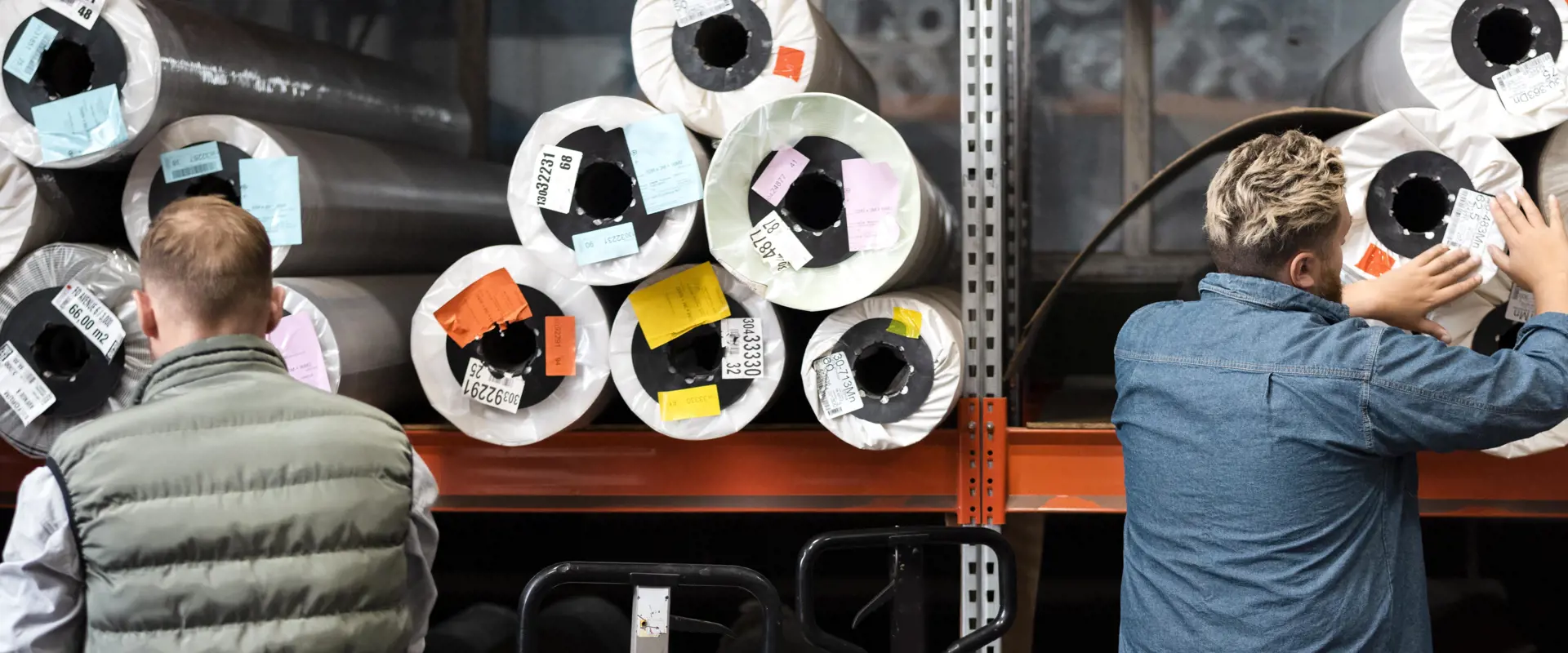
Why is traditional Kanban no longer an option?
The increasing connectivity of digital devices is not yet accompanied by a significant evolution of the Kanban method in the manufacturing sector. thinkin addresses this challenge by introducing digital Kanban, automating inventory management, and implementing real-time tracking of production batches.
According to an article published by Forbes, by the end of 2024, there will be over 207 billion devices connected to the global network of tools and equipment that make up the Internet of Things (IoT).
Exponential growth in quantity will not be in computers or smartphones but in devices ranging from toothbrushes to heavy industrial machinery, all interconnected. These devices increasingly incorporate artificial intelligence (AI) and are capable of making autonomous decisions. The evolution of the Internet of Things (IoT) and the increasing interconnection of devices have a significant impact on workflow management.
