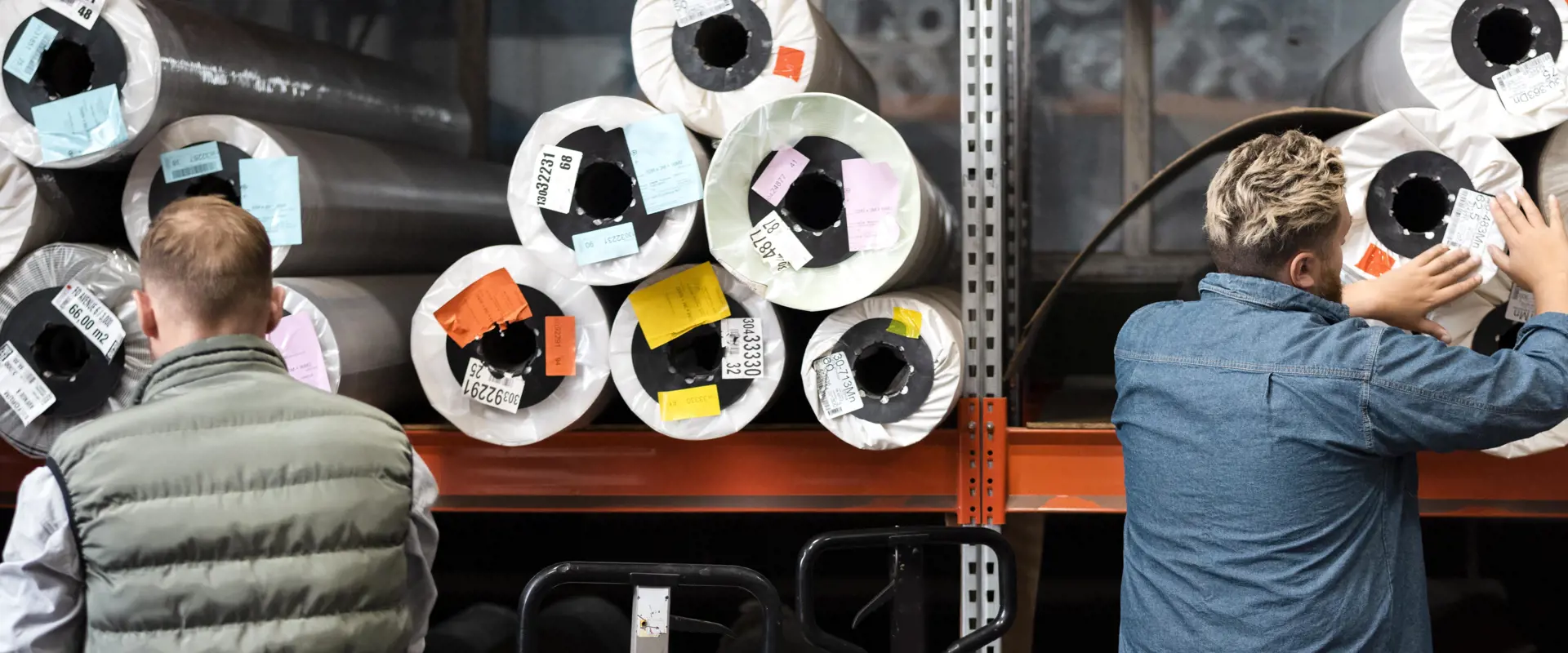
Perché il metodo Kanban tradizionale non è più un’opzione?
La crescente connettività dei dispositivi digitali non è ancora accompagnata da una significativa evoluzione del metodo Kanban nel settore manifatturiero. thinkin affronta questa sfida introducendo il Kanban digitale, automatizzando la gestione delle scorte e implementando il tracciamento dei lotti produttivi in tempo reale.
Secondo un articolo pubblicato da Forbes, alla fine del 2024 ci saranno più di 207 miliardi di dispositivi connessi alla rete mondiale di strumenti e apparecchiature che compongono l'Internet of Things (IoT).
