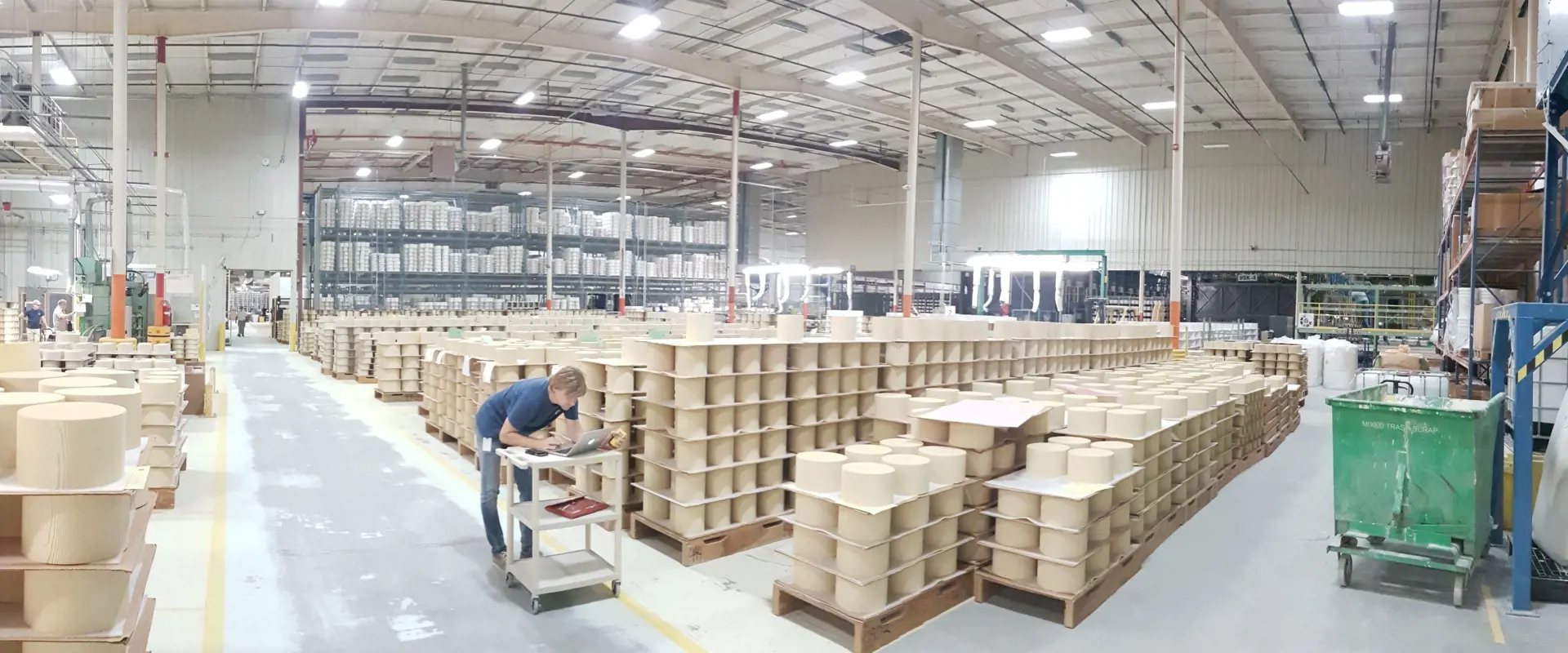
NGK Ceramics saves $152k annually with indoor localisation
NGK Ceramics, a US manufacturer of ceramic components for the automotive industry, was searching for an asset tracking solution able to reduce production delays and speed up inventory procedures. NGK Ceramics has chosen ThinkIN's digital twin thanks to the maturity of the solution and to a wide service offer.
- Savings of 80 labour hours / week
- Savings of USD 152,000 / year
- Integration with existing systems (ERP, MRP)
Introduction
NGK Ceramics is a global leader in the manufacturing of ceramic substrates used in catalytic converter applications for automotive, truck and off-road vehicles. The US manufacturing facility, located in Mooresville in North Carolina, covers more than 50.000 square meters and it is running 365 days a year, twenty-four hours a day.
