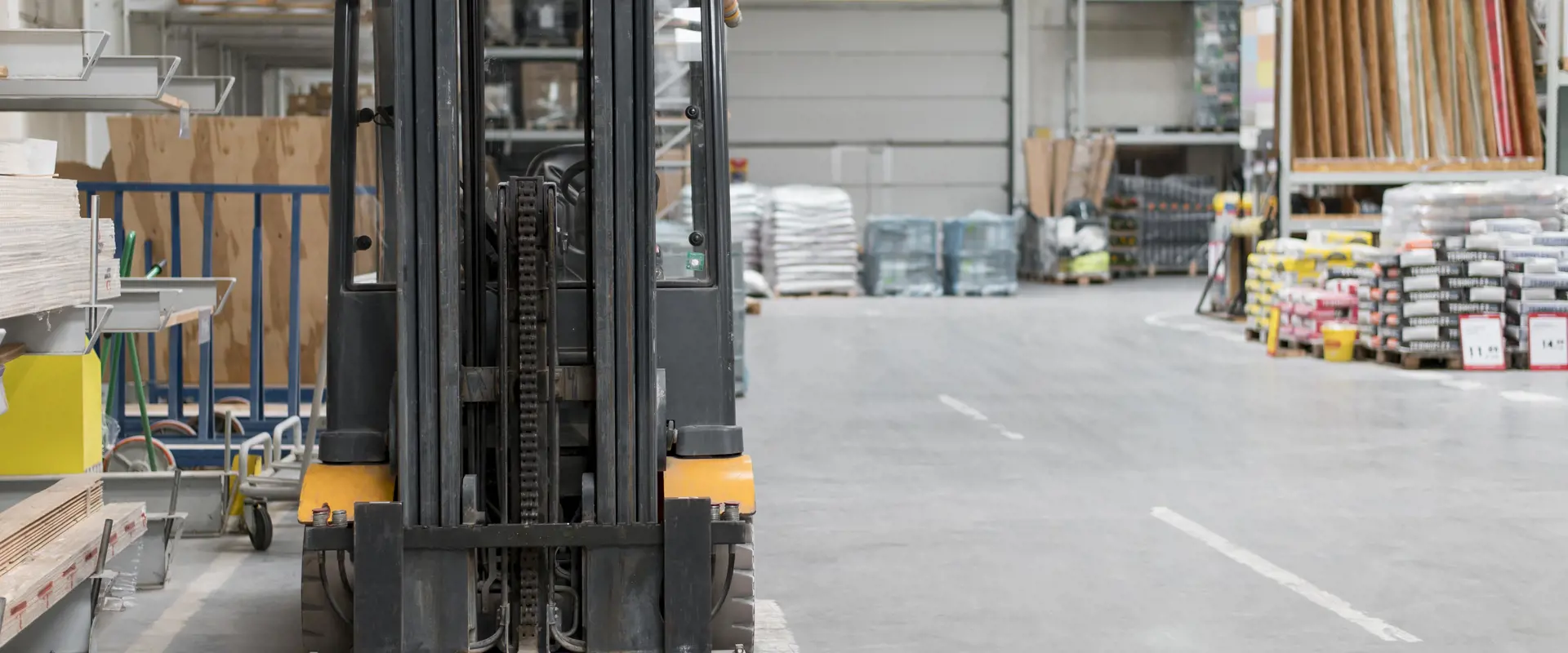
Material Handling: how to eliminate inefficiencies and optimize production with smart management
Material handling is a crucial process for any manufacturing company.
When properly managed, it ensures smooth production flows, reduces waste, and boosts productivity.
However, the reality is often quite different: delays, missing materials, inefficient handling equipment, and difficulties in coordinating operations.
- Material handling has a direct impact on lead times, costs, and production continuity. Yet, it is often managed with traditional tools and limited traceability.
- A digital and integrated approach makes it possible to optimize every flow — from material tracking to mission management for handling equipment.
- Thinkin offers concrete solutions to make Material Handling more efficient, visible, and synchronized with production.
According to a recent study by McKinsey & Company, waiting and handling times account for up to 40% of a product’s total lead time. Additionally, 47% of manufacturing companies lack real-time visibility over materials, leading to errors, waste, and unexpected disruptions.
