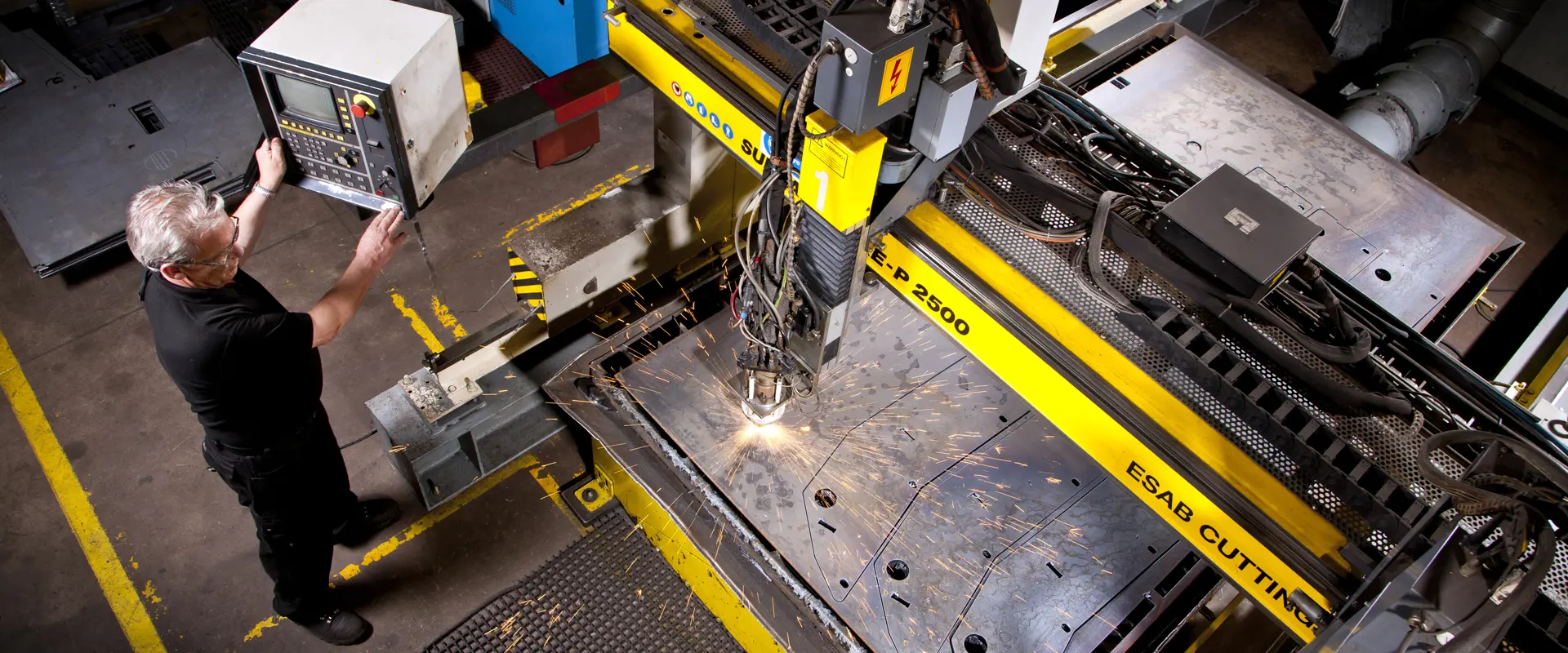
Asset tracking: Dyer Engineering cuts costs for £10.000/month
Dyer Engineering, a UK manufacturer of metal components and structures, was looking for an asset tracking solution for job orders to reduce production delays and operating costs. Dyer Engineering chose ThinkIN among 50 solutions.
- Reduction of costs of £ 10 000 / month
- 1000 tracked job orders
- Improved worker productivity and compliance with production planning
“We wanted to give the production teams the data to see what was going on in the area and where efforts to drive improvements could be made.””
