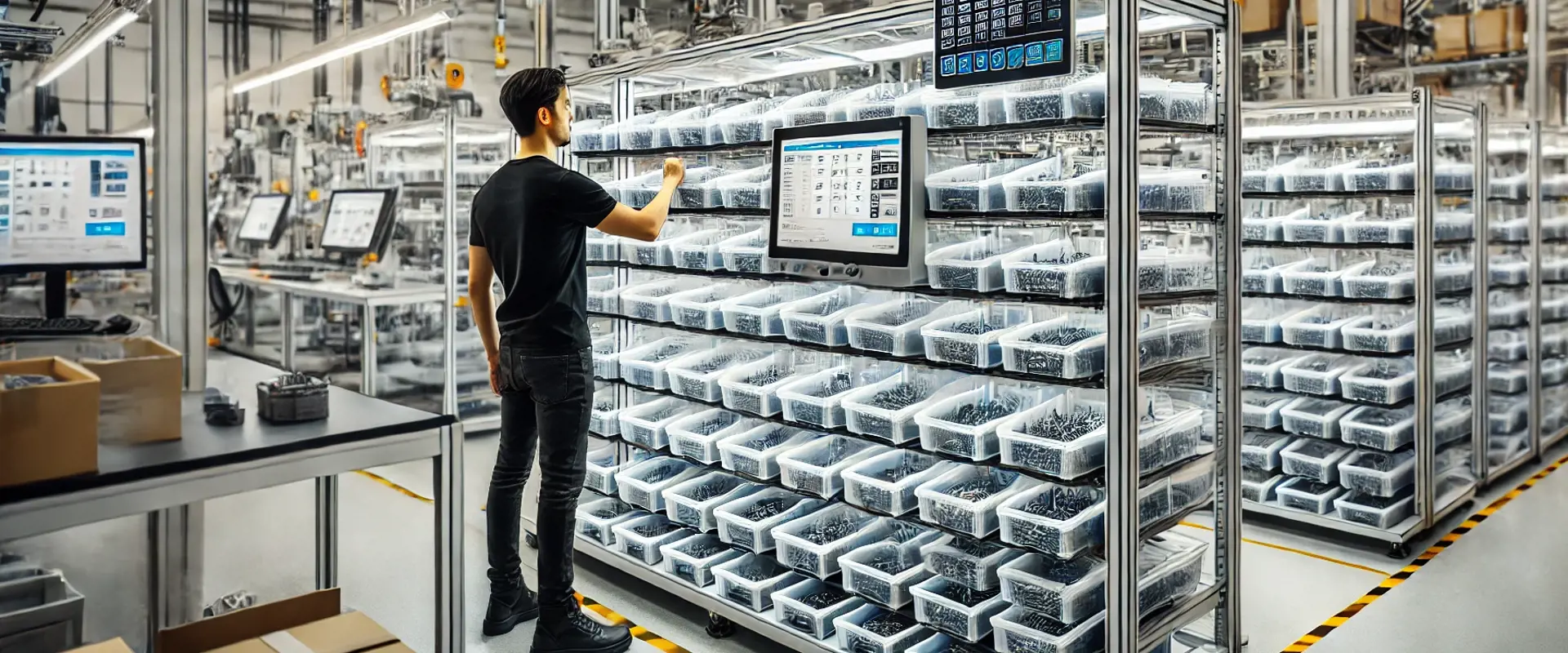
E-Kanban: L'evoluzione digitale che migliora la logistica in tempo reale
Immagina una produzione senza interruzioni
Immagina di poter eliminare tutte le inefficienze legate alla gestione manuale delle scorte, sapendo esattamente quando un componente sta per esaurirsi. Non servono più controlli visivi, cartellini cartacei o chiamate telefoniche. Con l'E-Kanban di Thinkin, puoi automatizzare tutto questo e avere un controllo totale sulla tua produzione.