Individual production steps are typically tracked through a MES system. However, especially in discrete manufacturing, materials are moved by operators using equipment (e.g., forklifts, pallet trucks) or manually (hand pallet jacks). These handling operations are often unrecorded, relying on operator processes and experience, resulting in a lack of visibility and control over material movements over time.
How can these issues be solved?
With a digital and integrated approach to Material Handling!
Digital, because every movement, request, tracking, and interaction is managed in real time through technology — with no paper and no manual processes.
Integrated, because all systems — production, logistics, warehouse, and internal fleets — communicate with each other, exchanging data and triggering automated actions such as:
-
Assigning missions to forklifts
-
Operational alerts (Andon)
-
Line-side stock updates
-
Asset localization
The result? A factory that can see, anticipate, and optimize every material flow — with no bottlenecks, waste, or inefficiencies.
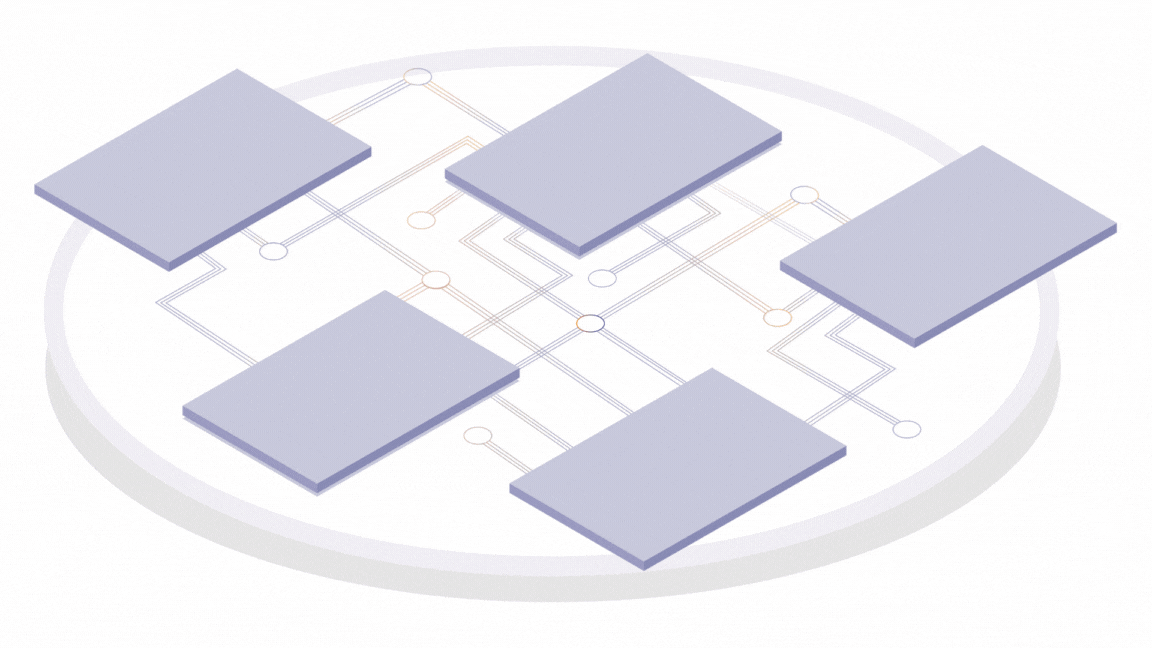
1. Lack of visibility over materials
A common issue in manufacturing plants is not knowing exactly where all materials, semi-finished products, and equipment are located.
Even if this affects only a small portion of the materials being moved, it can have a significant impact on productivity and on the workload of specialized operators.
Lack of visibility over materials can lead to:
- Wasted time, as operators spend valuable time searching for specific orders or materials.
- Production delays, because if a specific material arrives late at a certain production stage, it can affect the overall lead time.
- Logistics errors, with parts picked up or delivered to the wrong place.
- Low forklift efficiency, with non-optimal routes and sometimes empty trips.
Key data:
- 40% of an operator’s time is wasted searching for materials or equipment.
- Forklifts in an average plant operate at less than 50% efficiency.
Thinkin Solution
RTLS and GPS Tracking
Thinkin offers a wide range of technologies and solutions for tracking materials and semi-finished products, both in indoor and outdoor environments. Among the technologies adopted, we provide RTLS (Real-Time Locating System) for tracking in indoor or confined spaces, GPS for tracking assets across large areas, and RFID for detecting entry/exit from specific zones.
✔ The position of materials is digitally tracked over time.
