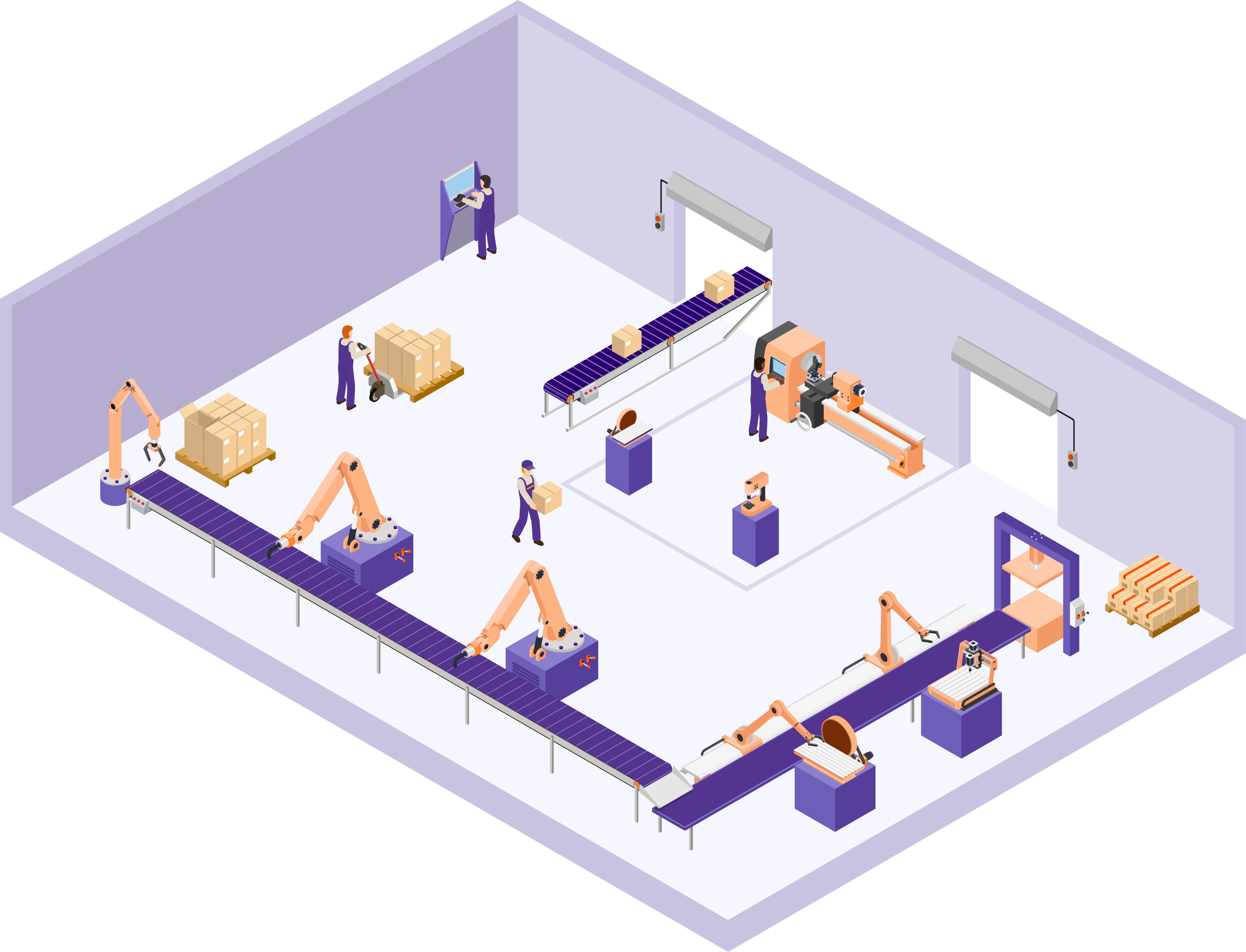
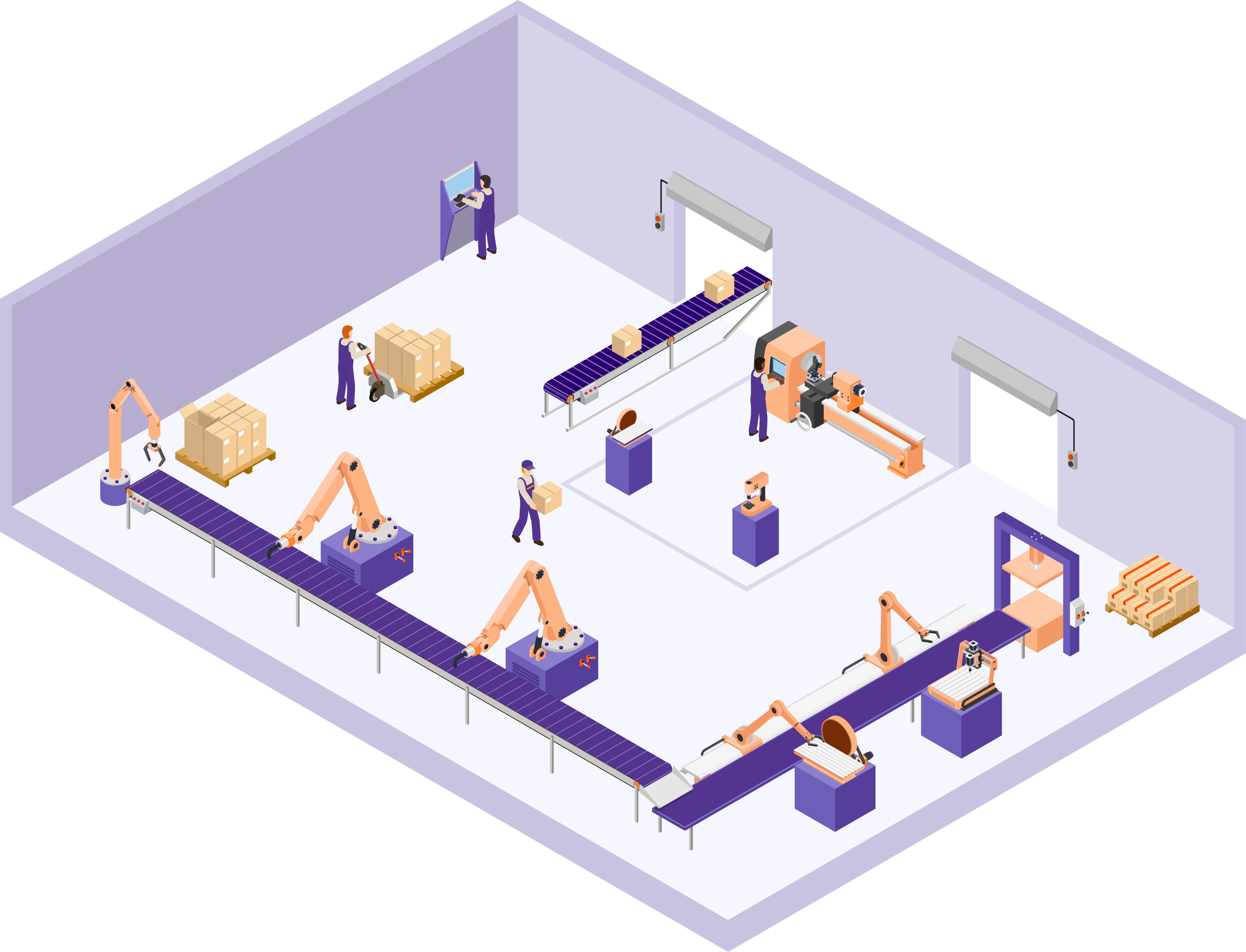
Real-time Digitalization for the Manufacturing Industry
In the manufacturing sector, challenges related to productivity, traceability, and resource management demand concrete and scalable solutions. Thinkin digitizes factory operations through IoT technologies such as RTLS and digital displays, providing full visibility over assets, production flows, and operational activities.
With our platform, companies can optimize processes, reduce waste, and improve performance—accelerating the transition toward a connected, data-driven factory model.
Your factory: connected, efficient, and smart.
What We Do
Thinkin is an IIoT platform designed to digitalize every aspect of factory operations.
We offer modular services that cover production, internal logistics, warehouse management, process monitoring, and safety.
By leveraging technologies such as RTLS, IoT sensors, digital displays, and edge computing, we collect field data and turn it into real-time visibility, smart automation, and in-depth operational analytics.
Our services integrate seamlessly with existing systems like ERP, MES, and WMS—without disrupting the customer’s infrastructure.