- Automatizza il riordino dei componenti bordo linea in tempo reale, riducendo i tempi di fermo e aumentando l'efficienza operativa.
- Fornisce visibilità completa sui livelli di scorte, evitando interruzioni e rotture di stock.
- Riduce i costi e migliora la pianificazione della produzione grazie a una gestione digitale precisa e affidabile.
Cos'è l'E-Kanban Digitale?
L'E-Kanban è un sistema avanzato che digitalizza il tradizionale metodo Kanban utilizzato per gestire il riordino dei componenti lungo la linea di produzione. Il servizio ThinkIN E-Kanban elimina i cartellini cartacei e introduce display digitali connessi che automatizzano il processo di riordino. Questo approccio consente di monitorare i consumi in tempo reale, ottimizzare le attività di ripristino e ridurre al minimo gli errori umani.
Non perdere l'occasione di scoprire come il nostro E-Kanban può fare la differenza nella tua linea di produzione.
Scarica la nostra brochure gratuita!
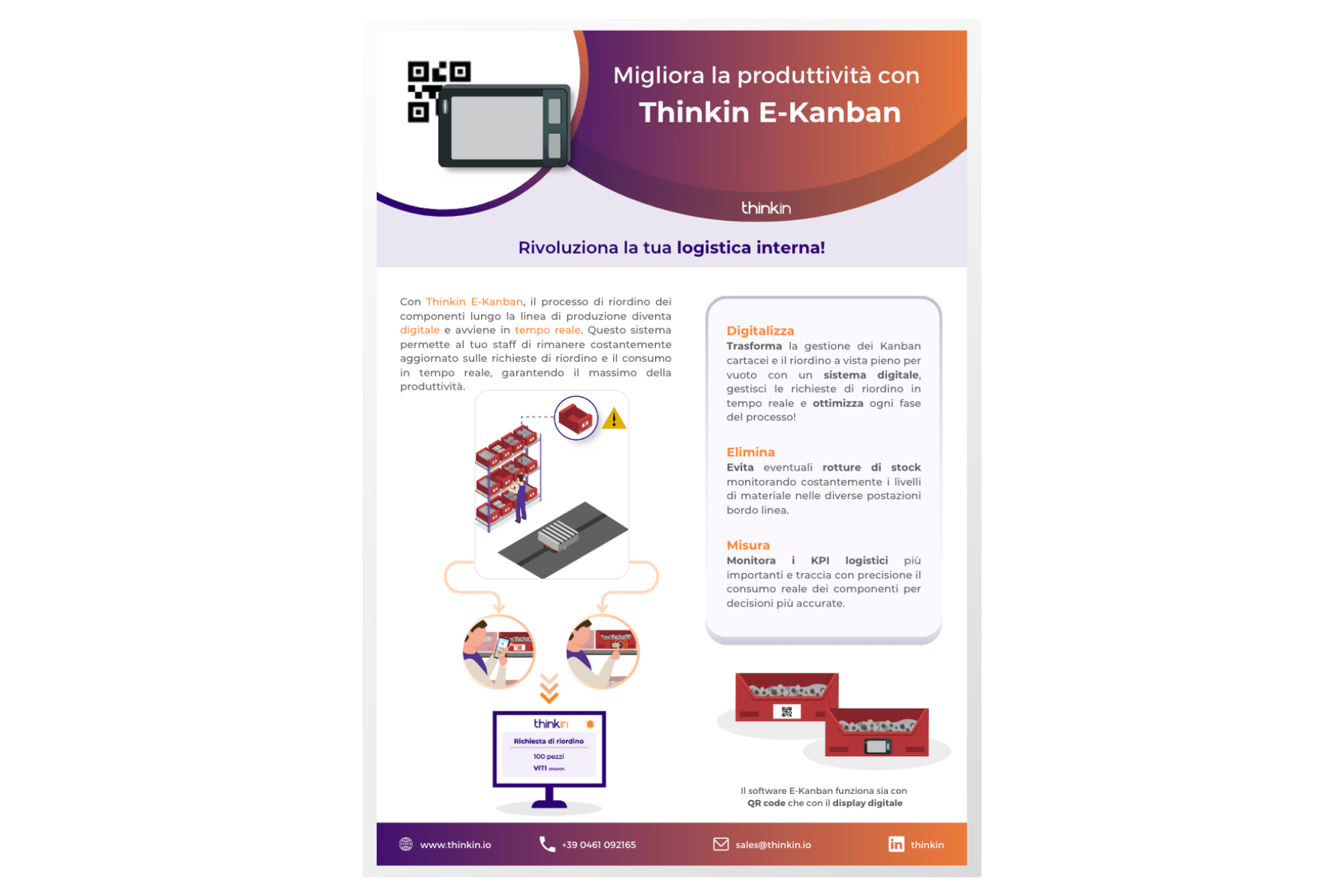
Come funziona l’E Kanban abbinato ai display digitali?
