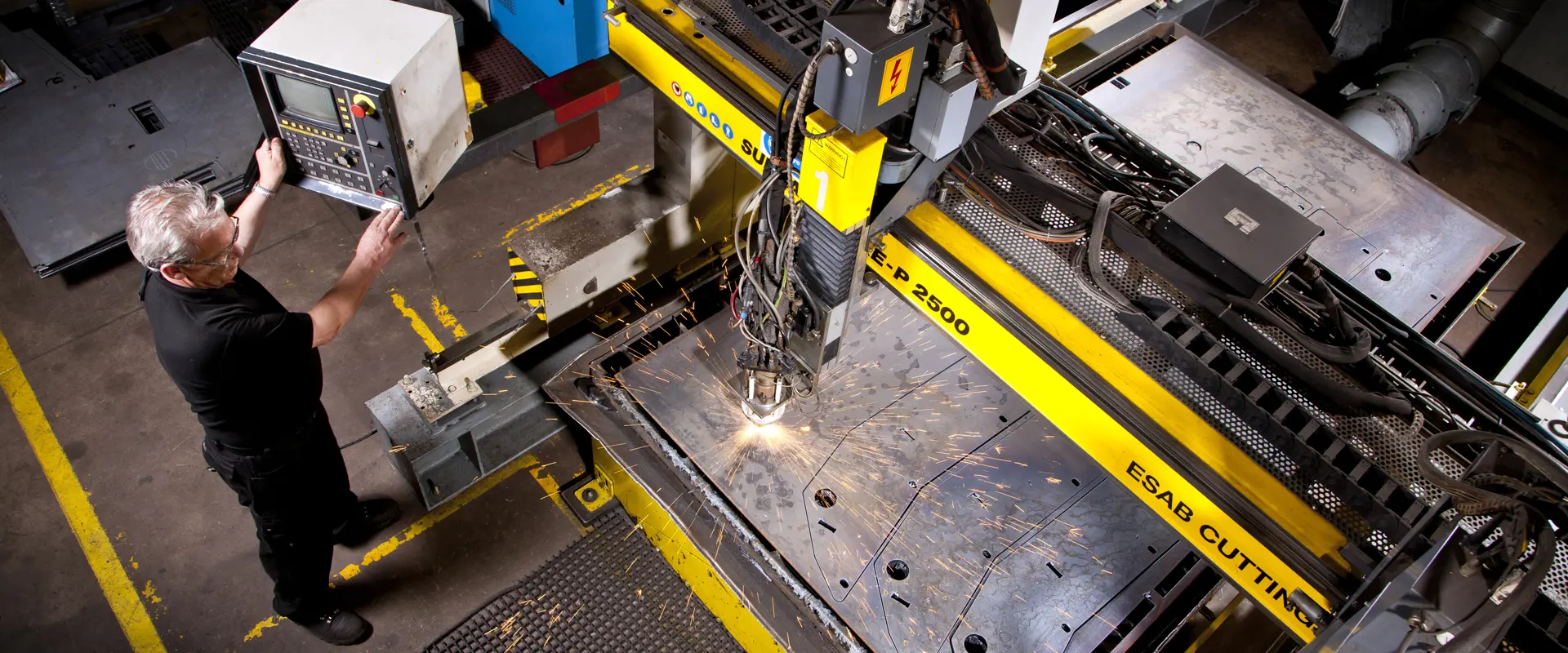
Asset tracking: - £10.000/mese di spese per Dyer Engineering
Dyer Engineering, produttore britannico di componenti e strutture metalliche, era alla ricerca di una soluzione di localizzazione e tracciamento degli ordini di lavoro per ridurre ritardi nella produzione e costi operativi. Dyer Engineering ha scelto ThinkIN tra 50 soluzioni.
- Costi ridotti di £10.000/mese
- 1000 ordini di produzione tracciati
- Migliore produttività dei lavoratori e rispetto della pianificazione
“Volevamo dare ai team di produzione i dati necessari per vedere cosa stava succedendo lungo il processo produttivo ed individuare aree di efficientamento”
RICHARD LARDER
Head of Digital Innovation
Dyer Engineering
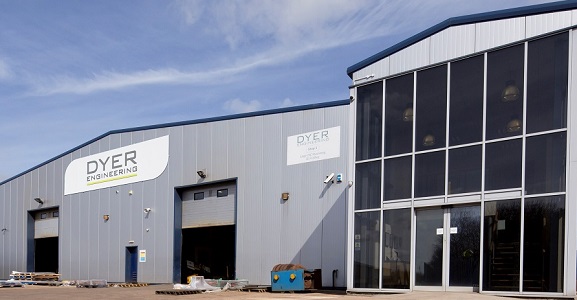
Introduzione
Dyer Engineering è un produttore britannico di componenti e strutture metalliche utilizzate in molteplici settori, tra cui quello automobilistico, petrolifero, del gas, ferroviario, della difesa, delle energie rinnovabili e dell'estrazione mineraria. Dal 1977, fornisce i suoi prodotti sia a livello locale che globale.