A crescere esponenzialmente in quantità non saranno computer o smartphone, ma dispositivi che vanno da spazzolini da denti a macchinari industriali pesanti, tutti collegati in rete.
Sempre più spesso si tratterà di device potenziati dall'intelligenza artificiale (IA) e in grado di prendere decisioni autonome. L'evoluzione dell'Internet of Things (IoT) e la crescente interconnessione di dispositivi hanno un impatto significativo sulla gestione dei flussi di lavoro.
In questo contesto, diventa essenziale per un'azienda manifatturiera non solo adottare le tecnologie più avanzate, ma anche digitalizzare parallelamente i propri processi e metodi di lavoro. Tra questi metodi, il Kanban tradizionale è uno di essi, ed è sempre più necessario che trovi la sua evoluzione in Kanban digitale.
Non perdere l'occasione di scoprire come il nostro E-Kanban può fare la differenza nella tua linea di produzione.
Scarica la nostra brochure gratuita!
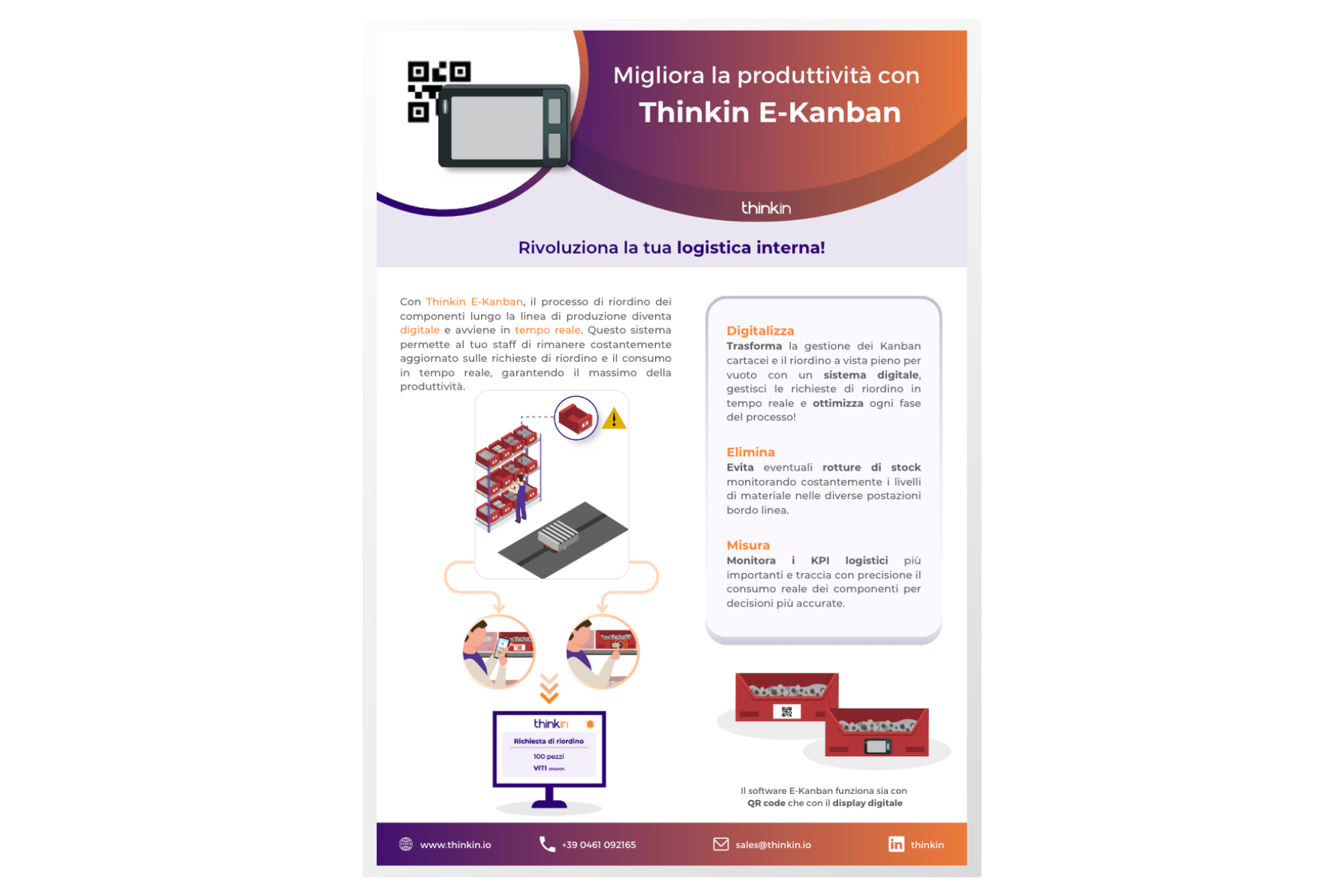
Intanto, cos'è il Kanban Tradizionale?