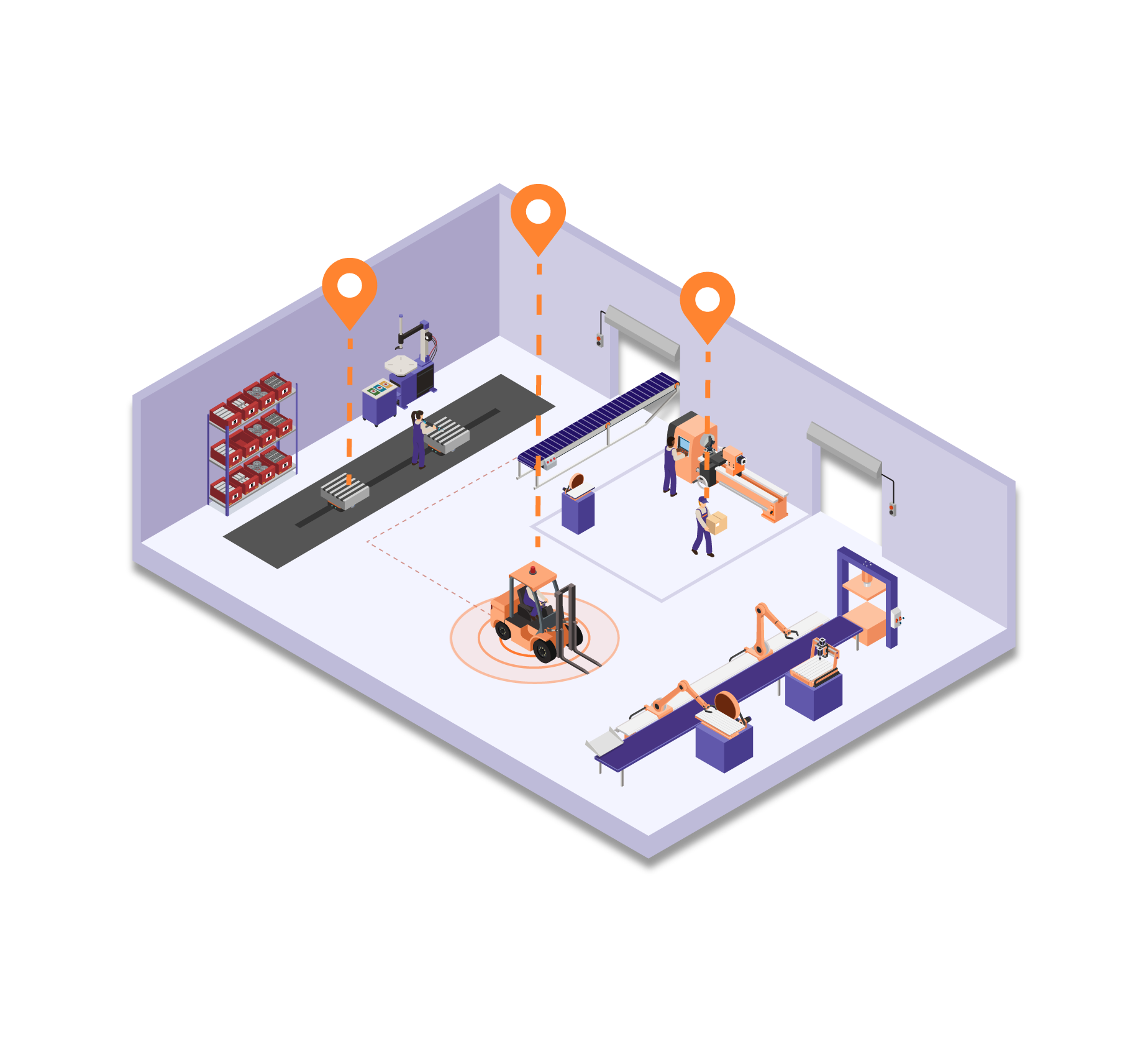
Why Choose Us
Because we help you improve efficiency, reduce waste, and boost your factory’s responsiveness—with a concrete, incremental, and customizable approach.
Every ThinkIN solution is designed to deliver measurable value from day one, supported by a clear roadmap for digital growth.
We work alongside you to optimize flows, cut downtime, and bring operational intelligence to every area of the plant—safely, scalably, and fully integrated with your existing processes.
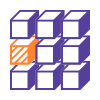
Using RTLS and IoT technologies, ThinkIN tracks equipment, reducing search times and optimizing resource utilization across the entire production line.
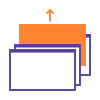
The platform collects and analyzes real-time data, highlighting inefficiencies and deviations from standard workflows.
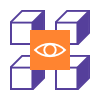
Digital displays, sensors, and smart scales enable automated replenishment management, enhancing efficiency and accuracy in intralogistics processes.
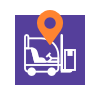
RTLS badges, emergency buttons, and equipment tracking help prevent risks and ensure the safety of both operators and environments.