Dyer Engineering ha sede nella contea di Durham con due impianti di produzione in funzione, a 3 miglia di distanza l'uno dall'altro, la cui superficie totale è di circa 9.200 metri quadrati.
Problema
In Dyer Engineering il processo produttivo non è lineare. Per essere lavorati correttamente, i vari tipi di metallo devono infatti attraversare diverse aree di produzione muovendosi in numerose zone dello stabilimento. Questo significa che, in un dato momento, sono in esecuzione fino a 1000 ordini di produzione, ognuno dei quali poi richiede diverse operazioni. Ne consegue che quasi 5000 parti e componenti si muovono contemporaneamente nelle 2 strutture con seri impatti sull’intera linea produttiva, se la loro posizione viene smarrita.
Qualsiasi componente mancante o persa all'interno dell’impianto può influire gravemente sul ciclo di vita del prodotto (PLC), determinando:
- gravi ritardi nella produzione e verosimilmente un aumento del lead time;
- ore lavorative perse nella ricerca manuale di ordini di produzione;
- aumento dei costi operativi;
- conseguente perdita di efficienza.
Per affrontare questi problemi, all'inizio del 2019, Dyer ha deciso di implementare una soluzione di asset tracking. Il progetto rientrava in un’iniziativa interna dedicata all’esplorazione delle tematiche legate all’Industria 4.0, in quanto l'azienda da sempre è attenta agli sviluppi digitali e tecnologici nel settore, essendo pioniere della Digital Transformation già dagli anni '90. L’asset tracking era una tra le tecnologie elencate da prendere in considerazione come efficaci soluzioni per alcune delle problematiche viste in precedenza.
A tal fine, Dyer ha lanciato una Request for Proposal (RFP) per trovare la migliore tecnologia sul mercato in grado di migliorare l'efficienza del proprio processo produttivo. La RFP è stata guidata da Digital Catapult, il centro leader nel Regno Unito per l'innovazione tecnologica digitale avanzata, che mira ad accelerare la crescita, promuovere le collaborazioni tra start-up, piccole imprese e grandi aziende e ad aumentare la produttività in tutta l'economia del Regno Unito.
Requisiti della soluzione di tracciamento
Dyer ha deciso di valutare una serie di soluzioni per l'implementazione di un sistema di localizzazione in tempo reale (Real-Time Locating System, RTLS) che potesse monitorare la movimentazione di materiali e semilavorati durante il processo industriale. I requisiti chiave che la soluzione doveva soddisfare erano:
- Copertura del sistema e costi associati: essendo l’impianto piuttosto ampio, la quantità di dispositivi hardware richiesta e i loro relativi costi erano chiaramente un fattore importante da considerare, poiché il numero di antenne RTLS da installare incide sul costo di cablaggio e connettività;
- Precisione: la precisione dei dati di posizionamento delle varie risorse doveva essere inferiore al metro (in particolare mezzo metro) a causa dell'elevata densità di risorse e materiali che si spostano contemporaneamente all’interno dello stabilimento;
- Capacità di tracciare un numero elevato di risorse (asset): inizialmente la soluzione prevedeva di tracciare in tempo reale fino a 500 asset contemporaneamente, ma con la possibilità di espandere il tracciamento a tutte le risorse interessanti da monitorare;
- Maturità della soluzione: Dyer Engineering era alla ricerca di una soluzione matura con un sistema attivo di monitoraggio, supporto e manutenzione. L’azienda scelta doveva inoltre essere in grado di fornire dei piani di progetto dettagliati per quanto riguardava l’installazione, la configurazione e il funzionamento del progetto pilota.