Il termine "Kanban" in giapponese significa "cartellino" o "tabellone visivo". Il Kanban tradizionale è un sistema visuale di gestione del flusso di lavoro che utilizza una tavola con colonne e carte, spesso chiamate "task cards" o "Kanban cards", per tracciare e gestire il lavoro. Questo metodo è stato originariamente sviluppato da Toyota negli anni '50 come parte del Sistema di Produzione Toyota (Toyota Production System o TPS).
Il Kanban tradizionale è un metodo altamente efficace per gestire i flussi di produzione in modo visuale e collaborativo. Tuttavia, con l'avanzamento della tecnologia e la crescente necessità di lavorare in modo remoto o distribuito, il passaggio al Kanban digitale è diventato un'opzione interessante per molte aziende.
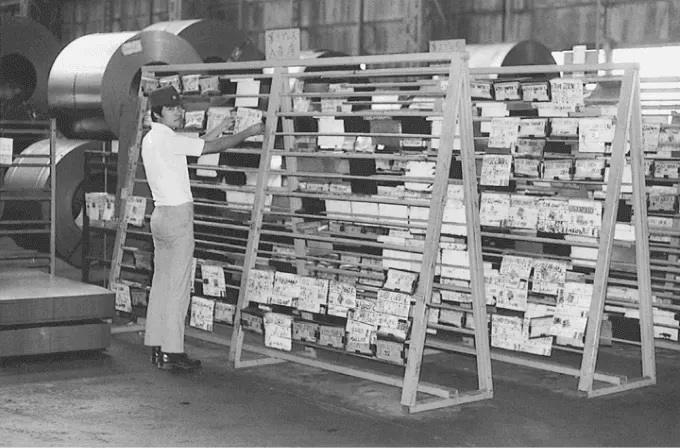
Ecco i dilemmi del Kanban tradizionale:
- Mancanza di visibilità in tempo reale
La mancanza di visibilità in tempo reale costituisce una sfida significativa all'interno del contesto del kanban tradizionale. Questo metodo si basa sullo spostamento manuale dei cartellini dal processo a valle al processo a monte. Tuttavia, questa metodologia può comportare ritardi significativi nella produzione a causa del mancato monitoraggio in tempo reale delle scorte o dei componenti nella fase di assemblaggio.
Di conseguenza, si verificano difficoltà nella gestione e nell'allocazione efficiente delle risorse, in quanto i team devono attendere il trasferimento dei cartellini per ottenere informazioni aggiornate sullo stato attuale delle scorte. Questi ritardi possono causare problemi di pianificazione e limitare la flessibilità nella gestione dei progetti.

- Riordino manuale dei componenti
Nel kanban tradizionale, il riordino manuale dei componenti rappresenta una delle sfide principali. Questo processo richiede la costante supervisione delle scorte di materiali necessarie per la produzione e l'intervento manuale quando tali scorte raggiungono livelli critici o si esauriscono.
