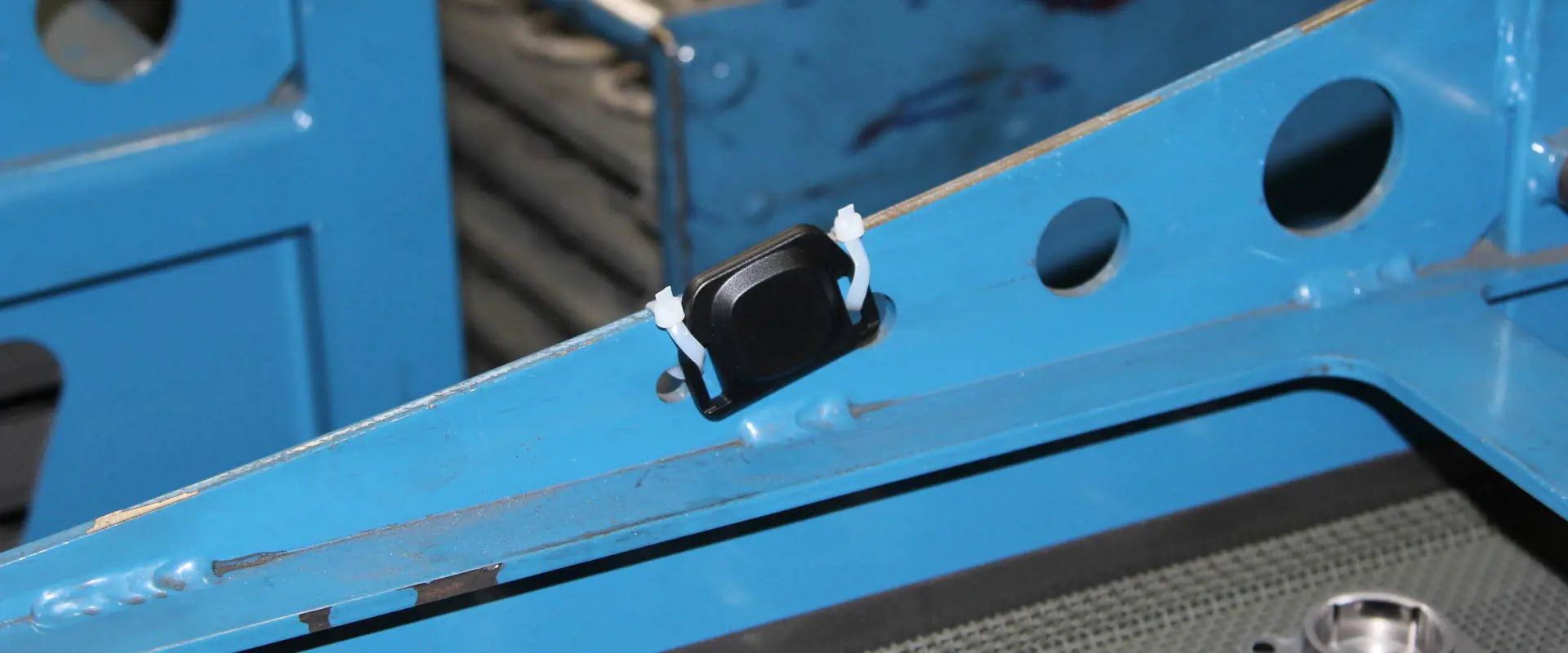
Impresa manifatturiera massimizza l’efficienza produttiva grazie alla localizzazione indoor
Un’impresa manifatturiera di componenti metallici per l’industria automobilistica era alla ricerca di una soluzione per ottenere visibilità sulla movimentazione di un parco carrelli di più di 1000 unità, col fine di evitare ritardi di produzione e deviazioni dal planning di produzione.
