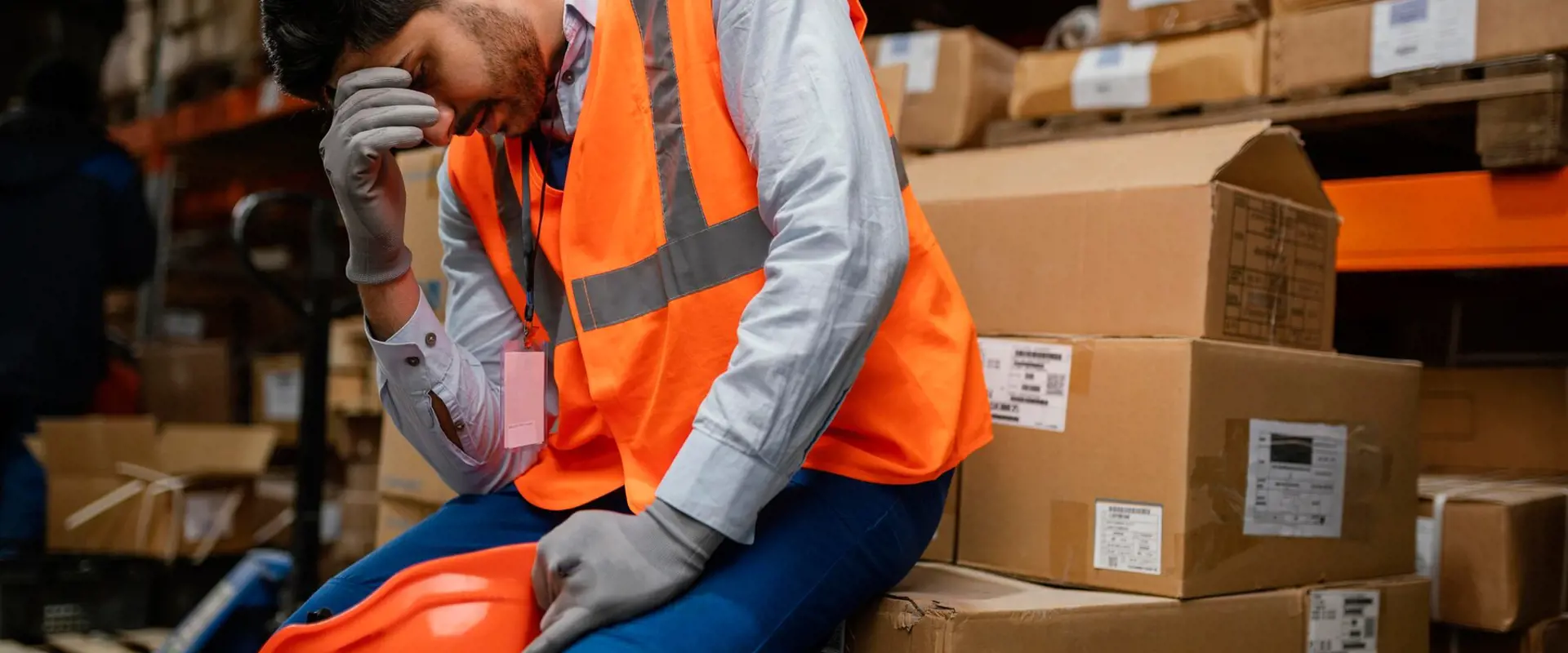
Sapresti calcolare quanto tempo impieghi al giorno nel cercare un lotto smarrito?
Ti sei mai chiesto quanto tempo impieghi ogni giorno a cercare lotti smarriti in un ambiente aziendale frenetico? Uno studio condotto su 120 aziende manifatturiere italiane rivela che il 76% perde circa 2 ore al giorno nella ricerca di elementi fondamentali, influenzando la produttività e generando stress. Esplora casi d'uso pratici e immagina un futuro in cui il tempo dedicato alle ricerche venga impiegato in attività più significative.