La dipendenza da interventi umani in questo processo può portare a errori, ritardi e inefficienze. Inoltre, il riordino manuale è influenzato da fattori esterni, come errori nell'identificazione delle scorte basse, mancanza di visibilità in tempo reale sullo stato delle scorte e fluttuazioni impreviste nella domanda dei clienti, che possono causare scorte eccessive o insufficienti, comportando costi aggiuntivi o rischi nella catena di approvvigionamento.
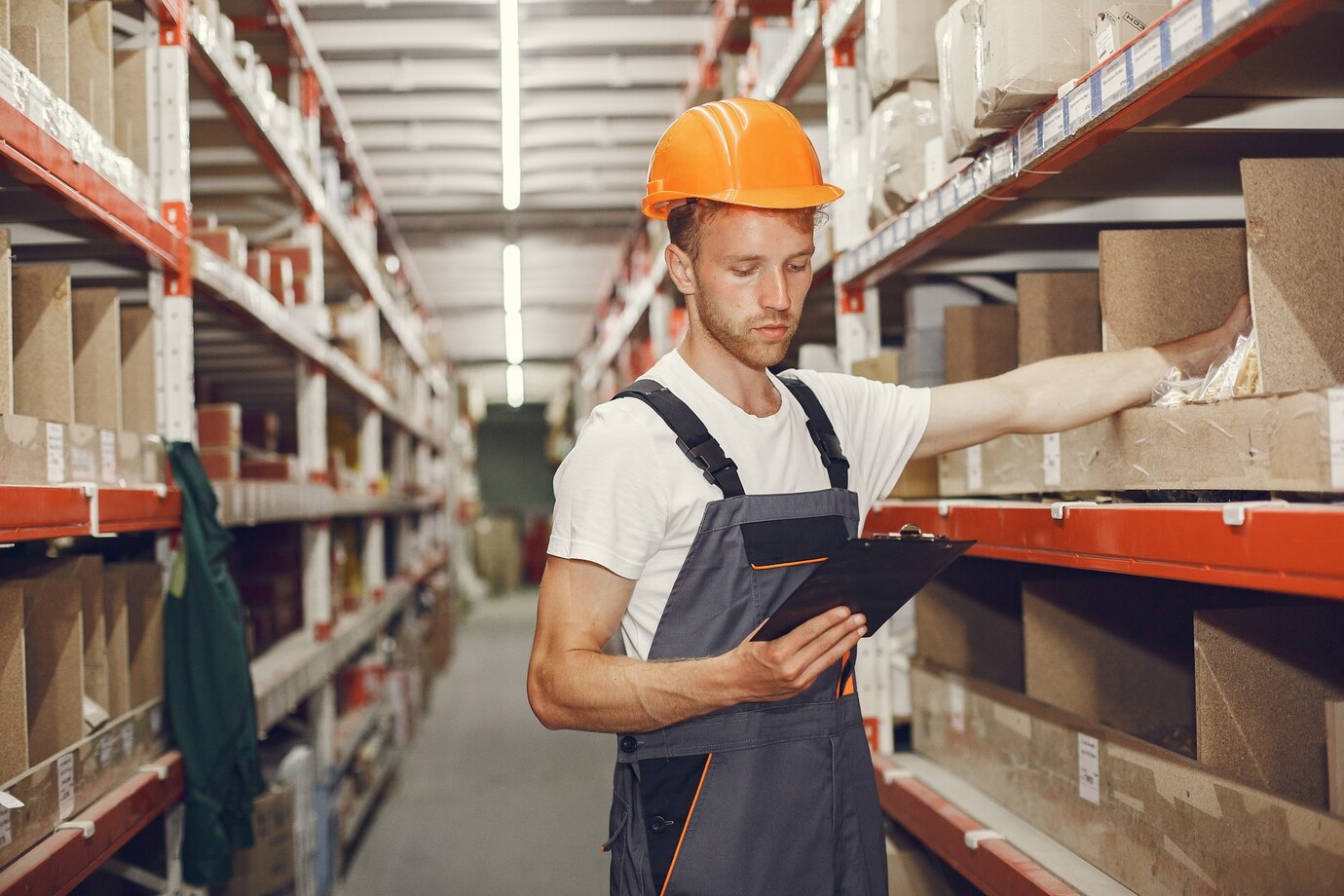
- Poca sostenibilità ambientale
Sotto il profilo ambientale, il sistema Kanban tradizionale può generare inefficienze che contribuiscono a una gestione non sostenibile delle risorse. Ad esempio, l'eccessivo utilizzo di cartellini fisici o materiali per la scrittura per tracciare le attività può dar luogo a sprechi di carta e di altri materiali.
