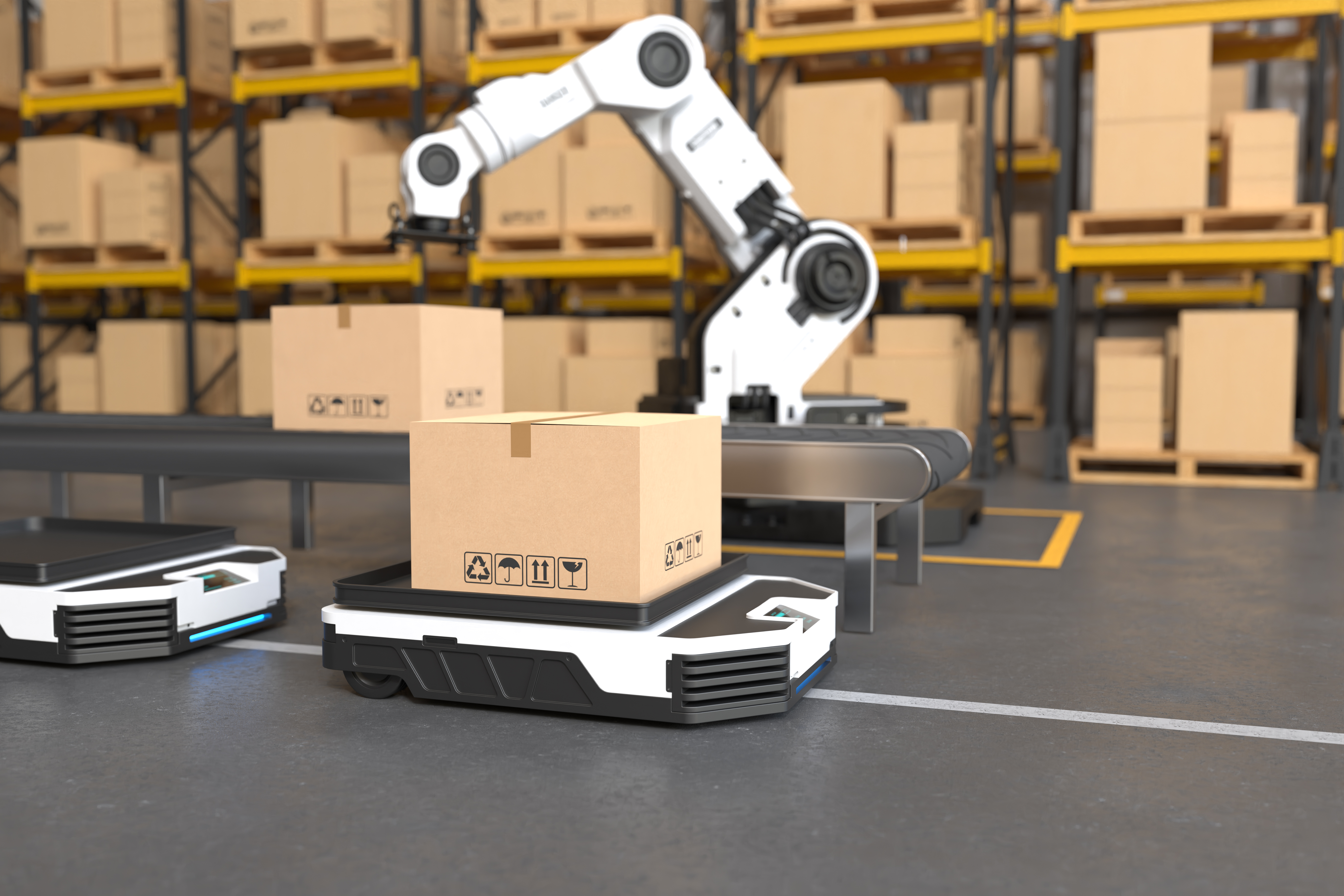
WIP Monitoring with Digital Labels:
If you usually don't track Work in Progress (WIP) on production line conveyors or mainly on assembly benches, thanks to RTLS technology, you can follow every movement directly from the office. Better yet, you can communicate directly with field operators through digital labels applied directly to production batches. In this way, the information on the label in the production area will correspond to what you see on your computer. For example, if a batch needs to move from the welding phase to the painting phase, the label will show a command indicating the end of welding and readiness for painting. Clicking on the label button will update this information on your computer system as well. This approach can also be applied in various scenarios, such as in production following the Kanban method.