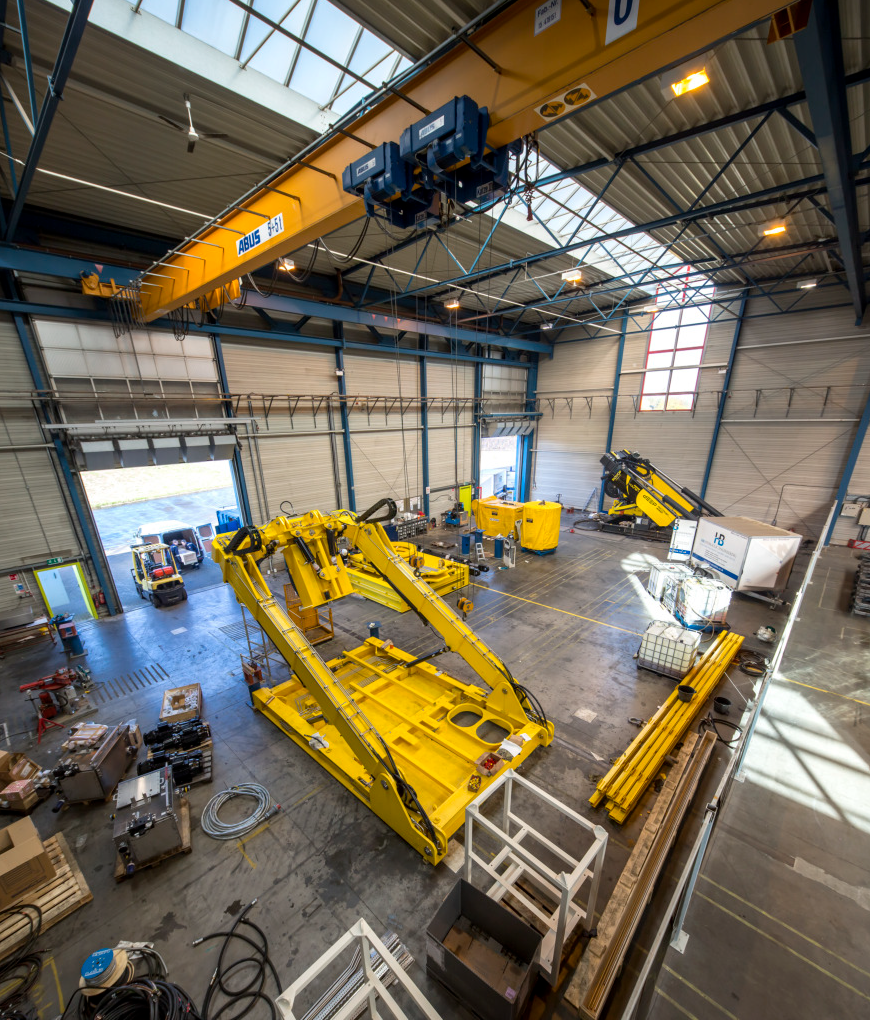
Soluzione
La soluzione ThinkIN è stata scelta tra 50 manifestazioni di interesse e 9 proposte finaliste, in quanto si è rivelata la migliore corrispondenza con l'elenco dei requisiti stabiliti da Dyer Engineering.
ThinkIN crea un gemello digitale del processo produttivo localizzando, tracciando e monitorando in tempo reale materiali, merci, semilavorati, pallet e qualsiasi altro asset rilevante all'interno dello stabilimento. La tecnologia ThinkIN si basa sull’infrastruttura RTLS di Quuppa per la localizzazione ad elevata precisione delle risorse all’interno della fabbrica. Quuppa utilizza un’unica combinazione di Bluetooth Low Energy (BLE) e Angle of Arrival (AoA) col fine di fornire dati di posizionamento indoor molto accurati.
ThinkIN processa tali dati e fornisce una serie di servizi abilitati dalla localizzazione indoor, come ad esempio:
- Ricerca e tracciamento degli asset;
- Analisi di processo;
- Servizi di monitoraggio e controllo in tempo reale.
Complessivamente, sono state installate 55 antenne per coprire le due strutture e sono stati impiegati 1000 TAG per tracciare gli ordini di produzione. Ogni ordine di produzione è associato dinamicamente a un dispositivo di tracciamento, grazie alla scansione del codice presente su tale ordine e del codice QR del relativo TAG. ThinkIN, inoltre, si integra facilmente con il sistema ERP di Dyer, arricchendo le informazioni di base di un ordine di produzione con tutti i dati necessari per il relativo processo produttivo.
La configurazione dell'infrastruttura e l'avvio del sistema hanno richiesto circa 1 settimana. L'obiettivo principale del progetto era la ricerca degli asset in tempo reale, insieme alla possibilità di accedere ai dati storici, al fine di trovare inefficienze e migliorare la programmazione e il processo di produzione. Ciò è stato ottenuto grazie a un'interfaccia dedicata che consente ai team leader, ai supervisori e agli operai di individuare parti e componenti su una mappa in tempo reale, eliminando le lunghe ricerche manuali delle risorse.
In un secondo momento, la tecnologia ThinkIN è stata utilizzata per analizzare il processo di produzione di Dyer Engineering, misurando i tempi di consegna nelle diverse fasi di produzione e identificando dove e come migliorare l'efficienza di processo.
Primi risultati e prospettive future
Grazie all’implementazione della soluzione di asset tracking ThinkIN, Dyer Engineering è ora in grado di risparmiare ore di lavoro, precedentemente utilizzate nella ricerca manuale delle risorse. Questo si traduce in un taglio nei costi di £ 10.000 al mese (basato sulle 125 ricerche del sistema per individuare gli ordini di lavoro).
Inoltre, a causa della disposizione degli edifici, parti e componenti erano soliti bloccarsi in luoghi diversi per giorni o intere settimane e finivano col perdersi. Questo portava i dipendenti a scegliere l'ordine di lavoro più vicino da elaborare, invece di dedicare tempo a cercare ordini con priorità maggiore. Grazie alla possibilità di ricercare le risorse, ora digitalizzate grazie alla piattaforma ThinkIN, i dipendenti sono ora più produttivi ed efficienti.
Più recentemente, il sistema è stato ampliato per tracciare e localizzare componenti ad iniezione jigs e così ridurre ulteriormente i costi e i tempi di consegna.