Inoltre, la necessità di spostare fisicamente le schede da un luogo all'altro può richiedere trasferimenti fisici o il consumo di energia, contribuendo così all'impatto ambientale complessivo. Questo assume particolare rilevanza, considerando che frequentemente i cartellini si smarriscono, comportando una perdita di tempo nella loro ricerca (che a sua volta rappresenta uno spreco di risorse) e la necessità di ristamparli, portando quindi ad un doppio utilizzo di carta. Questi aspetti diventano cruciali nell'attuale contesto in cui la sostenibilità ambientale rappresenta una crescente priorità per molte organizzazioni.
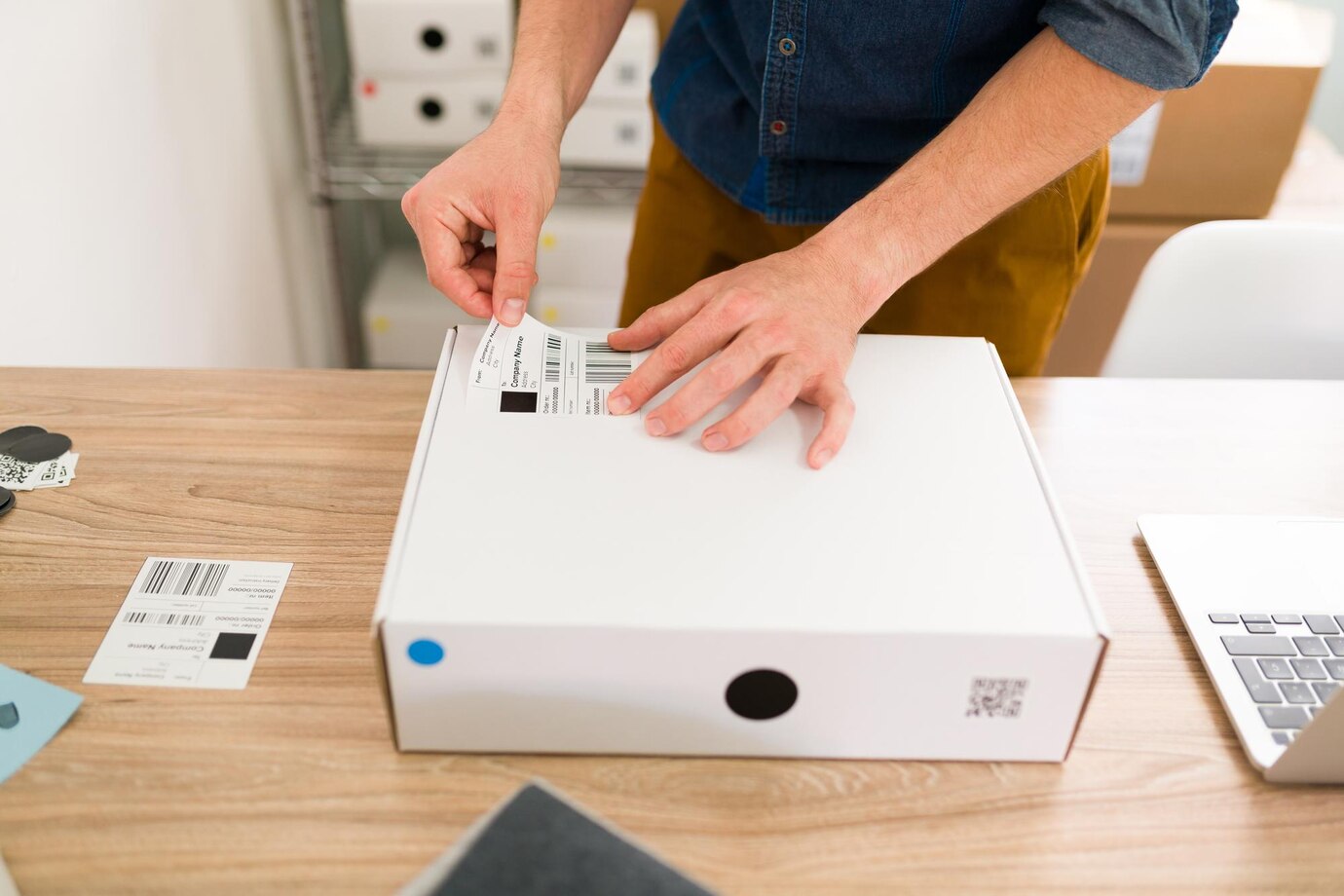
Quindi, in che modo thinkin colma questa mancanza?
Ora che abbiamo visto le principali sfide del Kanban tradizionale, vediamo come thinkin affronta queste lacune e ha sviluppato una servizio software in grado di mettere in pratica il metodo Kanban digitale:
- Automatizza la gestione delle scorte: l’operatore può effettuare il riordino automatico dei componenti direttamente dalla fase a valle a sistema gestionale. Questo consente di conservare l’approccio kanban tradizionale, ma in un ambiente digitale, più efficiente perché monitorato in tempo reale.
- Personalizza e ottimizza: il software viene adattato di volta in volta alle esigenze specifiche del team. thinkIN offre la possibilità di impostare regole e automazioni personalizzate, se necessario, per migliorare ulteriormente la gestione del supermarket.
