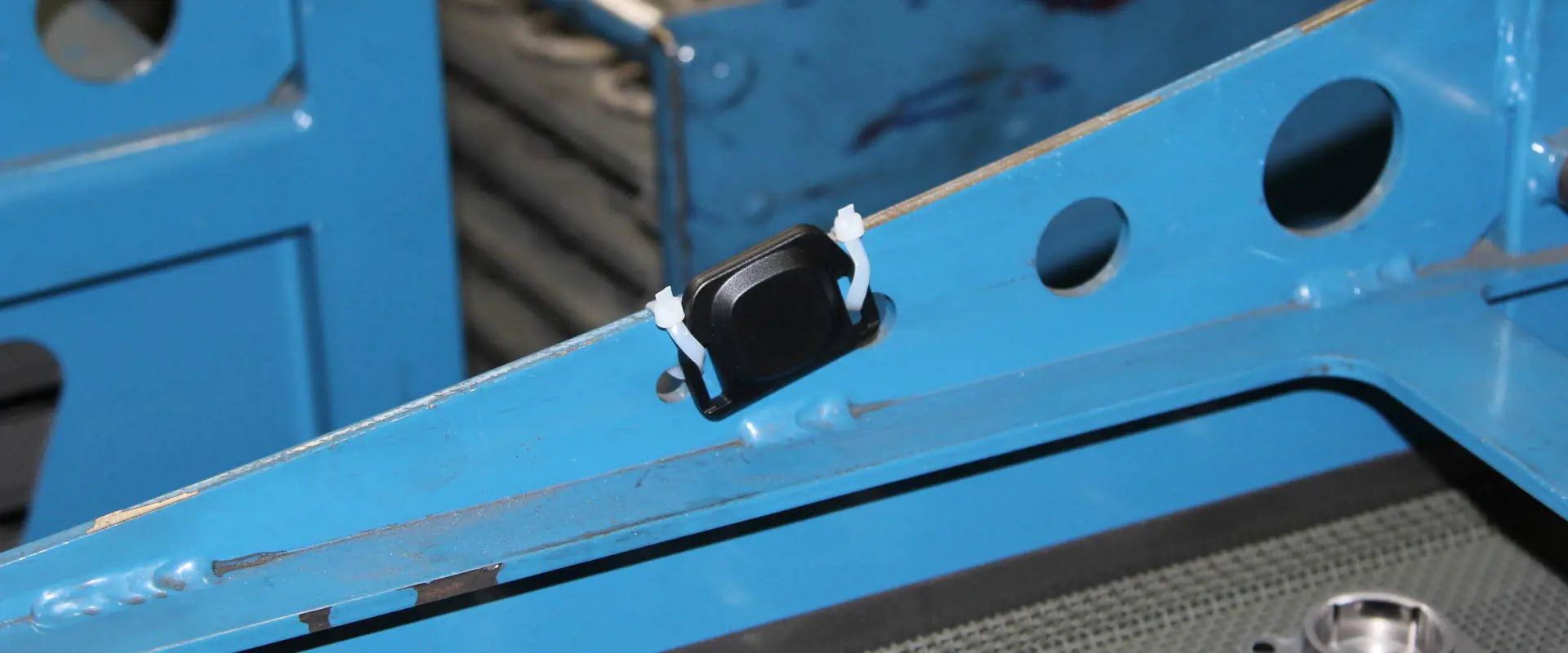
Manufacturing company maximises production efficiency through indoor location
A manufacturing company of metal components for the automotive industry was looking for a solution to gain visibility on the handling of more than 1000 trolleys, in order to avoid production delays as well as deviations from the production schedule.
- 1000+ tracked trolleys
- Simple and quick location and search of trolleys and production orders
- Increased production efficiency and improved workforce coordination
Introduction
The customer is a mid-sized manufacturing company producing metal components for some of the major automotive companies. The industrial plant is a very complex environment, with metal surfaces (walls, ceilings, bars, etc.) of variable height distributed throughout the entire space and featuring hundreds of large machineries used in the production process.
The customer receives orders for large volumes of components. Therefore, a careful planning of the production process is needed, which for a single order can take a few days.
During the production phase, each single metal component goes through multiple production phases (at least 4). During this process, large industrial trolleys are used to move components from a production phase to the following one. In a single industrial plant more than 1000 trolleys are used.
Problem
The customer is using state-of-the-art tools for the proper scheduling of production orders, including PLCs and SCADA for monitoring the status of the different machineries involved in the process. However, they have limited visibility on the status of the production and, in particular, of the trolleys used to move components from one production line to the next one. This lack of real-time monitoring capability can severely impact the efficiency of the overall production process. Problems include:
- In the case of a machine out of service, it is not possible to easily re-schedule the production of the components assigned to that machine.
- The unavailability of trolleys can block the production. It is therefore very important to anticipate such needs and properly manage the numerous deposits of trolleys.
- The overall process requires a significant amount of manual work, especially when it comes to moving the trolleys from one production line to the following one.
Requirements of the tracking solution
The customer was looking for a solution to properly control the movements of trolleys within the industrial plant. Requirements included:
- The possibility to localise trolleys with a maximum 2 minutes delay and with a precision of approximately 1 metre;
- The possibility to dynamically control the production orders being transported on each trolley in the industrial facility;
- The possibility to search and locate trolleys by different criteria (production order, production phases);
- The possibility to monitor in real-time trolley deposits and receive notifications when specific conditions were met (e.g., number of trolleys above/below a specific threshold).

Solution
In order to meet the requirements put forward by the customer, we deployed our ThinkIN location intelligence solution. We used the Quuppa technology to localise trolleys in the industrial facility. Each trolley was equipped with a Bluetooth Low Energy (BLE) TAG, which could be either a standard Quuppa TAG or a Maxi BlueUp Beacon TAG. The used TAGs guarantee a long-life battery (approx. 3 years), which can be replaced later on. Overall, we used 13 antennas to cover an area of approximately 1500 square metres.
The collected data was processed by the ThinkIN platform and used to feed a web dashboard that was used by the customer to monitor the trolleys’ status as well as to analyse the evolution of specific KPIs over time.
Results
By utilising ThinkIN technology, the customer was able to obtain a much finer control on the production process, with measurable benefits in terms of:
- Workers’ efficiency and workforce coordination, by limiting the time spent searching for trolleys during the production process, eliminating waste of time and reducing delays.
- Production efficiency, by dynamically re-route specific production orders (based on the knowledge of the execution status of production orders) and exploiting all the available machines.
All in all, the solution provided was able to increase the overall productivity and to reduce costs related to the production of a single order.