In this context, it becomes essential for a manufacturing company not only to adopt the most advanced technologies but also to digitize its processes and working methods simultaneously. Among these methods, traditional Kanban is one, and it is increasingly necessary for it to find its evolution in digital Kanban.
Don't miss the opportunity to find out how our E-Kanban can make a difference in your production line.
Download our free brochure!
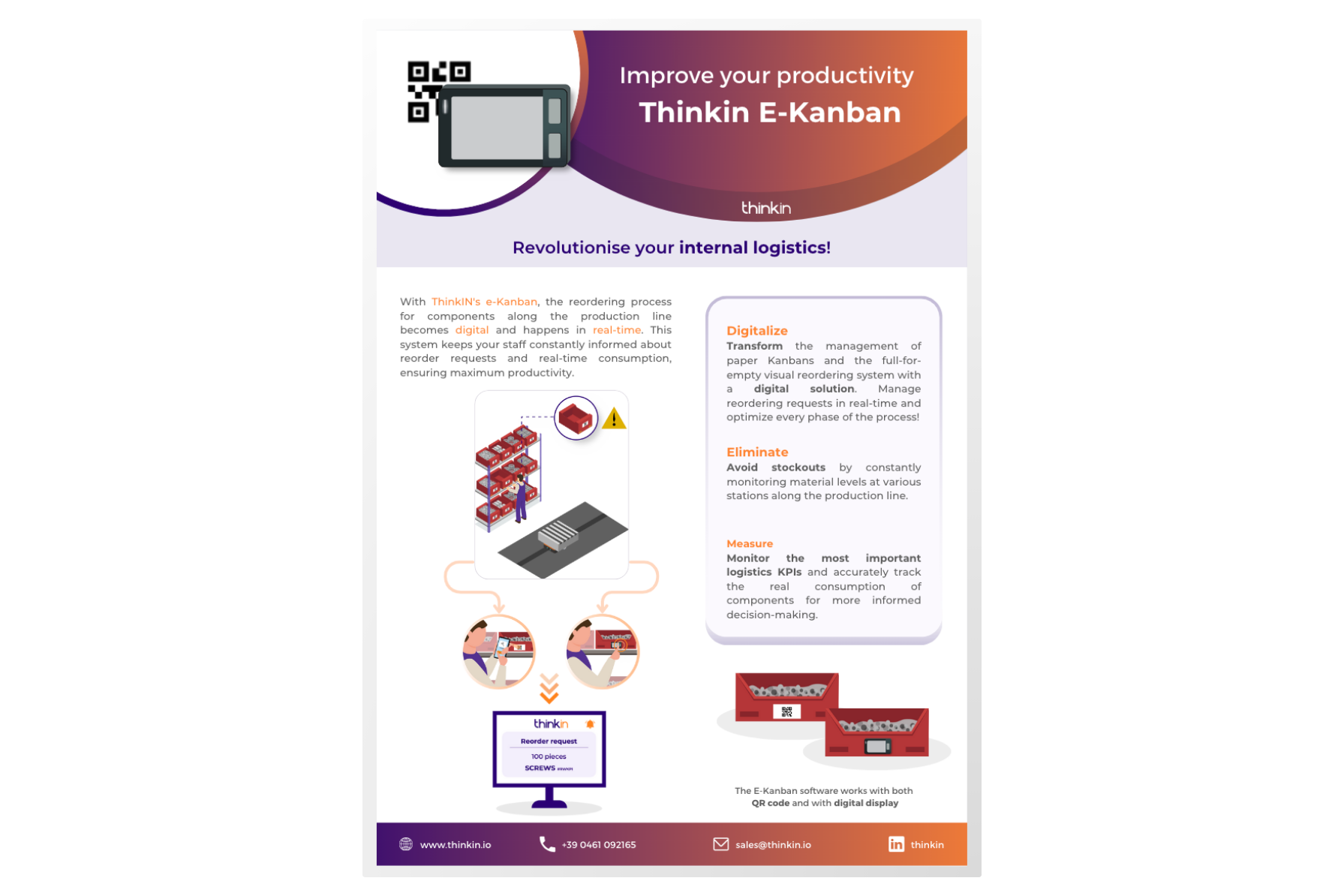
Meanwhile, what is Traditional Kanban?