- Realizza qual'è l'impatto causato dalla perdita di tempo nel cercare lotti andati persi
- Conosci le soluzioni tecnologiche IoT adatte a te
- Esplora i 3 principali casi d'uso
Uno studio realizzato da noi
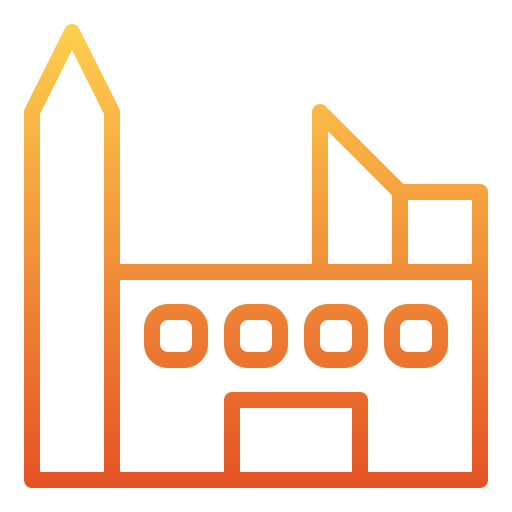
del settore manufacturing, internazionale e di dimensioni medio-grandi.
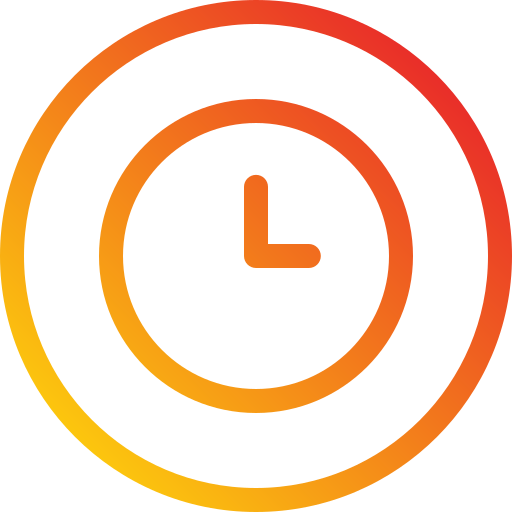
nella ricerca di semilavorati e oggetti di varie dimensioni
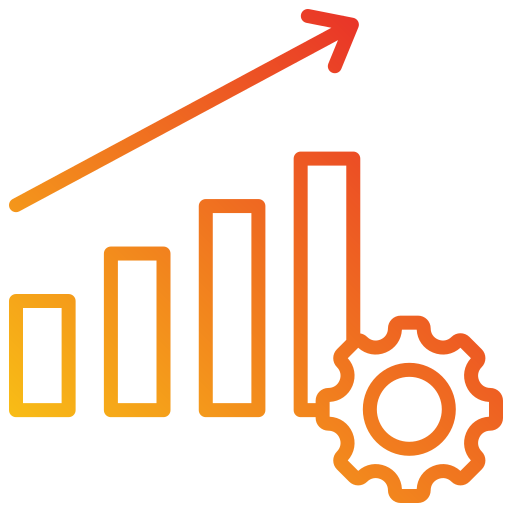
stimata durante le fasi di pianificazione
In un contesto aziendale sempre più frenetico, quanto tempo perdi nella ricerca di elementi fondamentali per il processo produttivo? Secondo uno studio da noi condotto su un campione di circa 120 aziende del settore manifatturiero italiano, il 76% perde circa 2 ore al giorno nella ricerca di semilavorati e oggetti di varie dimensioni (da carrelli e pallet a attrezzi di lavoro e minuteria). In pratica, quel tempo viene perso per assemblare i WIP come conseguenza del fatto che a volte dei lotti vanno persi o spostati e non è per nulla immediato riuscire ad individuarli.
Questo implica che il responsabile del reparto debba assegnare un paio di persone alla ricerca di ciò che è andato smarrito, interrompendo il loro lavoro effettivo, se non addirittura aggiungendo ore straordinarie. Di fatto le aziende perdono tempo prezioso e pagano risorse per la ricerca e movimentazione dei lotti, perdendo così almeno 2 ore al giorno di produttività. Tutto questo si traduce in costi aggiuntivi e in livelli di stress che aumentano a dismisura. Ti ritrovi in questo scenario?
Se moltiplicassimo queste 2 ore per una settimana lavorativa, fanno 10 ore settimanali; 40 ore al mese, 560 all’anno. Ma riflettici: questo tempo potrebbe essere impiegato in modo molto più efficiente.