RICHARD LARDER
Head of Digital Innovation
Dyer Engineering
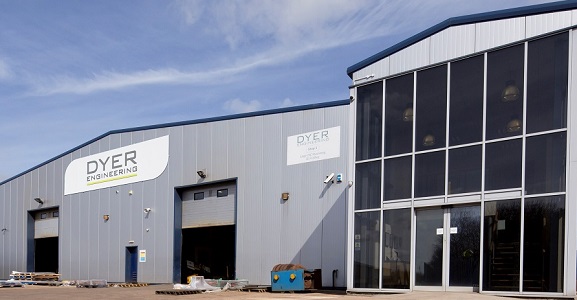
Introduction
Dyer Engineering is a UK manufacturer of metal components and fabricated and welded structures used in multiple industries including automotive, oil, gas, rail, defence, renewables and mining. It supplies its products both locally and globally since 1977. Dyer Engineering is headquartered in County Durham with two running manufacturing facilities, three miles apart one from the other, whose combined footprint is around 9.200 square meter.
Challenge
At Dyer Engineering, the production cycle is non-linear. In order to be correctly processed, different types of metals must cross several production areas and they typically move back and forth within the facility. At any given point in time, up to 1000 open jobs might be running at Dyer industrial plant, each of which includes multiple operations. It follows that nearly 5000 parts and components might be moving around in the two facilities at the same time and if the exact location of such items is unknown, the shop floor might experience serious troubles.
In fact, this complex setting of the production process suggests that any missing or lost component inside the facility can severely affect the Product Life Cycle (PLC), resulting in:
- heavy delays in production and possibly an increase of lead time;
- additional labour hours wasted in manual asset searching across the facility;
- increased operating costs;
- subsequent loss of efficiency.
In order to deal with these issues, in early 2019 Dyer decided to pilot an asset tracking solution. The project was part of the Industry 4.0 landscape exploration, as the company has always kept an eye on digital and technological developments in the domain, being a pioneer in Digital Transformation already since the 90s. Asset tracking solutions were indeed the next technology for the Digital Innovation team to look upon, in order to address some of their key challenges. For this purpose, Dyer launched a Request for Proposal (RFP) to find the best technology in the market able to improve the efficiency of its production process. The RFP was led by Digital Catapult, the UK leading centre for advanced digital technology innovation, that aims to accelerate growth, foster collaborations among start-ups, small businesses and corporations, and increase productivity across the UK economy.
Tracking solution: requirements
Dyer decided to evaluate a number of different solutions for implementing a Real- Time Locating System (RTLS) to track the flow of materials and semi-finished goods throughout the industrial process. The key requirements to be addressed by the solution were:
- Coverage and associated costs: as Dyer facility is rather large, the amount of hardware required and the associated costs were clearly an important factor to consider, as the number of RTLS antennas to be installed clearly affects the cost of cabling and connectivity;
- Accuracy: asset location data were required to be of sub-meter accuracy (specifically 0.5 meters) due to the high density of assets and materials moving across the shop floor at the same time;
- Ability to track a remarkable number of assets: the solution was initially expected to track in real-time and simultaneously up to 500 assets, together with the possibility to further expand it to the whole assets’ range;
- Maturity of the solution: Dyer Engineering was searching for an enterprise- ready solution with active monitoring, support and maintenance and for a company able to deliver detailed project plans for setup, configuration and operation of the pilot.