✔ Materials are always visible and searchable on a digital map.
✔ Operators know exactly where to pick up and deliver.
✔ Forklifts receive optimized missions to reduce empty trips.
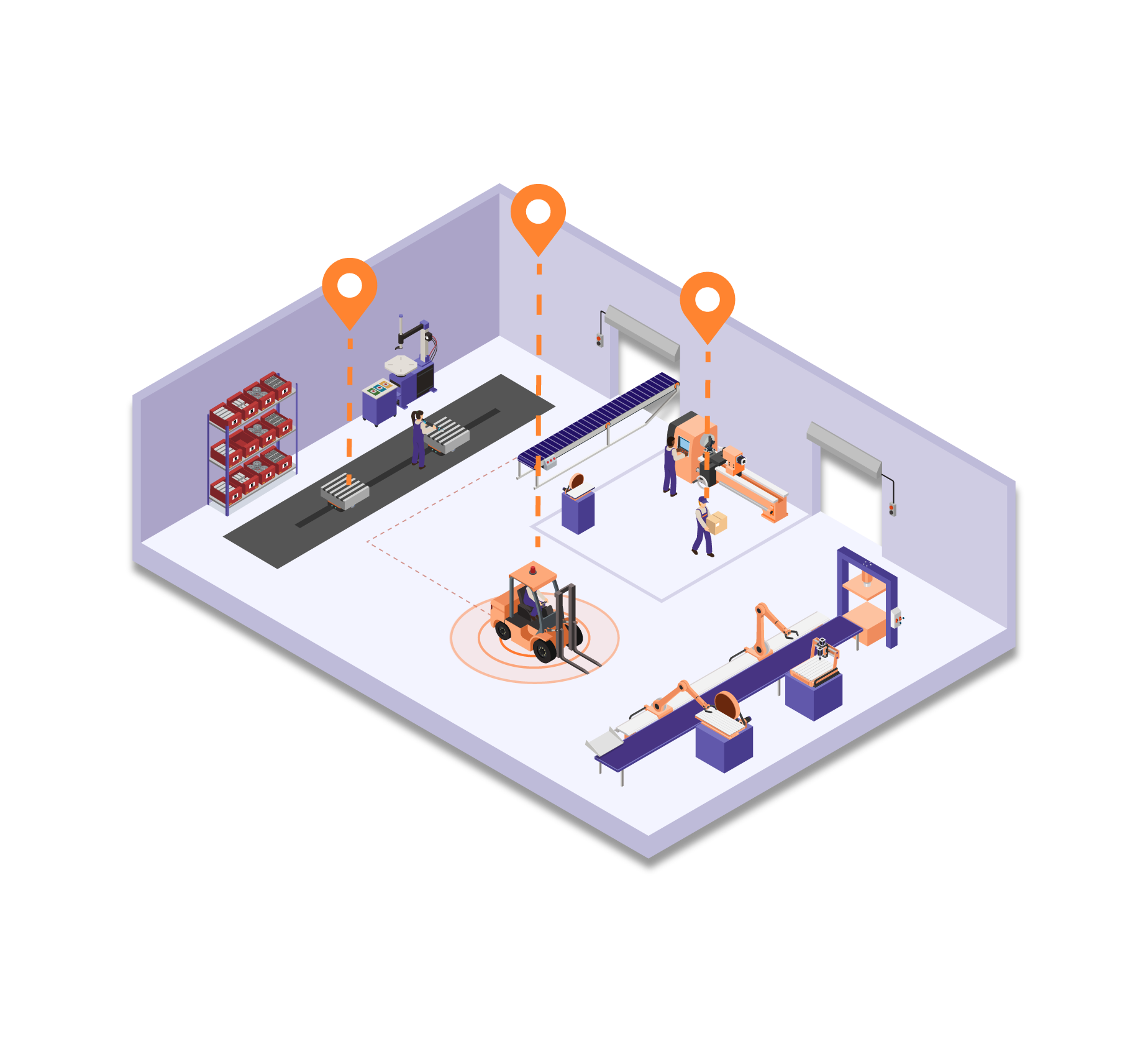
2. Slow replenishments and production delays
A production line must work in perfect sync with material supply and support requests. A line that slows down while waiting for a component results in high costs. Inefficient management of line-side materials can lead to:
- Errors and delays in material requests: requests are made verbally or on paper, causing confusion, duplicate requests, or missed deliveries.