Le cause principali di questo scenario possono essere molteplici.
Innanzitutto, questa situazione si verifica principalmente nelle produzioni di tipo discreto, dove un lotto può passare attraverso un reparto più di una volta o richiedere lavorazioni a più fasi. Non è, ovviamente, il caso di una catena di montaggio.
Inoltre, si tratta di lotti che vengono spesso disposti su carrelli e trasportati manualmente da un reparto all'altro. Senza alcun codice identificativo, capita spesso che l'operatore sposti il carrello sbagliato o che saltino le regole del FIFO (first in, first out), se si tratta di una produzione di quel tipo.
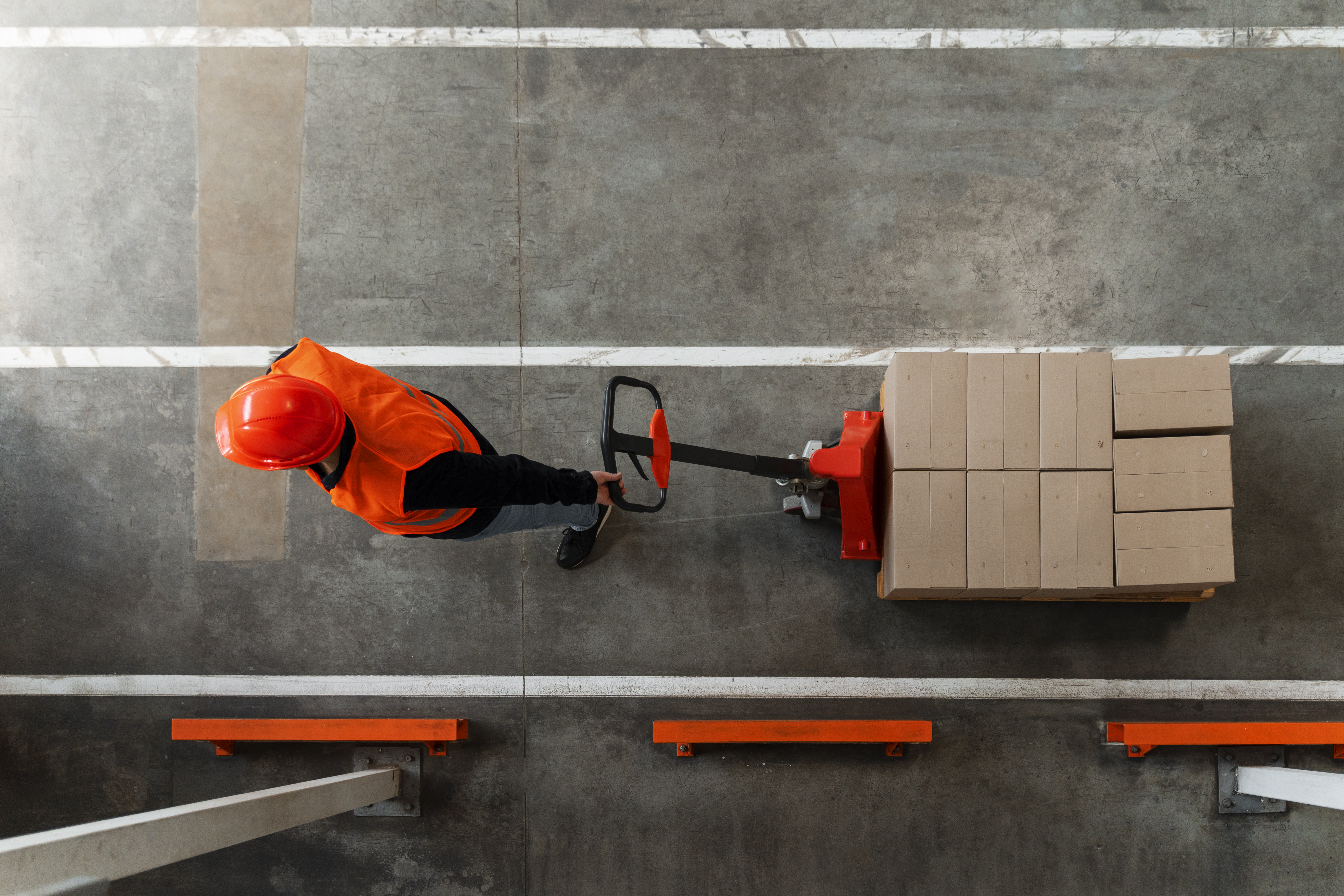
La gestione inefficace dei sistemi informativi aziendali e la mancata integrazione tra i software contribuiscono ulteriormente all'inefficienza produttiva. Nonostante molte aziende utilizzino sistemi MRP nei loro ERP aziendali per la gestione del materiale, la mancanza di strumenti adeguati per verificare i tempi di produzione e calcolare la capacità produttiva provoca colli di bottiglia e ferma carrelli per lunghi periodi, portando a una significativa perdita di efficienza, stimata attorno al 30% durante le fasi di pianificazione.