- Monitora e adatta: Il passo successivo è quello di monitorare costantemente il flusso di lavoro digitale. ThinkIN raccoglie ed analizza dati per identificare aree di miglioramento. Questo permette di apportare le correzioni necessarie per ottimizzare la gestione delle scorte e prevedere la fornitura nel modo corretto.
A livello pratico, thinkin ha identificato nel settore manifatturiero due problematiche o casi d’uso principali legati al metodo kanban e ha sviluppato le seguenti soluzioni:
Tracking in tempo reale dei lotti produttivi con l'App Zone Presence
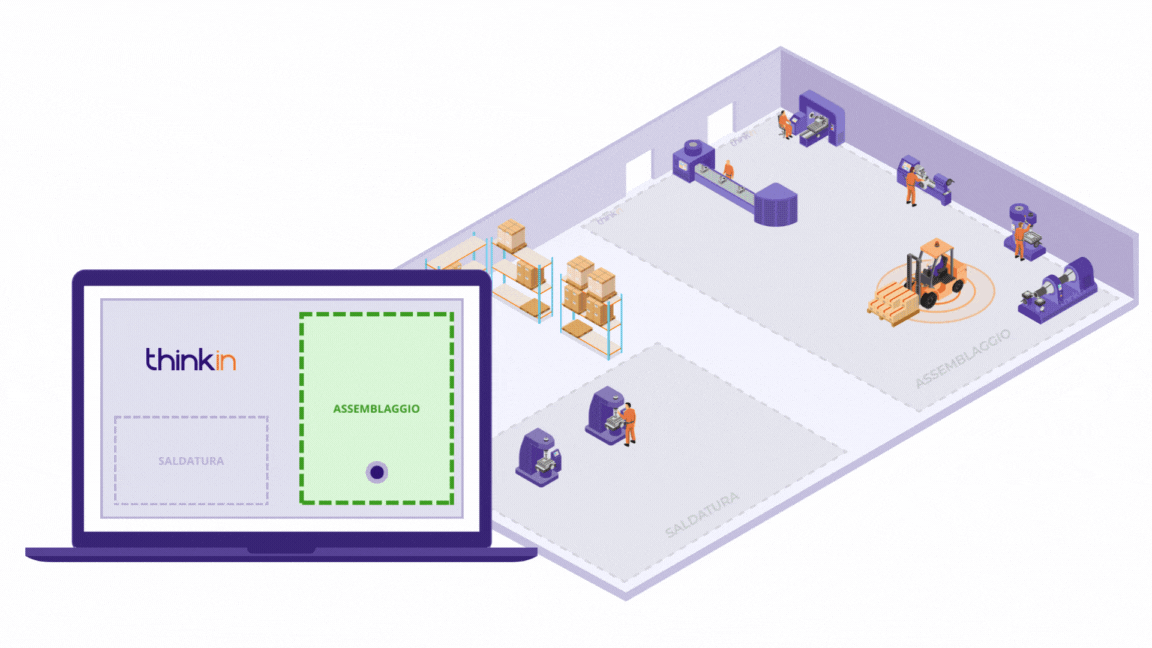
Guarda il nostro video su YouTube: Servizio E-Kanban
- Nel contesto tipico in cui un lotto produttivo si sposta da una fase all'altra, un operatore su un muletto preleva un lotto e lo trasferisce tra le diverse fasi di produzione, come la saldatura e l'assemblaggio. Di solito, l'operatore registra manualmente questo spostamento prendendo un cartellino dal carrello o dal cassone e portandolo alla kanban box. Di solito, un altro operatore poi passa a prendere i cartellini e li riporta a monte (alla kanban board).
- Tuttavia, nell'approccio del Kanban digitale, il processo viene digitalizzato e automatizzato attraverso il servizio Zone Presence di thinkin. Questo coinvolge l'installazione di un'infrastruttura RTLS (Real-Time Location System) all'interno dello stabilimento, con antenne posizionate in alto nell'area produttiva. Queste antenne rilevano il passaggio di tag, che possono essere applicati direttamente sui carrelli o cassoni (per il tracciamento diretto dei lotti) o sui muletti (per il tracciamento indiretto dei lotti).