The term "Kanban" in Japanese means "signboard" or "visual board." Traditional Kanban is a visual workflow management system that uses a board with columns and cards, often called "task cards" or "Kanban cards," to track and manage work. This method was originally developed by Toyota in the 1950s as part of the Toyota Production System (TPS).
Traditional Kanban is a highly effective method for visually and collaboratively managing production flows. However, with technological advances and the growing need to work remotely or in a distributed manner, the shift to digital Kanban has become an interesting option for many companies.
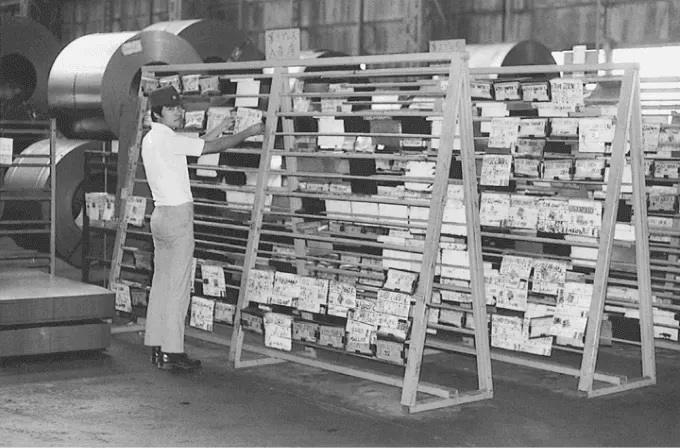
Here are the dilemmas of traditional Kanban:
- Lack of real-time visibility
The lack of real-time visibility poses a significant challenge within the context of traditional Kanban. This method relies on the manual movement of cards from the downstream process to the upstream process. However, this methodology can cause significant production delays due to the lack of real-time monitoring of inventory or components in the assembly phase.
As a result, there are difficulties in managing and efficiently allocating resources, as teams must wait for the transfer of cards to get updated information on the current status of inventory. These delays can lead to planning issues and limit flexibility in project management.