I display digitali del sistema E-Kanban di ThinkIN e offrono un'interfaccia semplice e intuitiva per gli operatori.
Ecco come funziona il processo:
- Riordino con un click: Ogni referenza gestita in modalità Kanban è dotata di un display digitale personalizzabile. Quando un componente si avvicina al livello minimo di scorta, l'operatore a bordo linea può premere un semplice pulsante sul display per richiedere il riordino. Non è più necessario utilizzare un cartellino carteceo per triggerare il riordino. La richiesta viene trasmessa in tempo reale al magazzino, dove l'operatore riceve immediatamente la notifica di riordino, gestisce il riordino verificando la giacenza e confermando il riordino tramite applicativo backoffice.
- Aggiornamento automatico del display: Una volta inviata la richiesta e fino al completa del riordino, il display digitale si aggiorna automaticamente, mostrando lo stato dell’operazione in tempo reale. Questo feedback immediato elimina l'incertezza e permette agli operatori sia a bordo linea sia in logistica, di essere aggiornati tempestivamente sull’intero processo di riordino.
- Personalizzazione completa: I display digitali possono essere personalizzati con le informazioni più rilevanti per ogni componente: codice articolo, descrizione, immagini, e persino note specifiche. Le informazioni vengono gestite centralmente e collegate al gestionale aziendale (ERP), garantendo dati sempre aggiornati . Supportano inoltre funzionalità avanzate come il "long press" per segnalare priorità urgenti.
- Monitoraggio e analisi del processo Tutte le richieste di riordino vengono tracciate e registrate in un applicativo di backoffice, dove è possibile monitorare l'avanzamento delle richieste e analizzare i tempi di risposta. Grazie a un cruscotto di analitiche, i manager possono identificare colli di bottiglia e ottimizzare i tempi di riordino, garantendo una produzione fluida e continua.
Guarda il nostro video su YouTube: Servizio E-Kanban
Vantaggi dell'implementazione del sistema E-Kanban di ThinkIN
-
Efficienza operativa: Automatizzando il processo di riordino, il sistema riduce al minimo i tempi di fermo e mantiene un flusso di materiale verso il reparto produttivo regolare.
-
Riduzione degli errori: La gestione digitale elimina gli errori umani legati alla gestione dei cartellini, migliorando la precisione e riducendo i costi operativi.
-
Scalabilità e flessibilità: Il sistema può essere facilmente espanso per includere nuovi display o funzionalità aggiuntive, adattandosi alle esigenze crescenti della tua produzione.
-
Maggiore coinvolgimento degli operatori: I display digitali offrono un'interfaccia intuitiva e facile da usare, migliorando il coinvolgimento e la soddisfazione degli operatori.