Per garantire un miglioramento sostenibile delle dinamiche produttive, è fondamentale adottare una visione a lungo termine, orientata all'innovazione e all'ottimizzazione continua. In questo contesto, superare gli ostacoli legati alla perdita di efficienza richiede un approccio integrato e tecnologico, che non si limiti a interventi superficiali, ma investa nella trasformazione strutturale dei processi aziendali e cioè nella trasformazione digitale.
L'implementazione di soluzioni avanzate, come sistemi intelligenti di monitoraggio e controllo, rappresenta un primo passo verso una gestione più efficiente delle risorse. Questi sistemi non solo forniscono una visibilità in tempo reale dei processi produttivi, ma permettono anche l'analisi dei dati per identificare punti critici e ottimizzare le operazioni.
Allo stesso modo, sfruttare le tecnologie emergenti, come l'integrazione di dispositivi IoT e l'uso di algoritmi avanzati, consente una comunicazione più rapida e precisa tra i reparti. Questo non solo riduce gli errori derivanti da informazioni obsolete o incomplete, ma facilita anche una collaborazione sinergica tra i team, contribuendo a superare le sfide legate alla dispersione di tempo e risorse.
Inoltre, l'investimento in avanzati sistemi di gestione del magazzino diventa cruciale per garantire una tracciabilità accurata degli inventari e una gestione ottimale dei materiali. La previsione della domanda futura e l'ottimizzazione della disposizione dei materiali sono obiettivi che possono essere raggiunti attraverso l'applicazione di tecnologie avanzate e l'analisi predittiva.
Vediamo ora alcuni casi d'uso pratici nei quali adottare una soluzione RTLS ha portato ad un miglioramento generale dell’andamento produttivo:
Gestione del magazzino di prodotti finiti:
Se gestisci un magazzino di prodotti finiti, in cui i pallet vengono stoccati in modo dinamico, e desideri ridurre al minimo il tempo per trovarli, la soluzione potrebbe essere l'integrazione di un sistema RTLS e una piattaforma di location intelligence. Con questa tecnologia è possibile rilevare con precisione submetrica la posizione dei prodotti finiti in magazzino, accelerando le operazioni di prelievo e fornendo una visione completa in tempo reale delle risorse presenti e di quelle in uscita.