- Excess or shortage of line-side stock: without a system that detects actual needs, there’s a risk of excess materials taking up space or shortages that block production.
- Long waiting times for operators: workers wait for the necessary materials to proceed, directly impacting productivity, efficiency, and costs.
Key data:
- 30–40% of total production lead time is due to inefficiencies in material handling.
Thinkin Solution
E - Kanban digitale and Andon Wireless
With digital E-Kanban, replenishment requests are automated.
Operators no longer need to manage paper cards or call the warehouse.
✔ The system automatically detects material needs and triggers replenishment.
✔ The warehouse receives accurate, real-time requests.
✔ Operators can report anomalies with a single click thanks to Andon Wireless, reducing machine downtime.
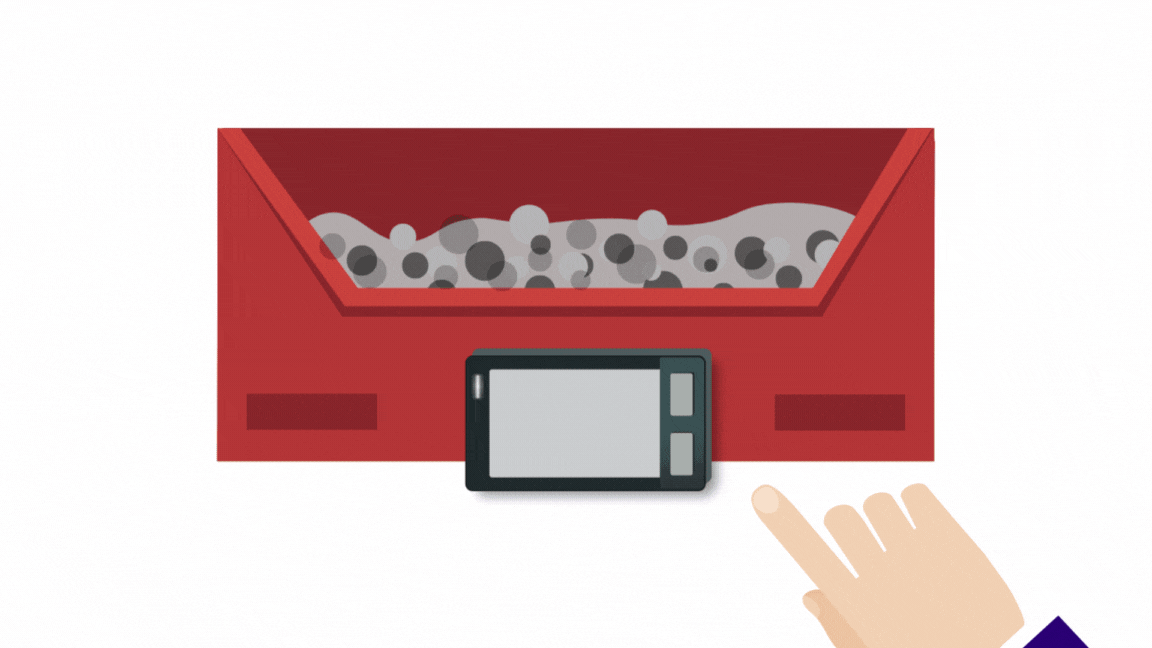
3. Paper-based processes and misaligned information
Many companies still use paper cards, spreadsheets, and verbal communication to manage Material Handling. This leads to:
- Transcription errors and lost orders.
- Outdated information between warehouse and production.
- Poor traceability of operations.
Key data:
- The use of paper in production processes can increase operational costs by up to 15%.
Thinkin Solution
Display Digitali
Digital displays provide constantly updated information directly on containers, shelves, and picking areas.
Pick-by-Light visually guides operators, reducing errors and speeding up operations.
✔ No more lost paper documents or outdated information.
✔ Operators receive clear, real-time instructions.
✔ Picking areas light up to indicate the correct material.