E-Kanban: Il caso di una fabbrica Automobilistica Italiana
Un'importante azienda italiana del settore automotive si trovava spesso in difficoltà con il riordino dei componenti, affidandosi ancora a cartellini Kanban cartacei. La gestione manuale causava ritardi, errori e stock eccessivi. Decisa a migliorare l'efficienza, l'azienda ha scelto di implementare il sistema E-Kanban di ThinkIN.
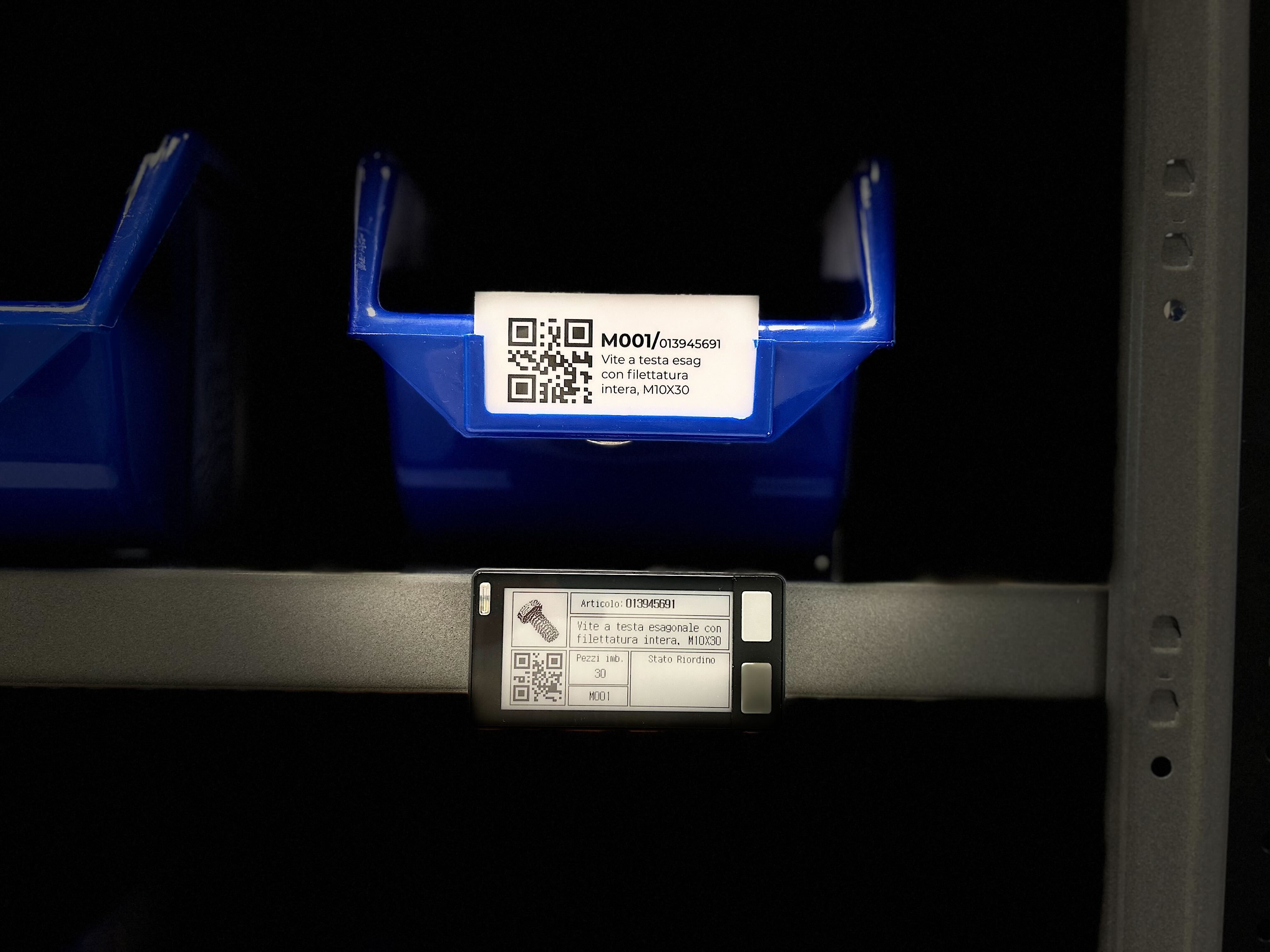
La situazione di partenza
Prima di implementare il sistema E-Kanban di ThinkIN, la fabbrica utilizzava il metodo Kanban tradizionale, basato su cartellini cartacei per segnalare il riordino dei componenti bordo linea. Questo processo richiedeva agli operatori e di spostare i cartellini nei contenitori di riordino una volta esaurito il materiale. Tuttavia, spesso accadeva che:
- I cartellini venivano persi o mal posizionati, causando ritardi nella richiesta di riordino.
