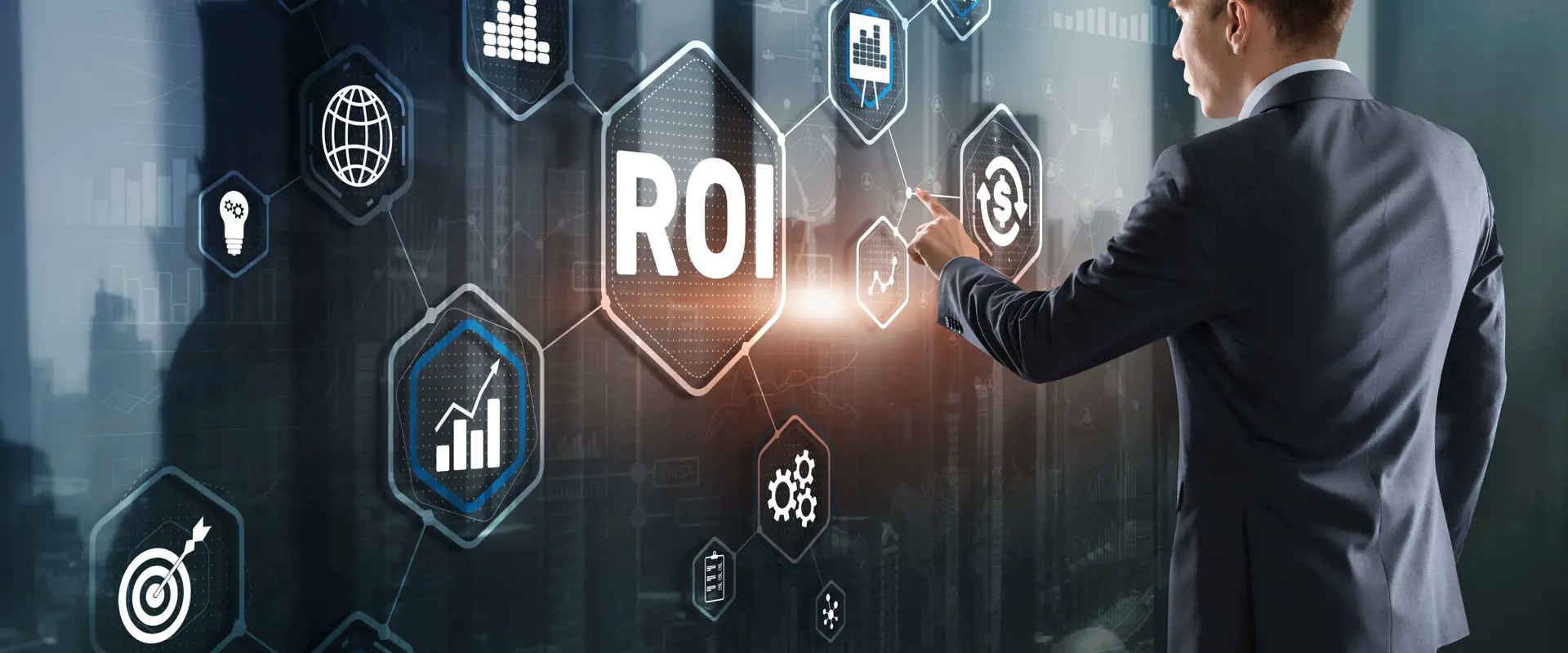
Progetto RTLS: Ritorno di investimento e risk management
Le tecnologie IoT sono essenziali per la digitalizzazione della produzione, migliorando l'efficienza e la pianificazione. Valutare costi e benefici è fondamentale prima di investire in queste tecnologie, considerando ritorni tangibili e intangibili. La gestione del rischio, attraverso analisi dettagliate e progetti pilota, è vitale per il successo di progetti IoT nell'ambito manifatturiero.
- Le tecnologie IoT sono fondamentali per la digitalizzazione del processo produttivo
- Valutare attentamente i costi e benefici è essenziale per l'investimento in IoT
- La gestione del rischio è cruciale per il successo del progetto IoT
Tecnologie IoT, e di localizzazione in particolare, sono fondamentali per la digitalizzazione di un processo manifatturiero, soprattutto quando questo è caratterizzato da un'elevata movimentazione di semilavorati, materiali e merci. Riuscire a creare una immagine fedele dell’avanzamento produttivo, allineando la pianificazione della produzione, il reparto vendite e i fornitori per l'approvvigionamento di materiali e parti, permette di gestire al meglio la capacità produttiva e di avere importanti ritorni in termini di efficientamento, soddisfazione dei Clienti e, in ultima battuta, utili.