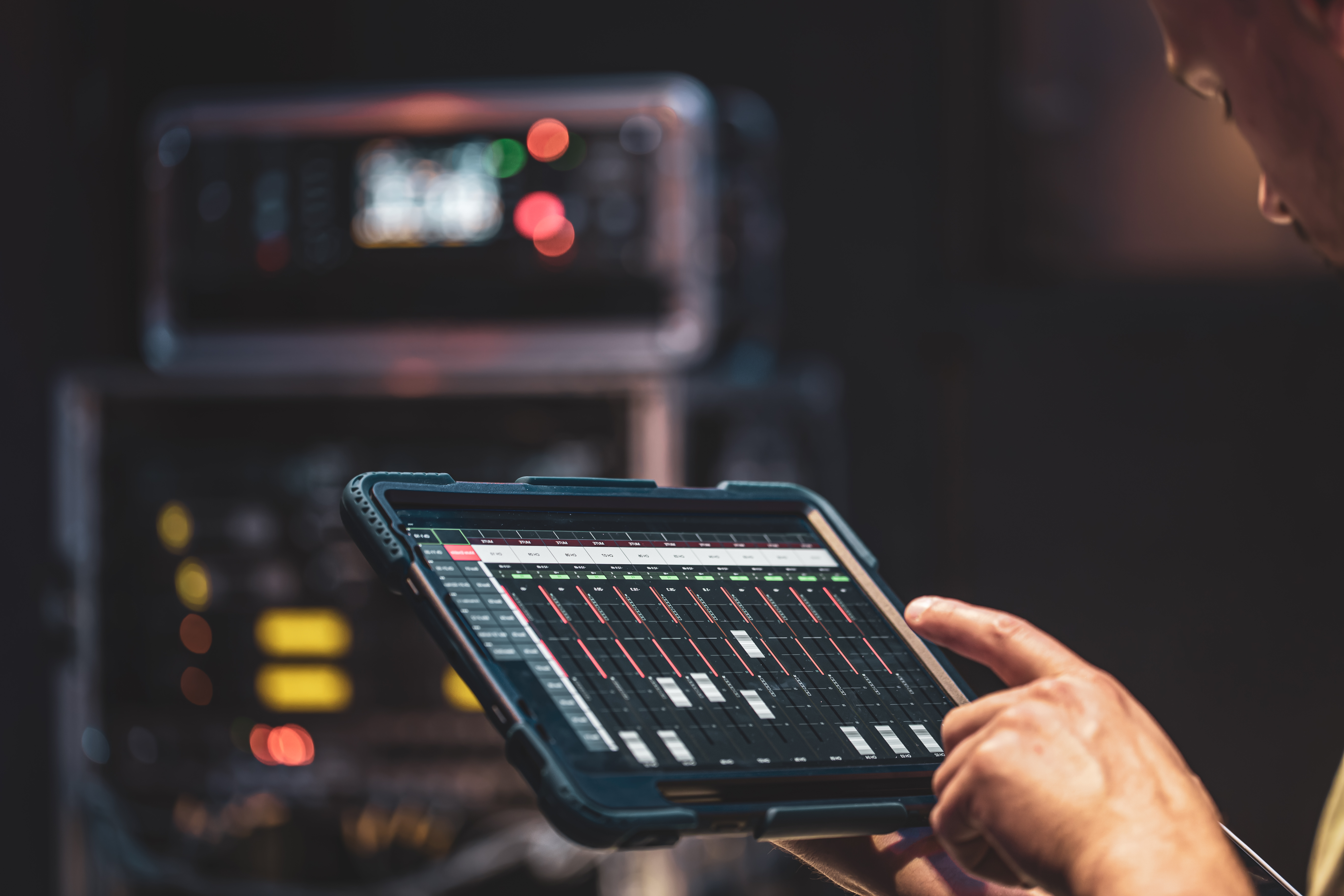
In summary, embracing a mindset of continuous innovation and adopting advanced technological solutions not only addresses immediate challenges related to efficiency loss but also establishes a solid foundation for the future. This approach not only reduces time lost in material search but promotes sustainable growth in overall productivity, positioning the company more competitively and resiliently in the ever-evolving market.
Have you noticed similar dynamics in your production or warehouse environment?