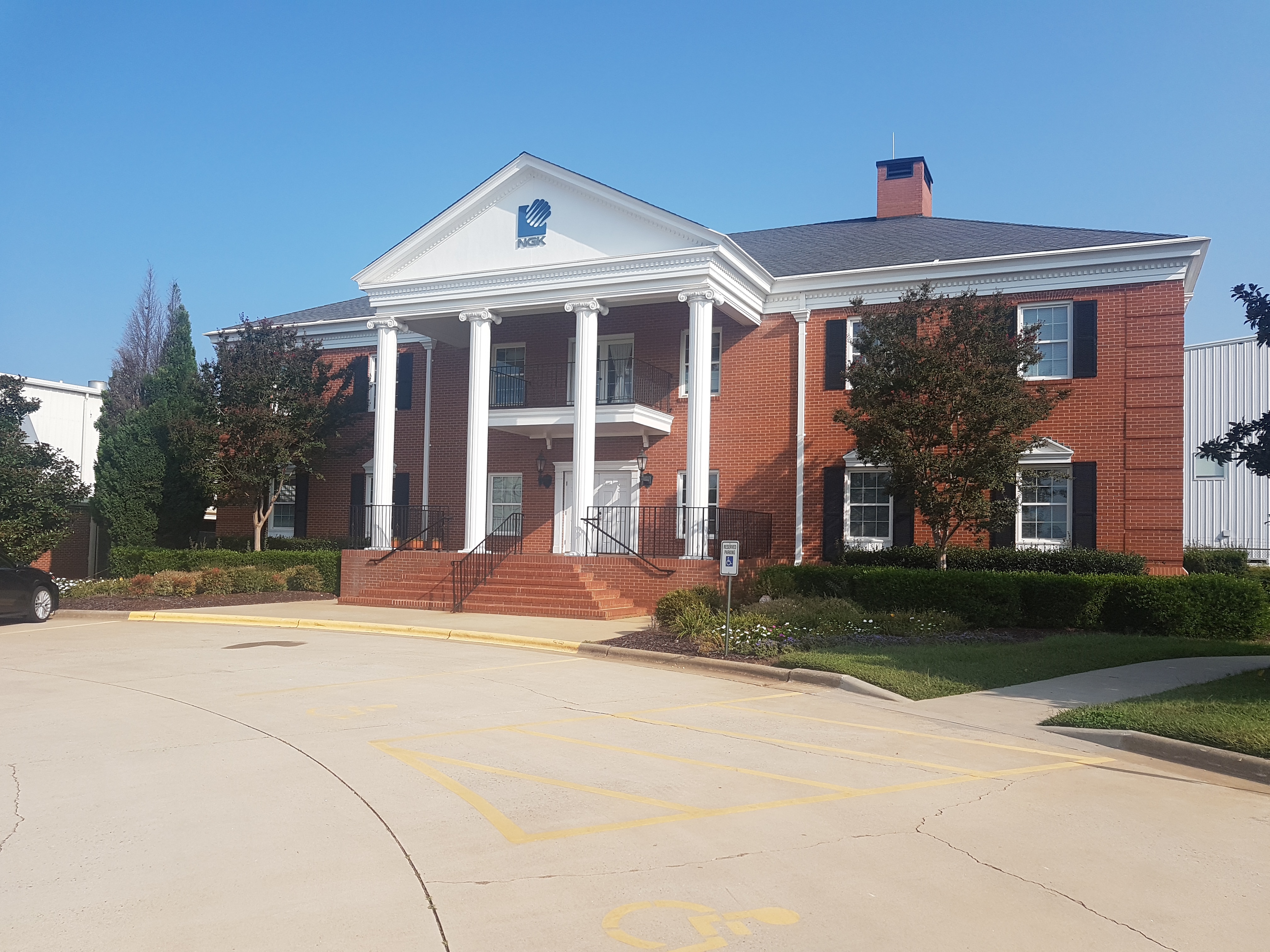
Challenge
The facility was initially designed in 1988 to serve a limited geographical area in the US. However, with the business growing faster than expected and more areas being served by the same production plant, NGK faced a major challenge: how to grow the capacity of the North Carolina industrial plant, in order to keep up with the market demand.
As a first step, ASRS (Automated Storage and Retrieval Systems), together with AGV’s (Automated Guided Vehicles), were introduced to move pallets and materials in the shop floor without human intervention.Even if this mitigated the problem, it was still not enough to manage high, yet variable, production demands in the long run. As a result, during production peaks, the pallets were temporarily stored all around the shop floor. This introduced a significant new problem: the additional time spent finding and moving pallets from one production phase to the next, with at least two workers per shift assigned to this task.
In addition to this, at least once a year a complete plant inventory was required to verify all materials stored in the facility, but not yet shipped or sold. During this activity, the entire plant was surveyed, and all pallets were identified and verified against the data registered in the internal ERP system. This activity could take up to one week, with the slow down (if not interruption) of the production activities. Inevitably, any items lost or duplicated created an impact on the bottom line.