Our Applications
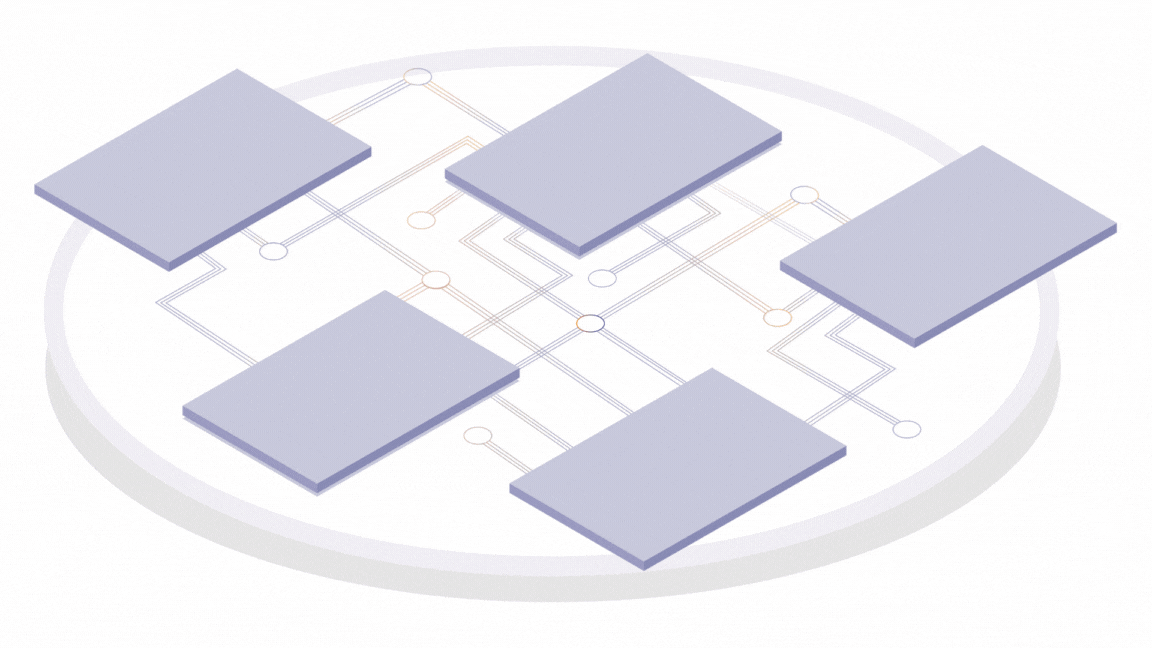
Material Handling: Optimize Material Movement Within the Plant
Thinkin tracks flows, equipment, and handling vehicles in real time to improve internal logistics, reduce transport times, and enhance safety.
Our services supporting material handling include: WIP Management, Fleet Management, E-Kanban, Mission Control, and Andon Wireless.
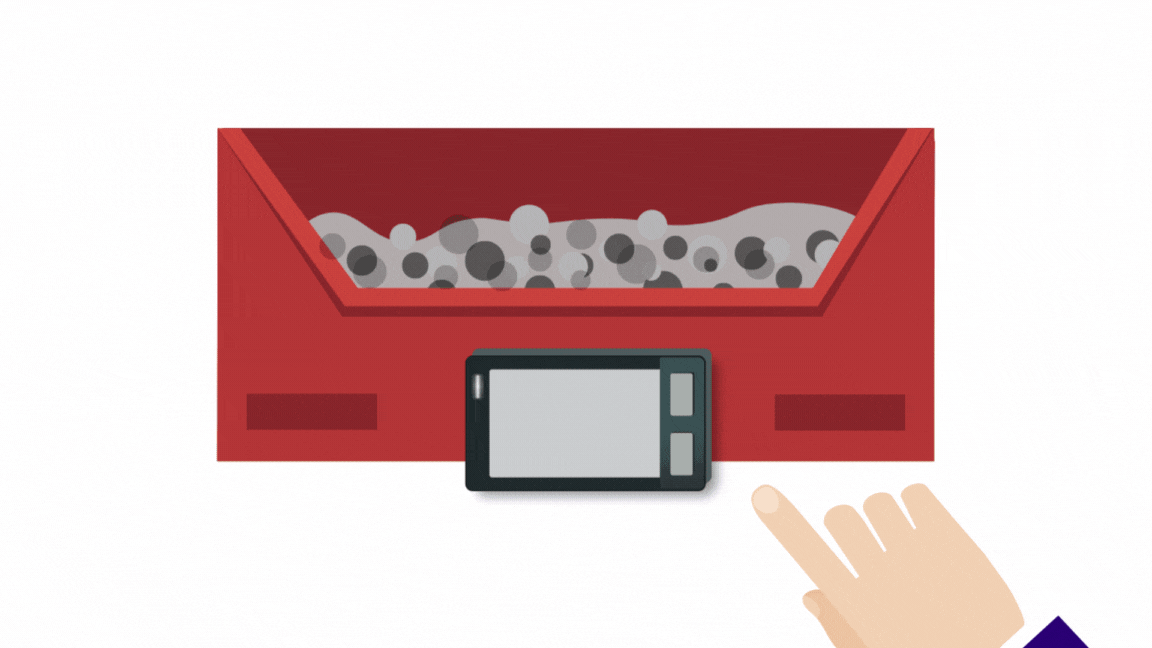
E-Kanban: Automate Line-Side Material Replenishment
Thinkin digitalizes replenishment processes with smart displays and wireless buttons, ensuring a continuous material flow and reducing downtime.