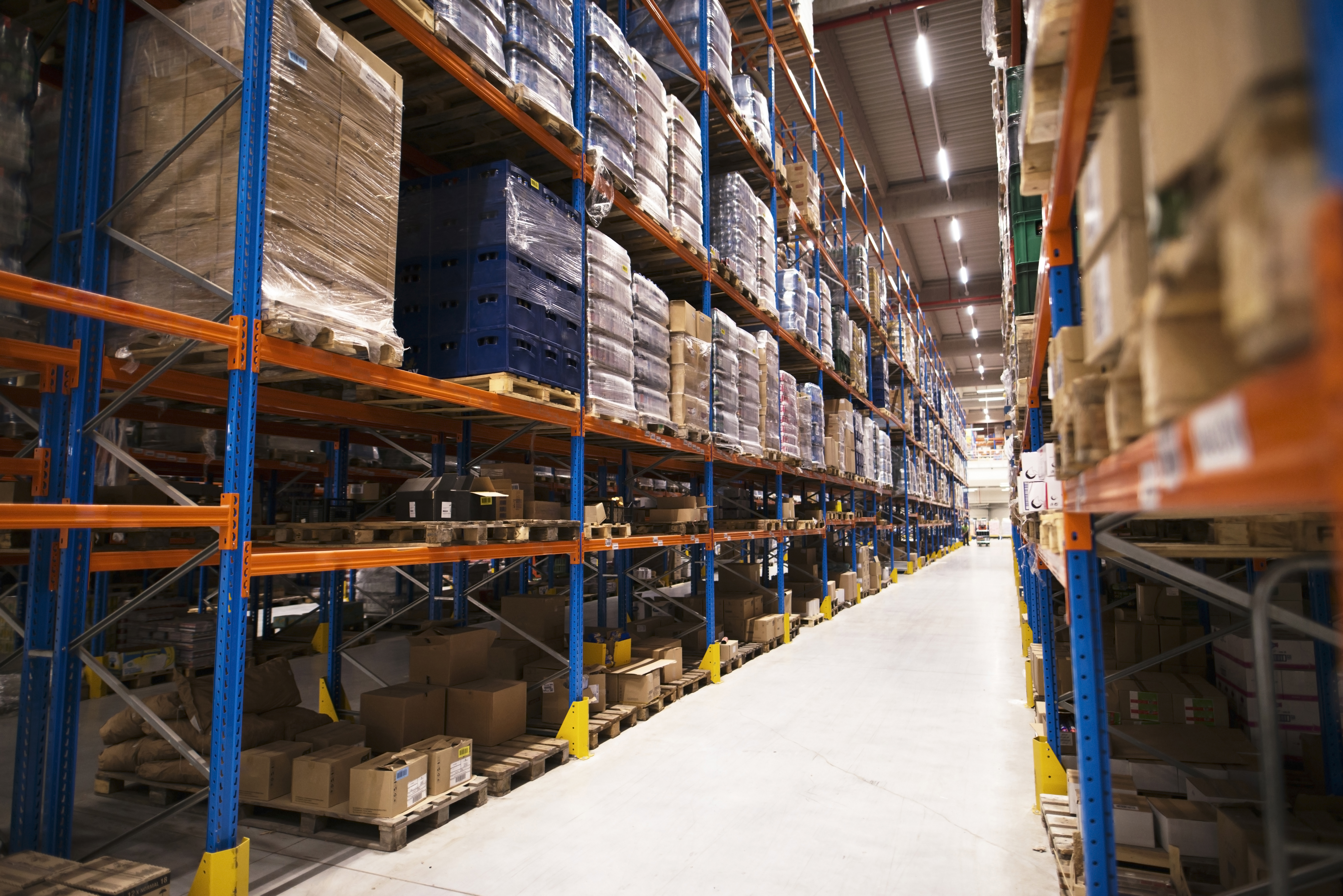
Manutenzione di veicoli a guida automatizzata (AGV):
Un'altra modalità operativa consiste nel tracciare gli AGV utilizzati per spostare merci, semilavorati e materiali in tutto lo stabilimento di produzione e garantire che siano sottoposti a regolari operazioni di manutenzione. Ciò risolverebbe il problema di non sapere mai dove si trovano, dato che si muovono autonomamente all’interno dei grandi impianti di produzione. Conoscere la posizione in tempo reale degli AGV con grande precisione è anche molto utile per la sicurezza aziendale, prevenendo collisioni con muletti e/o altri operatori.