In order to deal with these issues, and with the continuous increase in production demand, in 2017 NGK Ceramics decided to explore how solutions based on a Real Time Locating System (RTLS) could help by providing a Digital Twin of the manufacturing plant where the location of every pallet would be tracked continuously and that information synchronized with NGK’s MRP systems.
Tracking pallets provides a real-time view of their location throughout the industrial plant, with a number of supporting services to easily and rapidly search for them and smoothly manage the production cycle. After an evaluation of more than eight solutions, ThinkIN technology, together with Quuppa Intelligent Locating System™, was chosen based on a number of criteria including: accuracy, maturity of the solution, total cost of ownership, infrastructural requirements and support for a broad variety of services.
Tracking solution: requirements
NGK Ceramics decided to evaluate a number of different scenarios for implementing an RTLS solution to track the progress of material and semi-finished goods throughout the flow of its manufacturing process. The key requirements to be addressed by the solution were:
- Configurable tracking accuracy: since the industrial plant covers a large area (approx. 50.000 square meters), with different uses of the spaces within the plant (production area vs. stocking areas vs. corridors), the ability to vary the location accuracy of asset tracking was important. In some areas, where the density of pallets is typically high (such as the warehouse) sub-meter accuracy is required in order to easily locate a specific pallet among the many stocked there. On the other hand, a 10-meter accuracy is sufficient in corridors or transit zones, where it is enough to verify the presence of the pallet in the zone;
- Infrastructure cost: as NGK Ceramics facility is rather large, the number of RTLS antennas required to achieve the desired accuracy was clearly an important variable of the solution to be adopted. This impacted both the cost of the infrastructure as well as the costs related to the cabling (e.g., connectivity and power). Another factor was the cost of the TAGs to be attached to the pallets, considering as well the potential cost of replacing the batteries;
- Asset search and location functionalities: NGK wanted this Digital Twin to be used in a variety of ways, from centralized systems to hand-held devices. In fact, the system had to be easily usable by the end user, that is, the worker in the shop floor. This required addressing issues related to the usability and ergonomics of the system, Machine-2-Machine (M2M) application integration, while delivering on its intended use and the need to facilitate the searching and location of assets.
- Maturity of the solution: an enterprise-ready solution was requested with active monitoring services of both the platform and the RTLS infrastructure. Any device or software component deployed in the facility needed to be monitored, with notifications being sent in case of anomalies and running out batteries of TAGs.
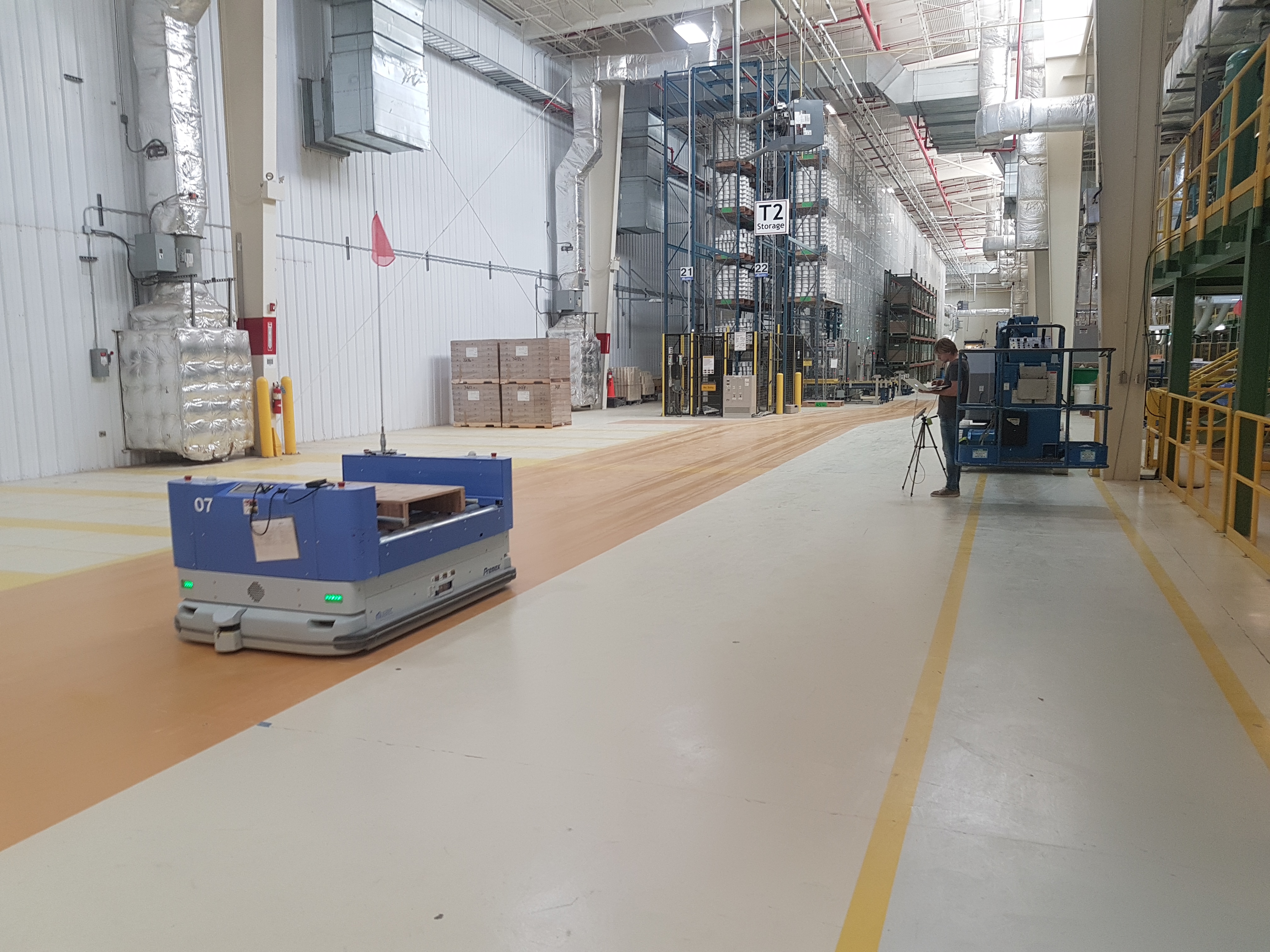
Solution
NGK retained the services of Statler Consulting, a specialist in the area of beacons and RTLS technologies, and issued a Request for Proposal (RFP) for a solution able to track assets in real-time and to deliver the necessary supporting services for the optimisation and real-time control of their production process.