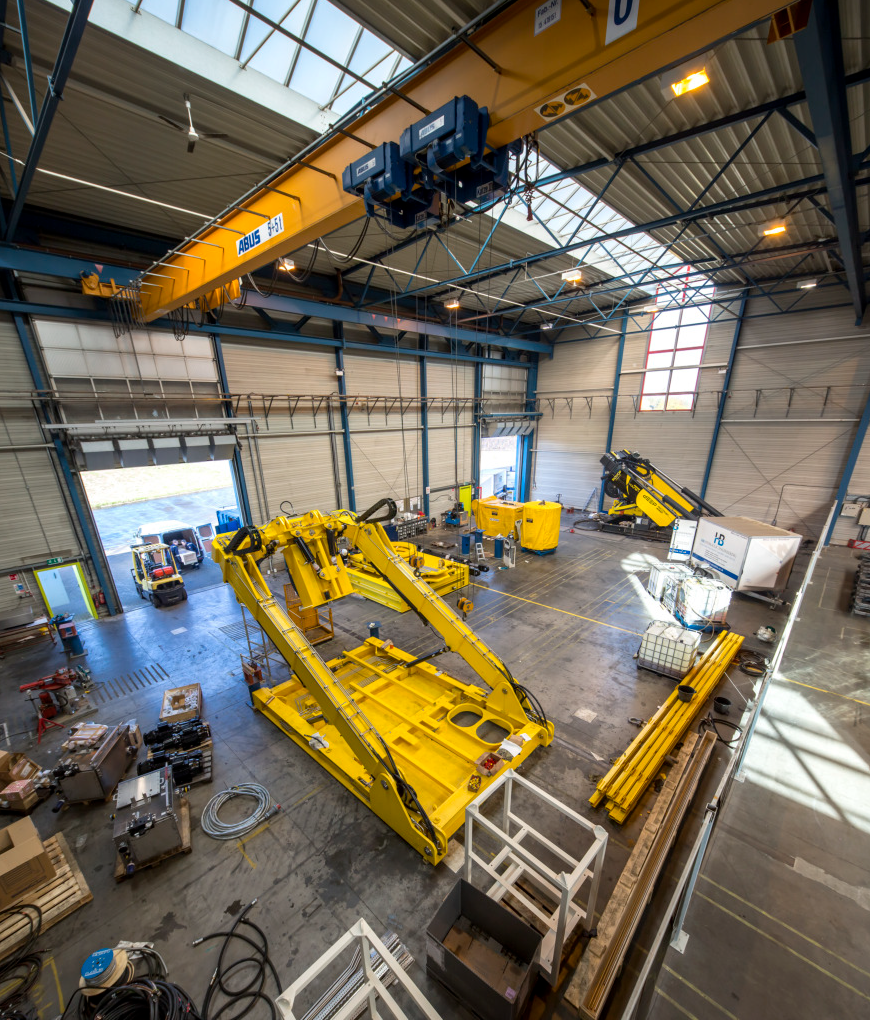
Solution
ThinkIN solution was chosen among 50 expressions of interest and 9 shortlisted proposals, as it proved to be the best match to the list of requirements set by Dyer Engineering.
ThinkIN is an innovative platform that creates a Digital Twin of the manufacturing plant by locating, tracking and monitoring materials, goods, semi-finished goods, pallets and any other relevant asset inside the factory in real-time. ThinkIN technology is based on Quuppa RTLS infrastructure for the high-precision location of assets across the shop floor. Quuppa uses a unique combination of Bluetooth Low Energy (BLE) and Angle of Arrival (AoA) methodology to provide highly accurate indoor positioning data.
ThinkIN processes the stream of these location data and provides location-based services, such as:
- track&trace of assets across the shop floor;
- process analytics;
- real-time monitoring and control services.
Overall, 55 antennae have been installed to cover the two Dyer facilities, with 1000 TAGs employed to track production orders across the facility. Each new production order is dynamically associated to a tracking device thanks to ThinkIN scanning application. ThinkIN has been easily integrated with Dyer’s ERP system, enriching the existing information of a production order with all the necessary data about the related production process.
Setting up the infrastructure, and getting the system up and running, took approximately 1 week. The primary goal of the project was to lookup assets in real-time, together with the possibility to access and review historical data (i.e. asset data trace playback), in order to find further efficiency gains along the production scheduling and process. This was achieved through a dedicated mobile interface which allows team leaders, supervisors and workers to locate parts and components on a map in real-time, while eliminating time-consuming manual searches for items.
As a second step, ThinkIN technology was used to model Dyer Engineering production process, measuring lead time across the different production phases and identifying where and how efficiency could be improved.
First results and looking ahead
By implementing ThinkIN asset tracking solution, Dyer Engineering is now able to spare labour hours previously used in manually searching for assets, translated into a reduction of costs of £10 000 per month (based on the 125 searches of the system to locate job orders).
Moreover, due to the layout of the buildings, parts and components used to stop in different locations for days or weeks and get lost in the process, resulting in employees picking the nearest job order to process rather than spending time searching for jobs with higher priority. Thanks to the possibility of digital search for assets with ThinkIN platform, employees are now more productive and efficient.
More recently, the system has been expanded to track and locate end-of-line inspection jigs and further cut costs and decrease lead time.