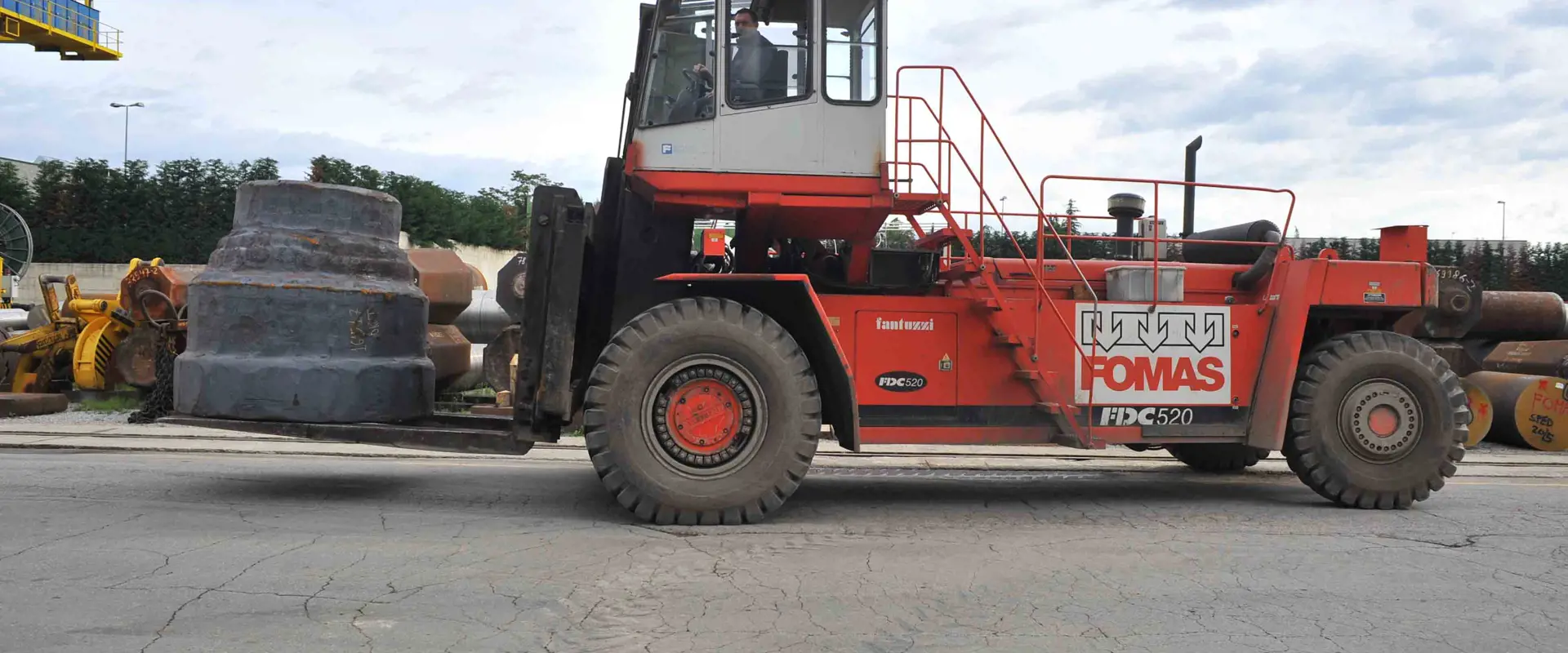
Digitalizzazione e tracciabilità: il caso FOMAS Group
Nel panorama dell’innovazione industriale, molte aziende manifatturiere devono affrontare sfide complesse legate all’organizzazione dei processi produttivi. FOMAS Group, multinazionale di origine italiana fondata nel 1956 e leader nella produzione di componenti forgiati, anelli laminati e polveri metalliche, ha avviato un percorso di trasformazione digitale per migliorare la tracciabilità dei materiali, ottimizzare i flussi di produzione e aumentare l’efficienza operativa nello stabilimento di Osnago (Lecco).
- Tracciabilità completa dei materiali, sia interni che verso i terzisti, lungo tutto il ciclo produttivo.
- Riduzione della carta dai processi logistici
- Digitalizzazione dei processi logistici
Thinkin ci ha accompagnato con entusiasmo, professionalità e competenza, affrontando al nostro fianco queste sfide.