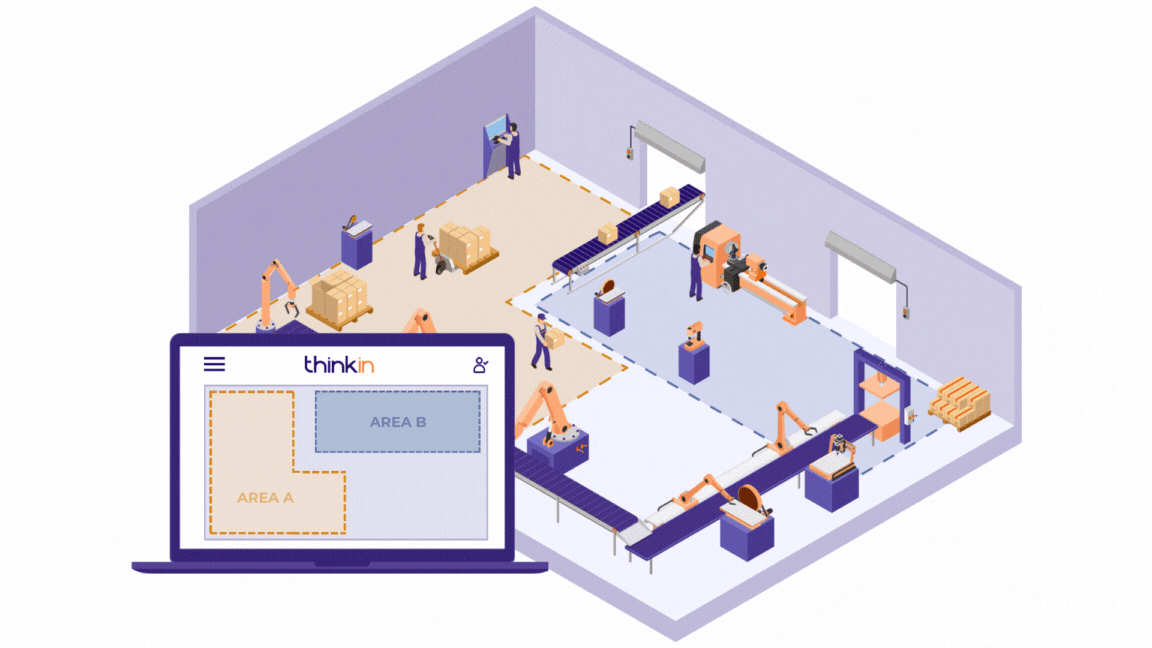
Tool Management: Track and Optimize Tool Usage in Real Time
With IoT technologies, Thinkin monitors tool location and usage, reducing search times, preventing waste, and improving maintenance.