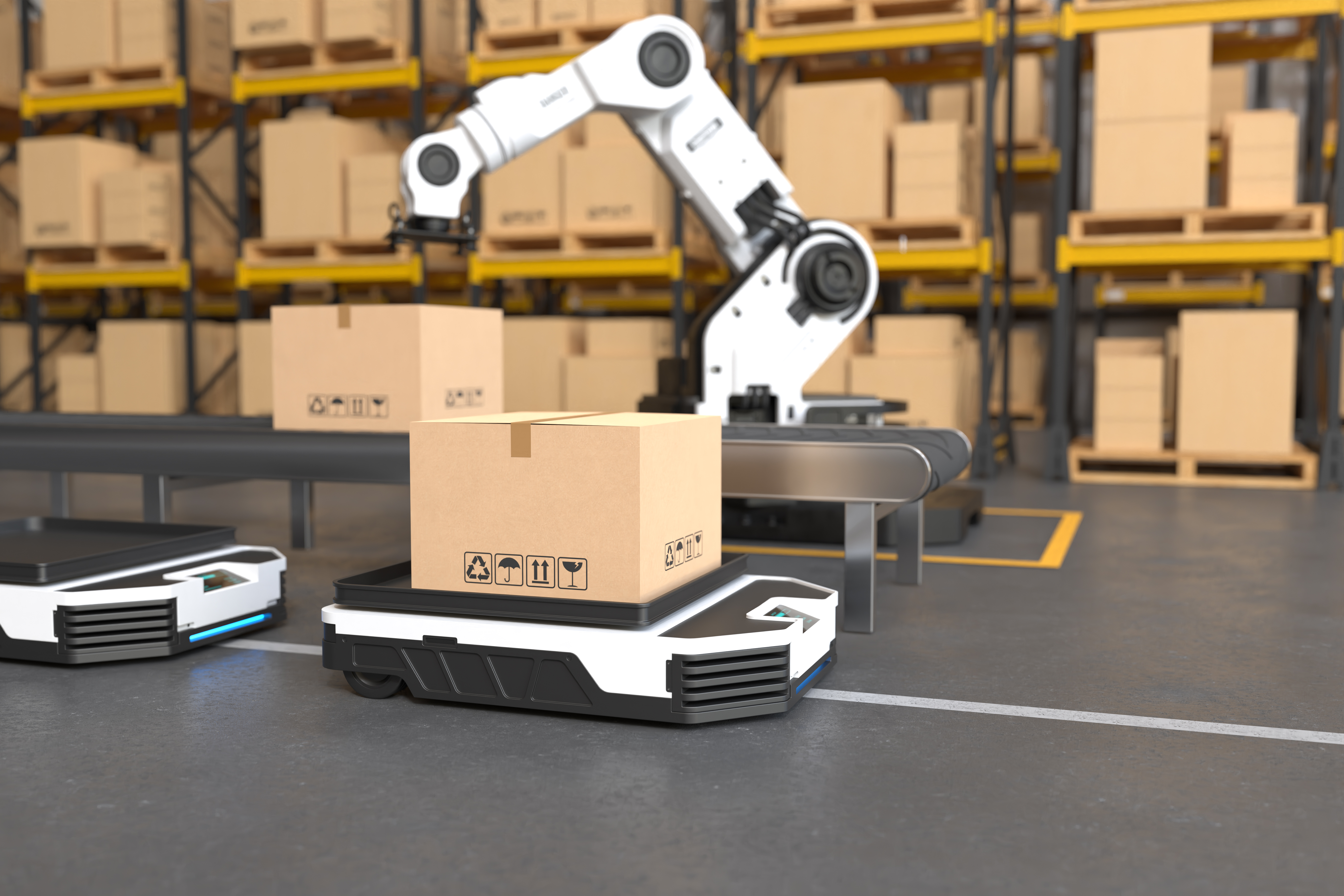
Monitoraggio WIP con etichette digitali:
Se di solito non tracci il WIP sulle rulliere della linea di produzione o principalmente sui banchi di assemblaggio, grazie alla tecnologia RTLS puoi seguire ogni spostamento direttamente dall'ufficio. Ancora meglio, puoi comunicare direttamente con gli operatori sul campo tramite etichette digitali applicate direttamente sui lotti produttivi. In questo modo, le informazioni sull'etichetta in sala produzione corrisponderanno a quelle visualizzate sul tuo computer. Ad esempio, se un lotto deve passare dalla fase di saldatura a quella di verniciatura, l'etichetta mostrerà un comando per indicare la fine della saldatura e la disponibilità per la verniciatura. Cliccando sul pulsante dell'etichetta, questa informazione sarà aggiornata anche sul tuo sistema informatico. Questo approccio, inoltre, può essere applicato in vari scenari, come nel caso di una produzione che segue il metodo Kanban.