- Manual reordering of components
In traditional Kanban, manual reordering of components is one of the main challenges. This process requires constant supervision of the materials inventory needed for production and manual intervention when these stocks reach critical levels or run out.
Dependency on human interventions in this process can lead to errors, delays, and inefficiencies. Moreover, manual reordering is influenced by external factors, such as errors in identifying low stocks, lack of real-time visibility into inventory status, and unforeseen fluctuations in customer demand, which can result in excessive or insufficient stocks, causing additional costs or risks in the supply chain.
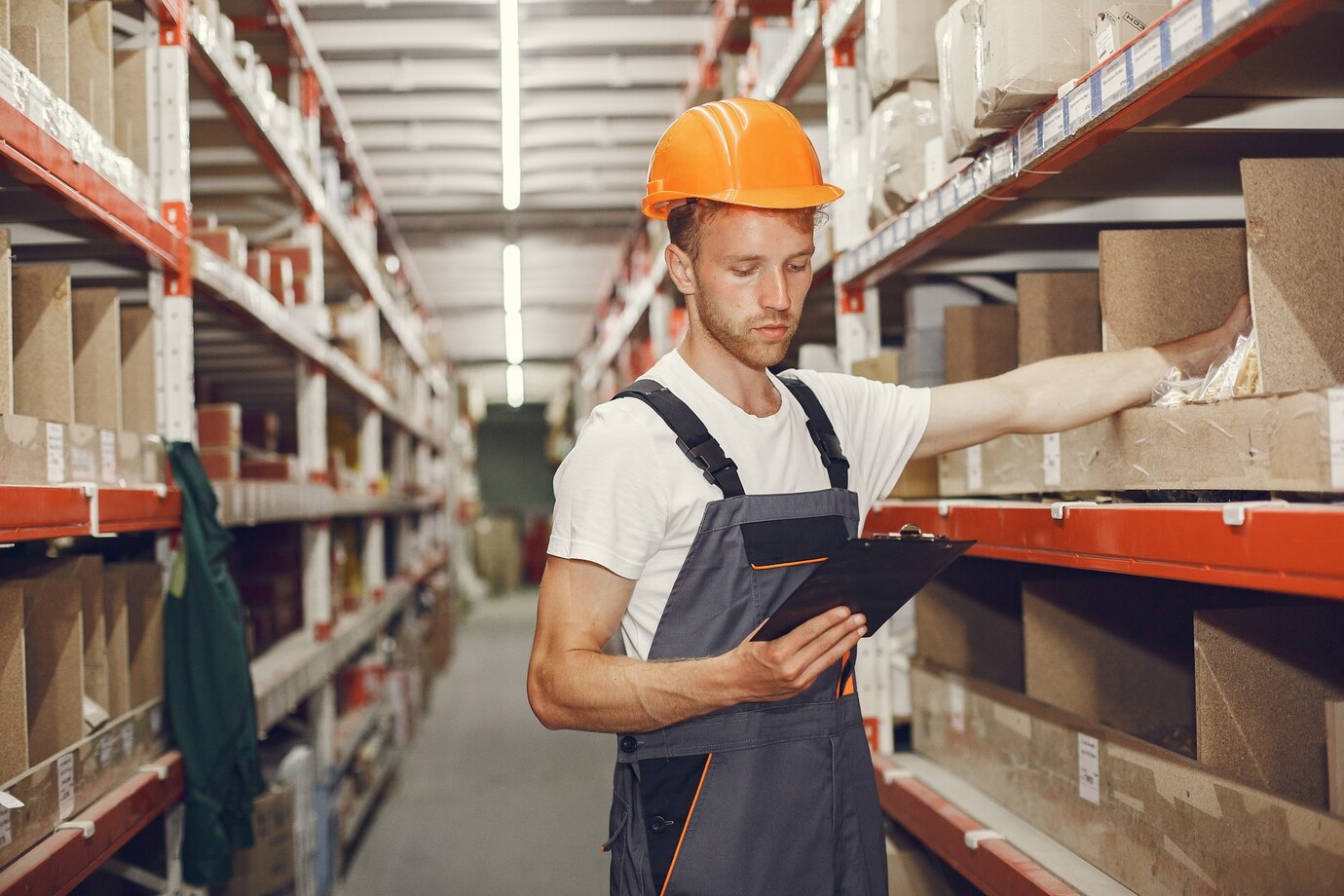
- Limited environmental sustainability
From an environmental perspective, the traditional Kanban system can generate inefficiencies contributing to unsustainable resource management. For example, the excessive use of physical cards or writing materials to track activities can lead to paper and other material waste.
Additionally, the need to physically move cards from one place to another may require physical transfers or energy consumption, contributing to the overall environmental impact. This becomes particularly relevant, considering