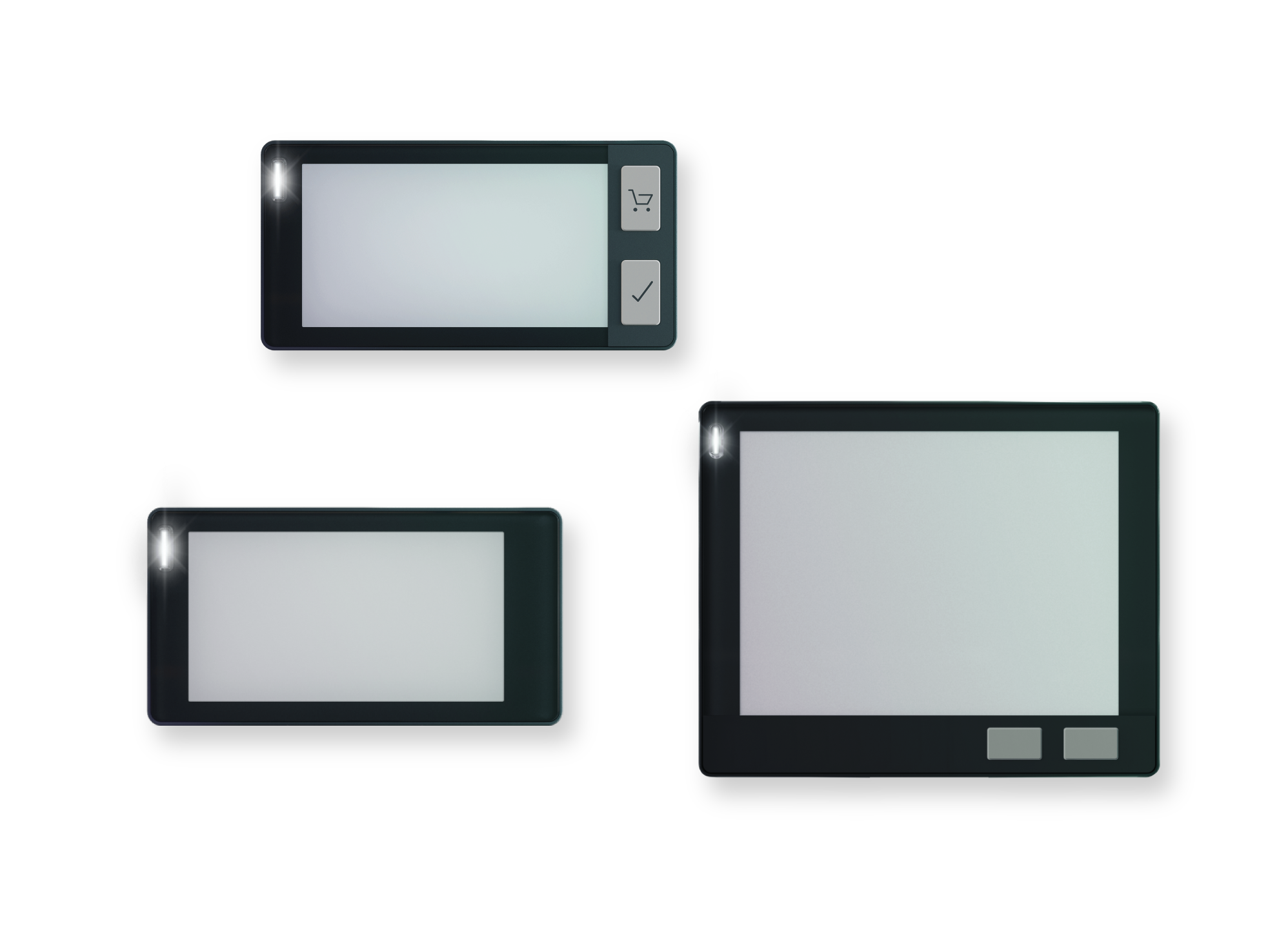
4. Unoptimized handling equipment
Handling equipment often operates without a clear logic, following inefficient routes and overlapping tasks.
Proper coordination is essential to optimize operational costs and ensure effective support for production.
A lack of coordination in material handling can lead to:
- Idle time and delays between activities.
- Congestion in production and warehouse areas.
- Increased operational costs.Dati chiave:
Optimizing internal fleets can reduce operational costs by 15–30%.
Thinkin Solution
Fleet Management and Mission Control
The Thinkin Fleet Management system monitors forklift activity in real time and assigns optimized missions.
✔ Smart assignment of missions to available vehicles.
✔ Optimized routes to reduce idle time and fuel consumption.
✔ Priority management enabled by Mission Control.