- 1000+ carrelli tracciati
- Facile e rapida localizzazione e ricerca di carrelli e ordini di produzione
- Aumento dell’efficienza produttiva e migliore coordinamento della forza lavoro
Introduzione
Il cliente è un'azienda manifatturiera di medie dimensioni che produce componenti in metallo per alcune delle principali case automobilistiche. L’impianto industriale è molto complesso, con superfici metalliche (pareti, soffitti, barre, ecc.) di altezza variabile e con centinaia di grandi macchinari utilizzati nel processo produttivo. Il cliente riceve ordini di grandi volumi per cui è necessaria un’attenta pianificazione del processo produttivo che, per un singolo ordine, può durare anche diversi giorni.
Durante la fase di produzione ogni singolo componente metallico attraversa più fasi produttive (almeno 4) e gli spostamenti tra una fase e quella successiva vengono eseguiti tramite l’utilizzo di carrelli industriali di grandi dimensioni. Più di 1000 carrelli vengono utilizzati contemporaneamente in un unico stabilimento industriale.
Problema
Il cliente utilizza diversi strumenti per la corretta programmazione degli ordini di produzione, inclusi PLC e SCADA per il monitoraggio dello stato dei diversi macchinari coinvolti nel processo. Ha però una visibilità limitata sulla movimentazione della produzione e, in particolare, sui carrelli utilizzati per spostare i componenti da una linea di produzione all'altra. Il mancato monitoraggio in tempo reale di questo tipo di risorsa ha un impatto negativo sull'efficienza dell'intero processo produttivo. I problemi includono:
- In caso di macchina fuori servizio, non è possibile riprogrammare facilmente la produzione dei componenti assegnati a tale macchina;
- L'indisponibilità di carrelli può bloccare la produzione, per cui è molto importante anticipare tali esigenze e gestire adeguatamente i numerosi depositi di carrelli;
- L'intero processo richiede una notevole quantità di lavoro manuale, soprattutto quando si tratta di spostare i carrelli da una linea di produzione a quella successiva.
Requisiti della soluzione di tracciamento
Il cliente era alla ricerca di una soluzione per il monitoraggio della movimentazione dei carrelli all'interno dell'impianto industriale con le seguenti specifiche:
- La possibilità di localizzare i carrelli con un ritardo massimo di 2 minuti e con una precisione di circa 1 metro;
- La possibilità di controllare dinamicamente gli ordini di produzione trasportati su ogni carrello nell'impianto industriale;
- La possibilità di ricercare e localizzare i carrelli secondo vari criteri (ordine di produzione, fasi di produzione);
- La possibilità di monitorare in tempo reale i depositi dei carrelli e ricevere notifiche quando sono insoddisfatte condizioni specifiche (ad es. numero di carrelli sopra/sotto una determinata soglia).

Soluzione
Per soddisfare i requisiti proposti dal cliente, abbiamo implementato la nostra soluzione di location intelligence ThinkIN. Per la localizzazione dei carrelli all’interno dell’impianto industriale, abbiamo utilizzato la tecnologia Quuppa. Ogni carrello è stato dotato di un TAG Bluetooth Low Energy (BLE) che poteva essere di due tipi: o un TAG standard Quuppa o un Maxi TAG beacon di BlueUp. I TAG utilizzati garantiscono una lunga durata della batteria, di circa 3 anni, successivamente sostituibile. Complessivamente abbiamo utilizzato 13 antenne per coprire un'area di circa 1500 mq.
I dati raccolti sono stati elaborati dal nostro software ThinkIN e forniti al cliente sotto forma di cruscotto online, che è stato utilizzato dal cliente per monitorare lo stato dei carrelli e per analizzare l'evoluzione nel tempo di specifici KPIs.
Risultati
Utilizzando la soluzione ThinkIN, il cliente ha potuto ottenere maggior controllo sul processo produttivo, con vantaggi misurabili in termini di:
- Efficienza dei lavoratori e coordinamento della forza lavoro, limitando i tempi di ricerca dei carrelli durante il processo produttivo, eliminando sprechi di tempo e riducendo ritardi.
- Efficienza produttiva, reindirizzando dinamicamente ordini di produzione specifici (in base alla conoscenza dello stato di esecuzione degli ordini di produzione) e sfruttando al meglio tutte le macchine disponibili.
Nel complesso, la soluzione ha portato ad un aumento della produttività e ad una riduzione dei costi associati alla produzione di ogni singolo ordine.