- Sulla piattaforma ThinkIN, dove è stato precedentemente replicato il gemello digitale dell'area produttiva, sono state definite delle zone di check-in che si attivano automaticamente con un sistema di notifica nel momento in cui si verifica il passaggio di un tag. Ad esempio, se il tag è stato posto sul muletto che trasporta il cassone, il passaggio 1 registrato da ThinkIN significherà che il muletto sta trasportando il cassone pieno da una fase A a fase B, il passaggio 2 invece significherà che il muletto sta riportando il cassone vuoto dalla fase B alla fase A.
- Questo permette di visualizzare non solo la posizione attuale dei singoli lotti all'interno delle diverse aree produttive, ma anche la quantità di ciascun lotto in ciascuna delle aree.
- In base alle regole configurate, il sistema considera il lotto come "utilizzato" o "in attesa di essere utilizzato." Le informazioni date da thinkin riflettono in tempo reale l’avanzamento produttivo e, di conseguenza, sarà possibile gestire il riordino dei componenti in modo automatico. In che modo? La piattaforma thinkin si integra con il sistema gestionale ERP o MES utilizzato in azienda. In generale, questo nuovo approccio e metodo di lavoro consente a tutti gli operatori di rimanere costantemente informati delle quantità di componenti utilizzate lungo tutta la linea produttiva e gestire in modo ottimale il carico di lavoro a monte.