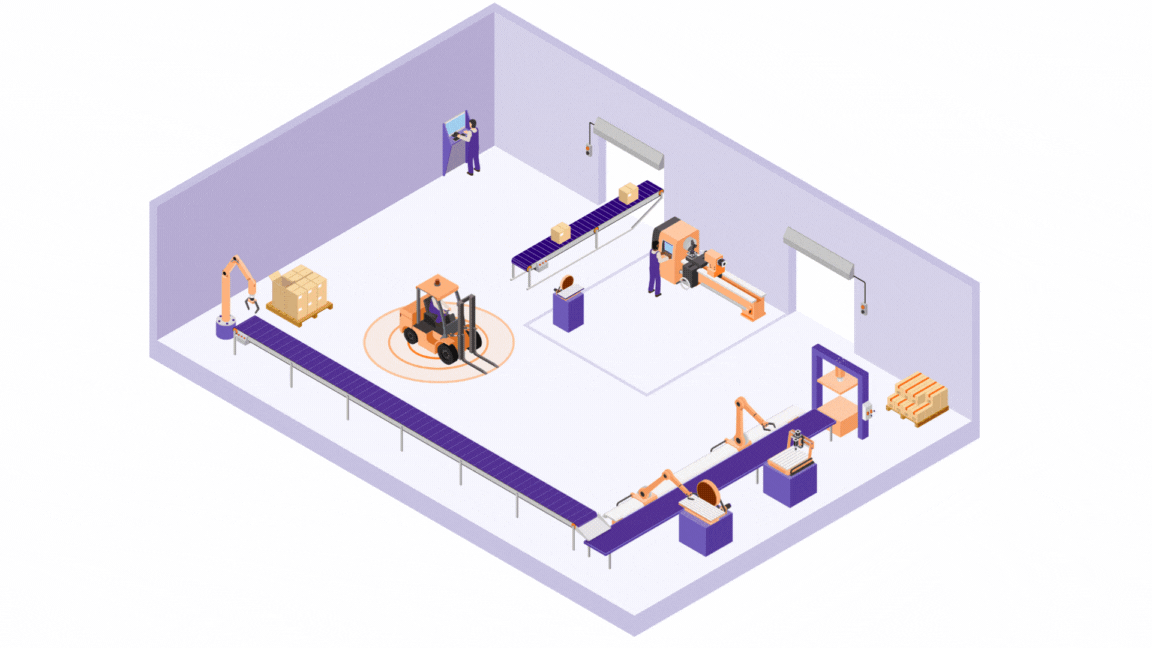
A new approach to Material Handling: smart, integrated, and efficient
Thanks to RTLS, GPS Tracking, e-Kanban, Andon Wireless, Digital Displays, Fleet Management, and Mission Control, Thinkin enables manufacturing companies to digitalize and optimize the entire handling process.
-
Greater efficiency in replenishment: materials always available where needed.
-
Full visibility: real-time monitoring of assets and vehicles.
-
Reduced operational costs: less waste and fewer delays.
-
Improved safety: lower risk of accidents and better working conditions.
Digital transformation is no longer an option, but a necessity for companies that want to stay competitive.
How far along are you in the digitalization of your Material Handling? 🎯
Find out in 2 minutes with our free quiz.
📊 Get your profile instantly and discover how to improve.