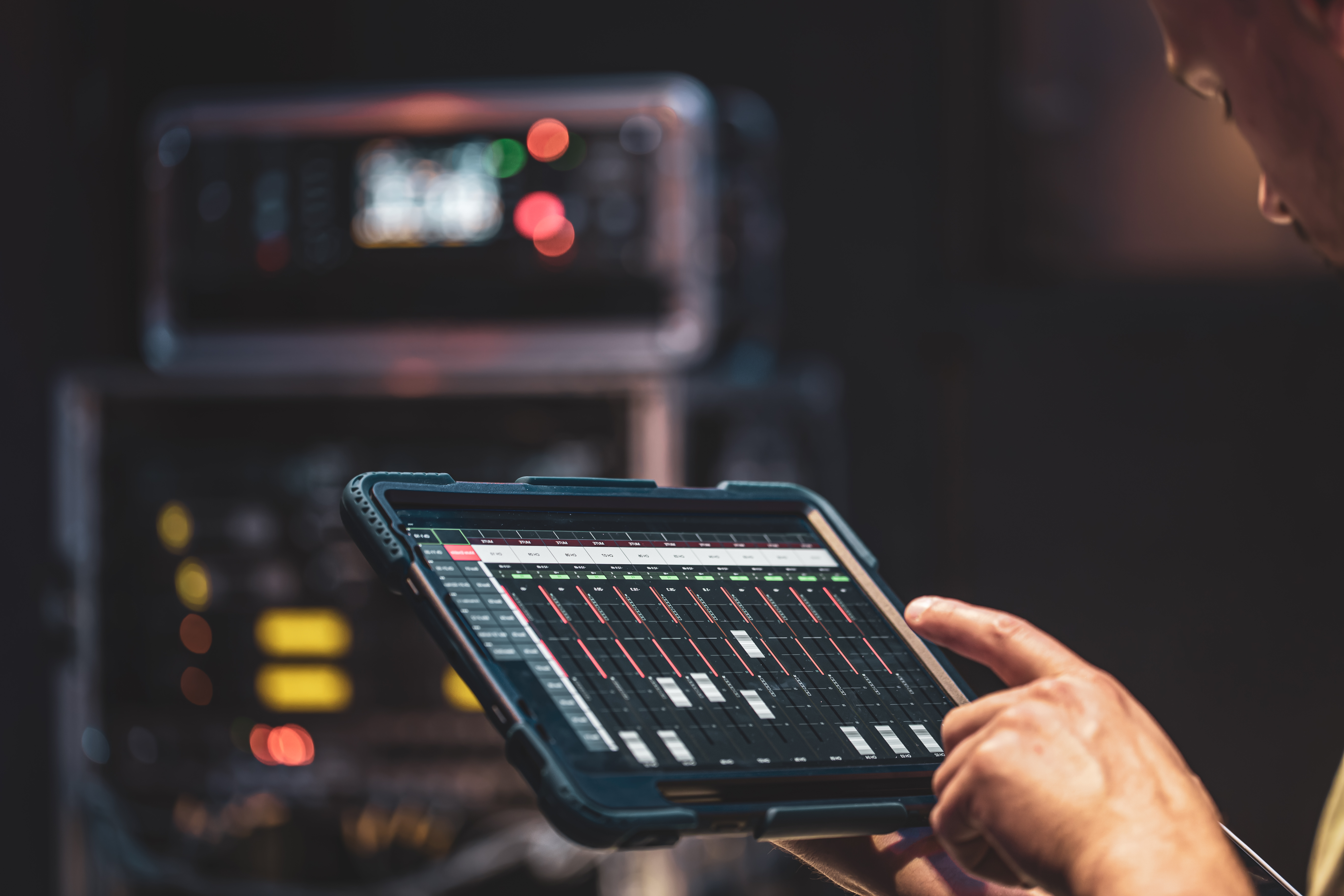
In sintesi, abbracciare una mentalità di innovazione continua e adottare soluzioni tecnologiche avanzate non solo affronta le sfide immediate legate alla perdita di efficienza, ma crea anche una base solida per il futuro. Questo approccio non solo riduce i tempi persi nella ricerca di materiali, ma promuove una crescita sostenibile della produttività complessiva, posizionando l'azienda in modo più competitivo e resiliente sul mercato in continua evoluzione.