- L'operatore del magazzino non sempre notava immediatamente i cartellini di riordino, prolungando i tempi di attesa.
- La pianificazione del riordino risultava inefficiente, portando a stock eccessivi o, al contrario, a rotture di stock che interrompevano la produzione.
La situazione risultava in tempi di fermo macchina frequenti, ritardi nelle consegne ai clienti e uno spreco significativo di risorse per la gestione manuale delle scorte.
La Soluzione: implementazione dell'E-Kanban di ThinkIN
L'azienda ha deciso di implementare il sistema E-Kanban di ThinkIN per digitalizzare il processo di riordino e migliorare l'efficienza operativa. La transizione è avvenuta in modo graduale, partendo da una singola stazione di montaggio per testare la nuova soluzione e monitorare i benefici. Ecco come è stato strutturato il progetto:
- Installazione dei Display Digitali Ogni postazione di lavoro è stata dotata di display digitali personalizzabili, collegati in rete con il sistema gestionale dell'azienda. I display mostrano informazioni dettagliate su ciascun componente presente nella postazione di lavoro, inclusi codice articolo, descrizione e immagine.
-
Automazione e feedback immediato Quando un operatore nota che il livello di scorte si avvicina alla soglia minima, preme il pulsante sul display. La richiesta viene trasmessa istantaneamente al magazzino, e il display si aggiorna in tempo reale, indicando che la richiesta è stata ricevuta e presa in carico. Se l'operatore rileva un'urgenza, può utilizzare la funzione "long press" per segnalare una priorità alta, evidenziata immediatamente nel gestionale con un avviso speciale.
-
Monitoraggio in tempo reale e analisi dei dati Tutte le richieste di riordino vengono registrate nel sistema di backoffice, dove i manager possono visualizzare lo stato delle richieste, il tempo medio di risposta e i colli di bottiglia nel processo. Grazie a un cruscotto di analitiche, l'azienda ha potuto analizzare i dati storici e ottimizzare la pianificazione del magazzino, riducendo significativamente i tempi di attesa.
Risultati pratici
In soli sei mesi, l'azienda ha ottenuto:
- Riduzione del 20% dei tempi di riordino, grazie alla trasmissione istantanea delle richieste.
- Zero sprechi: le scorte sono state mantenute ottimali, eliminando l'eccesso di inventario.
- Aumento del 10% dell'efficienza operativa, con operatori che ora possono concentrarsi su attività a maggior valore.
Il responsabile di logistica ha dichiarato: "Con l'E-Kanban abbiamo finalmente risolto i problemi di riordino. È un sistema pratico e affidabile che ha migliorato significativamente il nostro processo produttivo e la gestione del magazzino."
Conclusione
L'E-Kanban di ThinkIN ha dimostrato di essere una soluzione semplice ma potente per digitalizzare e ottimizzare il riordino dei componenti. Se stai cercando di ridurre i tempi di fermo e ridurre/eliminare le rotture di stock migliorare l'efficienza, l'implementazione di un sistema E-Kanban potrebbe fare al caso tuo.