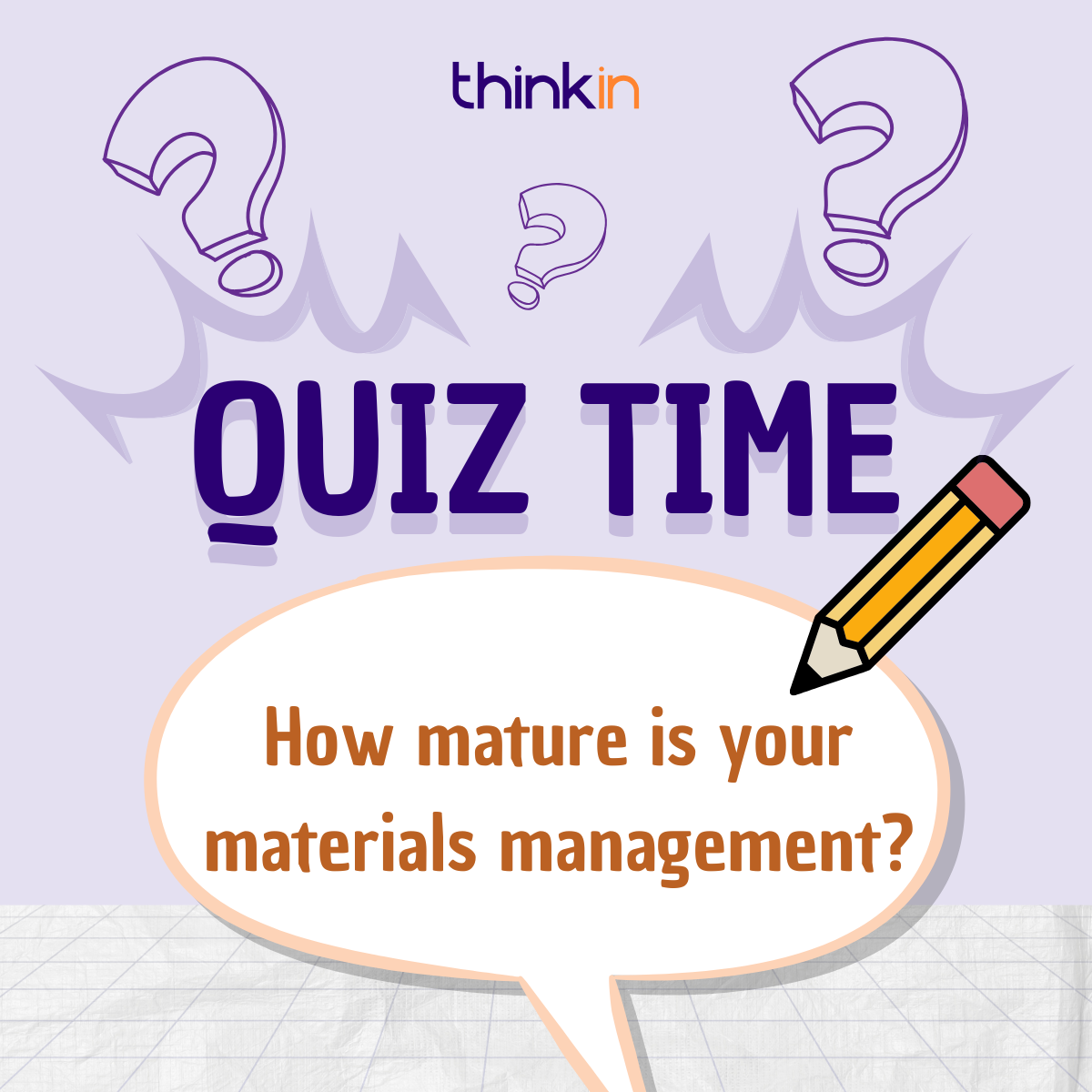
Download our brochure for your Material Handling
Enter your details below and download our free brochure!
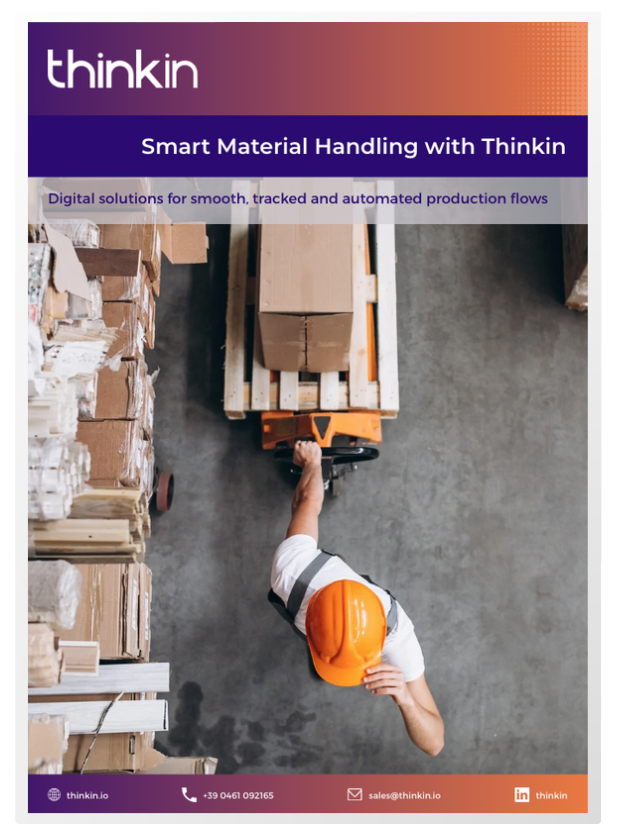