Riordino Automatico dal banco di lavoro tramite E-Paper o Cartellini Digitali
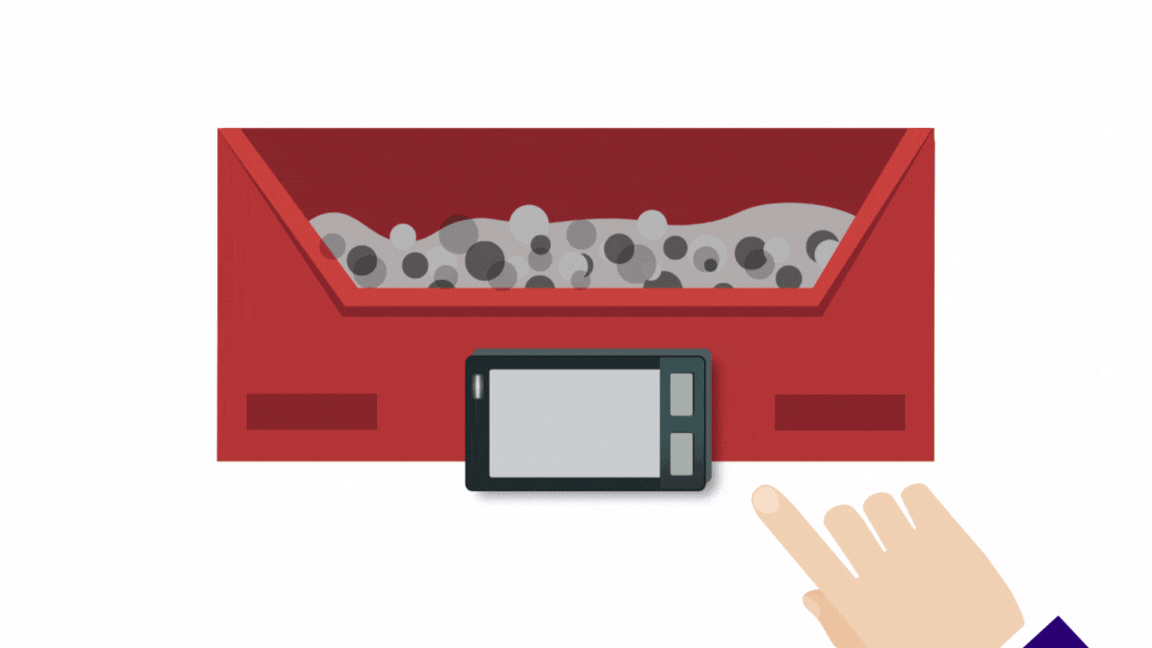
- Questa soluzione è particolarmente adatta per l'applicazione nei banchi di assemblaggio e nella gestione del riordino dei componenti più piccoli, come la minuteria. Prevede l'adozione di cartellini digitali per sostituire i tradizionali cartellini utilizzati per monitorare ciascuna commessa.
- L'idea di base è quella di collocare questi cartellini digitali sulle cassette di lavoro, direttamente sulle rulliere posizionate a bordo linea di produzione o, principalmente, sui banchi di assemblaggio. Gli operatori possono quindi inviare richieste di riordino di componenti semplicemente cliccando su uno dei pulsanti presenti sui cartellini digitali.
Questi cartellini digitali sono collegati alla piattaforma thinkin, il che significa che non solo sono localizzabili, ma permettono di attivare la notifica di riordino direttamente sul sistema gestionale ERP o WMS. - In pratica, questo elimina la necessità di una persona che raccolga fisicamente le informazioni o i cartellini per effettuare il riordino dei componenti. Il processo di riordino, quindi, segue la stessa logica del sistema Kanban, ma è applicato in modo efficiente per gestire i componenti più piccoli e la minuteria.
Con thinkin, puoi unire l'affidabilità del metodo Kanban tradizionale con la flessibilità e la visibilità in tempo reale offerte da un ambiente digitale. Questo approccio ti aiuterà a gestire i tuoi progetti e flussi di lavoro in modo più efficiente e affidabile, garantendo che il tuo team possa mantenere un controllo totale sulle attività e migliorare costantemente le prestazioni.
Se anche la tua azienda sta affrontando queste stesse sfide e desideri capire di più su come thinkin può aiutarti, contattaci qui. Sarà un piacere continuare la conversazione insieme!