Among the many solutions proposed, ThinkIN was chosen as it proved to be the best match to the requirements identified by NGK. ThinkIN is a location intelligence solution for the real-time tracking, monitoring and control of assets and workforce in industrial environments. ThinkIN technology is based on Quuppa RTLS for the high precision location of assets in the shop floor. Quuppa utilizes a unique combination of Bluetooth Low Energy (BLE) and the Angle of Arrival (AoA) methodology, as well as advanced location algorithms that have been developed over the course of more than 15 years.
ThinkIN platform provides a comprehensive set of services ranging from real-time support (e.g, asset search and location, alerts and geo-fencing, etc.), to process analytics. It also includes a number of tools to support the active monitoring of the infrastructure (both hardware and software) and a comprehensive set of user interfaces to explore the data collected and used to locate assets in real-time in the shop floor. In terms of tracking technology, Quuppa RTLS provided an optimal trade-off in terms of location accuracy, number of antennas required to cover the NGK facility and maturity of technology.
Overall 95 antennas are used to cover part of the NGK facility, with a location accuracy of approximately one meter in the areas of interest and approximately 5 meters in other areas. Different tag form factors were evaluated. Eventually, a custom Bluetooth Low Energy tag with a slim badge form factor was designed and manufactured in order to optimally align with NGK’s existing manufacturing process. The tag ensures 4+ years of life without battery replacement.
Pallets, carrying products or semi-finished goods, are identified by means of their Product Travel Ticket (PTT), which includes all the necessary information about the kind of product manufactured, together with information on production stage ( e.g. forming line, firing in kilns, etc.). At the very beginning of the production process, an RTLS TAG is associated with the pallet Travel Ticket through a mobile application running on a scanner. The application allows the scanning of both the QR code present on the PTT and the QR code on the TAG. This association creates a Digital Twin of the pallet, which is now tracked in real-time throughout its manufacturing process. The pallets can now be easily located through the ThinkIN mobile service.
Additionally, plant-level views allow staff to monitor the status of the pallets across the entire facility, maintaining an always up-to-date inventory of all pallets stocked or moving in the facility.
Additional services, delivered through ThinkIN platform, enable the quality control of pallets depending on their production stage, with alerts being triggered if the pallet moves into areas not allowed. To prevent this, a specific geo-localised workflow is imposed on the travel path of pallets depending on their production process. Warnings are raised when the specific workflow is not adhered to.
First results and looking ahead
The fully deployed production system has achieved the expected ROI, saving an average of 80 labour hours per week (previously used to search for lost pallets) and avoiding inventory shrinkage, with a total annual monetary savings of 152.000 USD.
ThinkIN’s platform has allowed NGK to digitize the shop floor by recreating the plant on screens accessible to all workers. A possible extension of services in the coming years is now being discussed at NGK facility.