Come per ogni progetto di innovazione, una volta messo a fuoco il problema che si vuole andare a risolvere, è necessario fare una valutazione dei costi / benefici dell'investimento richiesto e del ritorno sull‘investimento da effettuare. In generale, l’introduzione di queste tecnologie fa tipicamente parte di un percorso di digitalizzazione del processo produttivo, mirato a raccogliere dati che nel tempo permettano un maggiore controllo delle attività produttive e un migliore collegamento con la parte di pianificazione e gestione delle commesse.
In questo articolo tratteremo alcuni dei principali aspetti di cui IT manager, responsabili della produzione (o più in generale chi deve approvare l’investimento) devono tenere di conto in questo tipo di valutazioni. Andremo a dare alcune indicazioni sui criteri con cui valutare il ritorno sull’investimento e sugli aspetti di cui tenere di conto nella valutazione (e mitigazione) dei rischi annessi.
Ritorno sull'investimento
Attraverso l’analisi del ritorno sull’investimento si vanno a valutare i tempi con cui viene ammortizzato l’investimento fatto in infrastruttura e servizi RTLS, e quando i benefici andranno a superare i costi.
Questo tipo di valutazione spesso non è facile, in quanto non si è in grado di misurare l’impatto economico di un determinato problema. Ad esempio, il fatto che si perda tempo nella ricerca di semilavorati non è direttamente collegato ad un costo, a meno che non lo si vada a misurare e a legare con il costo orario del personale. Allo stesso modo, l’impatto economico che determinati eventi, seppur rari (es: mancato avvio di un macchinario a causa di uno stampo mancante), sono difficilmente valutabili.
Un altro aspetto che rende difficile questo tipo di valutazioni è il fatto che queste tecnologie possono avere un impatto su diverse funzioni aziendali, anche se la funzione che beneficia inizialmente dei servizi offerti è unica. Ad esempio, tracciare i muletti di un magazzino può portare dei chiari benefici in termini di efficientamento nell’utilizzo di questa risorsa. Questo può però avere delle ricadute anche in termini di sicurezza sul posto di lavoro e la stessa infrastruttura di tracciamento può essere utilizzata per tracciare anche strumenti di lavoro o valutare il riempimento di determinati cassoni presenti nello stabilimento.
Elenchiamo di seguito alcuni criteri con cui si può andare a fare un’analisi dei costi benefici. Questo è soprattutto un approccio metodologico, in quanto ogni caso è diverso ed ogni azienda segue un proprio percorso di digitalizzazione.
Orizzonte temporale
È importante valutare l’orizzonte temporale su cui si va a fare questo tipo di valutazione. Progetti RTLS, o IoT in generale, hanno un costo di avvio, a cui può seguirne uno di operatività a seconda del modello di costo scelto (es: SaaS vs. on-premise). Questo orizzonte può variare tipicamente da un minimo di 1, ad un massimo di 3 anni, a seconda del progetto che si va ad implementare e del problema che si va a risolvere. È comunque importante definire questo valore e su di questo basare le valutazioni successive.
Partire dai problemi noti
Il punto di partenza di questi progetti è un’esigenza specifica, legata ad un problema che si vuole andare a risolvere. Da qua si deve partire e provare a fare una prima valutazione dei benefici. Questa valutazione dovrebbe essere, per quanto possibile, basata su dei dati misurabili o stimabili. Un esempio di problemi misurabili sono:
- il tempo speso nella ricerca di semilavorati: il tempo che operatori specializzati perdono nella ricerca di parti, semilavorati o strumenti di lavoro può essere misurato su un arco temporale specifico.
- il numero di semilavorati, o parti, persi: in un ambiente produttivo (soprattutto nel caso della manifattura discreta), spesso succede che semilavorati o parti vengano perse, o non trovate in un tempo utile per la produzione. Questo ha un impatto sui tempi di consegna e sugli sprechi (e di conseguenza sui costi).
- OEE macchinari: l’assenza di una determinato ordine, componente o operatore specializzato, può comportare che un macchinario non sia utilizzato o rimanga in funzione senza produrre. Questo ha generalmente un costo non trascurabile, soprattutto nel caso di macchinari ad elevato consumo (es: forni) o elevato valore.
....
Vuoi leggere la versione completa? Compila il form qui sotto per scaricarlo gratuitamente