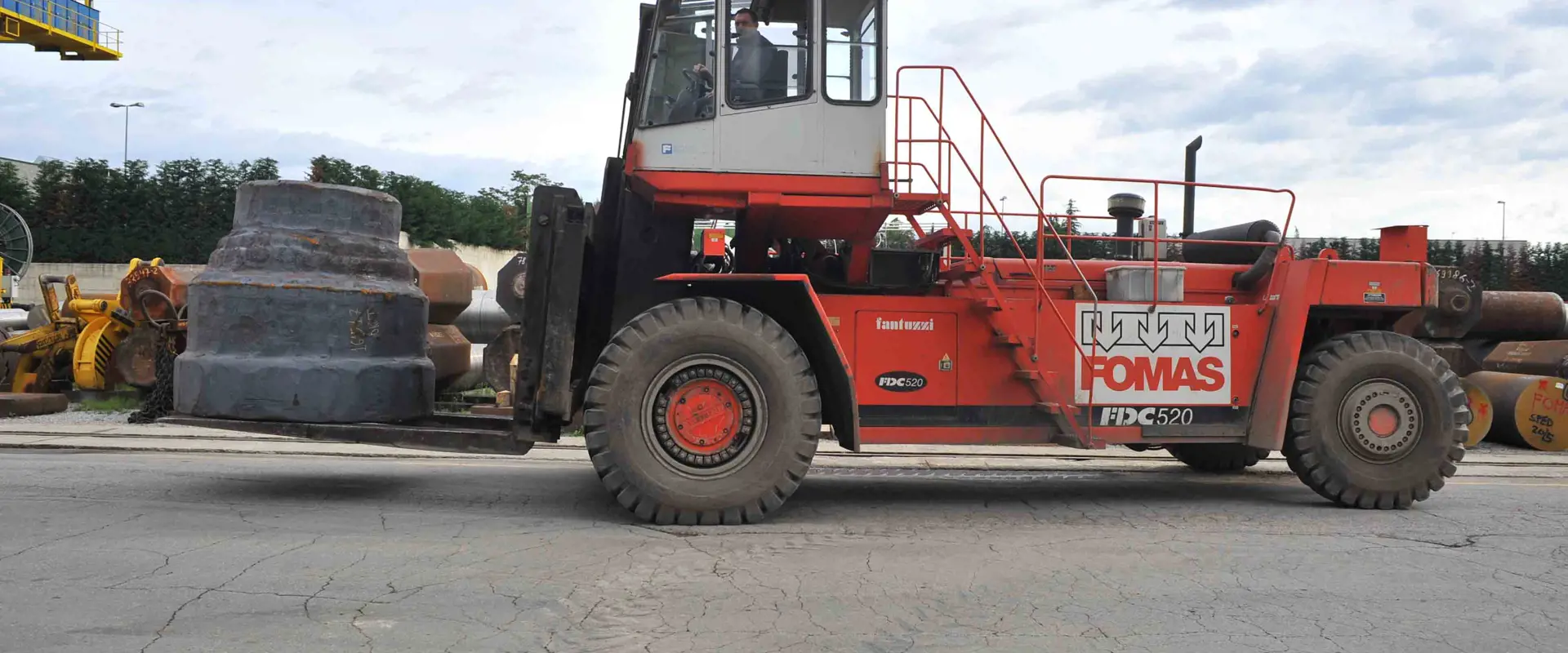
Digitalization and Traceability: The FOMAS Group Case Study
In the landscape of industrial innovation, many manufacturing companies face complex challenges related to the organization of production processes. FOMAS Group, a multinational company of Italian origin founded in 1956 and a leader in the production of forged components, rolled rings, and metal powders, has embarked on a digital transformation journey to enhance material traceability, optimize production flows, and increase operational efficiency at its Osnago (Lecco) plant.
- Complete traceability of materials, both internally and towards subcontractors, throughout the entire production cycle.
- Reduction of paper usage in logistics processes.
- Digitalization of logistics processes.
ThinkIN has supported us with enthusiasm, professionalism, and expertise, standing by our side to tackle these challenges.
The project is still in progress, but we are already so satisfied that we have decided to expand the mission management platform to the Rovigo plant and enhance it for the Osnago facility, including process control management.
We can’t do without it anymore!
- Production Processes Manager, Fomas
Implemented solutions:
- Mission Control for planning and managing logistics tasks.
- GPS tracking of forklifts to locate materials and optimize workflows.
The company has decided to tackle two key strategic challenges to optimize logistics operations at its Milan facility:
- Digitalizing material handling processes, including both loading/unloading operations with subcontractors and internal movements.
- Ensuring precise and reliable traceability of materials moved within the facility.
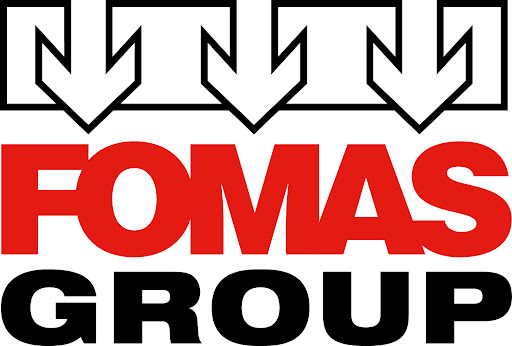
The Challenges of FOMAS
FOMAS Group boasts nearly 70 years of expertise in the transformation of special steels and non-ferrous alloys, with extensive experience in melting, forging, rolling, and atomization. The company is committed to ensuring that every stage, from initial production to final finishing, is managed efficiently and with the highest quality standards. This expertise has made FOMAS a global leader in its field, serving strategic markets such as energy, oil & gas, automotive, transportation, aerospace, and general industry, offering high-tech, customized solutions tailored to the specific needs of each sector.