Il progetto è ancora in fase di realizzazione, ma siamo già così soddisfatti che abbiamo deciso di espandere la piattaforma di gestione delle missioni allo stabilimento di Rovigo e di potenziarla per lo stabilimento di Osnago, includendo anche la gestione dei controlli di processo.
Non possiamo più farne a meno!
- Production Processes Manager, Fomas
Soluzioni implementate:
- Mission Control per la pianificazione e gestione delle missioni logistiche.
- Tracciamento GPS dei muletti per localizzare materiali e ottimizzare i flussi.
L’azienda ha deciso di affrontare due sfide strategiche fondamentali per ottimizzare le operazioni di logistica nel suo stabilimento di Milano:
-
Digitalizzare i processi di movimentazione dei materiali, comprese operazioni sia di carico/scarico verso i terzisti che di movimentazioni interne di materiai e semilavorati.
-
Garantire una tracciabilità precisa e affidabile dei materiali movimentati all’interno dello stabilimento.
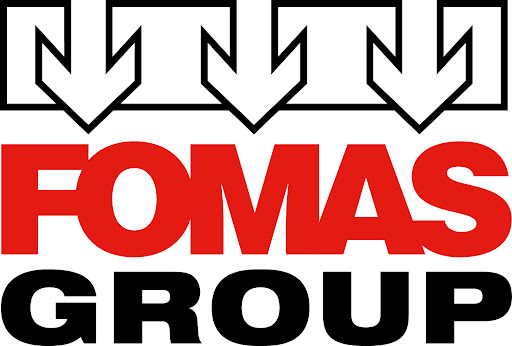
Le Sfide di FOMAS
FOMAS Group vanta quasi 70 anni di competenza nella trasformazione di acciai speciali e leghe non ferrose, con una forte esperienza nella fusione, fucinatura, laminazione e atomizzazione al servizio dei clienti per garantire che ogni fase, dalla realizzazione iniziale e alla finitura, sia gestita in modo efficiente e con alta qualità. Questo ha permesso a FOMAS di diventare leader mondiale nel suo ambito e di servire mercati strategici come energia, oil & gas, automotive, trasporti, aerospaziale e industria generale, offrendo soluzioni ad alto valore tecnologico e customizzate per rispondere alle esigenze specifiche di ogni settore.
FOMAS inoltre è da sempre molto attenta alle tecnologie e all’impatto che queste possono avere nell efficientamento dei processi produttivi. Da questo è nata la collaborazione con Thinkin.
Il processo produttivo di FOMAS si basa su diverse fasi di lavorazione del metallo, forgiatura, trattamento termico, controlli, fino alle fasi di finitura finale per garantire che il prodotto finito rispetti i massimi standard di qualità. Questo è un processo che si sviluppa prevalentemente internamente, ma con diverse fasi realizzate da fornitori esterni che ricevono un semilavorato per effettuare lavorazioni specifiche. La movimentazione di questi semilavorati, comprese le attività di intralogistica verso i fornitori esterni, risultano critiche per garantire un flusso di lavoro efficiente e massimizzare l’utilizzo degli spazi e dei mezzi a disposizione.