that cards are frequently lost, resulting in time loss in their search (which, in turn, represents a waste of resources) and the need to reprint them, leading to double paper usage. These aspects become crucial in the current context where environmental sustainability is a growing priority for many organizations.
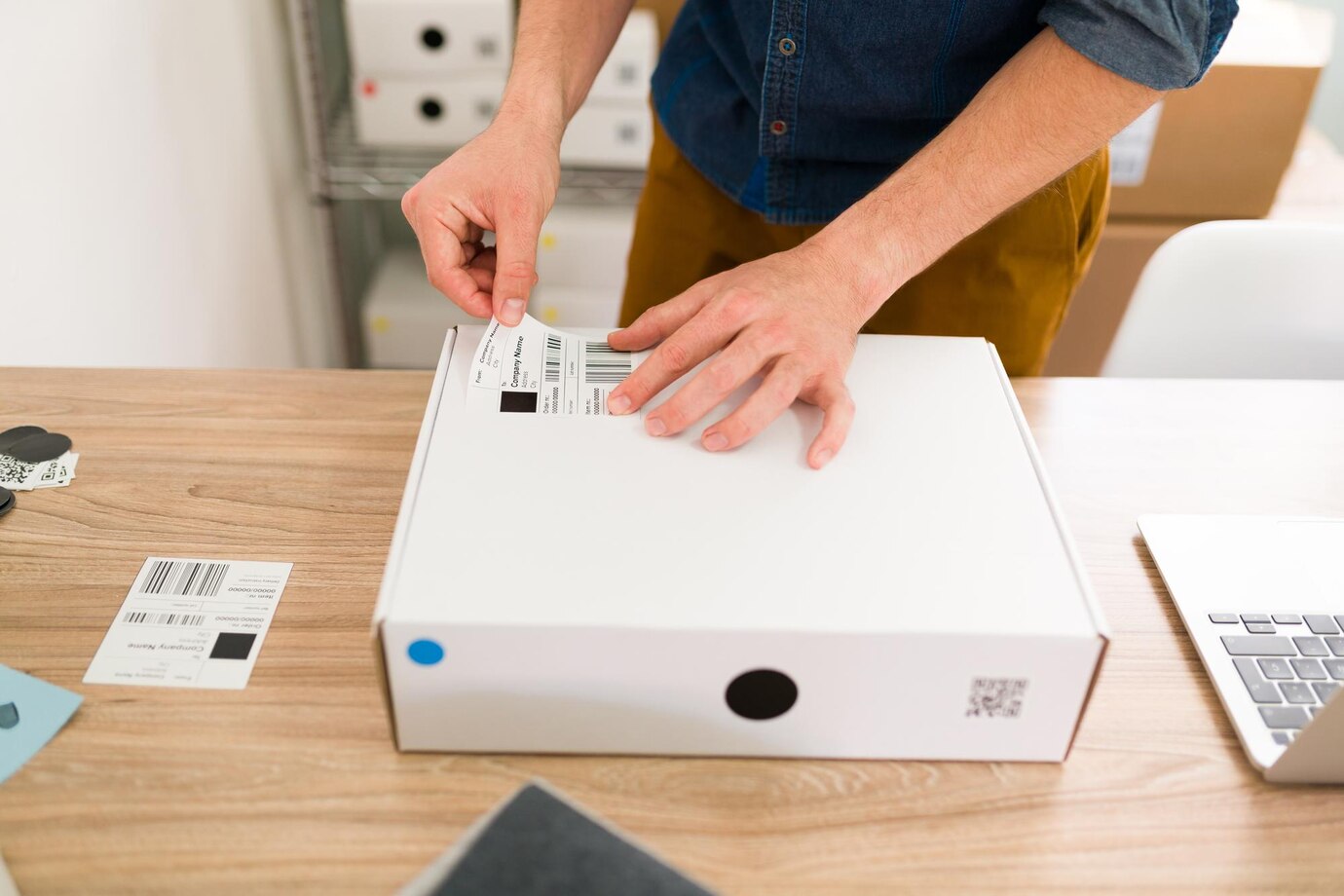
So, how does thinkin address this shortfall?
Now that we have seen the main challenges of traditional Kanban, let's see how thinkin addresses these gaps and has developed a software service capable of implementing the digital Kanban method:
- Automates inventory management: The operator can automatically reorder components directly from the downstream phase to the management system. This allows maintaining the traditional Kanban approach but in a digital, more efficient environment that is monitored in real-time.
- Customizes and optimizes: The software is adapted to the specific needs of the team. thinkIN offers the possibility to set rules and custom automations, if necessary, to further improve supermarket management.
- Monitors and adapts: The next step is to constantly monitor the digital workflow. thinkin collects and analyzes data to identify areas for improvement. This allows making necessary corrections to optimize inventory management and predict supply correctly.