FOMAS has always been highly attentive to new technologies and their impact on optimizing production processes. This commitment led to the collaboration with Thinkin.
FOMAS's production process involves multiple stages of metalworking, including forging, heat treatment, inspections, and final finishing to ensure that the finished product meets the highest quality standards. This process is primarily carried out internally, but certain stages are performed by external suppliers who receive semi-finished products for specific processing. The movement of these semi-finished products, including intralogistics operations with external suppliers, is critical to ensuring an efficient workflow and maximizing the use of available space and resources.
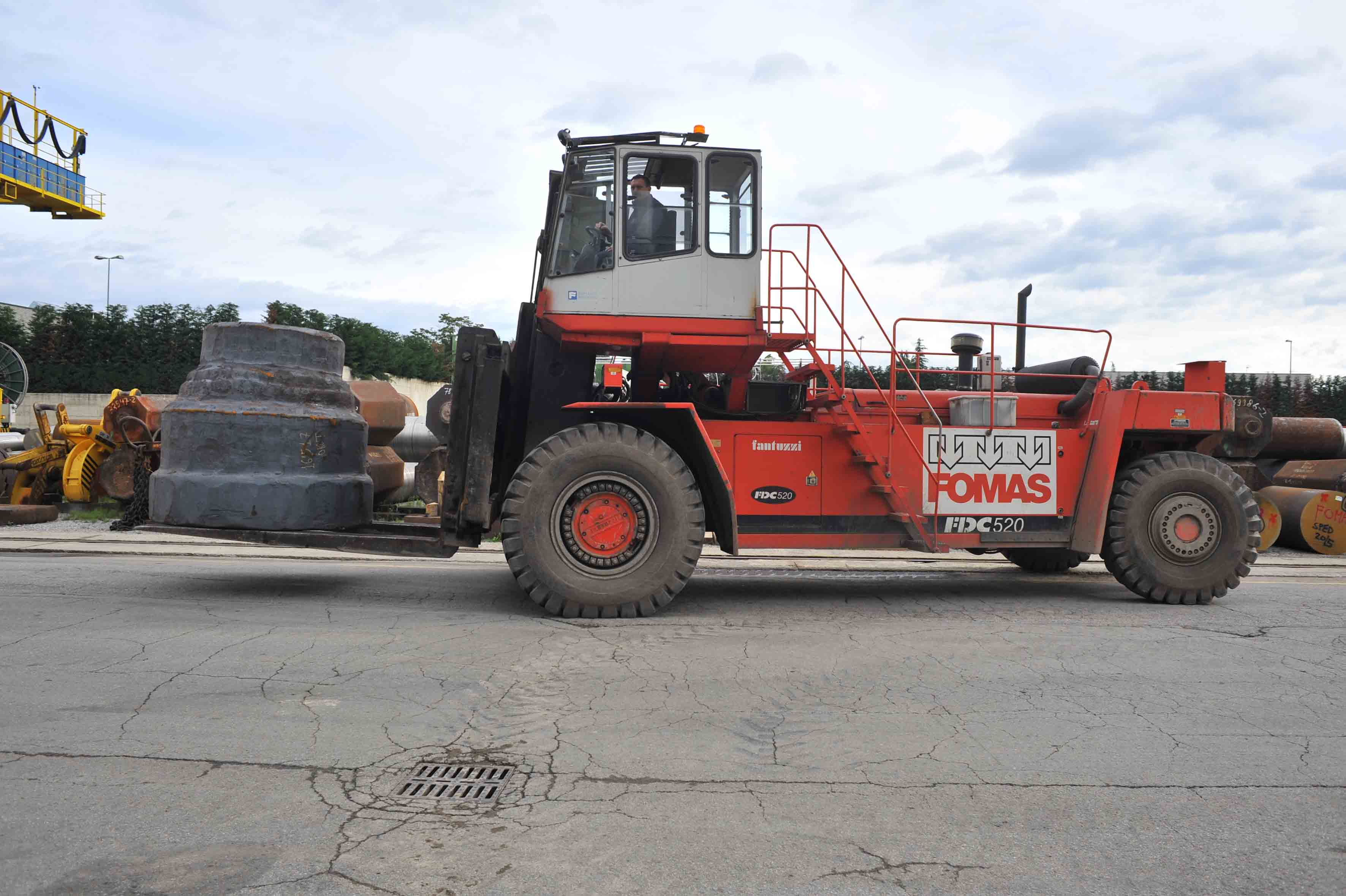
The Thinkin Solution
To address these challenges, FOMAS partnered with ThinkIN to launch a digitalization project for internal logistics operations related to semi-finished product movements. The goal was to enhance material handling efficiency and optimize resource utilization. The project included two interconnected modules:
-
Indirect WIP traceability to maintain an accurate, real-time map of semi-finished products within the facility and ensure an always-updated inventory.
-
Planning and coordination of forklift missions to streamline activity scheduling and improve the operational management of forklift operators.