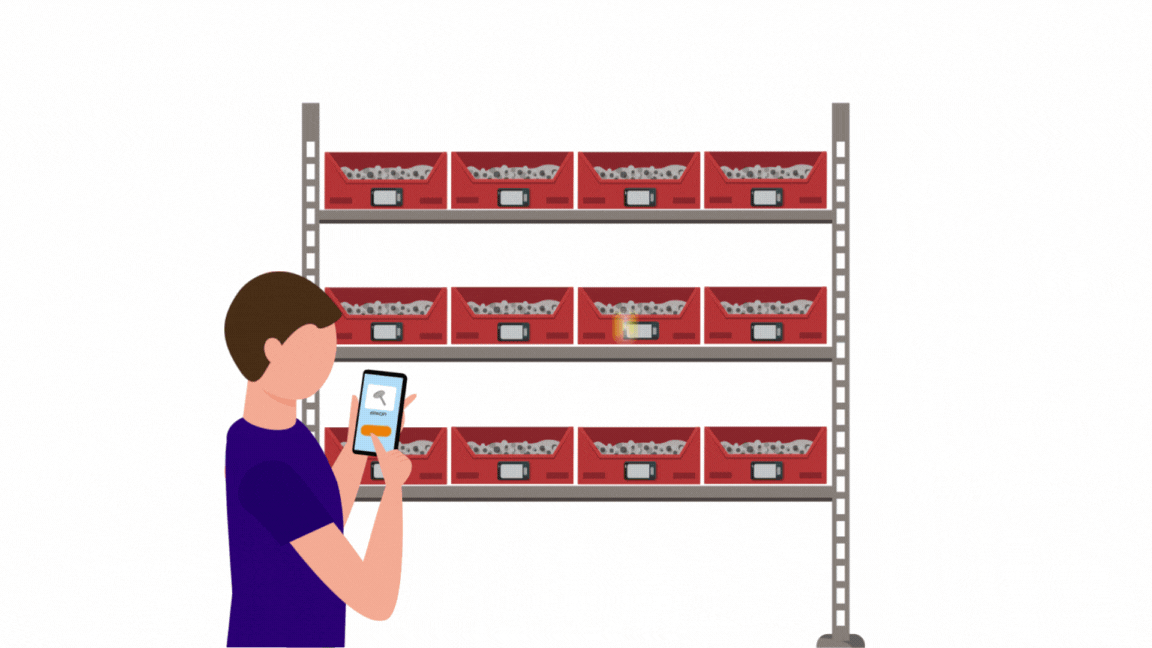
Simplify and Speed Up Production Picking
With guiding lights and visual cues, ThinkIN’s Pick by Light system supports operators in accurately retrieving materials—boosting both precision and speed.
Seamless Integration with Your Existing Systems
ThinkIN adapts to your needs: our platform integrates easily with existing systems such as ERP, WMS, and MES.
We provide a turnkey service—from technology demonstration to full installation—ensuring maximum added value.
Use Cases in Industry 4.0
1. Production Optimization with Real-Time Data on Processes and Assets
Ensuring operational continuity requires full visibility into what’s happening on the line. With ThinkIN, every stage of production is monitored in real time through the integration of RTLS, sensors, and wireless Andon buttons.
Our platform collects events, alerts, and performance data, displaying them on smart dashboards that help identify bottlenecks, machine downtimes, and process deviations.
The insights generated support operational planning, improve plant performance, and reduce downtime—ensuring a smooth and responsive production flow.
2. Traceability and Control of Moving Vehicles and Equipment
Inefficient movement of tools, materials, and internal vehicles can slow down processes and drive up operational costs.
ThinkIN tackles this challenge with services like Tool Management, Material Handling, and Fleet Management, leveraging RTLS, IoT sensors, and smart tags to track in real time the location and usage of forklifts, carts, and tools.
Through our interactive map, operators can visualize all moving resources and receive alerts on anomalies, overlaps, or delays. The system helps optimize routes, improve equipment availability, and reduce downtime and waste in internal logistics.
3. Advanced Control of Work In Progress (WIP) Along the Entire Line
Monitoring production progress is essential to meet deadlines and manage urgent orders effectively.
ThinkIN’s WIP Management service uses sensors, smart tags, and digital dashboards to track each batch or production unit across every stage of the process.
Companies gain real-time visibility into production status, with alerts in case of delays or stoppages.
This enables better prioritization, improved planning, and greater flexibility in managing orders—especially in highly variable manufacturing environments.
ThinkIN® digitalizes the entire factory operation by collecting real-time data from sensors, RTLS devices, and digital displays installed across production areas, warehouses, and logistics flows.
The platform transforms this data into operational visibility, continuously tracking the location of materials, tools, vehicles, and WIP across one or multiple plants.
With built-in business intelligence tools, Thinkin analyzes every production-related event—movements, stops, Andon calls, downtimes, and delays—providing KPIs, alerts, and insights to optimize time, resources, and operational decisions.
The solution is scalable, customizable, and enterprise-ready: it can be deployed in the cloud or on-premise, integrates easily with ERP, MES, and WMS systems, and ensures continuous monitoring of all hardware and software components.