In practical terms, thinkin has identified two main issues or use cases in the manufacturing sector related to the Kanban method and has developed the following solutions:
Real-time tracking of production batches with the Zone Presence App
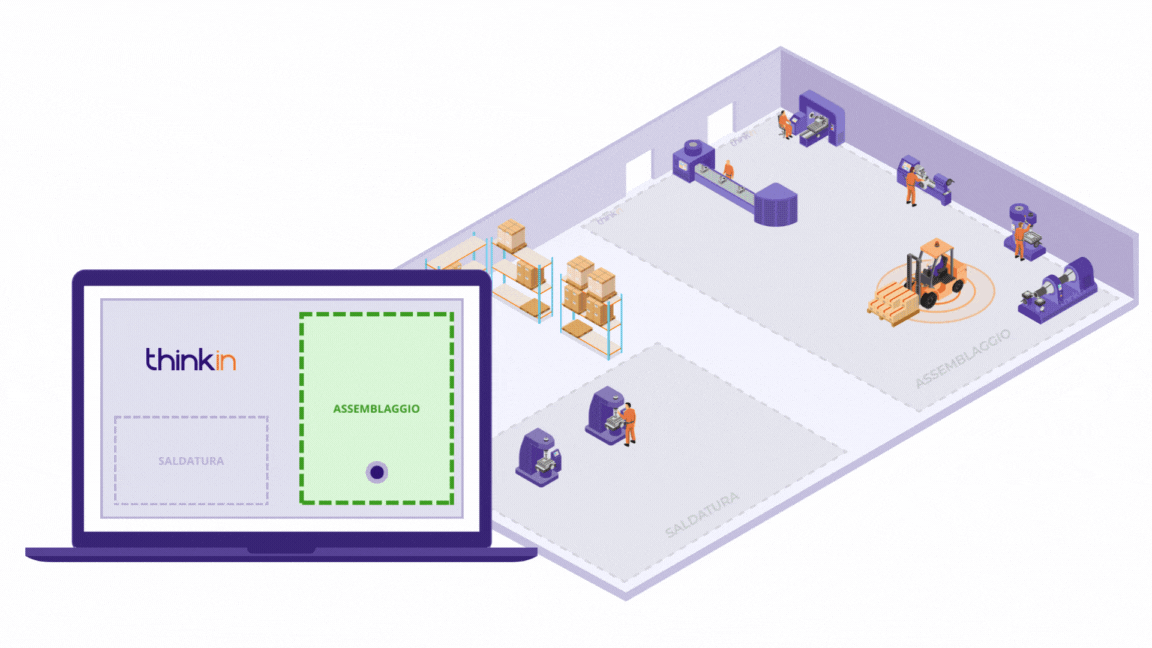
- In the typical scenario where a production batch moves from one phase to another, an operator on a forklift picks up a batch and transfers it between different production phases, such as welding and assembly. Usually, the operator manually records this movement by taking a card from the cart or crate and bringing it to the Kanban box. Usually, another operator then picks up the cards and returns them upstream (to the Kanban board).
- However, in the digital Kanban approach, the process is digitized and automated through thinkin's Zone Presence service. This involves the installation of a Real-Time Location System (RTLS) infrastructure inside the facility, with antennas positioned high in the production area. These antennas detect the passage of tags, which can be applied directly to carts or crates (for direct batch tracking) or on forklifts (for indirect batch tracking).
- On the thinkin platform, where the digital twin of the production area has been previously replicated, check-in zones have been defined that activate automatically with a notification system when a tag passage occurs. For example, if the tag is placed on the forklift carrying the crate, passage 1 recorded by thinkin will mean that the forklift is transporting the full crate from phase A to phase B, while passage 2 will mean that the forklift is returning the empty crate from phase B to phase A.
- This allows not only visualizing the current location of individual batches within different production areas but also the quantity of each batch in each of the areas.
- Based on the configured rules, the system considers the batch as "used" or "waiting to be used." The information provided by thinkin reflects real-time production progress, and as a result, it will be possible to manage the reordering of components automatically. How? The thinkin platform integrates with the ERP or MES management system used in the company. In general, this new approach and working method allow all operators to remain constantly informed about the quantities of components used along the entire production line and optimally manage the workload upstream.
Automatic reordering from the workstation via E-Paper or Digital Cards
- This solution is particularly suitable for application in assembly benches and managing the reordering of smaller components, such as hardware. It involves the adoption of digital cards to replace traditional cards used to monitor each order.
- The basic idea is to place these digital cards on workstations, directly on the conveyors positioned along the production line or, mainly, on assembly benches. Operators can then send requests for component replenishment by simply clicking on one of the buttons on the digital cards.
These digital cards are connected to the thinkin platform, which means that they are not only locatable but also allow activating the replenishment notification directly on the ERP or WMS management system.
- In practice, this eliminates the need for a person to physically collect information or cards to reorder components. The reordering process, therefore, follows the same logic as the Kanban system but is efficiently applied to manage smaller components and hardware.
With thinkin, you can combine the reliability of the traditional Kanban method with the flexibility and real-time visibility offered by a digital environment. This approach will help you manage your projects and workflows more efficiently and reliably, ensuring that your team can maintain total control over activities and constantly improve performance.
If your company is also facing these challenges and you want to learn more about how thinkin can help, contact us here. It will be a pleasure to continue the conversation together!