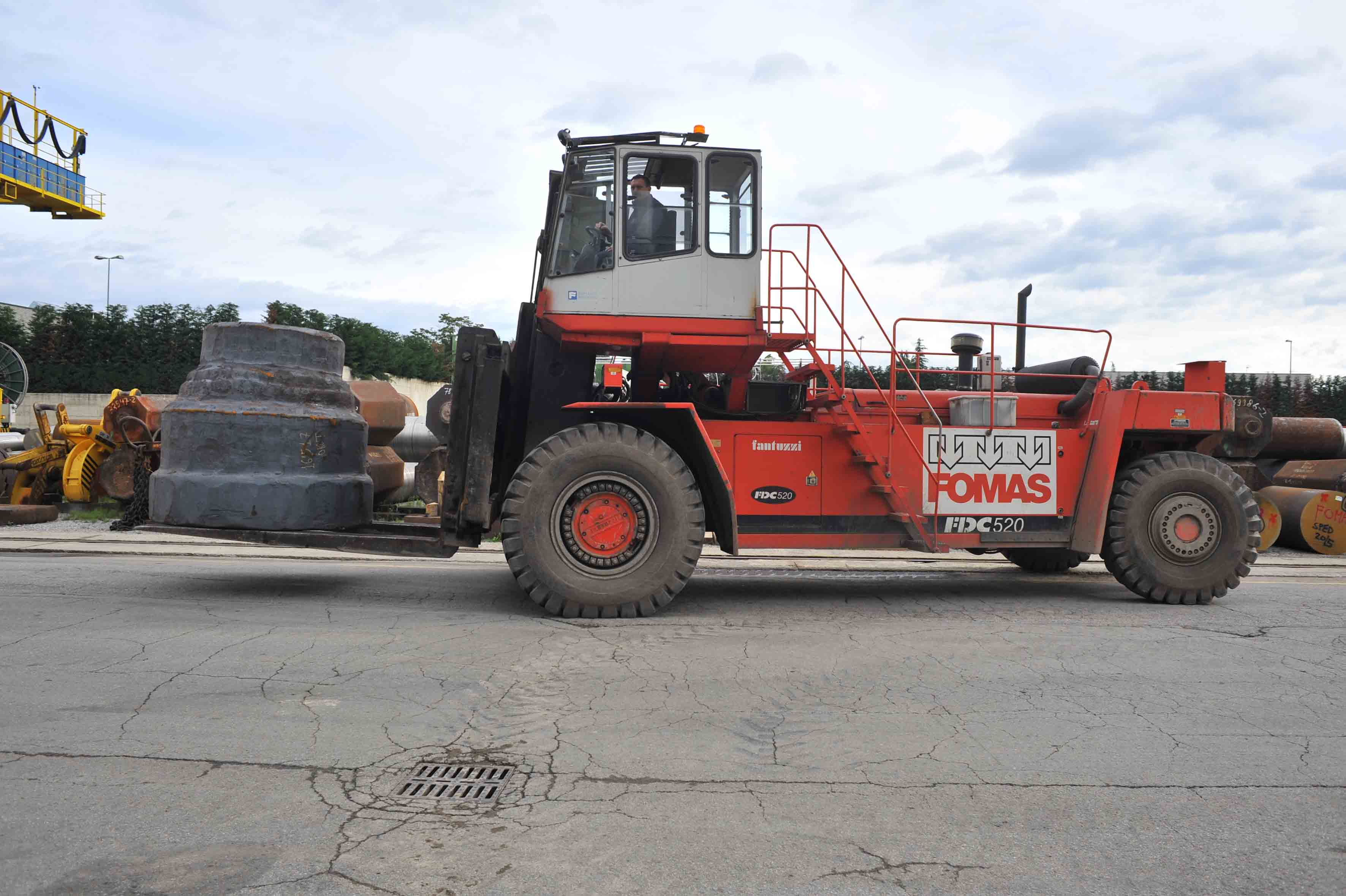
La Soluzione ThinkIN
A partire da queste difficoltà, FOMAS ha avviato con Thinkin un progetto di digitalizzazione delle attività di logistica interna legata alle movimentazioni dei semilavorati, con l’obiettivo di efficientare il processo di material handling e l’utilizzo delle risorse a disposizione. Il progetto ha coinvolto due moduli separati, ma collegati tra loro:
- Tracciabilità indiretta del WIP per avere una mappa precisa in ogni momento del dislocamento dei vari semilavorati nello stabilimento ed un inventario sempre aggiornato.
- Pianificazione e coordinamento delle missioni dei mulettisti, per facilitare la pianificazione delle attività e facilitare la gestione operativa dei car
La soluzione ThinkIN si è basata sui seguenti componenti tecnologici:
-
Un dispositivo Tablet veicolare, montato su ciascun carrello e con installata l’applicazione mobile ThinkIN material handling. Attraverso questo componente è possibile interagire digitalmente ed in tempo reale con i carrellisti e coordinare le operazioni di movimentazione dei carrellisti.
-
La piattaforma ThinkIN per la pianificazione back office delle missioni, la gestione degli spazi di FOMAS e l’integrazione con il MES. Attraverso questo strumento, il responsabile della logistica può programmare al meglio sia le attività di logistica verso/da fornitori esterni, che le movimentazioni interne attraverso le varie fasi produttive.